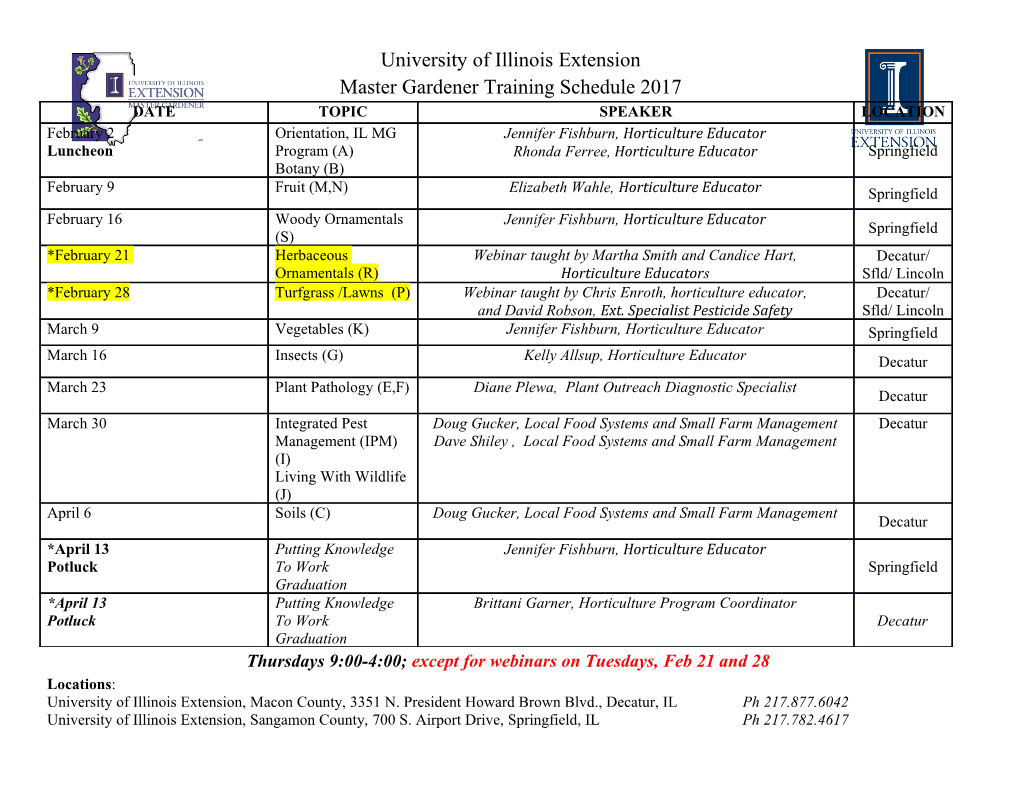
We look at thPe faoctrorss cthaht aeffec9 t a19111S’s riudeshpeigehtn, itsscieontner oGf greavoity,mandemtorry e. STORY BY CHRIS ANDROPOULOS PHOTOS BY CHRIS ANDROPOULOS AND PORSCHE A COMMON ADAGE among auto enthusiasts is that suspension point in space (see diagram) about which the sprung mass (essentially the body and design and tuning is a “black art.” While the practice of suspension anything else “suspended” by the suspen - tuning may seem to be more art than science and the results can be sion) of the car rolls. Both the front and rear quite subjective, there are some concrete fundamentals to suspension suspension each have their own roll center, which is determined by the configuration, design. It is practically impossible to cover all aspects of suspension length, and angle of the control arms as geometry in one article, as entire books have been written about sus - viewed from the front (or rear) of the car. The static roll center height can vary pension theory and design. But Porsche’s approach to the suspension greatly between different suspension design and geometry of its 911 road car (and its higher performance designs, and can even be below the and racing derivatives) can be distilled into one feature. ground in certain cases, but is usually located somewhere between the ground and the underside of the chassis of most vehicle’s mass to remain more evenly dis - performance vehicles. Ideally, the height SuTshpe nmsaiionngGoael oomf aeptreyrfBoramsiacns ce car tributed between the inside and outside of the vehicle’s CG and of that of the roll suspension is to maintain an optimal tires, which enhances cornering grip. center are as close as possible, which min - interface between all tire contact patches Another factor influencing cornering imizes body roll. If the CG is too high (which are relatively small at any given grip is body roll, which is induced by the and/or the roll center is too low, the instant) and the road during all phases of compliance of the suspension springs. sprung mass will exert greater leverage driving. There are myriad factors which Severe body roll causes the CG to move upon the suspension arms during corner - determine the tire contact patch during laterally, which increases the amount of ing, which increases body roll. transient maneuvers, such as the roll stiff - weight transfer to the outside tires during Furthermore, the location of the roll ness of the suspension, damping charac - a turn. Therefore, it is desirable to mini - center is movable and changes in con - teristics, vehicle weight distribution, tire mize the body roll of a performance car. junction with the movement of the sus - sidewall and tread stiffness, suspension An important concept to remember is pension arms (the diagram shows the bushing compliance, aerodynamics, and that even if a vehicle has a completely static roll center of a typical MacPherson so on. However, the basic geometry of the solid suspension and zero body roll, side- strut front suspension), so this must be suspension plays a major role in control - to-side weight transfer will still occur. taken into account by engineers. It is cru - ling the motions of the individual wheels Again, lowering the CG is the only way to cial to minimize the movement of the roll and affecting weight transfer during tran - decrease the amount of weight transfer. center during cornering to ensure pre - sient maneuvers. An easy method of quelling body roll dictable handling characteristics. When a vehicle is negotiating a turn, would be to install very stiff suspension In the days of the early 911, suspension the centripetal force exerted by the fric - springs and anti-roll bars, but this usually engineers hand-plotted the movable roll tion between the tire contact patches and results in a harsh ride and poor tire-to- center of the suspension with each degree the road causes weight transfer from the road contact on anything but the of body roll using paper and pencils, and wheels on the inside of the turn to the smoothest road surfaces. Besides lower - then tested the result with prototype chas - tires on the outside of the turn. The total ing the CG as much as possible, the best sis. In modern times, the same process is amount of weight transfer is determined way to control body roll and wheel move - simulated by using powerful computer by the combination of cornering force ment while cornering is by careful design models and is simulated down to the exerted upon the vehicle, along with the of the suspension geometry. most infinitesimal of details. Even so, the height of the center of gravity (CG) of the One of the crucial determinants of a concept is only fully proven when the rub - vehicle’s mass. In other words, the lower vehicle’s cornering behavior is the height of ber meets the road! the CG is, the less weight transfer will the roll centers of the front and rear sus - Suspension geometry is a three- occur, which is desirable as it allows