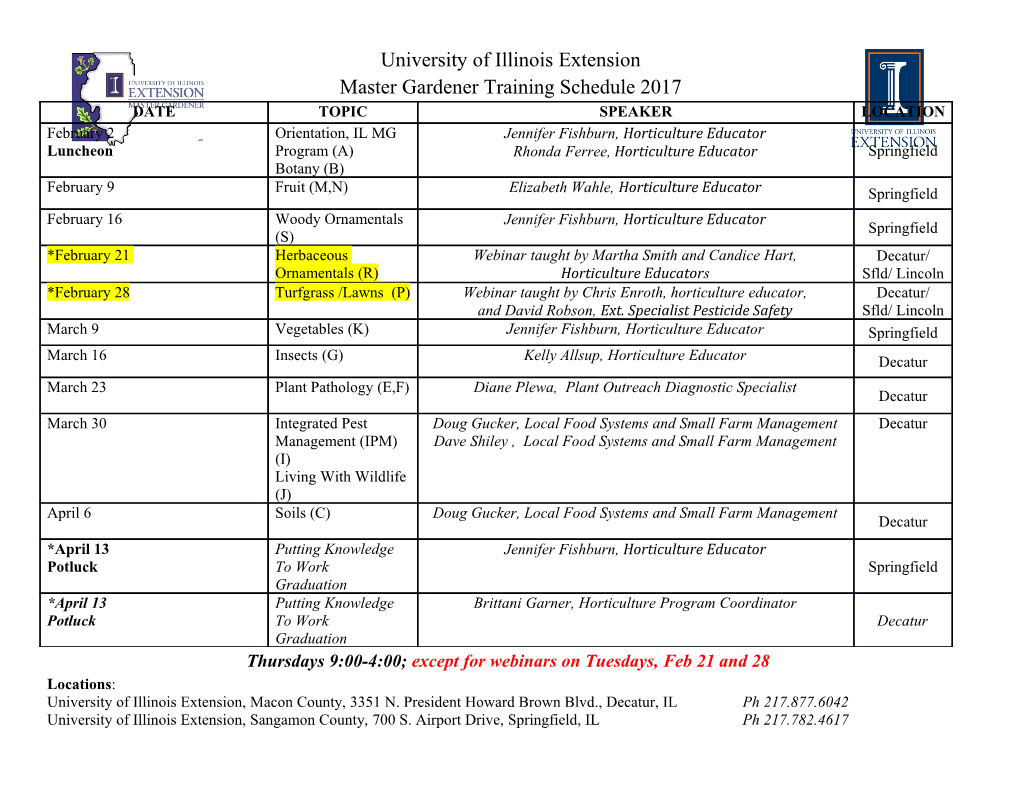
applied sciences Article An Experimental Study on the Reduction Behavior of Dust Generated from Electric Arc Furnace Mengxu Zhang 1, Jianli Li 1,2,3,* , Qiang Zeng 1 and Qiqiang Mou 1 1 The State Key Laboratory of Refractories and Metallurgy, Wuhan University of Science and Technology, Wuhan 430081, China 2 Hubei Provincial Key Laboratory for New Processes of Ironmaking and Steelmaking, Wuhan University of Science and Technology, Wuhan 430081, China 3 Key Laboratory for Ferrous Metallurgy and Resources Utilization of Ministry of Education, Wuhan University of Science and Technology, Wuhan 430081, China * Correspondence: [email protected] Received: 5 August 2019; Accepted: 29 August 2019; Published: 2 September 2019 Featured Application: This work expects to propose a direct-recycling process on basis of the mixture of EAFD powder and reductant (carbon or ferrosilicon) loaded into an electric arc furnace, in order to recycle Zn and Fe in the form of dust and molten steel. The results would provide the theoretical reference. Abstract: To improve the utilization value of electric arc furnace dust (EAFD) containing zinc, the reduction behavior of non-agglomerate dust was investigated with carbon and ferrosilicon in an induction furnace. The experimental results show that when the temperature increases, the zinc evaporation rate increases. When the reducing agent is carbon, zinc evaporation mainly occurs in the range of 900–1100 ◦C. When the reducing agent is ferrosilicon, zinc begins to evaporate at 800 ◦C, but the zinc evaporation rate is 90.47% at 1200 ◦C and lower than 99.80% with carbon used as a reducing agent at 1200 ◦C. For the carbon reduction, the iron metallization rate increases with a rise in the temperature. When the reducing agent is ferrosilicon, with an increase in temperature, the metallization rate first increases, then decreases, and finally, increases, which is mainly due to the reaction between the metallic iron and ZnO. In addition, the residual zinc in the EAFD is mainly dispersed in the form of a spinel solution near the metallic phase. Keywords: EAFD; reduction; Zinc; FeO; evaporation; metallization 1. Introduction Electric arc furnace dust (EAFD) is one of the by-products of electric furnace steelmaking, and its production accounts for 1~2% of the charging amount of steel scrap and other metal materials [1,2]. Because heavy metal elements like lead, chromium, and cadmium are contained in EAFD, these kinds of by-products are classified as toxic waste by many countries [3]. However, dust that contains iron, lead, zinc, and chromium can be used as a secondary resource. Therefore, the recovery of these resources plays an important role in environmental protection [4–7]. However, the zinc content of EAFD is generally <25 wt%, which does not meet the raw material requirements for the non-ferrous industry. Thus, a part of the EAFD can only be stacked or landfilled as disposal [8]. In order to reduce pollutant emissions and promote ecological progress, the environmental protection laws of the People’s Republic of China stipulate that the taxes for steelmaking slag, steelmaking dust, coal ash, and other solid waste are 25 yuan