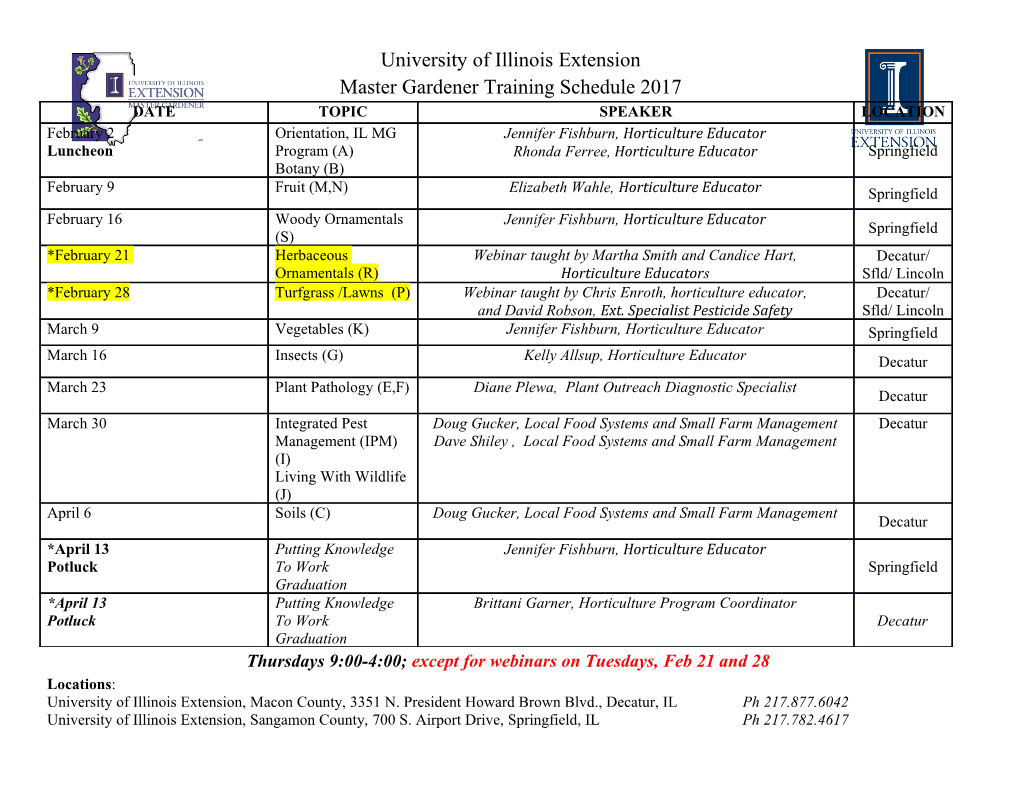
Force Image Cell Sensor BioMEMS Device Design Using PVDF Thin Film Thesis Presented in Partial Fulfillment of the Requirements for the Degree Master of Science in the Graduate School of The Ohio State University By Edward A. Meier, B.S. Graduate Program in Biomedical Engineering The Ohio State University 2012 Thesis Committee Professor Derek J. Hansford, Advisor Professor Yi Zhao Copyright by Edward A. Meier 2012 Abstract Researchers are predicting cancer will be the number one cause of deaths in the United States by 2030. Therefore, better methods of detecting and diagnosing cancer cells are required. Further research has shown that cancer cells act very differently than normal cells, and that these characteristics can be used to detect and diagnose certain cancers. One such characteristic is the force exerted by cells undergoing tumorigenesis. Polyvinylidene Fluoride (PVDF) has been of particular interest in recent years in bioMEMS devices because of its biocompatibility and piezoelectric properties. A device that takes advantage of PVDFs properties could measure these forces. Cellular force sensing can open new frontiers for diagnoses of diseases, better understanding of cellular mechanics, and a faster and less expensive than alternative methods of cellular force sensing. This thesis presents the development of a sensor based on a microstructured piezoelectric thin film on a CCD to measure these cell forces. First, a model was designed to show the feasibility of such a device. The model provided a theoretical range of forces that can be expected from the device. The model showed that each pillar would be capable of measuring forces from about 26fN/s to 100pN/s, which correlated with the forces measure by other cellular force sensors. Finally, a prototype ii device was created as a proof of concept. This device reacted to force stimuli and gave results that were expected. iii Dedication Dedicated to my mother, Debra. iv Acknowledgments I would like to thank Jeremiah Schley, Daniel Gallego-Perez, and Derek Hansford for their help in completing this project. v Vita 2003……………………………….. Greenville Senior High School 2008………………………………… B.S. Electrical Engineering Ohio Northern University 2008 to present………………. Master’s Degree in Biomedical Engineering Fields of Study Major Field: Biomedical Engineering vi Table of Contents Abstract ............................................................................................................................................ ii Dedication ....................................................................................................................................... iv Acknowledgments............................................................................................................................ v Vita .................................................................................................................................................. vi List of Tables ................................................................................................................................. viii List of Figures .................................................................................................................................. ix Chapter 1: Introduction: .................................................................................................................. 1 Chapter 2: Piezoelectricity ............................................................................................................. 14 Chapter 3: Theoretical Model of PVDF Pillar Force Sensor ........................................................... 23 Chapter 4: Experimental Methods ................................................................................................. 34 Chapter 5: Experimental Results .................................................................................................... 42 References ..................................................................................................................................... 50 vii List of Tables Table 1 Comparison of Force Sensors .................................................................... 13 Table 2 Bond lengths and bond angles of β-phase PVDF42 ................................ 20 Table 3 Ranges of the image sensor with an upper range at saturation of 100,000eV and lower range at the noise level of 15eV ...................................... 27 Table 4 Results from Model Design (a) Calculation of charge generated from single pillar; (b) Calculation of force sensitivity (slope of linear piezoelectric response); (c) Range of forces the sensor should be able to measure; (d) Range of forces per second for the sensor ............................................................. 