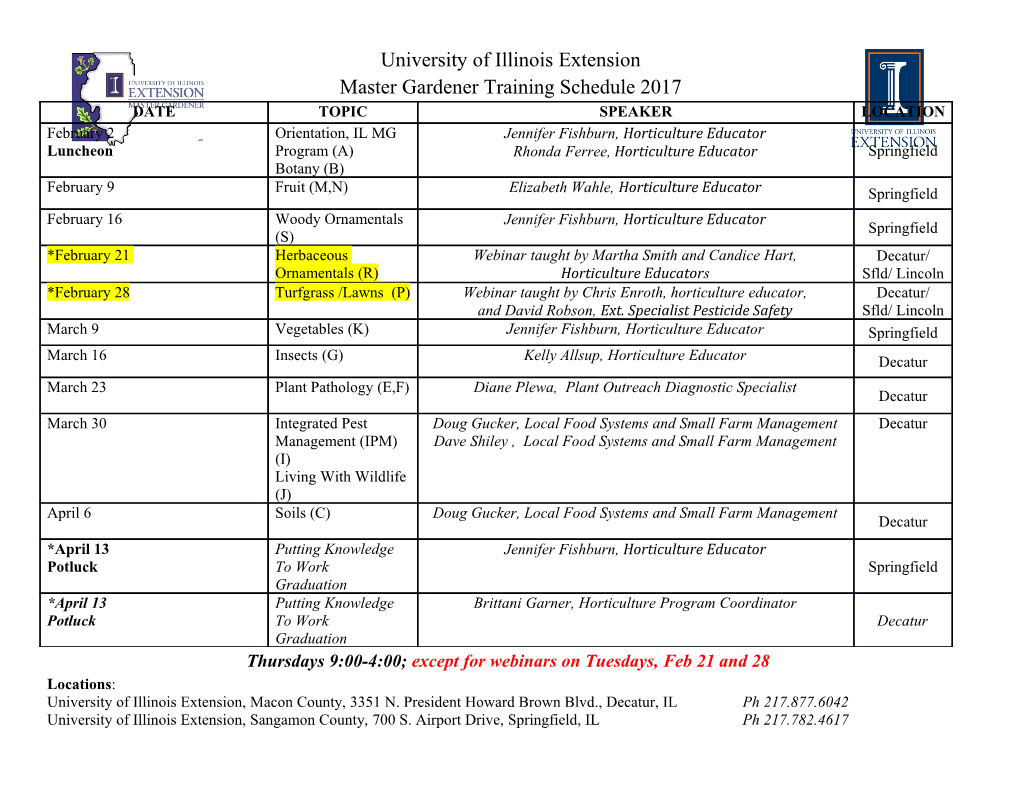
Carbonaceous Adsorbents Ali Ahmadpour Chemical Eng. Dept. Ferdowsi University of Mashhad Contents Industrial adsorbents Activated carbons Types Preparation methods Structures Applications Carbon molecular sieves Preparation methods Structures Applications CMS membranes Applications 2 Examples of commercial gas-adsorption separations Separation Adsorbent I. Gas bulk separations N-paraffins/iso-paraffins, aromatics Zeolite N2/O2 Zeolite O2/ N2 CMS CO, CH4, CO2, N2, Ar, NH3/H2 Zeolite, Activated carbon Hydrocarbons/vent streams Activated carbon H2O/ethanol Zeolite Chromatographic analytical separations Inorganic and polymeric agents II. Gas purification H2O/olefin-containing gas, NG, SG gas, air Silica, Alumina, Zeolite CO2/C2H4, natural gas, etc. Zeolite Hydrocarbons, solvents/vent streams Activated carbon, Silicalite Sulfur compounds/NG, hydrogen, LPG, etc. Zeolite SO2/vent streams Zeolite Indoor air pollutants-VOCs Activated carbon, Silicalite Tank-vent emissions/air or nitrogen Activated carbon, Silicalite 3 INDUSTRIAL ADSORBENTS FOR GAS SEPARATIONS Activated carbons Carbon molecular sieves (CMS) Molecular sieve membranes Zeolites Activated aluminas Silica gels Molecular gates 4 Commercial sorbents Some types of generic sorbents which have dominated the commercial use of adsorption are: activated carbon, zeolites, silica gel, activated alumina, and clays. Worldwide sales of these sorbents in 2001 were: Activated carbon $1,500 million (demand 1.2 million tons in 2010) Zeolites $1,070 million Silica gel $71 million Activated alumina $63 million Clays $16 million 5 Activated carbons Activated carbon is a predominantly amorphous solid that has an extraordinarily large internal surface area and pore volume. Its history can be traced to 350 BC when it was used by Egyptian for the reduction of copper, zinc, and tin ores. In modern day, it is widely used and is produced as a powder, granule, or preformed shapes (pellet, extrudate, and block). They have unique properties and low cost compared with other adsorbents. 6 Cont. ACs are extremely versatile adsorbents of major industrial significance and are used in a wide range of applications for the removal of species by adsorption from the liquid (e.g. Hg) or gas phase (e.g. sulphur), in order to effect purification or the recovery of chemicals. They are also used as catalysts or catalyst supports. Activated carbons are prepared from a variety of raw materials such as: coals, polymers, nutshells, … The surface area, dimensions, and distribution of the pores in ACs depend on the precursor and on the conditions of the carbonization and activation. 7 Cont. Activated carbon is a "universal adsorption medium". The lack of chemical uniformity of the surface and the wide variation of pore size of AC make adsorption of a variety of molecules possible. This variety is linked to some serious disadvantages. Therefore, activated charcoal is more often tailored to specific requirements, which improves performance even if at the expense of wide application. 