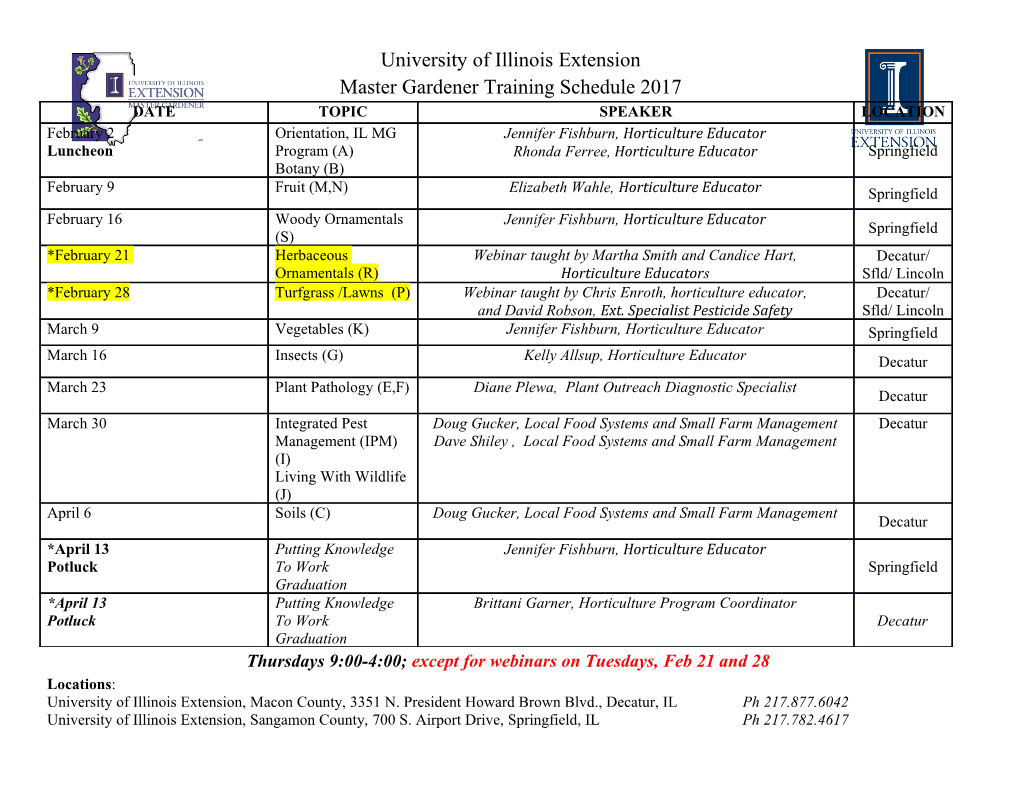
ASM Handbook, Volume 4C, Induction Heating and Heat Treatment Copyright # 2014 ASM InternationalW V. Rudnev and G.E. Totten, editors All rights reserved www.asminternational.org Principles of Induction Hardening and Inspection Valery Rudnev, Inductoheat Inc. Gregory A. Fett, Dana Corporation Arthur Griebel and John Tartaglia, Element Wixom Introduction Induction hardening of crankshafts and chemical composition, the quenching conditions, camshafts and the hardenability of the steel. Temperature Metals can be heated by the process of electro- Induction hardening of gears and gearlike distribution in induction surface hardening is con- components trolled by selection of frequency, power density, magnetic induction, whereby an alternating mag- netic field near the surface of a metallic (or Induction hardening of off-road machinery time of heating, and coil geometry. Typical induc- Coil design, systematic analysis of induction tion surface-hardening temperatures range from electrically conductive) workpiece induces eddy currents (and thus heating) within the workpiece. coil failures, and failure prevention approximately 880 to 1050 C(1620to1920 F). Quenchants and quenching devices The color associated with this range is orange to The basic components of an induction system are the inductor (coil), which can take different shapes, Formation of residual and transitional yellow. stresses The surface hardness, case depth, and core an alternating-current (ac) power supply, and the workpiece itself. An electrically conductive work- Computer modeling requirements will typically determine the grade Power supplies for induction heat treating of steel to be used. The attainable hardness piece (for example, steel) is placed inside an induc- tor or in its close proximity, the power is turned on, Process control and monitoring increases along with the carbon content of the Maintenance of heat treating equipment steel. This holds true up to approximately 0.65 and in a matter of seconds the part begins to glow red and then changes to orange or yellow without Defects and abnormal characteristics of to 0.7% C and then there is little or no further induction-hardened components increase in hardness with increasing carbon con- having any contact with the inductor. The heating process involves a complex combination of elec- Tempering of induction-hardened components tent. For any given carbon level, induction sur- face hardening provides a slightly higher tromagnetic and heat transfer phenomena, as With the expanded coverage from other articles in described in more detail in the article “Principles hardness than would be expected with traditional this Volume, an interested reader can obtain a more furnace hardening. This phenomenon is some- of Induction Heating” in this Volume. detailed understanding of induction hardening. Induction heating is used in a variety of heat times referred to as superhardening (Ref 12). treatment processes, such as annealing, normaliz- The microstructure present in a part prior to induction hardening can have a significant influ- ing, surface (case) hardening, through hardening, Metallurgical Overview tempering, and stress relieving (Ref 1–10). Vari- ence on how well a part hardens (Fig. 1). The most ous metallic materials, such as steel, cast iron, cop- common prior microstructure is a mixture of per, aluminum, brass, bronze, and so forth, can be The general aspects of metallurgy of induction pearlite and ferrite. The reason for this is not the heat treated by induction. Induction hardening of hardening of steels are discussed in several pub- ease of induction hardening but rather economics. steel components is the most common application, lications (Ref 1–11). The typical induction- A pearlitic-ferritic microstructure generally and surface (case) hardening is the dominant hardening procedure involves heating the com- requires no additional heat treatment after the part application of induction heat treatment of steel ponent, or its required area, up to the austenitiz- is forged. In components manufactured directly (see for example Ref 6). ing temperature, holding it at a temperature (if from bar stock the microstructure is usually This article discusses the general aspects of required) for a sufficient period for completion already a mixture of pearlite and ferrite. While a induction hardening—including common methods of austenite formation, then rapidly cooling it pearlitic-ferritic structure is not the best for ease of measuring case depth and hardness, along with below the martensite start (Ms) temperature of induction hardening it is certainly adequate some complications and ambiguities associated (see the subsequent article “Quenching in for many applications. The prior structure that with these measurements. As expected, the subject Induction