per ton. However, if the solid waste is comprehensively utilized and meets the standards of the national and local environmental protection laws, the corresponding tax can be Appl. Sci. 2019, 9, 3604; doi:10.3390/app9173604 www.mdpi.com/journal/applsci Appl. Sci. 2019, 9, 3604 2 of 11 temporarily exempted. The output of the EAFD increased rapidly with increases in the output of EAF steelmaking [9,10]. Therefore, the treatment and comprehensive utilization of EAFD is gradually focused, and a variety of studies have been carried out. At present, the Waelz kiln process, the rotary hearth furnace process (RHF), and the OxyCup process are the main processes used to treat steelmaking dust [11]. Although these processes can recycle the dust and sludge of iron and steel enterprises to some extent, they all have shortcomings. For example, the Waelz kiln process has higher requirements for raw materials, higher energy consumption, unstable production and operation, and a limited processing scale [12]. The main product of the RHF is metallized pellets, but its product has a high sulfur content, and the process has a low production efficiency and a large investment [13]. The OxyCup process’s product is molten iron, and its requirements for raw materials are relatively broad. However, its equipment operation cycle is short, and its maintenance work is difficult [11]. Furthermore, a homogenous mixture of EAF dust, reductant, and flux needs to be initially prepared in pellet form during the above processes [14]. In view of their shortcomings, it is an urgent issue to propose an eco-friendly practical process to recycle and utilize the valuable elements in the dust of iron and steel enterprises on the basis of environmental protection. Xu [15] and Zhang [16] mixed electric furnace dust with a reducing agent, without lumping or pelletizing, and then charged the mixture from the EAF directly into bags, which not only reduced the dust production by 40% and increased the zinc content in the dust to 29.7%, but also directly recycled valuable elements, such as iron, in the dust. Normal smelting is not affected by this process, but foaming slag occurs, while the zinc content of secondary dust without charging pellets is only 21% zinc. In order to further understand the behavior of zinc and iron in EAFD at different temperatures and provide theoretical reference for the recycling of EAFD containing zinc, the evaporation behavior of zinc and the metallization ratio of iron during EAFD reduction via carbon and ferrosilicon are investigated in this work. 2. Experimental The EAFD was obtained from an electric arc furnace (Xingtai Iron & Steel Corp. LTD, Xingtai, China). As shown in Table1, Fe 2O3 and ZnO were the main components of the dust, together comprising 67.09 wt% of it. In the dust, there was, simultaneously, CaO, MgO, SiO2, Cr2O3, MnO, and a small amount of Al2O3. Fe and Zn mainly existed in ZnFe2O4, Fe3O4, and ZnO, which were also the main phases of EAFD (Figure1). As shown in Figure2, EAFD mainly consisted of small particles, which were less than 2 µm. Ferrosilicon and carbon powder were used as reducing agents in the experiments. The ferrosilicon contained 74.64% Si and 24.00% Fe, and the content