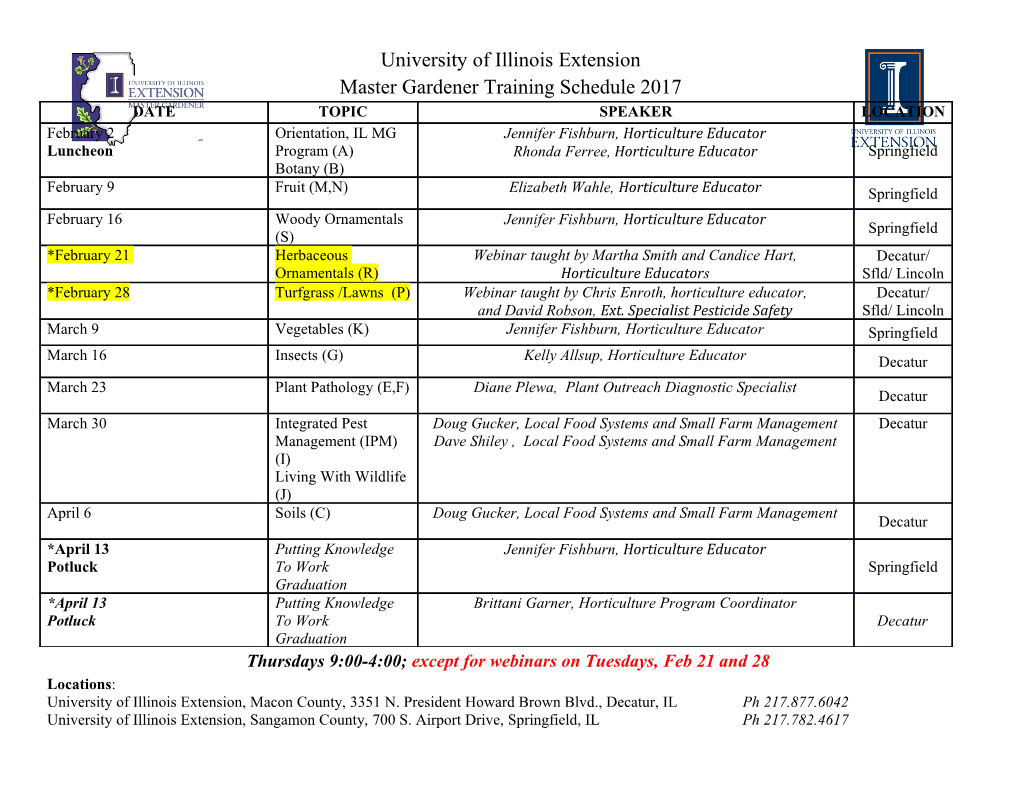
CO-DEFORMATION AND BONDING OF MULTI-COMPONENT BILLETS WITH APPLICATION TO Nb-Sn BASED SUPERCONDUCTOR PROCESSING DISSERTATION Presented in Partial Fulfillment of the Requirements for The Degree Doctor of Philosophy in the Graduate School of The Ohio State University By Xuan Peng ***** The Ohio State University 2005 Dissertation Committee: Approved by: Professor Mike Sumption, Advisor _________________________________ Advisor Professor Robert Wagoner, Advisor Department of Materials Science and Engineering Professor Katharine Flores Advisor Professor Glenn Daehn Department of Materials Science and Engineering ABSTRACT The standard procedure of the fabrication of low temperature superconductor precursors is the co-extrusion of composite materials followed by co-drawing. Defects including wire breakage and poor bonding between core and sleeve as well as between individual filaments are the main manufacturing problems. Understanding of interfacial bonding during the co-extrusion and co-drawing of the composites including the distributions of deformation, stress and temperature, and the generation process of interfacial bonding under different conditions will be helpful for the selection of parameters in the manufacture. First, the bonding created during the extrusion of subelements was examined and characterized using a focused ion beam (FIB) technique together with scanning transmission electronic microscopic (STEM) and the results confirmed that perfectly bonded subelements could be obtained by proper assembly, HIP, and subsequent extrusion. The second part of the work was aimed at the bonding generation during co-drawing process. Finite Element Method (FEM) was used to simulate the co-deformation process in order to investigate the effects of die angle, area reduction, core ratio, and the variation of bonding between components on the deformed geometry, and stress distribution in the ii product. The FEM simulation incorporated with a Pressure Bonding Model to study the generation process of interfacial bonding between components during the drawing process. This work starts with the multiple-pass drawing of a simple cylindrical monocore arrangement consisting of a Nb7.5%Ta core inside a Cu sleeve and a six- around-one restack of the monocores. The effect of the drawing pass, area reductions, die angles and core ratio on the deformation and bonding generation was investigated. On the experimental side, Cu-clad Nb7.5%Ta monocore "billet" was drawn to certain size, restacked into a Cu can to form a 7 restack multifilamentary billet, and then drawn to small size. High resolution scanning electron microscopy was used to observe the characteristics of the Nb7.5%Ta/Cu and Cu/Cu interfaces and mechanisms for the observed interfacial bonding were proposed. Furthermore, specially designed shear tests were carried out to determine the interfacial shear load. The results of these led to calculations of the interfacial shear stress (i.e. the bonding stress at the interfaces), the results of which were compared with the FEM predictions in order to establish the validity of the FEM model. iii DEDICATE TO MY BELOVED FAMILY iv ACKNOWLEDGMENTS I am sincerely grateful to a large number of people who have helped me throughout my study, research and daily life, and made my life in Columbus enjoyable. First of all, I would like to thank my advisors, Prof. Sumption, Prof. Collings and Prof. Wagoner for their guidance, instruction through my thesis work and other related research. I have learned much from them in both technical and non-technical aspects of life. I would also like to thank my family for supporting and encouraging me. I owe great appreciation to my husband, Xiangnan Wang, who is always behind me and support me. His understanding, encouragement and love helped me go through every obstacle and make my life here enjoyable and productive. I owe thanks to Mr. Mike Tomsic for introducing me to Hyper Tech Research Inc. and allowing me to do experiments there. Thanks John Philips and Kevin McFadden for helping me do the drawing experiments. I want to thank the support of staff members in Material Science Department. Lloyd Barnhart has been very helpful for mechanical tests. Henk Colijn and Cameron Begg taught me how to operate the SEM, XRAY, FIB and TEM machines. Their assistance is v very much appreciated. Christine Putnam is greatly appreciated for her administrative support. Finally, I would like to thank the cooperation, support, and friendship from all the members in LASM, Department of Materials Science and Engineering, The Ohio State University. vi VITA August 4, 1971. .Born – Shuangfeng, Hunan, China 1992. B.S in Metal Forming Northeastern University, Shenyang, China 1997. M.S in Metal Forming University of Science and Technology Beijing, China 2002. M.S. in Materials Science and Engineering The Ohio State University 1999 – Present. .Graduate Research Assistant The Ohio State University. PUBLICATIONS Research Publications 1. Sumption, M.D., Peng, X., et al., Fabrication and Phase-transformation Issues in CTFF-MA Processed A15 Superconductor, Adv. Cryo. Eng. 48B, 1057-1064 (2002). 