8 Types of Activated Carbons Coal-Derived Carbon For reasons of economy, the most favored starting material for making AC and CMS is coal. This type is used for removing color bodies and impurities from a variety of liquids and for solvent recovery. Polymer- Derived Carbon CMS and ACs can also be made from various polymers such as polyvinylidene chloride, polyacrylonitrile, phenol formaldehyde, etc. Carbon Derived from Other Materials ACs with very high surface areas (2800 m2/g), exceptional adsorptive capacities and unique structural features can be obtained by chemical activation of coal or petroleum coke with KOH. They are used for removing color bodies from water and hydrocarbons. 9 Activated carbon preparation Nut Crushing or CO2 Physical Coal Activation Steam KOH Chemical ZnCl2 Characterization How much? How fast? 10 Industrial manufacturing (physical activation) 11 AC structure The structure of AC is best described as a twisted network of defective carbon layer planes, cross-linked by aliphatic bridging groups. 12 SEM images of ACs 13 How Activated Carbon Works 14 Pore volume distribution of ACs 15 Pore size distribution of ACs 16 Adsorption isotherms of different adsorbents 17 AC market Demand for AC in the US is forecast to increase nearly 5% per year to 1.2 million tons in 2010. Since AC is used primarily as an adsorbent to remove organic compounds and pollutants from liquid and gas streams, the market is heavily impacted by the implementation of various environmental regulations. These laws, as well as ACs low cost and excellent performance, drive demand in many large volume markets, such as municipal and industrial water treatment, industrial air purification, automotive emission canisters and solvent recovery. 18 Some applications & advantages Removal of organic compounds from gas or liquid streams up to 1000 mg/L (cost effective), feasible up to 5000 mg/L GAC is used for toxic organic compounds from ground water and industrial waste streams PAC is used for biological treatment Higher BOD and COD removal than biological treatment More insensitive to changing influent composition than biological treatment Enhanced removal of toxic compounds and priority pollutants 19 Activated Carbon Systems 20 Breakthrough curve in Adsorption columns 21 AC contactor 22 Activated Carbon Evaluation Process It is important to establish a well defined Test Protocol so that the operating parameters are the same for each activated carbon being evaluated. Fixed Parameters: Quality of feedstock Temperature Contact time Activated carbon dose rate Particle size of activated carbon pH of color measurement 23 Activated Carbon Selection and Optimization Granular activated carbon vs. powdered activated carbon Dose rate Contact time Particle size of activated carbon Temperature vs. viscosity 24 Carbon molecular sieves Carbon molecular sieves (CMS) represent one member of the family of activated carbons. CMS can be made from activated carbons by a post treatment which narrows the pore size distribution to produce a material with a bimodal pore distribution having a predominance of pores less that 6Å. Key to the performance of these materials is specific size selectivity. 