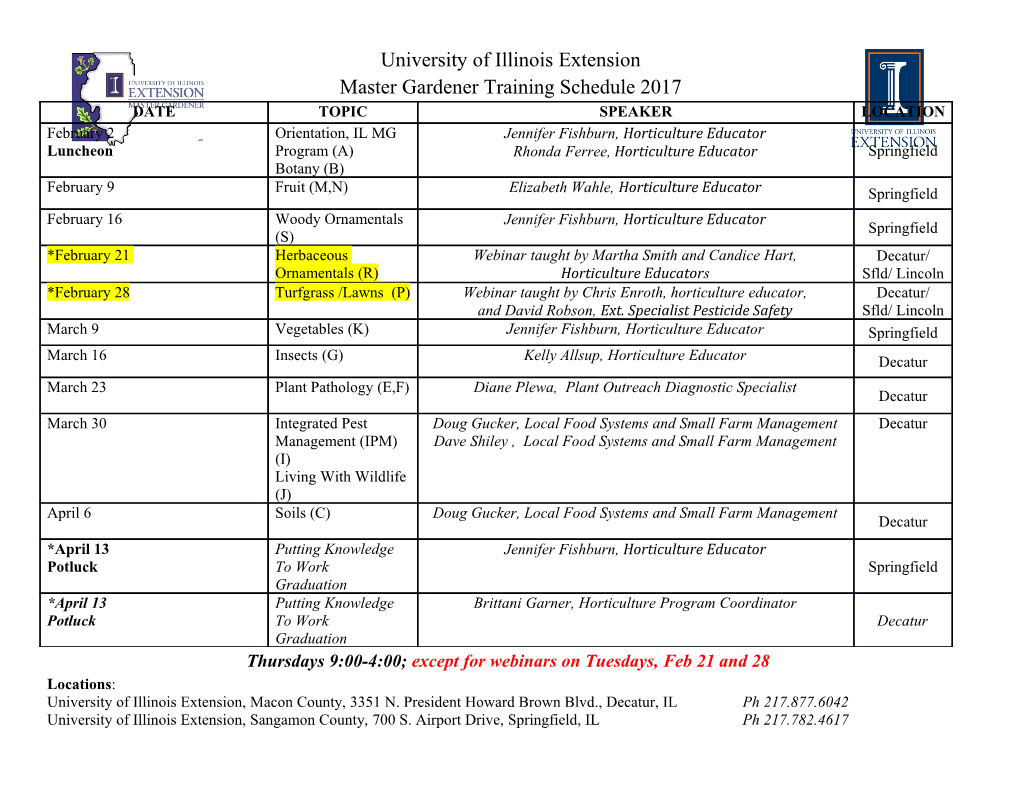
Design and development of the Nozzle Deployment Mechanism for the Vinci Cryogenic Engine (1) (1) (2) Sigmunn Strøm , Johan Krabberød , Olivier Condaminet (1) Kongsberg Defence and Aerospace, Kirkegårdsveien 45, 3610 Kongsberg, Norway Email: [email protected] ; [email protected] (2) Snecma, Foret de Vernon, Vernon, France. E-mail: [email protected] . ABSTRACT Snecma Space Engine Division in Vernon, France is developing a new cryogenic upper stage rocket engine, VINCI, for future version of the Ariane 5, the A5ME (Ariane 5 Midlife Evolution). Kongsberg Defence and Aerospace, Norway are responsible for the design, development and delivery of the Nozzle Extension Deployment Mechanism (MDD = Mécanisme Déploiement Divergent). The deployment mechanism is a complete new design functionally and structurally and includes use of novel components and materials. The paper describes the design principles, analysis methods, test campaigns and general information about obtained performance, electrical architecture and the Figure 1. Vinci with MDD – shown in Stowed and integration cycle of the MDD on the Vinci Engin e. Deployed position 1. INTRODUCTION Snecma Space Engine Division in Vernon, France is 2. REQUIREMENTS developing a new cryogenic upper stage rocket engine, VINCI, for A5ME future version of the Ariane 5. 2.1 Main Requirements. Kongsberg Defence and Aerospace, Norway are responsible for the design, development and delivery of Three main functional requirements determined the the Nozzle Extension Deployment Mechanism architecture of the MDD. They are: (MDD=Mechanism Deployable Divergent). The nozzle extension is to be deployed 1830 mm and Astrium is responsible for the development of the latched in < 10 s. CRIUS stage, and ESA/CNES is project manager of Latching resistance is defined by a statistical A5ME. distribution. The introduction of a deployable nozzle extension on Kinetic Energy at latch must be < Ecmax to avoid the Vinci engine provides a 5 % increase in engine damage of the nozzle by the final impact. thrust with a corresponding payload increase. The Vinci engine with the nozzle stowed and extended is To satisfy these requirements a deployment sequence shown in Fig. 1. as shown in Fig. 2 Other design driving requirements were: • Electronic speed control could not be used • Limited battery capacity for deployment and sequencing. • Endurance of vibration loads during launch of the first stage of the launcher. • Minimum mass • Dynamic behaviour of the deployment mechanism - nozzle extension system T3 T4 Speed Nozzle ∆P1 Switch tolerance T5 T7 1.83m ) ) 1 2 (T ing 0 Pos Break switch Position End Start Start Phase Phase 1 2 0 Pos atching atching X l X latch Figure 2. Principle deployment sequence at Hot and Cold conditions The selection of the two motors torque-speed curves 2.2 Design Restrictions and the motor to ballscrew gear ratio and ballscrew pitch was an essential and critical part of the system The three main functional requirements are in design. To minimize the effect of the variation in conflicting with each other. friction in the deployment system the motors had to be High deployment speed is required to meet the specified to operate at approx. 