the pension. The roll center is an imaginary dimensional subject, and there are many AUGUST 2017 excellen ce 107 1 2 34 more considerations that are beyond the with this configuration, the length and Another benefit of the revised RSR scope of this article. When the vehicle is angle of both the upper and lower A-arms spindle location is that it restored the cor - viewed from the side, an imaginary line can be altered to achieve the desired roll rect front A-arm angle in relation to the scribed between the front and rear roll center. More importantly, the movement body (at the original spindle height, the centers is known as the roll axis, the angle of the upper control arm can be used to A-arms angled upwards from the body of which is a major determinant of chas - enable camber gain of the outside wheel mounting point to the lower ball joint, sis balance (understeer vs. oversteer). The as the suspension compresses during cor - which served to lower the roll center configuration, length, and angle of the nering, which helps to prevent the tire height). Because the roll center height suspension control arms in relation to the sidewall from “rolling over.” The upper decrease was greater than that of the CG, vehicle’s CG as viewed from the side also mounting point of the MacPherson strut the potential body roll actually increased! determine the anti-dive behavior of the design is fixed, which limits the ability of Porsche also made suspension geome - suspension during braking as well as anti- the outside wheel to maintain a proper try changes to the rear of the 911 RSR. As squat characteristics of the rear suspen - camber angle during hard cornering. mentioned in the previous 911 suspen - sion during hard acceleration. However, the CG advantages afforded by sion article, the original 911 street car’s the low placement of the 911’s flat-six semi-trailing arm rear suspension geom - engine helped to mitigate these effects. etry was designed to keep the outside rear 911AsSouustpliennesdioinntGhee“o9m11etSruy spension Porsche’s first major change to the wheel as upright as possible throughout Evolution” article that appeared in the 911’s suspension geometry occurred with the suspension travel. February 2016 (#234) issue, the original the production-based 911 RSR racer of However, the ever-increasing envelope Porsche 911’s MacPherson front suspen - 1973. The front ride height had been of chassis and tire performance through - sion configuration was born out of prac - reduced significantly to lower the RSR’s out the 1960s meant that to maintain ticality rather than ultimate performance. center of gravity, which limited suspen - optimal contact patches for the fat 260 While the lack of upper control arms sion travel to the point where the suspen - mm-wide rear tires during cornering, the saves room for a luggage compartment, it sion would bottom out during certain RSR needed more negative camber of the does sacrifice some favorable wheel con - turns. Porsche remedied this by raising outside rear tire as the suspension com - trol characteristics. the height of the spindles by 0.7 inch to pressed. To this end, the forward mount - Most pure racing cars use the classic allow the lowered ride height while main - ing points at the rear torsion bar tube (or double A-arm or double wishbone design; taining full suspension travel. “pickup” points) of each rear trailing arm 108 excellen ce AUGUST 2017 56 1) This 911 track car has RSR-style raised front spindles to restore proper suspension travel and geometry. 2) A 935 engine with the “upside-down” transaxle that was necessary to restore proper axle angles at the 935 ʼs low ride height. 3) Detail of an original 993 Carrera 4 front upright and drive axle. 4) A lowered 993 Carrera with factory 993 RS front uprights and tie rods to restore correct front suspension and steering geometry. 5 & 6) Porsche has maintained the basic MacPherson strut front sus - pension design for its sports cars as shown in this example of a 996 GT3 front suspension. 7) Porscheʼs multi -l ink rear suspension design (996 shown) ensures precise wheel control in all planes. 7 were moved both inward and rearward. previous, normally-aspirated RSR (which pension design remained. The original This meant that the geometry of the RSR had coil helper springs). The sheet-metal 911’s strut housing with a welded-on trailing arms somewhat mimicked a 356 front A-arms of the street car were replaced spindle and steering arm was replaced by swing axle in that the negative camber of by lightweight, tubular versions with a modular design with a separate strut each rear wheel increased with suspension spherical bearings and turnbuckles to housing that bolted to a lightweight alu - travel (though in a much more precise allow for easy adjustment of camber, caster, minum wheel/hub carrier (or “upright” and controlled manner).
Details
-
File Typepdf
-
Upload Time-
-
Content LanguagesEnglish
-
Upload UserAnonymous/Not logged-in
-
File Pages5 Page
-
File Size-