25 Cont. The main distinction between CMS and AC is that activated carbons separate molecules through differences in their adsorption equilibrium constants. In contrast, an essential feature of the CMSs is that they provide molecular separations based on rate of adsorption rather than on the differences in adsorption capacity. This behavior is clearly evident in pressure swing adsorbers where gas dynamics dominate. The separation of nitrogen from air by PSA is the single most important application of CMS. 26 Kinetic separation of CMS 27 Preparation method General methods of manufacturing CMS materials include carbonizing coal or nut hulls in an inert atmosphere to produce chars. These chars may then be activated in a reactive atmosphere (e.g.. air or steam) to develop the necessary porosity. Non-O2 selective materials are made selective to O2 by depositing a gate-keeping layer on the pore entrances. This layer is often formed by pyrolysis of carbonaceous materials such as pitch, benzene, or furfuryl alcohol. 28 Major approaches for CMS preparation Carbon precursors Activation Pyrolysis Porous carbon Modification CMS with CMS with CVD lower adsorption higher adsorption capacity capacity 29 CMSs prepared by different methods (A) Formed by coke deposition ; (B) Formed by steam activation 30 CMS structure 31 Applications Pressure swing adsorption is a promising process for air separation, and the adsorbent is crucial to successful implementation of the technology. At present, carbon molecular sieves from coal and plants are used as the most common adsorbent in PSA. The major problem with currently available CMS is small effective pore volume (~0.3mL/g) while the ability to control the size of the pore openings in a CMS remains a major challenge in preparing CMS. 32 Cont. A variety of separation processes are carried out in industry by PSA on granular beds formed by CMS such as: O2/N2 CO2/N2 CO2/CH4 C2H4/C2H6 H2/CH4 33 Pressure swing adsorption PSA systems are used widely in the refining, petrochemical and air separation industries. Sample applications include H2 purification, reactant recovery from vent streams and air separation to produce enriched oxygen for combustion or nitrogen for inerting atmospheres. 34 Cont. The PSA process operates on the principle that an adsorbent’s capacity for an adsorbed component increases with increasing partial pressure. This principle is applied in cyclical manner where process steps typically include high-pressure adsorption, stepwise depressurization, and purge (generally with a light component and repressurization). The swing between the high adsorption pressure and regeneration at low pressure is completed in rapid cycles, generally on the order of a few minutes, to minimize the adsorbent inventory. 35 PSA highlights 1960: Drying of air and other gases. 1961: n-Paraffin removal 1966: H2 purification 1970: O2 production from air by zeolite 1976: N2 production from air by CMS 1977: N2 production from air by zeolite 1977: Poly-bed for large scale H2 production 1980: Single-bed for O2 production (medical use) 36 PSA systems 37 PSA for N2/O2 separation using CMS 38 PSA process for N2 production 39 PSA for hydrogen recovery 40 Hydrogen purification System for capacities from 100 to 10,000 Nm3/h and purities of up to 99.999+%
Details
-
File Typepdf
-
Upload Time-
-
Content LanguagesEnglish
-
Upload UserAnonymous/Not logged-in
-
File Pages62 Page
-
File Size-