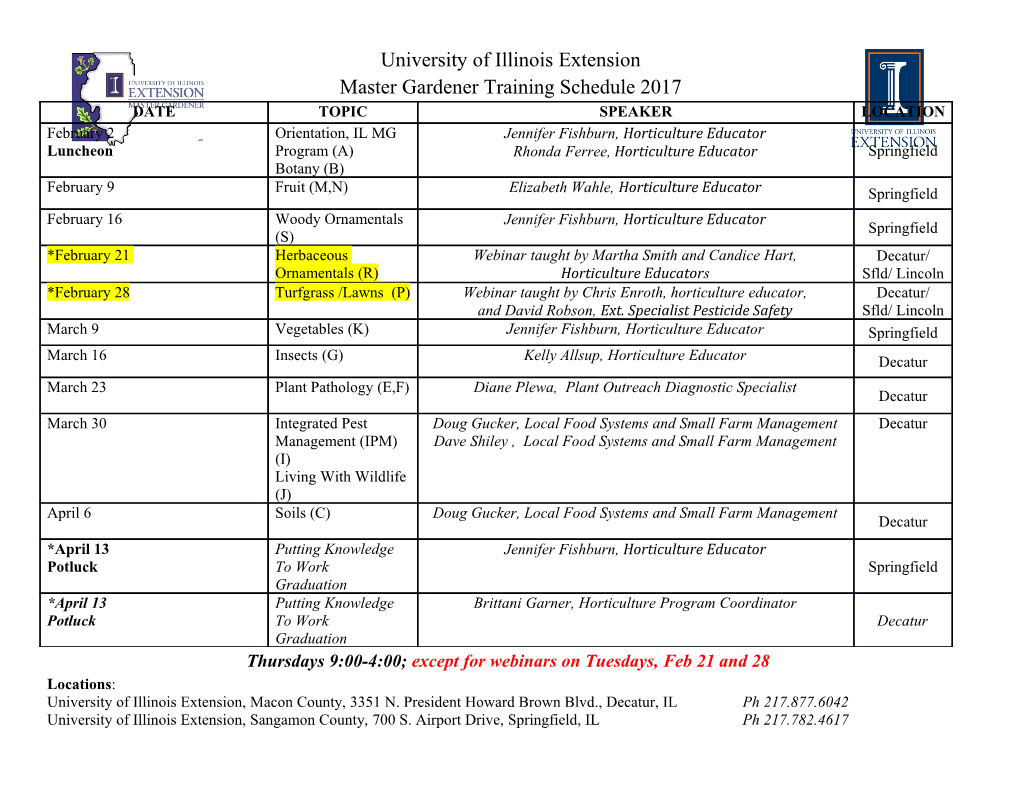
2,964,504 United States Patent Office Patented Dec. 13, 1960 2 polymerization and to improve polymerization catalyst efficiency. These and other objects, as well as the nature, 2,964,504 scope and operation of the invention will become more STEAM CRACKENG OF LIGHT NAPHTHA AND clearly apparent from the following description. In PREPARATION OF RESNS reading this description it should be understood that all Robert F. Leary, Cranford, Howard T. Oakley, Elizabeth, ratios, proportions and percentages are expressed through and John F. McKay, Cranford, N.J., assignors to Esso out on a weight basis, unless otherwise indicated. Research and Engineering Company, a corporation of It has been found that in making the petroleum resins Delaware about 0.5 to 2 percent of aluminum chloride catalyst 0 (based on total hydrocarbon feed to the polymerization No Drawing. Filed Dec. 10, 1956, Ser. No. 627,090 zone) is needed, more or less independently of the con centration of the polymerizable unsaturates present in 5 Caims. (C. 260-82) the feed. Because of this, when polymerizing a C5-plus fraction derived from steam cracking of ordinary light This invention relates to steam cracking of light 15 naphtha, the amount of catalyst required is necessarily naphtha. More particularly it relates to an improvement large in relation to the amount of resin produced since in the preparation of hydrocarbon resins from steam such a fraction normally contains large amounts of un cracked light naphtha. converted saturated hydrocarbons in addition to the Steam cracking of various petroleum hydrocarbon frac polymerizable cracking products. This relatively large tions such as gas oil or heavy naphtha is a well-known 20 ratio of catalyst to reactive components of the poly process that is assuming ever increasing importance as merizable naphtha fraction appears to be principally a source of ethylene, butadiene, etc. In addition to pro responsible for the unsatisfactory resin quality derived ducing the desired light olefins and diolefins, conven from steam cracked light naphtha. However, reduction tional steam cracking of the heavier petroleum fractions of catalyst concentration below about 0.5% based on also produces a valuable intermediate fraction boiling 25 total polymerization feed has been found impractical between about 60 and 250 F. and containing C5 and under normal circumstances, because low yields of resin higher hydrocarbons rich in olefins and diolefins. This are obtained. In addition the resin softening point be cracked naphtha fraction, after intervening separation of comes so low that the resin is not useful. cyclopentadiene and isoprene if desired, has been used It has now been discovered that the foregoing diffi as a feed for preparing high quality petroleum resins by 30 culties can be substantially eliminated and a high quality polymerization in the presence of about 1% of aluminum resin prepared even from steam cracked light virgin chloride based on polymerization feed. The unpoly naphtha, provided that the boiling range of the light merized remainder is a useful gasoline component. One naphtha used as cracking feed has a definite relation to such typical process is described, for instance, in Patent the boiling range of the steam cracked fraction used as 2,734,046. This steam cracking process served the art 35 polymerization feed. More particularly it has been well as long as gasoline