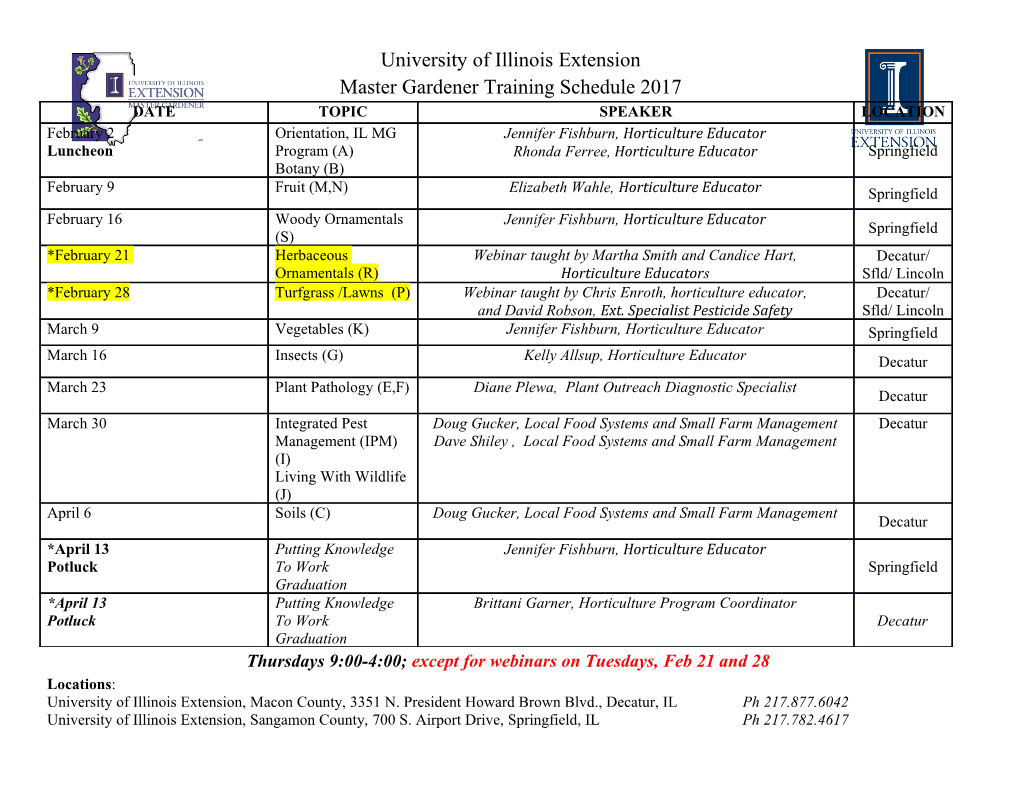
h * -' . 1 TUTKIMUSRAPORTTEJA FORSKNINGSRAPPOR TER RESEARCH REPORTS t Des ulph urization in peat-fired circulating and bubbling fluidized bed boilers ---- 6* Petri Kouvo @/ Keijo Salmenoja e*@ &@Y@ 4 DISCLAIMER Portions of this document may be illegible electronic image products. Images are produced from the best available original document. DES U LPH URlZATl 0 N I N PEAT- FI RE D CIRCULATING AND BUBBLING FLUIDIZED BED BOILERS PETRI KOUVO IMATRAN VOIMA OY IVO TECHNOLOGY CENTRE KEIJO SALMENOJA KVAERNER PULPING OY Published by Code IMATRAN VOIMA IVO-A-06/97 OY Date Name of project DesulDhurization in Deat-fried circulating and bubbling fluidized bed boilers Authors Commissioned by Petri Kouvo IMATRAN vowOY Keijo Salmenoja I Title DESULPHURIZATION IN PEAT-FIRED CIRCULATING AND BUBBLING FLUIDIZED BED BOILERS Abstract The new emission limit values for large combustion plants are under consideration both at the EU level and in Finland. Peat and wood are the only indigenous fuels of Finland. In 1995 appr. 8 8 of electricity was produced with peat. The lower heating value of peat is around 10 hWkg. The moisture content varies between 35-55 % and sulphur content in dry solids between 0.15-0.35 %. The total peat power capacity of Finland in 1995 was 1400 MW. Because there was not enough information available about the desulphurization of the flue gases from peat-fired fluidized bed boilers, a group of Finnish companies and Ministry of Trade and Industry decided to carry out the full-scale desulphurization study. In project the desulphurization with limestone injection into the furnace of two types of peat-fired boilers were studied. The goal of the project was to investigate -what the technically and economically feasible emission level is reachable by limestone injection in the fluidized bed combustion -how the limestone injection affects the other flue gas emissions and the fouling of the boiler and, -what the economy of desulphurization is. The tests were carried out at Kokkola and Kemi power plants in Finland. At Kokkola (108 MWf)circulating fluidized bed boiler, the emission limit of 200 mg/m3n was reached at a CdS-molar ratio of appr. 10, with limestone containing 92 8 of calcium carbonate, CaC03. At Kemi (267 MWf) bubbling fluidized bed boiler, the emission limit of 280 mg/m3n with limestone containing appr. 95 8 of CaCO3 was reached at a CdS-molar ratio of appr. 7.0. Emissions of NOx, N20, NH3 and dust after the ESP were not elevated due to the limestone feed. At the Kokkola power plant the NOx emissions varied from 300 to 400 mg/m3n, and, at the Kemi power station the NOx emissions were around 200 mg/m3n. The fouling of the Kemi boiler was found to be significant in the scheduled outage after the test period. The Kemi boiler was fii with waste sludges and bark between the test runs. This has most likely caused the fouling in the boiler. At the Kokkola power plant, the indications of fouling were not observed during or after the test. In both Kokkola and Kemi cases, the runs with the emission levels of 200 and 280 mg/m3n respectively about doubled the amount of the produced fly ash. The handling of the fly ash was aggravated because of the high free calcium oxide content. In the case of Kokkola power plant the desulphurization costs at the emission level of 360 mg/m3n (140 mgMJ, current emission level), are 7 900 FIW removed SOz tonne. At the emission level of 200 mg/m3n (appr. 77 mg/UT) the cost is 10 800 FIWremoved SOz tonne. The marginal cost of the desulphurization (360->200 mg/m3n) in Kokkola case is 12 600 FIWremoved SO2 tonne. In the case of Kemi power plant at the emission level of 360 mg/m3n, the cost is 8 400 FIWremoved SO2 tonne and at the emission level of 280 mg/m3n (the reached emission level), the cost is 11 600 LlhWremoved SO2 tonne. The marginal cost (360->280 mg/m3n) is 16 100 FIWremoved SO2 tonne. A calculation was also made for the Semi-Dry desulphurization method for both boiler type at the emission level of 200 mg/m3n. The costs for the Kokkola plant is 40 300 FIWremoved SOz tonne and for the Kemi power plant 19 OOO FIWremoved SOz tonne. The limestone price used in the calculations was 270 FIhWtonne at the site. ISBN Language [SBN 951-591-054-4 English Number of pages Confidentiality 25 Public Distributed by price- MATRAN VOIMA OY NO Technology Centre Tel. +358 9 856 11 01019 Ivo Telefax +358 9 563 2225 FINLAND FOREWORD Desulphurization in Peat-fired Circulating and Bubbling nuidized Bed Boilers project has been executed by Imatran Voima Oy (NO), a Finnish power company and Kvaerner Pulping Oy. Mr Ilari Ekman MSc (Eng) of NO has acted as the director of the project. Mr Petri Kouvo MSc (Eng) of IVO and Mr Keijo Salmenoja of Kvaerner Pulping Oy have acted as the project engineers. The members of the Management Group have been: Ms Sirpa Salo-Ashinen, Minis- try of the