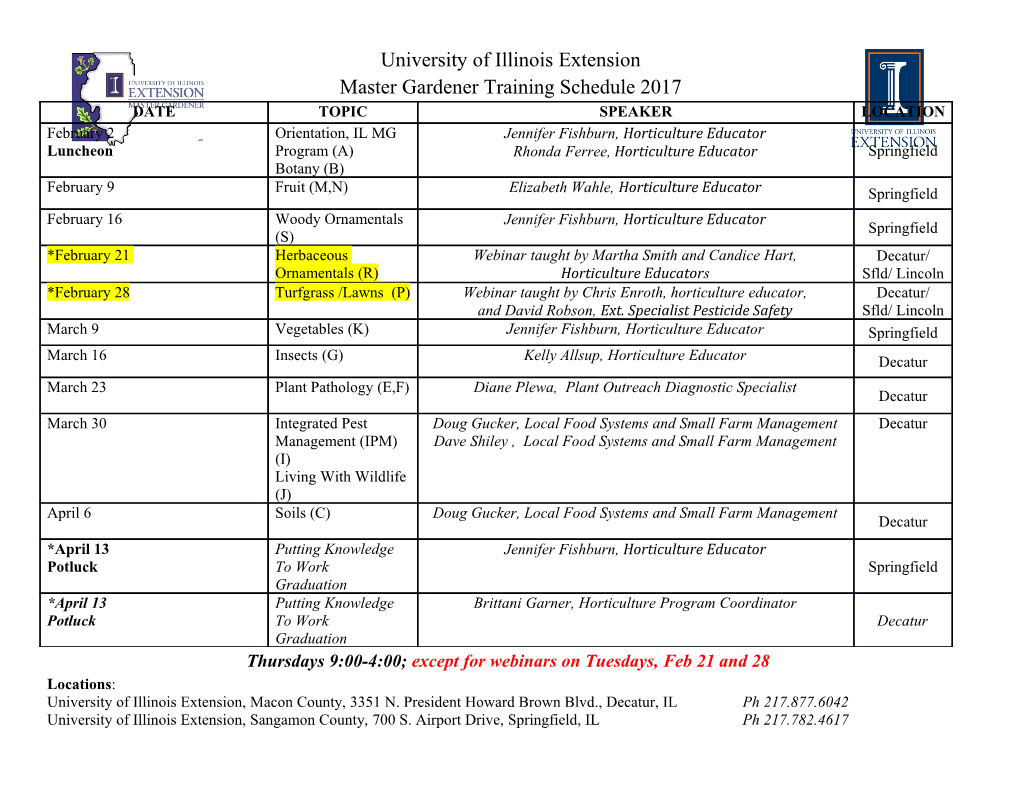
materials Article Relationship of Stiffness-Based Indentation Properties Using Continuous-Stiffness-Measurement Method Wai Yeong Huen 1,* , Hyuk Lee 1, Vanissorn Vimonsatit 1 and Priyan Mendis 2 1 Civil and Mechanical Engineering, Curtin University, 6102 Perth, Australia; [email protected] (H.L.); [email protected] (V.V.) 2 Infrastructure Engineering, University of Melbourne, 3010 Melbourne, Australia; [email protected] * Correspondence: [email protected] Received: 18 November 2019; Accepted: 18 December 2019; Published: 24 December 2019 Abstract: The determination of elastic modulus (E) and hardness (H) relies on the accuracy of the contact area under the indenter tip, but this parameter cannot be explicitly measured during the nanoindentation process. This work presents a new approach that can derive the elastic modulus (E) and contact depth (hc) based on measured experiment stiffness using the continuous-stiffness-measurement (CSM) method. To achieve this, an inverse algorithm is proposed by incorporating a set of stiffness-based relationship functions that are derived from combining the dimensional analysis approach and computational simulation. This proposed solution considers both the sink-in and pile-up contact profiles; therefore, it provides a more accurate solution when compared to a conventional method that only considers the sink-in contact profile. While the proposed solution is sensitive to Poisson’s ratio (ν) and the equivalent indentation conical angle (θ), it is not affected by material plasticity, including yield strength (σy) and work hardening (n) for the investigated range of 0.001 < σy/E < 0.5. The proposed stiffness-based approach can be used to consistently derive elastic modulus and hardness by using stiffness and the load-and-unload curve measured by the continuous-stiffness-measurement (CSM) method. Keywords: nanoindentation; stiffness; elastic modulus; hardness. 1. Introduction Nanoindentation is a commonly used technique to investigate submicron or nanoscale mechanical material properties such as elastic modulus (E) and hardness (H). These properties can be deduced from the load-unload curve using a popular method proposed by Oliver and Pharr [1,2], also known as the Oliver and Pharr method. Central to the Oliver and Pharr method is the determination of the projected area from the surface formed by the indenter’s impression, also referred to as the contact area. Determining the indentation’s impression area is a complex process where analytical solutions are difficult to obtain due to its dependence on the material’s elastic and plastic behaviour [3,4]. The original Oliver and Pharr method relies on the elastic-contact analytical solution first introduced by Sneddon [5], who described the shape of an indentation impression using a solid revolution of a nonlinear function. As a result, the Oliver and Pharr method generally apply well to material that has a sink-in contact profile, where the contact point between indenter and material is lower compared to that of the original material surface. However, for the same reason, it is unclear how well the Oliver and Pharr method can be used for material that exhibits a pile-up profile, where the contact area between indenter and material is higher than that of the original material surface. Both the sink-in and pile-up contact profiles are illustrated in Figure1. Materials 2020, 13, 97; doi:10.3390/ma13010097 www.mdpi.com/journal/materials Materials 2019, 12, x FOR PEER REVIEW 2 of 11 For this reason, researchers often cautioned the use of the Oliver and Pharr method when Materialsapplied2020, 13to, a 97 wide range of materials with contact profiles that no longer resemble the assumed elastic2 of 10 analytical solution [6–8]. FigureFigure 1. Sink-in 1. Sink and‐in and pile-up pile‐up contact contact profile profile createdcreated on on a a sample sample during during the the nanoindentation nanoindentation process. process. For thisTo address reason, researchersthis issue, other often researchers cautioned attempted the use of to the improve Oliver andaccuracy Pharr in method determining when the applied to a widecontact range area of by materials visual methods with contact [9–11], profiles a semiempirical that no longer approach resemble [12,13], the and assumed the computational elastic analytical solutionfinite [6‐element–8]. approach [8,14,15]. These efforts were further extended to investigate the relationship Toof the address material’s this issue,mechanical other properties researchers with attempted the contact to area improve using accuracy the dimensional in determining‐analysis the approach [16–19]. The dimensional‐analysis approach allows the derivation of the material’s contact area by visual methods [9–11], a semiempirical approach [12,13], and the computational mechanical properties