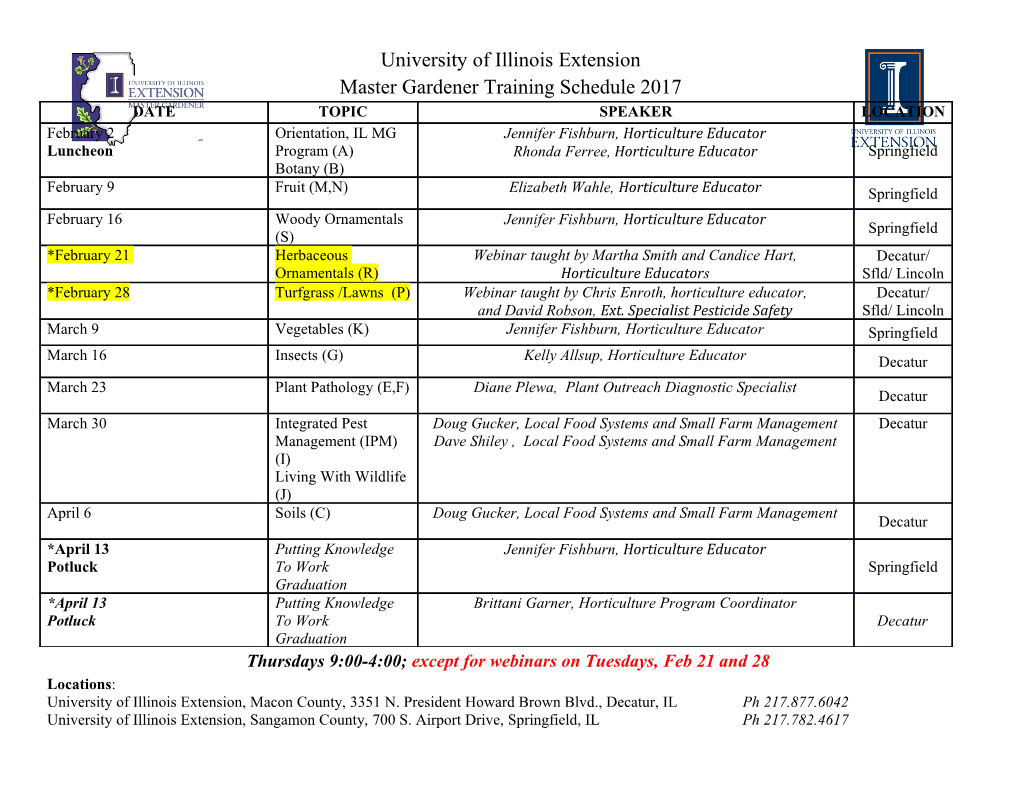
BIO-INSPIRED NACRE-LIKE CERAMIC MATRIX COMPOSITES by Jiacheng Huang APPROVED BY SUPERVISORY COMMITTEE: ___________________________________________ Majid Minary, Chair ___________________________________________ Dong Qian ___________________________________________ Yonas Tadesse ___________________________________________ Rodrigo Bernal Montoya Copyright © 2018 Jiacheng Huang All Rights Reserved To my family BIO-INSPIRED NACRE-LIKE CERAMIC MATRIX COMPOSITES by JIACHENG HUANG, BE, MS DISSERTATION Presented to the Faculty of The University of Texas at Dallas in Partial Fulfillment of the Requirements for the Degree of DOCTOR OF PHILOSOPHY IN MECHANICAL ENGINEERING THE UNIVERSITY OF TEXAS AT DALLAS December 2018 ACKNOWLEDGMENTS I would like to thank my doctoral mentor, Dr. Majid Minary, for his much appreciated financial support, workspace, and guidance throughout the course and research of my PhD work. I would also like to thank my committee members, Dr. Dong Qian, Dr. Yonas Tadesse and Dr. Rodrigo Bernal Montoya, for their suggestions and support. I am grateful for all my coauthors, collaborators, and colleagues that helped make this work possible. More importantly, I appreciate the continued support and encouragement from my family, especially, my wife Huiwen Shi. I acknowledge Dr. Zhe Xu (UTD), Seyed Soheil Daryadel (UTD), Dr. Ali Behroozfar (UTD), Seyed Reza Morsali (UTD), Salvador Moreno (UTD), Dr. Mahmoud Baniasadi (UTD), Dr. Xi Yang (UTD), Dr. Enlong Yang (Visiting Professor in UTD from JXU, China), Martha Serna (UTD), Dr. Tingge Xu (UTD), Xuemin Wang (UTD) , Dr. Winston Layne (Nanotech, UTD), Dr. Gordon Pollack, all cleanroom staff (UTD), Dr. Rajarshi Banerjee (UNT), Thomas W. Scharf (UNT) , William S Rubink (UNT), and Hunter Lide (UNT) for their insightful discussions, assistance with experimental equipment and computational simulations. November 2018 v BIO-INSPIRED NACRE-LIKE CERAMIC MATRIX COMPOSITES Jiacheng Huang, PhD The University of Texas at Dallas, 2018 Supervising Professor: Dr. Majid Minary, Chair Understanding the role of the ductile polymer phase in mechanical behavior of bioinspired hybrid composites is an important step toward development of materials with damage tolerant properties. In this dissertation,fabrication and characterization of a bioinspired lamellar composite by incorporation of a semicrystalline polymer into a freeze-casted scaffold is reported. The elastic modulus and ductility of the polymer phase can be changed by more than three and fifty five times, respectively, in addition to forty two folds decrease in modulus of toughness, by thermal annealing post-processing, after infiltration into the freeze-casted ceramic scaffold. The results show that although polymer phase affects the fracture toughness and flexural behavior of the composite, the drastic changes in mechanical properties of the polymer phase has only marginal effects on the resulted properties of the composite. In situ SEM experiments and finite element simulation were used to investigate the deformation mechanism and the effect of the polymer phase on the distribution of stress in the fabricated composites. Additionally, a metal-ceramic composite comprised of ~82 vol. % alumina (Al2O3) and ~18 vol. % nickel (Ni) was fabricated via co-assembly of alumina micro-platelets with Ni particles using the freeze-casting process followed by the spark plasma sintering (SPS). The SPS processing with vi a custom-designed temperature-pressure history resulted in formation of elongated Ni phase between the lamellar-ceramic phase. Results of the mechanical characterization showed that inclusion of Ni improveed the flexural strength of the composite by more than 47% compared to the lamellar ceramic. Additionally, the crack initiation (KIC) and crack growth toughness increaseed by 20% and 47%, respectively. The inclusion of softer Ni phase did not compromise the indentation modulus and indentation hardness of the composite compared to the pure ceramic. Infiltration of a molten metal phase into a ceramic scaffold to manufacture metal-ceramic composites often involves high temperature, high pressure, and expensive processes. Low-cost processes for fabrication of metal-ceramic composites can substantially increase their applications in various industries. In this disseration, electroplating (electrodeposition) as a low-cost, room- temperature process is demonstrated for infiltration of metal (copper) into a lamellar ceramic (alumina) scaffold. Estimation shows that energy consumption of this process is less than a few percent of the conventional molten metal infiltration process. Characterization of mechanical properties showed that metal infiltration enhanced the flexural modulus and strength by more than 50% and 140%, respectively, compared to the pure lamellar ceramic. More