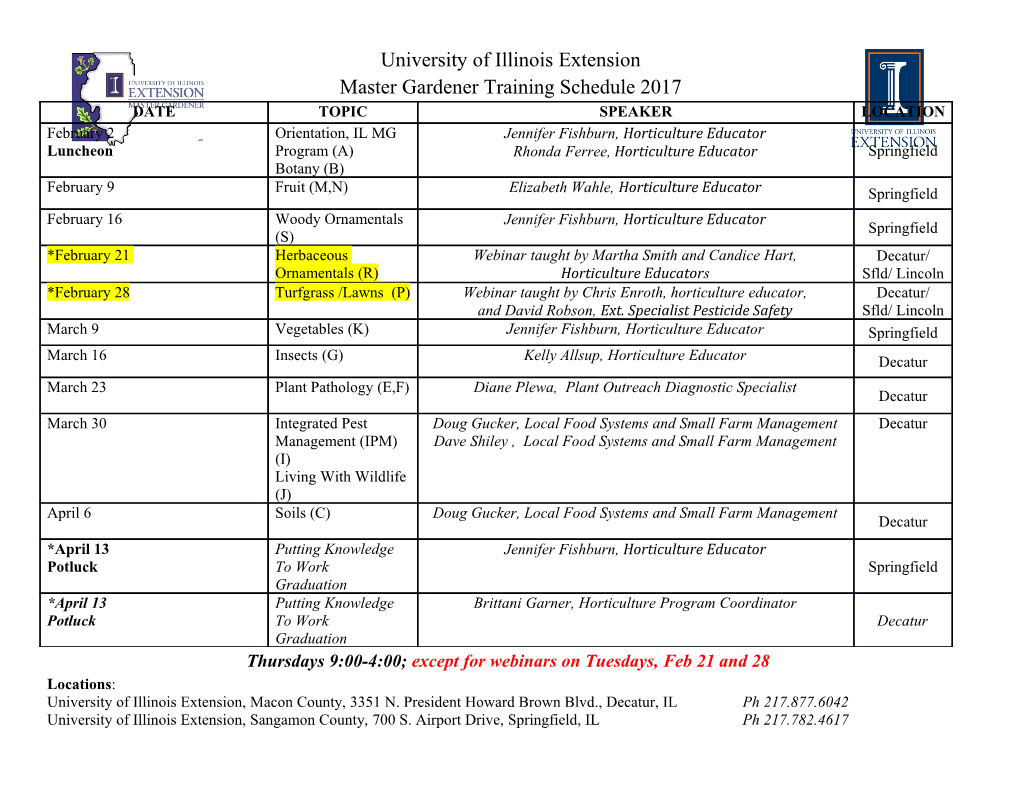
MAY 2002 / VOLUME 54 / NUMBER 5 ❿ BY BILL KENNEDY, CONTRIBUTING EDITOR cover story A look at recent advances in tap technology. What’s on Tap? Emuge orkpiece material char- thread flank is very high. The tap has to Hill said the major variable in creating acteristics. Tool design. contain or dispose of the chip it gener- material-specific taps is the geometry W Machine tool capabili- ates while producing a thread to precise of the cutting edges. Specifically, their ties. Speeds and feeds. As with any finish size. It’s a severe environment.” rake angle and amount of hook. metalcutting operation, these basic Tap manufacturers address multiple Rake is the inclination of the cutting process elements must be considered aspects of that environment in an on- edge, and hook is its degree of radius when tapping a thread. going effort to boost productivity. or curve (Figure 1). For tough-to-ma- But Dan Gajdosik, engineering man- chine materials, rake angles and hook ager for tapmaker Besly Products Material-Specific are generally lower, to strengthen the Corp., South Beloit, Ill., said tapping The machinability of the workpiece cutting edge and counter the high is, in many respects, the “most diffi- material is probably the key determi- torque needed to cut the threads. In cult of all machining” operations. nant of tapping performance. Vernon hard materials, too much hook or rake “The chip load per tooth on a tap is Hill, design engineer for The Hanson- can cause a tap to break. Furthermore, much higher than most cutting tools,” Whitney Co., Windsor, Conn., said Hill said, “if you have too much hook, he explained. “The tap is almost buried tapmakers are focusing on developing it can grab and tear the threads.” in the workpiece, and contact along the tools for specific workpiece materials. On the other hand, long-chipping materials require a steeper rake angle and hook, which curl and break the chip. The more acute angles result in a weaker cutting edge. Another material-dependent geomet- ric factor is the relief angle, or the clear- ance between the tap’s flute and the hole’s wall. Harder materials require more relief to reduce friction and per- Illustrations: Allen Benjamin mit coolant to reach the cutting edge. Figure 1: Rake is the inclination of the cutting edge, and hook is its degree of radius But larger relief angles offer less of a or curve. self-centering capability as the tap en- ters the hole. In soft materials, too much relief can result in oversize threads. Harder and tougher materials may require full ec- centric relief, which begins at the cut- ting edge. Con-eccentric relief, appro- priate with less-difficult-to-machine materials, features an unrelieved mar- gin behind the cutting edge followed Figure 2: Harder, tougher materials may require taps with full eccentric relief to reduce by an angle of relief (Figure 2). friction. Taps for less-difficult-to-machine workpieces can employ con-eccentric relief. Spiral-flute taps designed to thread blind holes in tough-to-machine mate- of the machine tool,” he said. carbide taps are beginning to thread rials have lower flute helix angles, to With smaller taps, the spindle speed more holes. improve structural strength. For exam- required to achieve the desired surface Carbide, traditionally, had problems ple, Hanson-Whitney’s ULTI-XT spi- speed [rpm = (sfm ✕ 3.82)/tap diameter] handling the high chip loads of tapping ral-flute taps for tougher 400-series may be beyond the spindle’s rpm ca- because the material, while very hard, stainless steels feature 15° flutes, while pacity. On the other hand, attaining is also more brittle than HSS. Even so, the company’s ULTI-XT 300 taps for high speeds with larger taps may re- carbide taps are proven performers in 300-series stainless have 41° flutes quire greater tapping torque and horse- materials such as cast iron and alu- (Figures 3a, 3b). power than the machine can provide. minum, where the main failure mecha- In addition, taps for tough-to-ma- “Where we might achieve 250 sfm nism is wear. chine materials often have a shorter with a 700-psi through-coolant tool, a Amy Haywood, general manager of thread length. This reduces the amount machine without through-coolant Allen Benjamin Inc., Tempe, Ariz., of torque required in the cut. Materials might only be capable of 150 sfm,” said: “Automotive manufacturers use with elastic memory, such as titanium, Shepherd said. “A tap, unlike most carbide for the longevity, because call for tools with greater back taper, or metal-removal tools, has an enormous they’re machining a lot of aluminum decreasing tool radius from tip to surface area that comes in contact with and cast iron. A carbide tap will long shank. The taper minimizes friction on the wall of the hole. Therefore, lubri- outlast a HSS tap in those materials. the shank as the material “springs cation is