such as elastic modulus (E), hardness (H), yield strength (σy), and work‐ finite-elementhardening approachexponent from [8,14 a, 15set]. of These relationships efforts wereusing furthera specific extended algorithm to to investigate extract key information the relationship of thefrom material’s a single nanoindentation mechanical properties load‐unload with curve the [20–22]. contact Another area key using contribution the dimensional-analysis is provided by approachthe continuous [16–19]. The‐stiffness dimensional-analysis‐measurement (CSM) approach method allows from the the derivation nanoindentation of the material’stechnique mechanicalwhere propertiesdirect measurement such as elastic of the modulus material’s ( stiffnessE), hardness is made (H possible.), yield Dimensional strength ( σfunctionsy), and created work-hardening using exponentmeasured from stiffness a set ofwith relationships indentation force using and a depth specific has been algorithm shown to to relate extract to the key material’s information elastic‐ from a singleplastic nanoindentation properties [23,24]. load-unload Solving these curve complex [20– dimensional22]. Another functions key contribution can be achieved is provided by making by the continuous-stian assumptionffness-measurement about the contact condition (CSM) method using a fromreverse the algorithm nanoindentation [21,24,25] or technique using an artificial where direct‐ measurementneural‐network of the tool material’s [26]. stiffness is made possible. Dimensional functions created using In this paper, a procedure to determine the contact area is presented by using a combination of measured stiffness with indentation force and depth has been shown to relate to the material’s the dimensional‐analysis approach and CSM. This is achieved by relating the contact area to elastic-plasticdimensional properties functions [ 23containing,24]. Solving stiffness these and complex other conventional dimensional nanoindentation functions can beparameters achieved by makingobtained an assumption from the load about‐unload the curve. contact The condition determined using contact a reverse area using algorithm the proposed [21,24 relationship,25] or using an artificial-neural-networkin this work is comparable tool [26 ].to those derived from a conventional methodology [1,27]. The Inmethodology this paper, proposed a procedure in this to determinework is considered the contact to be area an improvement is presented on by the using conventional a combination Oliver of the dimensional-analysisand Pharr method, approach where curve and fitting CSM. is Thisrequired is achieved to estimate by material relating stiffness. the contact In the area present to dimensional work, functionscurve containing fitting is no sti fflongerness andrequired other as conventional stiffness can nanoindentation be readily measured parameters by the CSM obtained method. from the load-unloadFurthermore, curve. the contact The determined area derived contact using the area dimensional using the‐analysis proposed approach relationship does not independ this workon is comparablethe shape to thoseof the derivedindentation from impression a conventional as prerequisite methodology information. [1,27]. Hence, The methodology it can be applied proposed to in materials with both a sink‐in and a pile‐up contact profile. this work is considered to be an improvement on the conventional Oliver and Pharr method, where curve2. fitting Theoretical is required Analysis to estimate material stiffness. In the present work, curve fitting is no longer required as stiffness can be readily measured by the CSM method. Furthermore, the contact area The continuous‐stiffness‐measurement method using nanoindentation can continuously derived using the dimensional-analysis approach does not depend on the shape of the indentation measure material stiffness along with indentation depth [1]. From the measured loading and impressionunloading as prerequisite responses, stiffness information. can be related Hence, to it indentation can be applied force to and materials depth, as with shown both in aEquations sink-in and a pile-up(1) contactand (2). profile.The gradient, represented by stiffness–depth and stiffness–force coefficients (Ch and Cf), 2. Theoretical Analysis The continuous-stiffness-measurement method using nanoindentation can continuously measure material stiffness along with indentation depth [1]. From the measured loading and unloading responses, stiffness can be related to indentation force and depth, as shown in Equations (1) and (2). The gradient, represented by stiffness–depth and stiffness–force coefficients (Ch and Cf), was observed Materials 2020, 13, 97 3 of 10 to be linear for isotropic
Details
-
File Typepdf
-
Upload Time-
-
Content LanguagesEnglish
-
Upload UserAnonymous/Not logged-in
-
File Pages10 Page
-
File Size-