60 to 80% of the no load deployment time target, while requirement for low speed. kinetic energy requires a low speed. The ESA rules for mechanism torque margin Sufficient latching force is required to guarantee calculation (ECSS-E-30-8A) could not be used to stay latching for worst case conditions, but limited in order in the allowed latching force. The requirement for a not to damage the fixed or the extendable nozzle. safety factor of 3 on friction and a motorization factor of 2, leads to a motor torque capability 6 times that The speed of deployment could only be controlled by theoretically required. This “oversizing” of the motors the equilibrium between the speed torque characteristic to satisfy the ESA rules for the latching effort led to of the motors and the frictional and inertial resistance low or negative margins on deployment time and in the gears and ballscrew system. kinetic energy specifications. A probabilistic design approach was therefore used. 3. DEPLOYMENT MECHANISM CONCEPT The most significant variables in the deployment EVALUATION analysis were assigned a mean value and a range of variation. Depending on the type of variable a normal Several system concepts were investigated attempting distribution with a standard deviation or a uniform to satisfy all requirements. Initially a concept using two distribution was used. identical brush motors, one acting as a brake/generator and one driving through the same gears was proposed. A Monte Carlo method was used to make up to 1 One of the motors was short circuited to a million draws to calculate the mean value and the generator/brake a short distance from the latching standard deviation and then to demonstrate the level of point. The required combination of high deployment reliability for meeting the requirement specifications. speed, low latching speed and the required latching force was not obtainable. It became clear that two different motors with different gearing ratio were required. 4. MDD DESIGN DESCRIPTION The central Power Unit contains: • Motor 1 driving through a spur gear. • Motor 2 driving through a geared freewheel 4.1 General and a spur gear. The MDD design consists of three ball screws, 120° • Main gearbox with three output drive shafts apart, supported by struts at the upper end and by the • Locking Mechanism with manual operation fixed nozzle at the lower end. The ball nuts are access. attached to the extendable nozzle via flexible • Position Sensor couplings. Each ballscrew is driven through a gear • Electronic circuits with sequencing and chain consisting of a 90º gearbox, a transmission shaft, switching relays a “three shaft” main gearbox, and two electrical motors. A block diagram of the MDD is shown in Fig. 3 and a drawing of the complete MDD is shown in Fig.4. 4.2 Mode of operation During EAP-EPC flight phase of Ariane 5 the nozzle is Power Unit locked in stowed position by a locking arrangement in Lock Position switches the power unit. Main 90º Motor 1 Transmission Shaft The deployment is initiated by command from the Gearbox Gearbox Ball screw BNA Ariane 5 control unit (SEL). The MDD is from this 90º moment fully autonomous and controls the deployment Motor 2 Transmission Shaft Ball screw Gearbox sequence. BNA Freewheel Nozzle 90º The sequence starts with the release of the locking Man. Drive Transmission Shaft Ball screw Gearbox mechanism by operating a memory alloy pin puller BNA