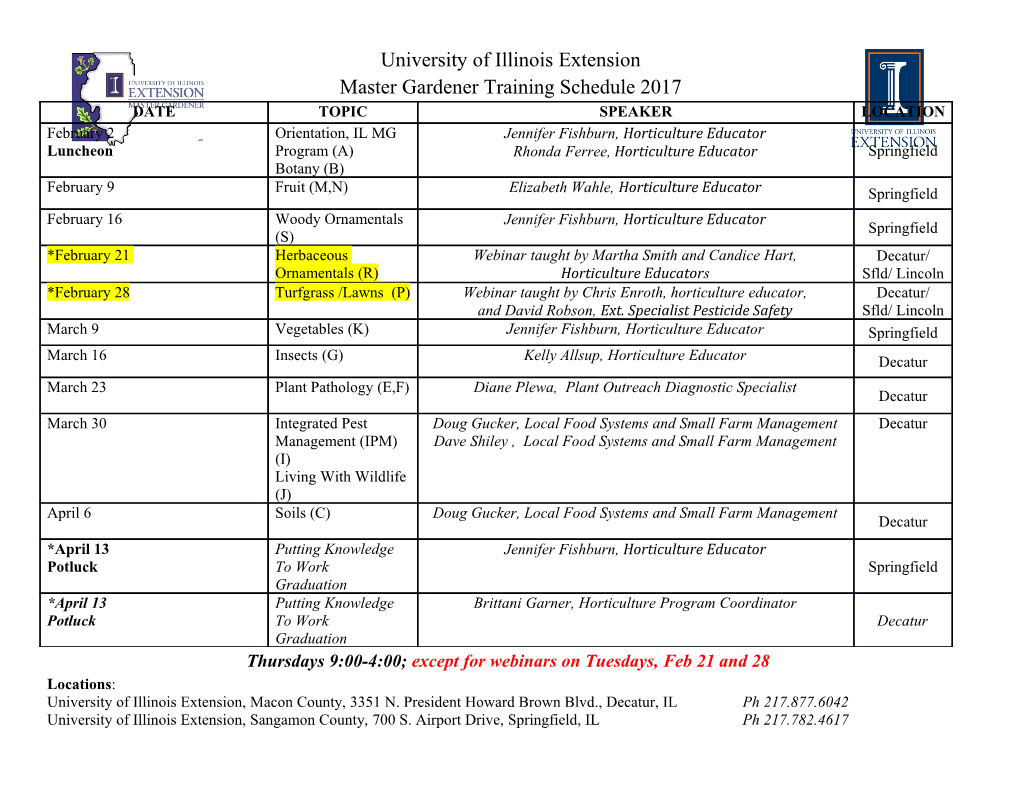
Int J Adv Manuf Technol (2013) 67:2259–2267 DOI 10.1007/s00170-012-4647-5 ORIGINAL ARTICLE Optimisation of CNC routing operations of wooden furniture parts Tomasz Gawronski´ Received: 21 May 2012 / Accepted: 13 November 2012 / Published online: 20 December 2012 © The Author(s) 2012. This article is published with open access at Springerlink.com max Abstract The aim of this paper is to develop mathemat- fT maximum feed rate available for selected tool, max ical model and computational procedure for optimisation fM(x) maximum feed rate available at machine along of feed rate at CNC routing operations of wooden furni- Xaxis, max ture parts. The proposed approach takes into consideration fM(y) maximum feed rate available at machine along special characteristics of solid wood, like changes in cut- Yaxis, max ting forces and obtained surface quality along with cutting fM(z) maximum feed rate available at machine along direction. A multistage optimisation procedure is devel- Zaxis, oped, which employs binary search method and genetic Fi unit feed vector at micro-segment i, algorithm. Because of the problem of full specification of g chip thickness, feasible region in the form of inequalities, a fuzzy logic i index of micro-segment, is used for correction of intermediate results within com- j index of final segment, putational procedure. The developed method is verified by Ji binary decision variables for joining of micro- optimisation of routing operation of a typical furniture part, segments, i.e. commode top. As a result of optimisation, the processing lj length of final segment j, time is reduced by 54 %. n number of micro-segments, n number of final segments, · · · Keywords Furniture CNC routing Optimisation n number of initial segments, · 0 Wood Processing time P machine’s main motor power, p penalty function, Notation q fitness function, Si micro-segment i, Ai cross section area of layer or profile being cut at t processing time, micro-segment i w cutting width, = ck correction coefficients (k 1,...,7) for κ , Wi component of wood fibre vector in the direction = ck# correction coefficients (k 1,...,7) for κ#, within cutting plane perpendicular to cutting edge, ⊥ = ⊥ ck correction coefficients (k 1,...,7) for κ , Wi# component of wood fibre vector in the direction fi feed rate at micro-segment i, along cutting edge, fi optimised feed rate at micro-segment i, Wi⊥ component of wood fibre vector in the direction perpendicular to cutting plane, fi feed rate after correction at micro-segment i, α code size ratio, fj feed rate at final segment j, β penalty function coefficient, γ1 strength of membership function for do-not-slow- T. Gawro´nski ( ) down action, Department of Furniture Design, Pozna´n University of Life Sciences, Wojska Polskiego 28, 60-637 Pozna´n, Poland γ2 strength of membership function for slow-down e-mail: [email protected] action, 2260 Int J Adv Manuf Technol (2013) 67:2259–2267 δi feed per tooth at micro-segment i, 28]. All of above cited papers involve numerical optimisa- f assumed accuracy of determination of fi, tion which is done prior to the processing of parts, so all ε tool attack angle, processing parameters and processing times are known in η mechanical efficiency of machine’s main drive, advance. κi specific cutting power at micro-segment i, On the contrary, there are no published research that κ specific cutting power for typical cutting conditions address similar issues in case of solid wood processing. along wooden fibres, Moreover, because solid wood is a highly anisotropic mate- κ# specific cutting power for typical cutting conditions rial of specific fibrous structure, most of the methods across wooden fibres, developed for metalworking optimisation cannot be easily κ⊥ specific cutting force for typical cutting conditions adopted. Some papers in this field applicable to furniture perpendicular to wooden fibres, industry are [17, 20], which assume medium-density fibre- B μϕc membership function of fuzzy set bad cutting edge board as material to be processed. In the area of solid wood direction angle, processing, numerical optimisation has been proposed for B μϕf membership function of fuzzy set bad feed direc- through feed operations like ripsawing and four-side plan- tion angle, ning [8]. However, because of constant feed rate and feed G μϕc membership function of fuzzy set good cutting edge direction, through feed operations are much simpler than direction angle, CNC operations. There are promising solutions dedicated G μϕf membership function of fuzzy set good feed direc- to CNC operations in solid wood working [6, 10], which tion angle, involve on-line feed rate adaptation based on monitoring of ϕc angle between cutting edge and wood fibres, acoustic emission. While, generally, on-line adaptation of ϕf angle between feed direction and wood fibres. processing parameters may outperform ahead-of-time opti- misation, it also has some significant drawbacks. First of all, it requires additional monitoring equipment and mod- 1 Introduction ification