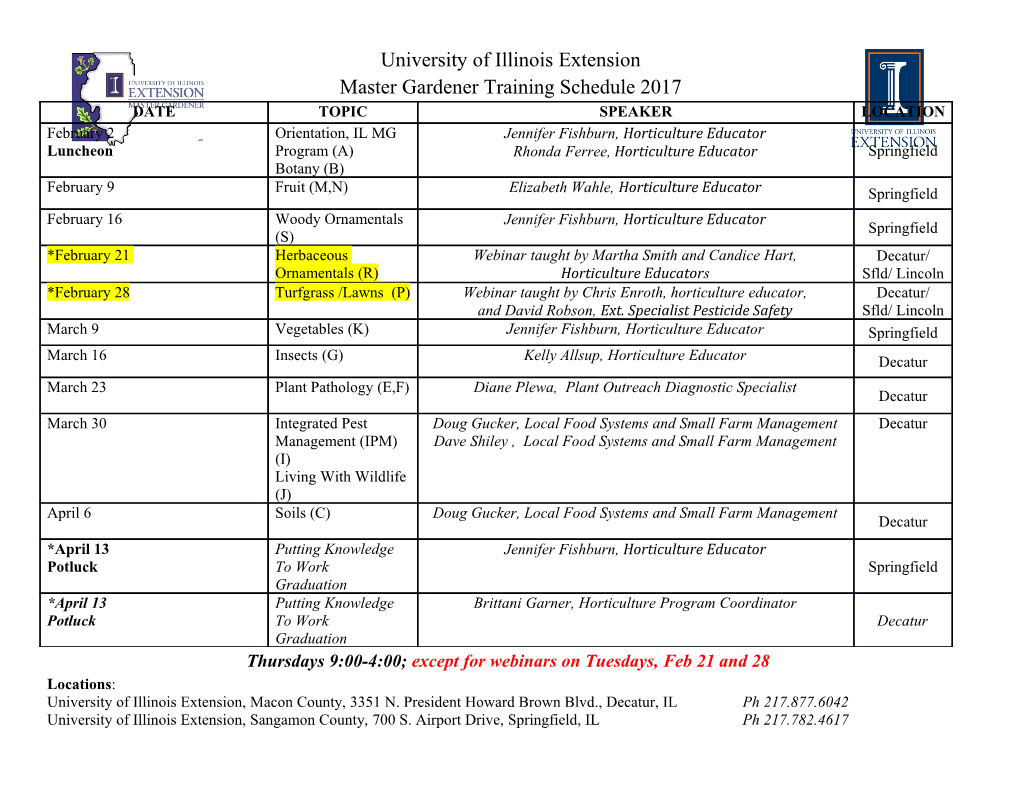
Advanced Computational Methods in Heat Transfer VI, C.A. Brebbia & B. Sunden (Editors) © 2000 WIT Press, www.witpress.com, ISBN 1-85312-818-X Ice melting driven by natural convection in the vicinity of the density maximum G.Vieira' , S. L. Braga* & D. Gobiir* 'Mechanic Engineering Department - UCP, Brazil 'Materials and Mechanic Engineering Department - IME, Brazil ^Mechanic Engineering Department - PUC, Brazil 7608 - CNRS - Paris VI, France Abstract A numerical investigation is presented concerning the melting problem of a vertical ice layer in the presence of horizontal temperature gradients. The main heat transfer mechanism is due to natural convection in water near the density maximum. The solution procedure uses a front tracking method which allows us to solve the fluid flow problem and the interface motion separately. 1 Introduction The phenomena involving solid-liquid phase change are associated with many practical applications of current engineering interest and also in geophysics. Among them, there are, for example, energy storage systems using phase change materials (Stampa and Braga [1]), thermal environmental control, crystal growth processes (Ostrach [2]) and freezing of soil in cold weather regions (Zhang and Nguyen [3]). Many simulation codes have been designed to solve these problems. The first numerical study regarding natural convection involving phase change of a pure substance and considering the finite volume method was done by Sparrow et al. [4]. A purely numerical comparison exercise may be found in Bertrand et al. [5], which compares different numerical procedures applied to a simple melting problem. The main mathematical difficulty comes from the non- linearity due to the moving of the liquid-solid interface and natural convection effect. Due to extra difficulty introduced by the presence of a density maximum in the temperature range of interest, the problem of ice melting has received much less attention, except in the case of the horizontal layer, where the complexity of the stability problem has justified a number of studies. The literature concerning Advanced Computational Methods in Heat Transfer VI, C.A. Brebbia & B. Sunden (Editors) © 2000 WIT Press, www.witpress.com, ISBN 1-85312-818-X 228 Advanced Computational Methods in Heat Transfer VI heat transfer during the melting process of ice in a confined space appears to be mostly restricted to the cylindrical geometry [6-7]. This kind of problems find many applications such as ice thermal storage techniques for the air-conditioning, production of ice, oceanographic studies dealing with iceberg melting. Fluids like water, tellurium, liquid bismuth, antimony and gallium exhibit a maximum density near their freezing points. Then, the usual linear approximation of the temperature effect on density is not valid near this region, which becomes the problem more complex. Numerical and experimental studies may be found regarding natural thermal convection with maximum density (Lin and Nansteel [8]; Bennacer et al [9]). When also accounting the influence of the phase change, the need of more specific testing is clear. Schutz and Beer [10] developed a study, in which they analyzed the fusion of ice in salt water, involving thermosolutal natural