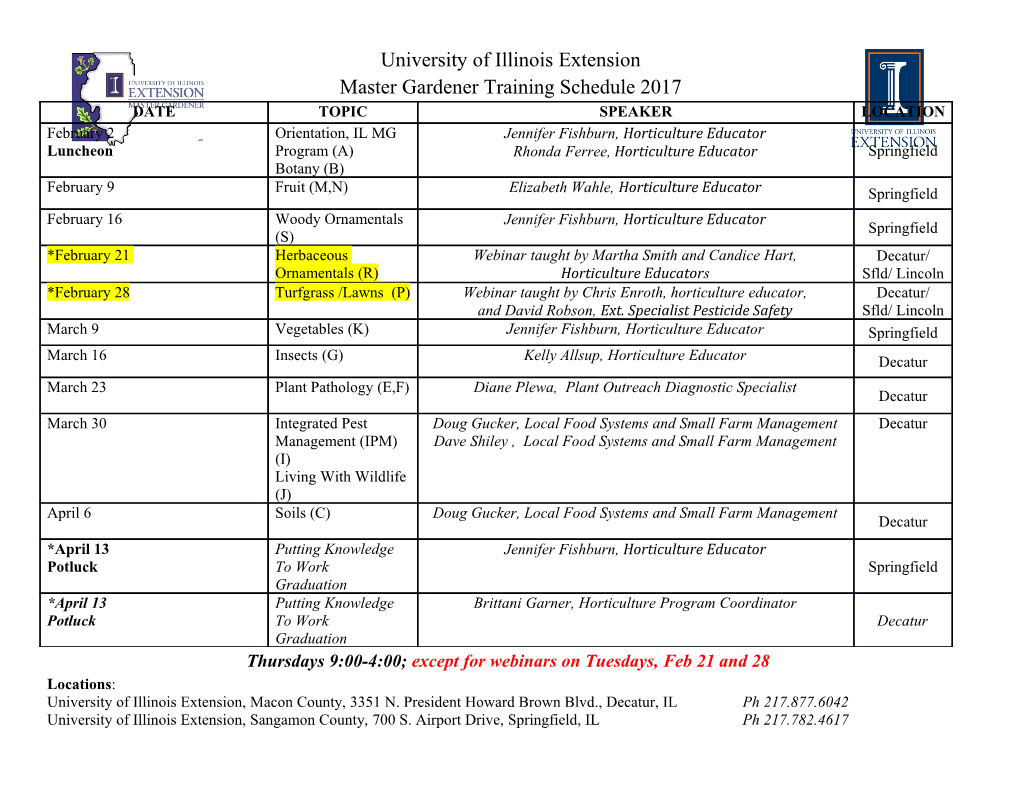
Strategies for Increased Supply Chain Flexibility: How to Meet Uncertainty in Demand From a Supply Chain Perspective A Case Study on ABB Robotics Stefanie Selmosson & Lina Hagström Student Vt 2015 Master’s Thesis, 30 credits Master of Science in Industrial Engineering and Management, Optimization and Supply Chain Management Abstract An increase in the uncertainty of customer demand has led to that industries and firms are realizing the need of being responsive, and are therefore incorporating flexibility as a core strategy. ABB Robotics is also realizing the need of flexibility and therefore, strategies should be developed in order to be able to meet the volatile demand. This study aims to analyze the Supply Chain Flexibility of ABB Robotics and to give recommendations of how ABB Robotics should incorporate and use strategies and ways to work with the concept in order to be more responsive in their supply chain. This is a qualitative study on ABB Robotics’ supply department, ABB Robotics suppliers and with benchmarking studies of three firms; Volvo Cars, Volvo Trucks and Bombardier. The authors have developed a model of Supply Chain Flexibility that fits ABB Robotics’ supply chain. The model includes the dimensions Volume Flexibility, Product Mix Flexibility, Delivery Flexibility, Sourcing Flexibility and Information System Flexibility. The conclusions are that the following four strategies increases Supply Chain Flexibility for ABB Robotics: using local supply/hubs and developing separate supply chains, using module suppliers, empowerment of suppliers and connectivity in the supply chain network. Supply Chain Flexibility has to be created and invested in, in order for firms to realize it. Implementing strategies for Supply Chain Flexibility is a way of working proactively to have the ability to be reactive. Sammanfattning En ökning i osäkerheten angående kunders efterfrågan har lett till att industrier och företag ser behovet av att vara reaktiv och införlivar därmed flexibilitet som en kärn-strategi. ABB Robotics ser även behovet av flexibilitet och därmed behöver företaget strategier för att ha möjligheten att möta den volatila efterfrågan. Denna studie syftar till att analysera flexibilitet i värdekedjan hos ABB Robotics samt att ge rekommendationer för hur ABB Robotics bör inkludera och använda strategier och sätt att arbeta med konceptet för att vara mer reaktiv i deras försörjningskedja. Studien har genomförts med kvalitativa studier på ABB Robotics inköpsavdelning, ABB Robotics leverantörer och med en jämförande studie på tre företag; Volvo Personvagnar, Volvo Lastbilar och Bombardier. Författarna har utvecklat en modell för flexibilitet i värdeflödeskedjan som passar på ABB Robotics värdeflödeskedja. Modellen inkluderar dimensionerna volymflexibilitet, produktmixflexibilitet, leveransflexibilitet, inköpsflexibilitet och informationssystemsflexibilitet. Slutsatsen är att de följande fyra strategierna ökar flexibiliteten i värdekedjan för ABB Robotics: använda lokal produktion/externa lager och utvecklande av separata värdekedjor, använda modulleverantörer, bemyndigande av leverantörer samt att koppla samman värdeflödesnätverket. Flexibilitet i värdekedjan måste skapas och investeras i för att möjliggöras. Implementationen av strategier inom flexibilitet är ett sätt att arbeta proaktivt för att kunna