Hardening” in this Volume). Rapid provides the best response for induction harden- of induction hardening is quite complex, compris- cooling or quenching allows replacement of ing is a quenched and tempered (QT) microstruc- ing electrothermal phenomena, physical effects, the diffusion-dependent transformation process ture consisting of tempered martensite or possibly technological subtleties, and knowhow. Due to by a shear-type transformation, creating a much an austempered microstructure consisting of bai- space limitation, coverage is necessarily limited harder constituent called martensite. Martensite nite. These microstructures are very easy to auste- in this article. However, several other articles in can be formed and hardening may be done either nitize in the short heating time associated with this Volume cover more material related to certain on the surface of the workpiece or throughout induction hardening, and as a result they can be aspects of induction hardening, including: the entire cross section. readily converted to martensite upon quenching. The main factors that affect the hardness and In most cases the quenchants used are water- Metallurgy of induction hardening case depth are the temperature distribution, the based polymers, so there is typically no fire haz- Induction hardening of axle shafts starting microstructure of the material, the ard or environmental concern. Principles of Induction Hardening and Inspection / 59 Depth, mm the center. For this reason surface hardening can 1.52 1.78 2.03 2.29 2.54 2.79 3.05 3.30 3.56 3.61 improve part performance with these two load 16 cases, because it increases the strength at the sur- 14 face where it is needed the most. 3.49 cm (1.375 in.) In addition, surface hardening normally 12 round 10 kHz leaves the surface of the part with a residual com- pressive stress, which acts as a crack arrester and 10 Annealed 2 increases torsional and bending fatigue life. The 3000 Hz, quenched Normalizedand drawn residual compressive stress is a result of the 8 expansion that takes place during the transforma- Quenched and drawn tion of the microstructure to martensite during hardening. Another reason for induction surface 6 hardening is to improve wear resistance or contact strength and/or contact fatigue life. Power density, kw/in 5 Induction through hardening also may be used for some parts such as snowplow blades, springs, 4 chain links, truck bed frames, certain fasteners (including nails and screws), and so forth. In these cases, the temperature of the entire 3 cross section is raised above the temperature at 0.06 0.07 0.08 0.09 0.10 0.11 0.12 0.13 0.14 0.15 which transformation to austenite is completed Depth, in. (Ac3 critical temperature) and then quenched. Through-hardening applications require uniform Fig. 1 Influence of prior structure (fineness of microstructure constituents) on power requirements for surface heating through the entire cross section. Selection hardening. Source: Ref 13 of the appropriate frequency and time is very important for achieving the proper surface-to- An annealed prior microstructure consisting of and poor formability. Even so, there are a variety core temperature uniformity. ferrite and spheroidal carbides has the poorest of applications including valve-spring wire, drill response to induction hardening. This type of bits, grinding balls, cutting tools, and others, for microstructure can be formed by subcritical which high-carbon steels (such as SAE 1060 to annealing. Spheroidized annealing is typically 1095) are specified. Electromagnetic and Thermal used to aid in cold formability. It is not uncommon Although plain carbon steels are the least Aspects for this type of microstructure to be only partially expensive steels, there may be engineering martensitic after induction hardening. Substan- applications where they may not be suitable. As detailed in the article “Principles of Induc- tially longer times and higher temperatures are Applications which require more hardenability tion Heating” in this Volume, the primary mech- required for a sufficient austenitization of these for increased case depths, or greater impact anism of the heat generation is Joule heating microstructures, noticeably dropping some of resistance, or higher fatigue life, may require (I2 R) by the induced eddy current, where R is the main advantages of induction hardening. The the use of alloy steels. Examples of alloy steels electrical resistance of the workpiece and I is poor induction-hardening response can be alle- used in induction hardening are SAE 4140, the induced current. An alternating current (ac) viated by normalizing the part after forming. 4150, 4340, 5150, 5140, and 52100. in the induction
Details
-
File Typepdf
-
Upload Time-
-
Content LanguagesEnglish
-
Upload UserAnonymous/Not logged-in
-
File Pages9 Page
-
File Size-