importantly, metal infiltration remarkably enhanced the crack initiation and crack growth resistance by more than 230% and 510% compared to the lamellar ceramic. The electrodeposition process for development of metal-ceramic composites can be extended to other metals and alloys that can be electrochemically deposited, as a low-cost and versatile process. vii TABLE OF CONTENTS ACKNOWLEDGMENTS .............................................................................................................. v ABSTRACT ................................................................................................................................... vi LIST OF FIGURES ....................................................................................................................... ix LIST OF TABLES ....................................................................................................................... xiii CHAPTER 1 INTRODUCTION .................................................................................................... 1 CHAPTER 2 EXPERIMENTS AND METHODS ......................................................................... 9 2.1 Fabrication and characterization of Lamellar Ceramic Semicrystalline-Polymer Composite .. 9 2.2 Fabrication and characterization of alumina-nickel composite .............................................. 14 2.3 Fabrication and characterization of Alumina-Copper Composite .......................................... 18 2.4 Experiment Calculation and simulation .................................................................................. 24 CHAPTER 3 LAMELLAR CERAMIC SEMICRYSTALLINE-POLYMER COMPOSITE FABRICATED BY FREEZE-CASTING..................................................................................... 28 3.1 Results and Discussion ........................................................................................................... 28 3.2 Conclusions ............................................................................................................................. 45 CHAPTER 4 ALUMINA-NICKEL COMPOSITE PROCESSED VIA CO-ASSEMBLY USING FREEZE-CASTING AND SPARK PLASMA SINTERING ...................................................... 47 4.1 Results and Discussion ........................................................................................................... 47 4.2 Conclusions ............................................................................................................................. 58 CHAPTER 5 MANUFACTURING OF METAL-CERAMIC COMPOSITE THROUGH INFILTRATION OF COPPER INTO FREEZE-CAST ALUMINA SCAFFOLD BY ELECTROPLATING ................................................................................................................... 60 5.1 Results and Discussion ........................................................................................................... 60 5.2 Conclusions ............................................................................................................................. 71 CHAPTER 6 OUTLOOK ............................................................................................................. 73 REFERENCES ............................................................................................................................. 76 BIOGRAPHICAL SKETCH ........................................................................................................ 82 CURRICULUM VITAE viii LIST OF FIGURES Figure 1.1. Illustration of the toughening mechanisms of in nacre [16]. .........................................2 Figure 2.1. Illustration of the vacuum infiltration process. Pictures of the samples before polymer infiltration, during polymer infiltration and after polymer infiltration. .............................10 Figure 2.2. A photo of the mechanical experiment under the optimal microscope. ......................12 Figure 2.3. The illustration of the freeze-casting setup and a photograph of the main parts of the freeze-casting setup. ...........................................................................................................15 Figure 2.4. The schematic of the sample cross-section for the electrodeposition process. Red arrows indicate that the deposition starts from the bottom of the ceramic scaffold all the way to the top and finally forms a copper cap at the top the scaffold. ..............................19 Figure 2.5. The illustration of the electrodeposition process. Copper ions flow freely through the ceramic scaffold until are deposited onto the conductive layer (the cathod) under the ceramic scaffold. ................................................................................................................21
Details
-
File Typepdf
-
Upload Time-
-
Content LanguagesEnglish
-
Upload UserAnonymous/Not logged-in
-
File Pages99 Page
-
File Size-