demand was sufficient to con found that a surprising improvement in resin production stitute the most economic outlet for light virgin naphtha is obtained if the boiling range of the steam cracked streams and as long as there was a sufficient supply of . fraction used as resin polymerization feed is such that it the higher boiling fractions or the so-called middle dis is essentially completely below the boiling range of the tillates to be used economically as a feed for steam 40 light virgin naphtha used as steam cracking weed. As cracking. a corollary, since the bulk of the reactive hydrocarbons More recently, however, especially in some regions, the useful in making the petroleum resins are in the C5 range, demand for middle distillates, i.e., diesel and jet aircraft it is essential for the purposes of the present invention fuels as well as domestic and industrial fuels, has become to use as steam cracking feed a light virgin naphtha from quite high in relation to gasoline. As a result, situations 45 which normally present CA and C5 hydrocarbons, i.e., have developed where the supply of light naphtha exceeds materials boiling below 120 F., have been excluded, that needed for gasoline while all the middle distillates and then prepare a polymerization feed by segregating produced find an attractive market as fuels. In such situ from the steam cracked products a fraction boiling from ations it would be preferable to make ethylene, butadiene about 60 F. approximately up to the initial boiling point and the like by steam cracking light naphtha rather than 50 of the virgin naphtha feed. Of course, it is possible to the heavier distillates. However, when light naphtha is use as cracking feed light naphthas having an initial steam cracked, the resulting C5-250 F. fraction is a very boiling point higher than 120 F., e.g. 160 or even 180° unsatisfactory feed for preparing the aforementioned F., in which event it will be possible correspondingly to petroleum resins. When derived from such cracked raise the end point of the cracked fraction used as poly light naphtha, the resulting resins not only are obtained 55 merization feed. In brief, the steam cracking feeds in very poor yields, but also tend to contain appreciable suitable for purposes of the present invention are light amounts of catalyst residue, show poor color stability, naphthas boiling in the range from 120 to about 350 F., poor oxidation resistance as well as a relatively low e.g. 120-220 F. Another essential feature of the in softening point. This unfavorable combination of prop vention requires that the steam cracked products be erties consequently precludes their being put to premium 60 fractionated to provide as polymerization feed a fraction uses such as for paper sizing, etc. ranging from C5 hydrocarbons up to the initial boiling It is the main object of the present invention to devise point of the cracking feed used, preferably boiling from 60 to 120 F., and containing about 20 to 50 weight a process permitting the use of light naphtha as a steam percent, preferably 25 to 40 weight percent, of material cracking feed and simultaneously producing not only 65 polymerizable in the resin production step. ethylene, butadiene, etc., but also a cracked C5-plus The chemical composition of the feed has some effect fraction suitable as a polymerization feed in the prep on the yield of butadiene obtainable by steam cracking. aration of high quality petroleum resins. Still another However, as far as the by-product resin formation is con object is to improve the resin yields obtainable in the cerned, the source of the virgin naphtha feed is relatively 2,964,504 3 4. immaterial and may be either a predominantly parafiinic TABLE or a predominantly naphthenic crude. For instance, Yields of products from steam cracking naphthas at Arabian as well as Venezuelan light naphthas are suitable. 