convection. Braga and Viskanta [11] and Kowalewsky and Rebow [12] conducted works considering solidification of water in a maximum density environment inside rectangular cavities. Tsai et al [13] studied the maximum density effect on laminar water pipe flows solidification. This work is motivated by the need to gain a more complete understanding of the heat transfer process during solid-liquid phase change in connection with natural convection and a density maximum. Particularly, it is analyzed the melting of a vertical ice slab upon a gravitational field. 2 Mathematical modeling The process being studied occurs inside a rectangular cavity (height //, width L, Fig. 1) containing a pure substance at its fusion temperature, To=T^. Initially, half the material's volume is in a solid state, while the other half is in a liquid state. The solid material is isothermal to the fusion temperature while one of the vertical walls of the cavity is heated. Therefore, the entire process is controlled by natural convection during the liquid phase. At /*=#, the system receives energy through the vertical wall at the liquid side, heated at T//>7}^. The opposite wall is maintained isothermal at TQ. Horizontal walls are adiabatic. The position of the melting front is defined by a space and time function, c* (z*, t*). This relation is equal to the horizontal distance between the heated wall and the melting front at height z*. Since the governing equations will be nondimensionalized later, the asterisk superior index (*) has been used to indicate the dimensional variables. LJ adiabalie surface Liquid Solid Phase Phase H A//) ^ adiabatic surface Figure 1 - Problem definition, t* =0. Advanced Computational Methods in Heat Transfer VI, C.A. Brebbia & B. Sunden (Editors) © 2000 WIT Press, www.witpress.com, ISBN 1-85312-818-X Advanced Computational Methods in Heat Transfer VI 229 The hypothesis below were assumed: - The flow is laminar and two-dimensional; - The liquid material is Newtonian and incompressible; - The fluid's physical properties are constant, except for density in the buoyancy force term; - The viscous dissipation is negligible; - The density change of the material upon melting is neglected; - It is assumed that the velocity of propagation of the melting front is several orders of magnitude smaller than the fluid velocities in the boundary layers on the vertical walls. This suggests that it is possible to divide the process in a number of quasi-static steps, separating, therefore, the melting front motion calculations from the natural convective calculations. Based on the above hypothesis, the governing equations used in the liquid domain can be written in their dimensionless form as following: V*V=0 (1) — V^8 (3) Pr The equations shown above were included in their dimensionless form using as reference length, height //of the cavity and the cinematic viscosity u for velocity and time. Therefore: y = y*/H, z = z*/H, r=7*H/u, t = t*»/H*, P = P*v/H^ e c(z,t) = c* (z* ,t* )jH , in which V is the dimensionless velocity vector; P is the dimensionless pressure; p^y is the reference density (equal to the average density of the period imposed by wall temperatures) and k is the unitary vector in the vertical direction. The dimensionless temperature is defined by 6 = (r - 7^,]/Ar, where