2. Peng, X., Sumption, M. D. et al, FEM study of hydrostatic extrusion and bonding of superconductor precursors, IEEE Trans. Appl. Supercond. 13, 3434-3437 (2003). 3. Sumption, M.D., Peng, X., et al., Fabrication and properties of PIT Nb-Al and Nb- Sn based superconductors, IEEE Trans. Appl. Supercond. 13, 3486 -3489 (2003). 4. Peng, X., Sumption, M. D. et al, Finite Element Analysis of Extrusion of Multifilamentary Superconductor Precursor, Adv. Cryo. Eng., 50B, 425-432 (2004). 5. Sumption, M. D., Peng, X., et al, Magnetization and deff in HEP Relevant RIT Type Nb 3Sn Strands-Influence of Internal Barriers, Adv. Cryo. Eng., 50B, 836-843 (2004). vii 6. Sumption, M.D., Peng, X., et al., Analysis of magnetization, AC loss, and deff for various internal-Sn based Nb 3Sn multifilamentary strands with and without subelement splitting, Cryogenics, 44(10), 711-725 (2004). 7. Peng, X., Sumption, M. D. et al, Finite Element Analysis of Drawing of Multifilamentary Wires, to be published in IEEE Trans. Appl. Supercond 8. Peng, X., Sumption, M. D. et al, Microstructural Investigation of Internal-Tin Nb 3Sn Strands, to be published in IEEE Trans. Appl. Supercond 9. Peng, X., Sumption, M. D. et al, Magnetization and deff in Multifilamentary Nb 3Sn Strands, to be published in IEEE Trans. Appl. Supercond 10. Wu, X., Peng, X., et al, Ti and Sn Diffusion and Its Influence on Phase Formation in Internal –Tin Nb 3Sn Superconductor Strands, to be published in IEEE Trans. Appl. Supercond 11. Peng, X., Sumption, M. D. et al, Investigation of Bonding Generation during the Drawing of Multifilamentary wires, under review for the publication in Adv. Cryo. Eng. 12. Peng, X., Wu, X., Sumption, M. D. et al, Characterization of Ti and Ta Influence on Grain Shape and Size, as well as Transport Properties of Conductors Fabricated by the Internal-Sn Process, under review for the publication in Adv. Cryo. Eng. FIELDS OF STUDY Major Field: Materials Science and Engineering viii TABLE OF CONTENTS P a g e Abstract. .ii Dedication. .iv Acknowledgments . v Vita . .vii List of Tables. .. .xiii List of Figures . .xiv 1. INTRODUCTION ........................................................................................………... 1 2. BACKGROUND REVIEW.......................................................……………….……..5 2.1 Fabrication of Nb 3Sn superconductor precursors.................................................….6 2.1.1 Fabrication Methods ...................……………………...............................…6 2.1.2 Fabrication Challenges...................……………………..........................….13 2.1.3 Summary................……………....……………………..........................….14 2.2 Co-deformation of Bi-metallic and Multi-metallic Composite Wire........………..14 2.2.1 Forming Process................……………....……………………...............….16 2.2.2 Bonding Generation................……………....………..………...............….29 2.2.3 Summary................……………....……………………..........................….32 ix 2.3 Objective and Format of this Document………....……………………............…..34 3. LITERATURE REVIEW ON SOLID BONDING....................…................……...36 3.1 Main Solid State Bonding Processes and its Application........................................36 3.1.1 Diffusion Bonding...........................……………….......................................37 3.1.2 Explosive Bonding...........................……………….......................................39 3.1.3 Friction Bonding...........................……………….........................….............41 3.1.4 Ultrasonic Bonding...........................…...………….......................................43 3.1.5 Cold Pressure Bonding....................……………….......................................45 3.2. Characterization of Interfacial Bonding..................................................................45 3.3 Summary................……………....……………………..........................………....55 4. BONDING GENERATION DURING CO-EXTRUSION OF SUBELEMENTS ..........................……………………………………………………..56 4.1 Experimental Procedure..........................................................................................57 4.1.1 Subelements Construction..............................................................................57 4.1.2 FIB Technology for Underlying Interface Observation and Sample Preparation.....................................................................................……………......60
Details
-
File Typepdf
-
Upload Time-
-
Content LanguagesEnglish
-
Upload UserAnonymous/Not logged-in
-
File Pages202 Page
-
File Size-