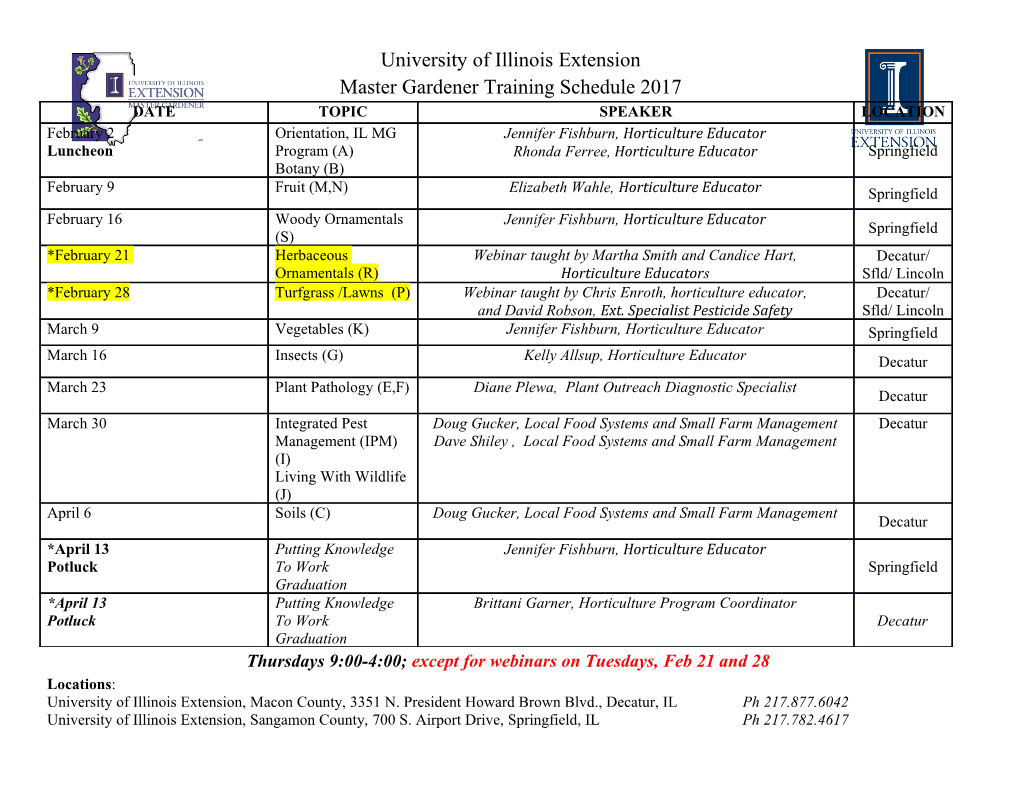
See discussions, stats, and author profiles for this publication at: https://www.researchgate.net/publication/282997310 Common Mistakes on the Application of Plaxis 2D in Analyzing Excavation Problems Article · January 2014 CITATIONS READS 0 4,815 1 author: Tjie-Liong Gouw Binus University 10 PUBLICATIONS 1 CITATION SEE PROFILE Some of the authors of this publication are also working on these related projects: Shore protection project View project All content following this page was uploaded by Tjie-Liong Gouw on 20 October 2015. The user has requested enhancement of the downloaded file. International Journal of Applied Engineering Research ISSN 0973-4562 Volume 9, Number 21 (2014) pp. 8291-8311 © Research India Publications http://www.ripublication.com Common Mistakes on the Application of Plaxis 2D in Analyzing Excavation Problems GOUW Tjie-Liong Civil Engineering Department, Bina Nusantara University, 11480 Jakarta, Indonesia Email : [email protected] Abstract The advance of computer technology has made the finite element method (FEM) more accessible than ever. Many engineers have tried FEM geotechnical software in handling their geotechnical projects. However, like a pilot with inadequate training, it would backfire if he were to fly a sophisticated jet fighter. Engineers with insufficient geotechnical background may gain access to the sophisticated FEM software without realizing the risk behind it. They make mistakes that may lead to the bad performance or even failure of the geotechnical structures. The author himself, along the years of learning and applying the geotechnical FEM software, has made many mistakes. This paper, with Plaxis application as example, tries to elaborate the common mistakes found in applying the FEM geotechnical software in handling excavation problems. Keywords: Finite Element Method, Plaxis, Deep Excavation 1. Introduction The application of Finite Element Method (FEM) is not new, it has been used in many engineering practice for over forty years. Throughout the seventies to mid-nineties, the method could only be applied by large universities that could afford to have the so called main frame computers. By the end of the 20th century, the advancement of computer technology had made personal and laptop computers able to run sophisticated FEM software, and hence, the method starts gaining its foot among engineers. To the author knowledge, specially built FEM software for geotechnical applications started to appear in the market in the early 1990s with the appearance of Feadam, Sage-Crisp, Plaxis, and others. As computer processors becomes faster and 8292 GOUW Tjie-Liong faster, many commercial geotechnical FEM software are becoming available, e.g.: Plaxis, Phase2, Geo5fem, Gfas, Sigma/w, Midas, Geofea, etc. The author started becoming familiar with the geo-technical FEM software in the early 1990s. Started with Feadam in the 1990, Sage-Crisp in 1997, Plaxis from 1995, and lately also trying Phase2, Gfas, and Geo5fem. Along the years, in the process of learning, teaching and applying the FEM for geotechnical structures, through the mistakes of others and himself, he has gain some experiences that has made him wrote this paper to share the lessons learned. The write up given in this paper is based on Plaxis 2D software. 2. Modelling Excavation in Plaxis 2D 2.1 Plane Strain vs Axisymmetry Model Though it is a relatively simple concept, many practicing engineers fail to understand the meaning of plane strain and axisymmetry. For example the shaded portion in Figure 1 will result in a long out of plane excavation if a plane strain model is adopted. On the other hand, it will result in a circular shape excavation if an axisymmetry model is adopted. Y X Z Figure 1. Plane Strain vs Axisymmetry Model The plane strain model means the strains can only take place in the xy plane. Along the longitudinal axis (out of plane direction) the strain is assumed to be zero, z = 0. Consequently, the length of the excavation must be significantly larger than the width of the excavation. The axisymmetric model means the lateral, or more precisely, the radial strains of the model are equal in all direction, x = z. As the name implies the structures in the model is symmetrical along the vertical Y axis and the model is rotated at the Y axis, hence the model in Figure 1 results in a circular excavation. Note: in Plaxis the rotating axis is always at the left boundary. Common Mistakes on the Application of Plaxis 2D 8293 Of course failure in choosing the right model of plane strain or axisymmetry will lead to incorrect output. 