Electrical before powering the motors. circuit & IF connectors Motor 1 is driving in high speed phase of the deployment, while Motor 2 is idling via a free-wheel. Figure 3 MDD block diagram The brake-position, at approx 95 % of the deployment distance, is detected by the Position Sensor integrated in the Power Unit. At this moment Motor 1 is switched Main off and short-circuited by the sequencing electronics to Power Gearbox Unit provide dynamic braking before the latching phases. In the latching phase Motor 2 provides the driving 90º force. Transmissio Gearbox n Shaft Supporting Bracket Power Unit 4.3 Component design Sub Assembly 4.3.1 Motors Ball KDA identified three suppliers of aerospace/launcher Screw qualified brush motors. Two US suppliers, Kollmorgen and MPC and one French supplier, Artus. Based on KDA’s simulation for the MDD system for a range of ball screw pitch, gear ratios and motor characteristics a requirement specification for the motors were developed in cooperation with Artus. To limit cost, both motors were built with identical external dimension and common internal parts to the extent possible. Motor 1 was specified with low torque constant and low winding resistance for the high speed low torque deployment duty. Motor 2 was specified with high torque constant and Ball Nut high winding resistance for the slow speed high torque Adapter latching duty. Figure 4 MDD components Figure 7 Gearbox with 4 output shaft. Figure 5 Motor 1 (deployment motor) with pinion. The drive torque is connected to the ballscrews via 3 4.3.2 Gear Chain slender transmission shafts with universal joints and 3 90ºgearboxes, as shown in Fig.8. The arrangement on Several variables determine the ratio between the the Vinci engine is shown in Fig 9 and the motor speed and the linear deployment velocity and 90ºgearboxes.in Fig 8. latching force. Motor 2, the latching motor, need a large ratio from the rotational speed to linear nozzle velocity, this can be obtained by a small pitch ball screw and relatively large gear ratio. Motor 1, the deployment motor, needs a small ratio from rotational speed to linear nozzle velocity, this can be obtained by large pitch ball screw and smaller gear ratio. The difference in gear ratio is obtained by engaging Motor 2 to the external diameter of the freewheel, in that way a two stage parallel gear is obtained for Motor 2 as shown in the drawing in Fig. 6. Motor 1 is engaged directly to the crown wheel. This solution in combination with a compromised ball screw pitch provided the right combination of speed and torque in the different phases of the deployment. Crown Wheel Figure 8 90ºgearboxe Free wheel output pinion The main driving requirement for the gearboxes is the Motor 1 pinion Free wheel gear dynamic loads during launch which transmitted through the gearboxes to the Locking Mechanism and the need to limit the variation in efficiency and the no load frictional torque over the operating range. Motor 2 pinion Motor 1 Motor 2 Freewheel Figure 6 Motor1 and Motor 2 gearing arrangement The torque from the motors is turned from vertical to horizontal and split to the 3 ballscrews in a gearbox with 4 output shafts as shown in Fig.7.
Details
-
File Typepdf
-
Upload Time-
-
Content LanguagesEnglish
-
Upload UserAnonymous/Not logged-in
-
File Pages8 Page
-
File Size-