32 Table 5 Cost benefit analysis of various types of CCDs ...................................... 39 viii List of Figures Figure 1 Cellasic’s microfluidic channels are passively driven which eliminates the need for pumps and motors.7 ............................................................ 3 Figure 2 Cellectricon High Quality Automated Patch Clamp: Left: wells are filled with buffer and compound, shown at left, and then pressurized with a lid; a patched cell is moved between the flows created by pressurizing the lid Right: shows the micro-channels from the wells to the patch-clamp8 ............... 4 Figure 3 Dynamic Array IFC showing microfluidic channels, chambers and valves and are reusable, decreasing costs9 ............................................................... 5 Figure 4 IonFlux works by pushing cells through the main channel where they get trapped and introduced to up to 8 compounds. Then, electrodes (circled above) are measured using a patch clamp to produce the data on the particular ion channels.10 .............................................................................................. 6 Figure 5 Sandia Labs silicon mirror and drive assemble (www.sandia .gov) .. 7 Figure 6 Sandia Labs MEMS device showing spider mite on gears (www.sandia.gov) ........................................................................................................... 7 Figure 7 Chemotherapy BioMEMS device that can control the release of the drug inside by heating up a coil16 ................................................................................ 9 Figure 8 Principle of magnetic twisting cytometry: the bead is magnetized in a known directions (Φ0), then the vertical magnetic field, H, twists the bead and the magnetometer records the change in magnetic field (B)35 .................. 10 Figure 9 From Harris, et al.: measurement of cell forces using a silicone rubber substrate being deformed by (a) single fibroblast cell and (b) cells spreading outward28 ................................................................................................... 11 ix Figure 10 From Rajagopalan, et al. linear high-resolution bioMEMS force sensor: shows large deflections in probe without large deflections in the beams.26 ......................................................................................................................... 12 Figure 11 From Ferrell, et al.: optical phase contrast image of polystyrene cantilever sensor at (a) 0min (b) 15min (c) 30min and (d) 45min shown prior to release of sacrificial layer. WS1 fibroblast cells are to be seeded into the middle of the device.27 ................................................................................................ 12 Figure 12 Perovskite structure: smaller cations of titanium and zirconium are surrounded by the larger cations of lead39 ..................................................... 15 Figure 13 Shows the effect of an electric field on a piezoelectric material (left) before applying the electric field V=n and (right) after applying the electric field V=n; shows an exaggerated effect of elongation (right) in the axis of poling on a material undergoing the poling procedure and the resulting orientation of the polar domains39 .......................................................................... 16 Figure 14 Matrices for piezoelectric materials: (a) elasticity matrix (b) dielectricity (c) piezoelectricity ................................................................................ 17 Figure 15 Crystal structure of α-phase PVDF41 .................................................... 19 Figure 16 Structure of β-phase PVDF (a) crystal structure showing distances between carbon chains (a and b); arrow indicates poling direction and (b) polymer chain diagram; arrow indicates poling direction42 .............................. 20 Figure 17 Side by side comparison of α-phase and β-phase PVDF; Note the difference in polarity and symmetry between the two ....................................... 21 Figure 18 Unit cell model of force sensor showing the individual layers and the direction of the applied force which will be a 1nN test force: The top layers are composed of PVDF connected to the silicon base of the CCD with wire glue conductive adhesive .................................................................................. 24 x Figure 19 Flat sheet of PVDF with force normal to the surface circuit diagram .......................................................................................................................................... 26 Figure 20 Wire Diagram showing the direction of the 1nN force in COMSOL; the lower arrows indicate that the unit is fixed on the bottom surface........... 28 Figure 21 Surface Charge Density
Details
-
File Typepdf
-
Upload Time-
-
Content LanguagesEnglish
-
Upload UserAnonymous/Not logged-in
-
File Pages68 Page
-
File Size-