the average temperature given by Tw=(Tf] + Tpuj)/2 , T is the dimensional temperature and AT" = 7// - Tp^ . The Prandtl number is given by Pr = u / a , being a the thermal diffusivity. At the moving interface, the energy balance equation is: V6#»=— (4) di dc where — represents the local velocity of the melting front along /?, the normal dr vector to the interface and i =Ste x Fo with Stefan number given by Ste - CpATY Lp , being Cp the specific heat and Lp the latent heat. The boundary conditions were specified aty and z. Along z = 0: 0 (5) Advanced Computational Methods in Heat Transfer VI, C.A. Brebbia & B. Sunden (Editors) © 2000 WIT Press, www.witpress.com, ISBN 1-85312-818-X 230 Advanced Computational Methods in Heat Transfer VI w and v being the vertical and horizontal components of the dimensionless velocity vector V. Along the top horizontal wall, where z= 1: dQ(y,l)/dz = 0; w(y,l) = 0; v(y,l)=0 (6) Along the left vertical wall, wherey=0: Q(0,z) = 0,5; w(0,z) = 0; v(0,z) = Q (7) Along the melting front, where >>=c(z,f): Q(c(z,t),z) = —0,5; w(c(z,t),z) = 0; v(c(z,t),z) = 0 (8) Density approximation proposed in the buoyancy term. For a temperature range below 10°C, the approximation proposed by Gebhart and Mollendorf [14] presents good results and is given by the equation: ,/,\ (9) where y is the phenomenological coefficient; for water: y = 8 x Iff* °C* and q=2; Pref is the maximum fluid density, also denominated p^; T^ is the temperature of the maximum density, also denominated TM , for water TM=3,98 °C. m this case, the number of Grashof appears modified and is based on the cavity height and on the maximum temperature interval, given by: g.^.Y.(A^)' - 3 - ^ ' i) The modified Rayleigh number is: hi order to understand the meaning of the maximum temperature interval A7^,we should consider that the variation effect of p is approximately symmetric in relation to the maximum density. The formulation, which refers to the maximum density, predicts a bicellular flow. On the other hand, the linear approximation predicts a unicellular flow. Therefore, as the density variation is approximately symmetric in relation to TM, the greatest cell will generally appear at the side where the TM temperature is of greatest importance. Consequently, the smallest cell will be situated at the wall side where the temperature is nearest to T^. Therefore, the relative density variation, which induces the flow in each of the cells, is directly linked to the intervals between TM and Advanced Computational Methods in Heat Transfer VI, C.A. Brebbia & B. Sunden (Editors) © 2000 WIT Press, www.witpress.com, ISBN 1-85312-818-X Advanced Computational Methods in Heat Transfer VI 23 1 the wall temperatures given by: TH-TM (12) TM-TO (is) As heat transfer at the greatest cell dominates energy transfer at the cavity, the Grashof and Rayleigh number were defined, modified based on A7^ , as: (14) The coordinates were transformed with the objective of mapping the irregular space occupied by the liquid in a rectangular computational space. This work uses the same Manseur [15] coordinate transformation method, which was adapted to the phase change problem.
Details
-
File Typepdf
-
Upload Time-
-
Content LanguagesEnglish
-
Upload UserAnonymous/Not logged-in
-
File Pages10 Page
-
File Size-