1400 F. and 12 p.s.i.a. HCPP Thus, a useful steam cracking feed is a light virgin naphtha having the following typical characteristics: Run No-------------------------------- 1 2 4. TABLE I Analysis of cracking feed Naphthahtha Feed-------------------------- C-2200'i. C-220F. C-250°F. Boiling range, F------------------------- 120-220 O Yields-Wit. percent on Feed: Gravity, API------ - - - - - - - - - - - - - - - - - - - - - 72 C3 and Lighter------------------- 45.0 45.0 45, 0 Composition, weight percent Total C4's------- 1.1 1.1 2.4 Isoprene----------------------------Piperylene----- } 0.7 .5 2.1 Butanes ------------------------------------ O Total Cs's---- 13.0 6.4 6.6 Cs-Co. Cyclopen 0.9 1.2 1.3 Isopentane ---------------------------------- 0.5 Benzene----------- 2.0 2. 3.3 n-Pentane ---------------------------------- 2.0 15 Toluene.---------------------------- 2.5 2.9 4.1 Cyclopentane ------------------------------- 0.5 Cs and Heavier--------------------- 43.9 43.9 40, 6 Branched hexanes---------------------------- 14. n-Hexane ----------------------------------- 21.0 Comparing Runs 1 and 2, it is seen that Run 2 produces about twice as much isoprene and piperylene than Run 1, Methylcyclopentane -------------------------- 4.0 20 Benzene -------- m - as as a are saw as marr or run-uru un a as a 1.5 while the total C fraction (including amylenes and some Dimethyl pentanes---------------------------- 8.5 cyclopentadiene) is only about half as large in Run 2 Cyclohexane -------------------------------- 4.0 as in Run 1. Of course, in Run 2 all of the C5 hydro Methyl hexanes------------------------------ 10.0 carbons represent cracking products whereas in Run 1 3-ethyl pentane------------------------------- 2.5 a large proportion of this fraction is unconverted feed. Dimethylcyclopentanes ----------------------- 3.0 25 As seen in Run 4, the Canadian naphtha gave a product 2,2,4-trimethylpentane ------------------------ 0.5 somewhat richer in benzene and toluene than obtained in n-Heptane ---------------------------------- 21.5 the other two cracking runs. Methylcyclohexane --------------------------- 4.5 The steam cracked naphtha can be processed in various Toluene ------------------------------------ 2.0 ways. For instance, the products may be fractionated 30 into four principal fractions; namely, C8 and lighter gases it can be seen that this naphtha is about 80% par (e.g., ethylene, propylene, etc), a C4 cut, a C5 to 125 F. affinic, mostly hexanes and heptanes, about 15% naph cracked naphtha fraction, and a higher boiling naphtha. thenic, and less than 5% aromatic, with less than 3% of fraction. In view of the iow end point of the light C5 and lower hydrocarbons. More broadly speaking, naphtha feed used in this invention, the amount of steam suitable cracking feeds shall contain not more than 5% 35 cracked product boiling above about 250 F.
Details
-
File Typepdf
-
Upload Time-
-
Content LanguagesEnglish
-
Upload UserAnonymous/Not logged-in
-
File Pages4 Page
-
File Size-