important. If you overheat Much of it depends on the end user’s back” after machining. high-speed steel, the tool breaks down application and what they are trying to When attempting to optimize tap per- and burns up.” achieve in the long run. In the automo- formance, tapmakers also consider Newer high-performance taps are de- tive industry, downtime to change taps other factors than just the tool. signed to take maximum advantage of is obviously a factor.” The long life of Alan Shepherd, technical director for a machine tool’s spindle speed and carbide taps minimizes tool changes. Emuge Corp., Northborough, Mass., horsepower. The geometries of Development of submicron-grain car- said newly developed high-perform- Emuge’s line of high-performance taps bide substrates has produced tools that ance taps can cut significantly faster feature “higher rates of relief and offer significantly increased toughness than traditional tools. “In tapping cast higher back taper,” Shepherd said. without sacrificing carbide’s wear-re- iron, previously you might have run at And edge configurations are match- sisting hardness. Haywood said these 35 to 50 surface feet per minute, but ed with a specific surface coating, such tools extend tool life, compared to HSS the new taps enable you to tap as fast as as TiN, TiCN, CrN or TiAlN. These tools, when cutting hardened steels, 250 sfm,” he said. heat-resistant and lubricious coatings plastics and difficult-to-machine nickel- He pointed out, though, that the extend tool life, reduce cutting forces base aerospace alloys. The company upper limits of performance can be re- and permit higher cutting speeds. says its PRX-series taps, under certain alized only with a certain range of taps conditions, have been able to thread and machine tools with specific capa- Carbide Rising more than 200 holes in Inconel 718 be- bilities. “The most productive speeds Just as carbide tools gradually re- fore they require resharpening. are sometimes limited by the capacity placed the HSS tools used for turning, According to Gene Delett, national sales manager for Regal Cutting Tools, South Beloit, Ill., carbide taps comprise Rigid rules of tapping one of the fastest growing markets for his company’s products. “The new mi- achining faster with the same—or greater—level of accuracy is always de- crograin carbides are suitable for some M sirable. But achieving the desired results requires use of the proper machine. general machining,” he said. “You can When it comes to high-speed threading, Pete Kainovic, machining center prod- run five or six times faster, and tool life uct manager for Okuma America Corp., Charlotte, N.C., said there are two classes can be 100 times greater. The cost is of machines that are commonly used. First is the small, dedicated CNC drilling and obviously many times that of a stan- tapping machine, such as those produced by Brother Industries, designed only to dard HSS tool, but the payback is drill and tap small-diameter holes. These machines feature CAT 30 spindles, which greater than the payout, especially in operate at extremely high acceleration and deceleration rates, and CNCs optimized high-volume situations such as auto- for tapping. Some permit tapping at speeds of 6,000 rpm or higher. motive.” Kainovic also said that much of the threading performed today takes place on Haywood added that “a lot of oper- machining centers, employing synchronized, or “rigid,” tapping cycles. When rigid ations, like hand tapping, aren’t cor- tapping, the machine’s CNC synchronizes the spindle speed and Z-axis ballscrew. rect for carbide.” But with the advent Rigid tapping contrasts with non-CNC tapping processes, which require taps to of synchronous tapping (see sidebar, be held in nonrigid, or floating, holders to compensate for differences between page 31) and strong fixturing, carbide the machine tool feed and the thread’s lead. taps are a valid option for a growing Float is necessary because a tap’s feed must equal its lead. For example, a 1/4- range of materials and applications. 32 tap has 32 threads per inch (the tap advances 1" every 32 revolutions). Before David Miskinis, technical specialist present-day CNC technology, precisely matching machine feed and tap lead was- with Greenfield Tap and Die/Ken- n’t possible. Tap chucks, therefore, were designed with springs that permitted axial nametal Greenfield IPG, Evans, Ga., float, enabling the tap to feed exactly at its lead rate. agreed that state-of-the-art taps feature Kainovic said Okuma, like most machine tool builders, offers machining centers “bodies of premium steel, powder with standard rigid-tapping programs that synchronize the spindle speed with Z- metal or carbide, are coated, and have axis movement to exactly match the tap’s lead.
Details
-
File Typepdf
-
Upload Time-
-
Content LanguagesEnglish
-
Upload UserAnonymous/Not logged-in
-
File Pages5 Page
-
File Size-