vara reaktiv. Acknowledgements We would first of all like to express our gratitude to ABB Robotics and our supervisor Ronny Jansson for all the support he has given us, despite his busy schedule. We would also like to thank the staff at ABB Robotics and the representatives from Kablageproduktion AB, CEPA Steeltech AB, Bufab Sweden, Enics, Volvo Cars, Volvo Trucks and Bombardier for your great engagement. We would also like to thank our supervisor from Umeå University, Lars Silver, for all the guidance. Thank you all! Table of Contents 1 Introduction 1 1.1 Problem definition 2 1.2 Purpose and Objective 2 1.3 Delimitations 2 1.4 Assumptions 3 1.5 Concepts and Abbreviations 3 1.6 Disposition and Readers Guide 3 2 Theory 5 2.1 What is Flexibility? 5 2.2 Flexibility and Organizational Performance 6 2.3 Supply Chain Flexibility 6 2.3.1 Cost of Supply Chain Flexibility 7 2.4 Supply Chain Networks 7 2.5 Dimensions of Supply Chain Flexibility and Developed Supply Chain Flexibility Model 8 2.6 Concepts that is Important to Supply Chain Flexibility 10 2.6.1 Information Systems in Supply Chains 10 2.6.2 Connectivity and Willingness of Information Sharing 11 2.6.3 The Bullwhip Effect in Networks 11 2.6.4 Postponement of De-Coupling Point in Networks to Reduce Uncertainty 12 3 Method 13 3.1 Process of Developing the Supply Chain Flexibility Model 13 3.2 Primary Data Collection and Process 13 3.3 Secondary Data Collection 14 3.4 Benchmarking 14 3.4.1 Benchmarking and Quantitative Measurement 14 3.5 Process of Developing Strategies of Increased Supply Chain Flexibility 15 3.6.1 People Connected to ABB Robotics 15 3.6.2 People Independent from ABB Robotics 16 4 ABB Robotics 17 4.1 ABB Robotics and Their Products 17 4.2 The Different Customer Segments 18 4.3 Forecasting Customer Demand and Turning it Into a Purchasing Forecast 18 4.4 The Supply Department 20 20 4.4.1 The Organization 20 4.4.2 Operational Supply 20 4.4.3 Strategic Supply 20 4.4.4 Supplier quality 21 4.4.5 KPIs (Key Performance Indexes) 21 4.5 The Categories 21 4.6 Flexibility Requirements on Suppliers 23 5 Empirical Study - Flexibility of Suppliers 24 5.1 Cable and Harnesses 24 5.1.1 The Network in the Category Cable and Harnesses 28 5.2 Castings and Machining 28 5.2.1 The Network in the Category Castings and Machining 31 5.3 PCBA inclusive Drives 32 5.3.1 The Network in the Category PCBA inclusive Drives 35 5.4 Standard and others 36 5.4.1 The Network in the Category Standards and Others 39 5.5 Gears and Motors 39 6 How Others Manage Supply Chain Flexibility 40 6.1 Quantitative Measurement of Supply Chain Flexibility 40 6.2 Bombardier 41 6.2.1 Supply Chain Flexibility at Bombardier 42 6.3 Volvo Trucks 42 6.3.1 Supply Chain Flexibility at Volvo Trucks 43 6.4 Volvo Cars 44 6.4.1 Supply Chain Flexibility at Volvo Cars 45 7.1 The Use of Hubs/Localization - Developing Separate Supply Chains 48 7.2 Empowering suppliers 52 7.3 Modules 55 7.4 Connectivity - The Exchange of Information 57 8 Discussion 61 8.1 Discussion of Supply Chain Flexibility Measurement 63 10 Conclusion 66 11 References 67 11.1 Scholarly Articles 67 11.2 Books 69 11.3 Internet Sources 69 11.4 Documents from ABB 70 12 Appendices 71 Appendix A - Dimensions of Flexibility 71 Appendix B - Flexibility in dimensions for the category Cable and Harnesses: Kablageproduktion AB 72 Appendix C - Flexibility in dimensions for the category Castings