2.2 Interface Element The interaction between the structural element and the soil is modeled by means of interface. The interface element is used to reduce the friction between the structural element and the soil. Introducing interface value, termed as Rinter, which has value between 0.01 and 1.0, does this. The lower bound value of 0.01 means there is practically no friction between the structural element and the soil. The upper bound value of 1.0 means the structural element and the soil is completely in contact, it means the soil and the structural component cannot slip one another. In this case, the contact is termed as rigid. Values in between mean the friction is reduced by the given number of Rinter, and the structural element and the soil mass can slip between one another. The common mistake is to apply the interface element in modeling pressure grouted ground anchors as shown in Figure 2. The free length of ground anchors is modeled by node to node anchor. As the name implies, in node to node anchor, the anchor is connected at both ends to nodes in the structural element, as if there is no contact along the anchor body to the surrounding soil. Therefore, there is no use to apply interface element along the body of the node to node anchor. The bond length of ground anchors is modeled by geogrid (tensile) element. In practice the bond length is normally pressure grouted as such that the soil around the grouted body is completely in contact with the grouted body. Figure 2. Mistake in Modeling Ground Anchor Therefore, failure surface take place not between the grouted body and the soil, but within the soil seams that stick to the grouted body and the soil around it. It means the full frictional force of the soil can be developed; therefore, no interface element should be introduced. Applying interface element and giving Rinter less than 1 is a mistake. 8294 GOUW Tjie-Liong 2.3 Material Models There are many options to simulate soil behavior, e.g.: Mohr-Coulomb (MC) model, Soft Soil Model, Hardening Soil Model, Soft Soil Creep, Hardening Soil with Small Strain, Modified Cam-clay, etc. Every model has each own pro and cons. Two of the soil models that are often adopted for modeling deep excavation problems, shall be discussed below, 2.3.1Mohr-Coulomb (Mc) Model Being the simplest and the one that engineers were being trained with in their undergraduate study, Mohr-Coulomb is widely adopted by practicing engineers, often without realizing the limitation. Mohr-Coulomb modeled the non-linear behavior of the soil into two bilinear lines, as presented in Figure 3. Inherent in this Mohr-Coulomb bilinear elastoplastic approached, the soil stiffness, taken as E50, is constant throughout the elastic zone, until the stress state reaches the plastic (failure) zone. In reality, the soil behaves non linearly which means the soil stiffness is never constant, instead it changes with the stress level within the soil mass. Therefore, at stress level less than 50% of the ultimate strength, the MC model will over-predict the ground movement, whereas at stress level higher than 50% (means factor of safety less than 2) it can dangerously under predict the ground movement. Figure 3. Mohr Coulomb Model Another serious drawback in the MC model is: it assumed the soil unloading- reloading stiffness modulus, Eur, equal the soil loading stiffness, E50, i.e. Eur=E50 as presented in Figure 3b. In reality, under unloading-reloading condition soils generally have much stiffer modulus compared to under loading condition (see Figure 4). The Common Mistakes on the Application of Plaxis 2D 8295 unloading-reloading stiffness can be easily higher by a factor of 2 to 5 as compared to the loading stiffness i.e. Eur ≈ 2~5 E50. This means that when applied to evaluate excavation problems, the MC model will generally over predict the soil heave in an unrealistic manner. Due to this reason, in excavation problem, when MC model is adopted, it is suggested to input the soil stiffness in Eur value rather than E50. q Perfectly Plastic Eur>E50 1 E50 1 e z Figure 4. Real Soil have Higher Unloading-Reloading Modulus Apart from the drawback on the assumption of the stiffness modulus, which leads to the inaccuracy of predicted soil movement, MC model also have its limitation in analyzing undrained problem. This shall be discussed in the next section. 2.3.2Hardening Model The real soil stress strain behavior shows that when loaded the soil behaves non- linearly. As the load goes higher the stiffness modulus of the soil becomes lower and lower (see Figure 5). Figure 5. Non-linear Stress Strain Curve and The non Constant Soil Stiffness This non-linear stress strain behavior can be approximated by hyperbolic model developed by Duncan & Chang, 1970. In Plaxis, this hyperbolic model is known as Hardening Soil model (HS model), and often applied in evaluating soft soil or hard ground condition. The formulation of the model is shown in Figure 6 below, 8296 GOUW Tjie-Liong Ei = initial stiffness (Young’s Modulus) Figure 6.
Details
-
File Typepdf
-
Upload Time-
-
Content LanguagesEnglish
-
Upload UserAnonymous/Not logged-in
-
File Pages23 Page
-
File Size-