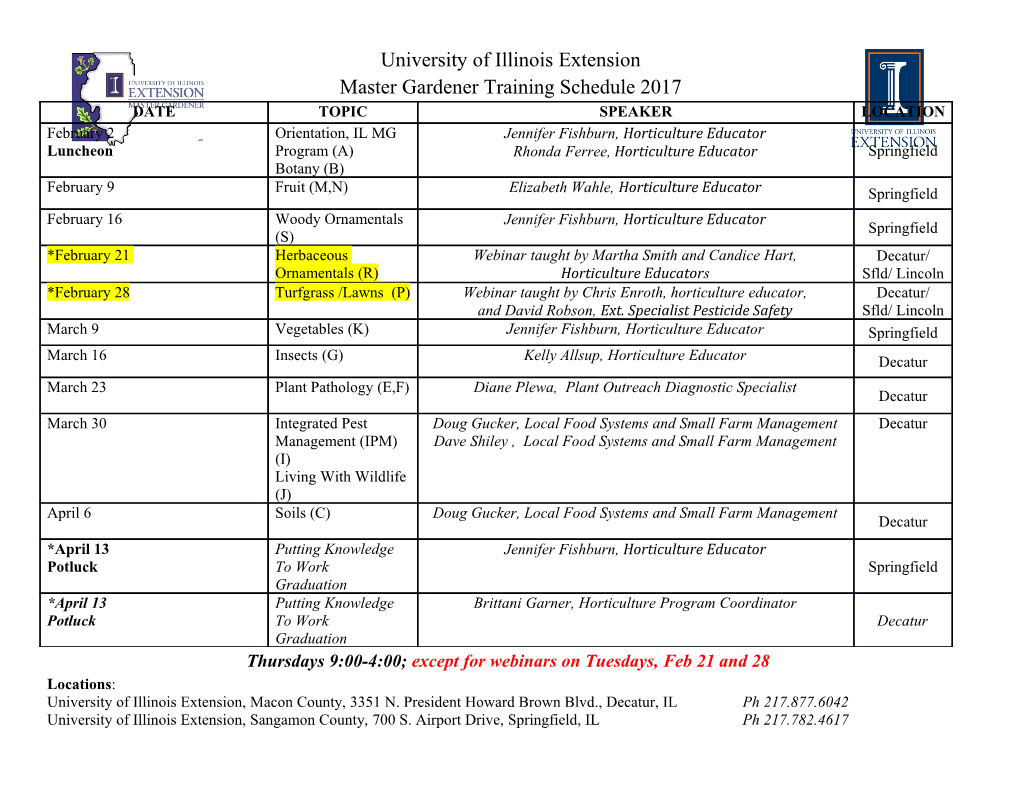
Optimal Motion of a Vertically Sculling Hydrofoil System for Efficient Propulsion and Power Extraction by Franck Jack Billarant Ing6nieur E.S.T.A.C.A. (Ecole Sup6rieure des Techniques A6ronautiques et de Construction Automobile) Titulaire d'une Maitrise de M6canique de la Faculte des Sciences et des Techniques de Nantes Submitted to the Department of Aeronautics and Astronautics in partial fulfillment of the requirements for the degree of MASTER OF ENGINEERING IN AERONAUTICS AND ASTRONAUTICS at the MASSACHUSETTS INSTITUTE OF TECHNOLOGY MASSACHUSETTS INSTITUTE June 2003 OF TECHNOLOGY @ Massachusetts Institute of Technology 2003. All rights reserved. SEP 1 0 2003 LIBRARIES P Author Department of Aeronautics and Astronautics May 9, 2003 Certified by. Professor Mark Drela Terry J. Kohler Professor of Fluid Dynamics Thesis Supervisor Certified by Professor Charles Boppe Senior Lecturer in Aeronautics and Astronautics Thesis Supervisor Accepted by V Edward M Greitzer H.N. Slater Professor of Aeronautics and Astronautics Chair, Committee on Graduate Students 2 Optimal Motion of a Vertically Sculling Hydrofoil System for Efficient Propulsion and Power Extraction by Franck Jack Billarant Submitted to the Department of Aeronautics and Astronautics on May 9, 2003, in partial fulfillment of the requirements for the degree of Master of Engineering in Aeronautics and Astronautics Abstract Autonomous Marine Vehicles (AMVs) provide an efficient and cost-effective platform to accomplish a variety of maritime tasks ranging from scientific data collection to underwater mine sniffing. Because of the multirole capabilities of these vessels, military establishments around the world have expressed interest in using AMVs to close the gap in mission performance and enhance mission capabilities. In order to be a viable alternative to the current operating methods, AMV military missions involving intelligence or surveillance/reconnaissance would need to be present on site for very long periods of time to cover large areas. However, currently, mission duration is greatly limited by available on- board power supplies. Typically, endurance of autonomous marine vehicles can be improved in three ways: through 1) drag minimization, 2) highly efficient means of propulsion, and 3) the real-time extraction of energy from natural sources. The goal of this work is to investigate a simple mechanical system to provide AMVs with all three of these attributes. The proposed system is based on a Vertically Sculling Hydrofoil (VSH) architecture, in which a horizontal wing of high aspect ratio plunges and pitches in the vertical plane. The wing provides lift to extract the hull of the vehicle to reduce wetted-surface friction drag and wave drag. The oscillation of the wing provides an efficient means of propulsion for the vessel in a way similar to birds or fish. Finally, energy can be extracted from an incoming flow by modulating the wing's incidence and damping the resulting heaving motion with an electric generator to produce power. When fitted on an autonomous marine vehicle, such a system could not only serve as a thruster but also as a means of replenishing the vehicle's power supplies to carry out