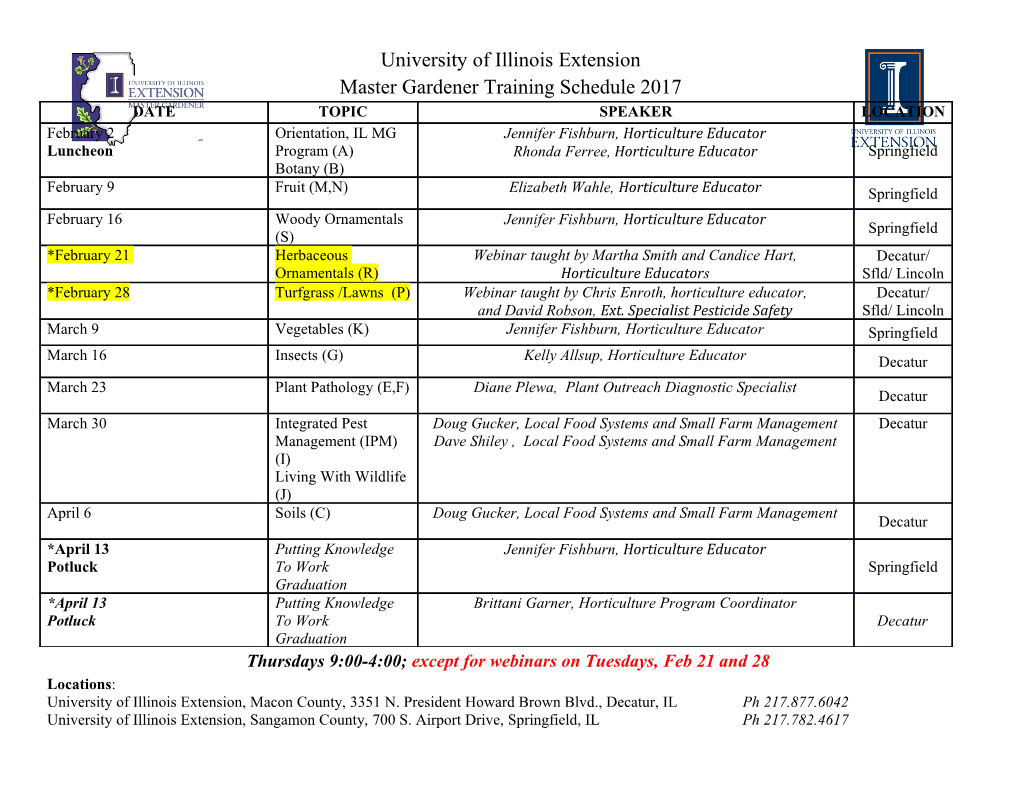
International Journal of Rotating Machinery (C) 1999 OPA (Overseas Publishers Association) N.V. 1999, Vol. 5, No. 2, pp. 77-87 Published by license under Reprints available directly from the publisher the Gordon and Breach Science Photocopying permitted by license only Publishers imprint. Printed in Malaysia. Axial Compressor Stall and Surge Prediction by Measurements H. HONEN * Institut jFtr Strahlantriebe und Turboarbeitsmaschinen, RWTH Aachen /Aachen University of Technology), 52062 Aachen, Germany (Received 3 April 1997;In final form 10 July 1997) The paper deals with experimental investigations and analyses of unsteady pressure dis- tributions in different axial compressors. Based on measurements in a single stage research compressor the influence of increasing aerodynamic load onto the pressure and velocity fluctuations is demonstrated. Detailed measurements in a 14-stage and a 17-stage gas turbine compressor are reported. For both compressors parameters could be found which are clearly influenced by the aerodynamic load. For the 14-stage compressor the principles for the monitoring of aerodynamic load and stall are reported. Results derived from a monitoring system for multi stage compressors based on these principles are demonstrated. For the 17-stage compressor the data enhance- ment of the measuring signals is shown. The parameters derived from these results provide a good base for the development of another prediction method for the compressor stability limit. In order design an on-line system the classification of the operating and load conditions is provided by a neural net. The training results of the net show a good agreement with different experiments. Keywords." Stall and surge monitoring, Unsteady pressure measurements, Compressor load analysis, Load parameters, Neural nets 1. INTRODUCTION high level. This aim only can be reached by an in- creasing observation and monitoring of the opera- The requirement ofhigh economy of turbomachines tional conditions inside the machine. causes higher efficiencies and power densities with Various efforts have been made to find measuring increasing profile and assembly loads. On the other and analysis methods for the detection of the hand the loads are limited by the requirement of stability limit of compressors (Ludwig and Nenni, operational safety of the machine. Therefore, the 1979; Paduano et al., 1991; Wang et al., 1993). For main aim is the guaranty of the availability on a save compressor operation it is necessary to know Fax: 0241-8888-229. 77 78 H. HONEN the distance of the momentary operation point is detected. Figure demonstrates these effects for from this limit. Therefore, the detection of the two different operating points of the stage. The occurrence of stall is not the only aim of all these radial turbulence distributions for the axial gaps struggles. Moreover, an indicator for the approxi- between the bladings visualize the influence of the mation to the stability limit has to be found. Several aerodynamic load onto the flow in the entire stage. investigations are looking for so called stall pre- Due to the increasing aerodynamic load a corner cursors which can be harmonic waves superposed stall region with fluctuating boundaries occurs in to the flow or other fluctuations which induce the the stator. With higher loads this seperation zone beginning of stall (Inoue et al., 1990; Garnier et al., grows in to the blade passage. Glue on hot film 1990). sensors on the stator vanes provided information Due to the progress in computer development it about the behavior of the unsteady flow. Thus, the is more and more possible to pick up and handle a extend of the corner stall region inside the stator high number of measuring data on-line. Even could be observed. One major result of these inves- unsteady effects can be observed in real time. Thus, tigations was the experience that only sensors out- the on-line calculation and observation of char- side of the separation region were able to measure acteristic values becomes realistic. The combina- periodic fluctuations due to the rotor/stator inter- tion of a suitable definition of detection and action. Measuring sensors positioned inside this observation parameters based on measuring results separation zone can only detect high turbulent together with the corresponding analysis algorithms fluctuations. All periodic information damped enables the operator to run a compressor close to down and does not reach the sensors. the stability limit at high efficiencies. Measurements in a 14-stage gas turbine com- pressor provided detailed information about the unsteady flow behavior in a multi stage compressor 2. EXPERIMENTAL INVESTIGATIONS influenced by different compressor loads. For a long term investigation the stages 11 and 13 were Measurements in three different axial compres- equipped with wall mounted piezo-electric pressure sors show the influence of the aerodynamic load sensors in the axial gaps between rotor and