of C in the carbon powder was >99%. Both were ground into powder for use. Fe2O3, ZnO, and MnO in the EAFD can be reduced to Fe, Zn, and Mn via the reducing agents. Based on Table1, it can be calculated that when 100 g EAFD was reduced by silicon or carbon, the required amounts of silicon and carbon were 15.63 g and 14.72 g, respectively. Since the ferrosilicon alloy was the carrier of silicon, its silicon content was 74.64%. Therefore, the actual amount of ferrosilicon alloy for 100 g dust was 20.92 g. In order to completely reduce the sample, the amount of the dispensed reducing agent should be slightly excessive. Therefore, the final amount of the ferrosilicon alloy and carbon powder was set to 22 wt% and 16 wt%, respectively. Table 1. The composition of electric arc furnace dust (EAFD) in wt%. Component CaO MgO SiO2 Al2O3 Cr2O3 Fe2O3 ZnO MnO KCl CaF2 Content 6.80 5.83 5.67 0.35 5.02 40.30 26.79 2.27 0.88 1.6 Appl. Sci. 2019, 9, x FOR PEER REVIEW 3 of 11 Appl. Sci. 2019, 9, 3604 3 of 11 1 1 1- ZnFe2O4, Fe3O4 1- ZnFe2O4, Fe3O4 2- ZnO 2 2 1 2 1 1 1 1 2 2 1 2 2 1 2 2 2 20 30 40 50 60 70 2θ / ° 2θ / Figure 1. XRD diffraction diffraction pattern of EAFD. Figure 2. The microstructure of EAFD. This experiment includes two series, referred to as A and B. A total of 50 g EAFD in series A Fe2O3, ZnO, and MnO in the EAFD can be reduced to Fe, Zn, and Mn via the reducing agents. wasBased mixed on Table with 1, 8 it g can carbon be calculated powder, while that when 50 g EAFD100 g EAFD in series was B wasreduced mixed by withsilicon 11 or g ferrosiliconcarbon, the alloyrequired powder. amounts The of uniform silicon mixing and carbon samples were were 15.63 charged g and into14.72 the g, corundumrespectively. crucible Since (innerthe ferrosilicon diameter 32alloy mm, was height the carrier 65 mm, of and silicon, wall thicknessits silicon 1 mm)content with was a corundum74.64%. Therefore, cover. The the crucible actual usedamount in this of experimentferrosilicon alloy was completelyfor 100 g dust dried was in 20.92 a mu g.ffl Ine furnaceorder to under completely 200 ◦C reduce for 3 hthe in sample, order to the eliminate amount the of influencethe dispensed of water. reducing The crucible agent containingshould be the slightly materials excessive. was loaded Therefore, into an inductionthe final amount furnace (60of kW,the 3ferrosilicon kHz) and keptalloy at and diff carbonerent temperatures powder was forset 30to 22 min. wt% Six and temperatures 16 wt%, respectively. were selected: 700 ◦C, 800 ◦C, 900 ◦ThisC, 1000 experiment◦C, 1100 includes◦C, and 1200two series,◦C. The referred numbers to as of A the and experiments B. A total of are 50 showng EAFD in in Table series2. A After was keepingmixed with a constant 8 g carbon temperature powder, while for the 50 predetermined g EAFD in series time, B was the samplesmixed with were 11 naturallyg ferrosilicon cooled alloy to room-temperaturepowder. The uniform in the mixing furnace. samples were charged into the corundum crucible (inner diameter 32 mm, height 65 mm, and wall thickness 1 mm) with a corundum cover.
Details
-
File Typepdf
-
Upload Time-
-
Content LanguagesEnglish
-
Upload UserAnonymous/Not logged-in
-
File Pages11 Page
-
File Size-