long-endurance missions. For a deeply submerged flapping wing, the unsteady loads are identical to the loads generated by a wing flapping in the air. However, when the VSH wing approaches the free surface, the problem of determining the unsteady loads is greatly complicated as a transfer of momentum between the foil and the water surface coexists. Additional drag and lift-reducing forces emanate from this free surface influence. To characterize vertically sculling hydrodynamics, a two-dimensional unsteady panel method code was devised allowing for the calculation of the unsteady loads exerted by a heaving and pitching foil with the influence of a free surface. Using this computational tool, a series of calculations were carried out to predict the optimal foil motion in order to achieve maximum efficiency for propulsion and power extraction. Based on the results, design recommendations are given for a VSH system. Thesis Supervisor: Professor Mark Drela Title: Terry J. Kohler Professor of Fluid Dynamics Thesis Supervisor: Professor Charles Boppe Title: Senior Lecturer in Aeronautics and Astronautics 3 4 Contents Abstract 3 List of Figures 10 List of Tables 13 Nomenclature 15 Acknowledgments 22 1 Introduction 23 1.1 Introduction-Project Motivation .. ....... ....... ........ .... 23 1.2 VSH Description .... ..... ..... ...... ..... ........ .... 24 1.3 Previous Work ...... ..... ...... ..... ..... ............ 25 1.3.1 Theoretical and Experimental Work . ..... ..... ........ ... 25 1.3.2 VSH Vehicle Concepts ..... ..... ..... .... ... ........ 27 1.4 Statement of Project Objectives ... .... .... .... ... .... ........ 28 2 Vertical Sculling Hydrodynamic Model 30 2.1 Fluid Flow Governing Equations . 30 2.1.1 Continuity Equation ... .... 30 2.1.2 Conservation of Momentum 32 2.1.3 Flow Equation Summary . 33 2.2 VSH Model Assumptions ... ... .. 33 2.2.1 Perfect Fluid Assumption . .. 33 2.2.2 Foil Shape Assumption . .. 34 2.2.3 Foil Motion Assumption . .. 34 2.2.4 Wake Assumption .... ... 34 2.2.5 Free Surface Assumption ... 34 5 2.3 VSH Flowfield Idealization 35 2.3.1 Flowfield Modeling Using Vortex and Source Sheets . ....... ...... 35 2.3.2 Boundary Conditions in Time Domain .. ....... ....... ...... 35 2.4 Flowfield Solution Methodology ....... ....... ........ ....... 40 2.4.1 Fourier Expansion Approach ...... .......... ......... .. 40 2.4.2 Boundary Conditions in Frequency Domain .......... ......... 41 3 Numerical Implementation of Model 43 3.1 Numerical Solution Outline ... ........ ........ ........ ..... 43 3.2 User Inputs . ...... ....... ...... ....... ...... ...... .. 44 3.3 Discretization of the Geometry .. ...... ...... ...... ...... .... 44 3.3.1 Foil Discretization ....... ....... ....... ....... ..... 45 3.3.2 Wake Discretization ...... ......... ......... ........ 45 3.3.3 Free Surface Discretization .... ...... ...... ..... ...... 46 3.4 Panel Induced Velocities ... ...... ...... ...... ...... ...... 47 3.5 Residual Formulation .. .......... .......... .......... .... 49 3.5.1 Definition of Residuals . ....... ....... ....... ....... .. 49 3.5.2 System Matrix Setup .. ......... .......... ......... .. 50 3.6 Post processing - Load Evaluation .... .......... .......... .... 