of CNC control system. Moreover, if a company uses enterprise resource planning software, the process- In modern furniture industry, CNC working centres are ing times should be known in advance. Another approach widely used, especially when high quality of product and involves experimental determination of optimal machining flexibility of manufacturing process are expected. Even parameter for particular wood species, equipment and parts though there are many advanced computer-aided manufac- to be processed [22, 26]. However, the application of that turing systems for furniture producers, some technological approach is very limited when the above conditions change parameters, like feed rates, must still be established arbi- frequently. trarily. It seems that, in case of sophisticated solid wood The above literature review indicates the need for furniture parts, there is general tendency to use low feed research on CNC operation optimisation dedicated to solid rates to guarantee high quality and to be sure that machine wood furniture production. Among routing and turning and tool limitations are satisfied. These practices are not operations, the former seems to be more popular in the always rational because of high processing times and, as a furniture industry, and, therefore, it should be of primary consequence, high manufacturing cost. Therefore, there is interest in the research. a need for an optimisation software that would allow for The aim of this paper is to develop mathematical model reduction of processing times under proper technological and computational procedure for optimisation of feed rate conditions. at CNC routing operations of wooden furniture parts. The The problem of CNC operation optimisation in metal- proposed method is designed to apply modification to CNC working has been well explored in the literature. Many programme, before actual processing of parts, without the researchers concentrate on the determination of optimal cut- need for further on-line readjustments. ting speed and feed rate at milling [1, 21, 27, 30, 31, 33]. In the above-mentioned papers, these parameters are assumed to be constant for particular operation and part. On the con- 2 General assumptions trary, variable federate is taken into consideration in [13, 25]. In turn, [23, 34] focus on CNC turning, adopting cut- In the furniture production, a vast majority of routing ting speed, feed rate and depth of cut as decision variables, can be performed with three-axis routers, and therefore, whereas [2, 32] consider constant depth of cut for the same this type of CNC machines dominates in that industry. operation. There are also various solution to the problem of Thus, current research has been limited to three-axis CNC optimal tool path during routing and turning [3, 4, 14, 15, routers. Int J Adv Manuf Technol (2013) 67:2259–2267 2261 Because of high anisotropy of solid wood, cutting force ally advantageous. In CNC routing, when the feed direction changes along with cutting direction. Moreover, it has been varies, significant changes in obtained surface roughness proved that the angle between feed and fibre direction can be expected at the same feed per tooth. Unfortunately, has significant impact on routing quality [7, 11]. There- in the literature, there is not enough data to develop a math- fore, the effective optimisation of such operations requires ematical model that would take into account the influence consideration of variable feed rate. of fibre orientation relatively to feed direction on acquired The tool path in CNC operations consist of segments surface properties. However, based on [7, 11], it is possible that are simple geometrical primitives (lines, circles, arcs). to select places along the tool path, where feed rate should When tool radius compensation is turned off, each of the be decreased to maintain cutting quality. Because the con- primitives is a result of single movement instruction in CNC ditions of operation to be optimised may be significantly programme (G-code). It is very likely to happen that cutting different from the conditions of the above research, the conditions (cutting depth, feed direction) change within a available data should be treated as showing general tenden- segment. On the other hand, typical G-code allows for set- cies rather than particular threshold values. Therefore, the ting only one nominal constant feed rate for each segment. feasible region cannot be fully defined by a set of inequali- Therefore, it may be reasonable to divide long segments ties as it is expected in case of numerical optimisation. into smaller parts to allow more frequent federate change. Because of the problem with direct formulation of math- However, the excessive division of segments produces long ematical model, it was decided to employ both numerical CNC programmes that may be difficult to handle by the methods and fuzzy logic for the optimisation. The use code interpreter.
Details
-
File Typepdf
-
Upload Time-
-
Content LanguagesEnglish
-
Upload UserAnonymous/Not logged-in
-
File Pages9 Page
-
File Size-