stator. onto the patterns of unsteady flow distributions. The measurements were carried out for a period of Experimental investigations of the unsteady three about four months during industrial operation dimensional flow inside a single stage research under full load conditions of the gas turbine. compressor provided a basis for the understanding During these measurements a failure in the gas of the unsteady effects in separation zones (Gallus turbine control system occurred and the operating and H6nen, 1986). Furthermore, these measuring point of the compressor drifted very slowly towards results visualized the influence of separated flow the stability limit. Finally the surge control of the regions onto the signal form and behavior of wall gas turbine provoked a shut down. mounted dynamic sensors as well as probes. During this time period the pressure sensors The aerodynamic load of the compressor was registered the same effect as demonstrated in the increased up to the stability limit. Measurements single stage compressor. At a certain load level in with hot wire probes in the axial gap between rotor the 13th stage the periodic information disap- and stator demonstrated the changes of the peared. This indicates that here a separation region unsteady flow patterns downstream the rotor. occurred which covered the measuring sensor. In Depending on the higher load the profile boundary order to be able to handle the great number of data layers become thicker which can be detected in from the long term investigation a data reduction wider blade wakes. In addition the stochastic fluc- by FFT analysis was carried out (Fig. 2). About tuations are elevated and a higher turbulence level half an hour before the automatic shut down the AXIAL COMPRESSOR STALL, SURGE PREDICTION 79 Tu 10 IGV rtip Rotor Stator rhub FIGURE Turbulence distribution in the axial gaps of a single stage research center. frequency spectra of the 13th stage only showed covers the wall mounted pressure sensor and high noise levels, whereas in the lth stage the damps down the periodic information coming to characteristic peak was increased caused by the measuring position. growing blade wakes due to the higher aerody- Another investigation was carried out in an namic load (H6nen and Gallus, 1995). industrial gas turbine. On a test field detailed The growing profile boundary layers in the rotor measurements were taken in the 17-stage axial com- are centrifugated to the casing where side wall pressor. The first two stages were equipped with five boundary layer thickness itself is also increased. wall mounted dynamic pressure sensors in the cas- This causes an accumulation of low energy ing over the rotors at several axial positions. In five material behind the rotor. The high back pressure test runs at part load with different operating con- at the compressor outlet disables the exit flow so ditions (Table I) the rotor speed of the machine was that a casing stall occurs. This separated region reduced until the stability limit of the compressor 80 H. HONEN lh sage f(8) t j t 1(9,10) (Y1 13th stage o.o lkl 29001).0 O.n (Hx) 20000.0 FIGURE 2 Comparison of the frequency patterns in the lth and 13th stage for two operating points (left side: normal operation, right side: stall operation). TABLE Comparison of the operation parameters for different test runs Test run VSV position Bleed door #1 Bleed door #2 Bleed door #3 20 Closed Closed Closed 2 0 Open Closed Closed 3 0 Closed Closed Closed 4 20 Closed Closed Closed 5 20 Open Open Closed was reached. The pressure signals were recorded in the static pressure is elevated up to a maximum. real time to a magnetic tape recorder and analyzed Just after the passing of the rotor blade a sharp after the experiments. decrease is observed due to the lower pressure at As an example the time averaged signals of the the suction side of the profile. The last measuring first test run are shown in Fig. 3 for the first position is located in the axial gap between rotor measuring position in stage 1. The patterns of the and stator. Here the flow is influenced by the blade first four pressure transducers show the wall wakes downstream of the rotor. pressure distribution above the passing rotor It becomes obvious that the signal patterns channels for the different sensor positions. From strongly depend on the measuring position. In the the suction side to the pressure side of the channels front part of the blading the signal forms are AXIAL COMPRESSOR STALL, SURGE PREDICTION 30O0 position 4 2000 position 1 1 000 3000 position 2 position 5 20O0 1 000 3OOO 2000 p 3 1 000 ..osition FIGURE 3 Time average pressure signals at the measuring positions over rotor 1. influenced by many different flow effects. In the conditions and the last one shows the conditions last third, especially at measuring position 4 a low about 50 revolutions before the beginning of surge.
Details
-
File Typepdf
-
Upload Time-
-
Content LanguagesEnglish
-
Upload UserAnonymous/Not logged-in
-
File Pages13 Page
-
File Size-