53 3.6.1 Vertical Force - Lift .. ......... .......... ......... .. 54 3.6.2 Horizontal force - Thrust ....... ....... ....... ....... 54 3.6.3 Pitching Moment . ............... .............. .... 55 3.6.4 Motion Power .. ............................ ...... 55 3.6.5 Coefficient Form .... .............. ............... 56 3.6.6 Efficiency Calculation .... .............. ............. 56 4 Model Validation 57 4.1 Infinite Depth Flows ............ ........................ 57 4.1.1 Steady Flow Validation ....... ....................... 57 4.1.2 Unsteady Flow Validation ............................. 58 4.2 Flows with Free Surface Effects ..... ........................ 61 4.2.1 Steady Flow Validation .............................. 61 4.2.2 Unsteady Flow Validation ........ .......... ......... .. 62 5 Computed Results and Design Implications 63 5.1 Computed VSH Results ............ .............. ........ 63 5.1.1 Influence of Design Parameters on Loads and Efficiency ............ 63 6 5.2 Foil Motion Optimization for Efficiency . ... 68 5.2.1 Optimization Problem Description .. 68 5.2.2 Optimization Results .. ... ... ... 70 5.3 VSH Design Implications .. ..... ..... 74 5.3.1 Interference Effects .. ..... ..... 74 5.3.2 Dynamic Foil Stall ... .... .... 75 5.3.3 Other Considerations ..... ..... 78 6 Summary, Conclusions and Recommendations for Future Work 79 6.1 Sum m ary ..... ..... ...... ..... ..... .... 79 6.2 Future Work ... ........ ........ .......... 79 A Analytic Panel Integrals 81 A. 1 Panel Influence Formulation ....... .... 81 B NACA 0012 Drag Polar 88 C Optimization Results - Propulsion 91 D Optimization Results - Power Extraction 110 Bibliography 119 7 8 List of Figures 1-1 Two-view of the Preposterous Pogo Foil.. ..... ....... ........ ..... 27 1-2 The inventor of the Trampofoil@ riding the craft. ....... ........ ..... 29 2-1 Flow regions in a high Reynolds number flow. .... ........ ....... .... 31 2-2 VSH flowfield idealization by means of vortex and source sheets. ............. 35 2-3 Chordline of the foil undergoing heaving and pitching displacements. All quantities posi- tive, as show n. .. .............. .............. .......... 36 2-4 Leading edge, pivot point and trailing edge trace of the foil undergoing a complex motion described by seven Fourier coefficients. The Fourier coefficients in this example are: 5 ho=O, hi =0.3, h2 =0.05, 0o=0, 01= , 02=2 and # 1 =135. ........ .. 40 3-1 Discretization of the foil, wake and free surface regions. .... .......... .... 45 3-2 Source strength distributions obtained with the control points located at: (A) 40% of panel length, and at (B) 50% of panel length. ........ .............. 47 4-1 Comparison of computed and analytical results for the -y-distribution on a flat plate. (N = 50 panels on the airfoil). ............... .............. 58 4-2 Comparision of computed and analytical results for the lift deficiency function C(k).(N = 50, M = 200 panels, nT = 30) .... .............. ............. 59 4-3 Comparison of computed and analytical results for the thrust coefficient in the case of: (A) a pure heaving motion (B) a pure
Details
-
File Typepdf
-
Upload Time-
-
Content LanguagesEnglish
-
Upload UserAnonymous/Not logged-in
-
File Pages119 Page
-
File Size-