and Machining: CEPA 75 Appendix D - Flexibility in dimensions for the category PCBA Incl. Drives: Enics 78 Appendix E - Flexibility in dimensions for the category Standards and others: Bufab 80 Appendix F - Supply Chain Flexibility Measurement of the Benchmarking Firms 82 John Gossman (1997), vice president of materials manage- ment at AlliedSignal: “Competition is no longer company to company, but supply chain to supply chain” 1 Introduction The quote above is an indication on that there has been a shift in focus during the last couple of decades, from competing with manufacturing to competing with supply chain management. Firms are realizing the importance of optimizing their supply chain, in order to decrease costs and to stay competitive. The uncertainty is increasing, which makes the probability of that the customers’ demand increases or decreases in volume, cancel or moving orders backwards or forward is higher than ever. The customers are also requiring customizations to a greater extent than before. This results in an uncertain environment for organizations to act on, which forces players on the market to be more flexible in many respects (Angkiriwang et al., 2014). Hence, uncertainty drives flexibility, which has now become an integral part of managers’ strategies, regardless of the market or structure of the organization. This paper aims to define Supply Chain Flexibility and to present strategies regarding how ABB Robotics should work with it. In order to do this, a case study has been made on ABB Robotics. ABB Robotics, hereafter referred to as Robotics, is a global manufacturer, which produces industry robots for different companies and industries all around the world. In markets where firms need to be more effective in order to decrease prices, the demand on industrial robots is increasing. Robotics has therefore been growing rapidly for some years. In the year 2020 Robotics is planning on producing 100,000 robots, which is a high volume increase in comparison with today’s volumes. Robotics is gaining market shares and has now approximately 18 % of the total market. The company is expecting the market for industrial robots to grow, since more factories in new and current markets are realizing the advantages and has the will to invest in robots. This means that Robotics is facing new challenges. Robotics is also experiencing that their demand curve has a higher volatility than ever. This is due to the fact that customers usually order in peaks, which leads to new challenges for the supply chain. The figure below visualizes Robotics daily production rate from 2008 up till now. As the reader can see, the production volume varies more on a daily basis with time. This figure represents the problem and the need of supply chain flexibility, since the peaks are more frequent now compared to 2008. 1 Daily Produc-on Rate Figure 1.1 - Daily Production Rate from January 2008 to February 2015. (ABB Robotics, 2015) 1.1 Problem definition The problem that is being addressed in this study is how ABB Robotics, that is experiencing a volatile demand and a higher pressure from customers, should operate and manage their supply chain in order to meet the volatile demand curve and create the ability to be responsive.
Details
-
File Typepdf
-
Upload Time-
-
Content LanguagesEnglish
-
Upload UserAnonymous/Not logged-in
-
File Pages89 Page
-
File Size-