Environment; Mr Seppo Oikarinen, Ministry of Trade and Industry; Mr Birger Ylisaukko-oja, Pohjolan Voima Oy; Mr Matti Hiltunen, Foster wheeler Ener- gia Oy; Mr Juha Sarkki, Foster Wheeler Energia Oy; Mr Markku Miettinen, VAPO Oy; Ms Maija Vihma, Partek Nordkallr Oy Ab; Mr Seppo Partonen, NO. The Chair- person of the Management Group has been Ms Leena Nurmento of NO’SEnviron- mental Protection Division. The project has been financed by: Ministry of Trade and Industry, Foster Wheeler En- ergia Oy, Kvaerner Pulping Oy, VAPO Oy, Partek Nordkalk Oy Ab, Pohjolan Voima Oy and Imatran Voima Oy. June, 1997 Imatran Voima Oy DESULPHURIZATION IN PEAT-F'IRED CIRCULATING AND BUBBLING FLUIDIZED BED BOILERS ABSTRACT FOREWORDS 1. BACKGROUND.................................................................................................................................. 5 2 . OBJECTIVES ...................................................................................................................................... 6 3 . THEORY OF DESULPHURIZATION ............................................................................................... 6 4 .FLUIDIZED BED COMBUSTION..................................................................................................... 7 4.1 DESULPHURIZATIONINFLUIDIZED BED BOILERS .................................................................................. 9 5. KOKKOLA POWER PLANT ..... .................................................................................................... 10 5.1 THFi TEST PROGRAM FOR KOKKOLAPOWER F'LANT ........................................................................... 11 5.2 MEASUREMENTS.SAMPLES AND ANALYSES ...................................................................................... 12 5.3 PEAT QUALITY AND PROCESS VALUES ............................................................................................... 13 5.4 TEST RESULTS ................................................................................................................................... 14 5.4.I CalS-ratio and the desuEphurizution rate ................................................................................. 14 5.4.2 Desulphurization and the bed temperature .............................................................................. 16 5.4.3 Desulphurization and the combustion air distribution ............................................................. 16 5.4.4 NOx emission and the limestone injection................................................................................ 16 5.4.5 N20emission ............................................................................................................................ 17 5.4.6Dust load .................................................................................................................................. 17 5.4.7 Fouling of the boiler ................................................................................................................. 18 6 . KEMI POWER PLANT ..................................................................................................................... 18 6.1 THE TESTPROGRAM FOR KEMIPOWERPLANT ................................................................................... 18 6.2 MEASUREMENTS,SAMF'LES AND ANALYSES ...................................................................................... 19 6.3 PEAT QUALITY AND PROCESS VALUES ............................................................................................... 20 6.4 TESTRESULTS................................................................................................................................... 21 6.4.1 CdS-ratio and the desulphurization rate ................................................................................. 21 6.4.2 NO, emissions and the limestone injection............................................................................... 23 6.4.3 NH, emission ............................................................................................................................ 23 6.4.4 N20 emission ............................................................................................................................ 23 6.4.5 Effect of limestone injection on the dust load ........................................................................... 23 6.4.6 Fouling of the boiler ................................................................................................................. 24 7. TIE COST OF DESULPHURIZATION .......................................................................................... 25 8. UTILIZATION OF THE END PRODUCT (FLY ASH) ..................................................................
Details
-
File Typepdf
-
Upload Time-
-
Content LanguagesEnglish
-
Upload UserAnonymous/Not logged-in
-
File Pages48 Page
-
File Size-