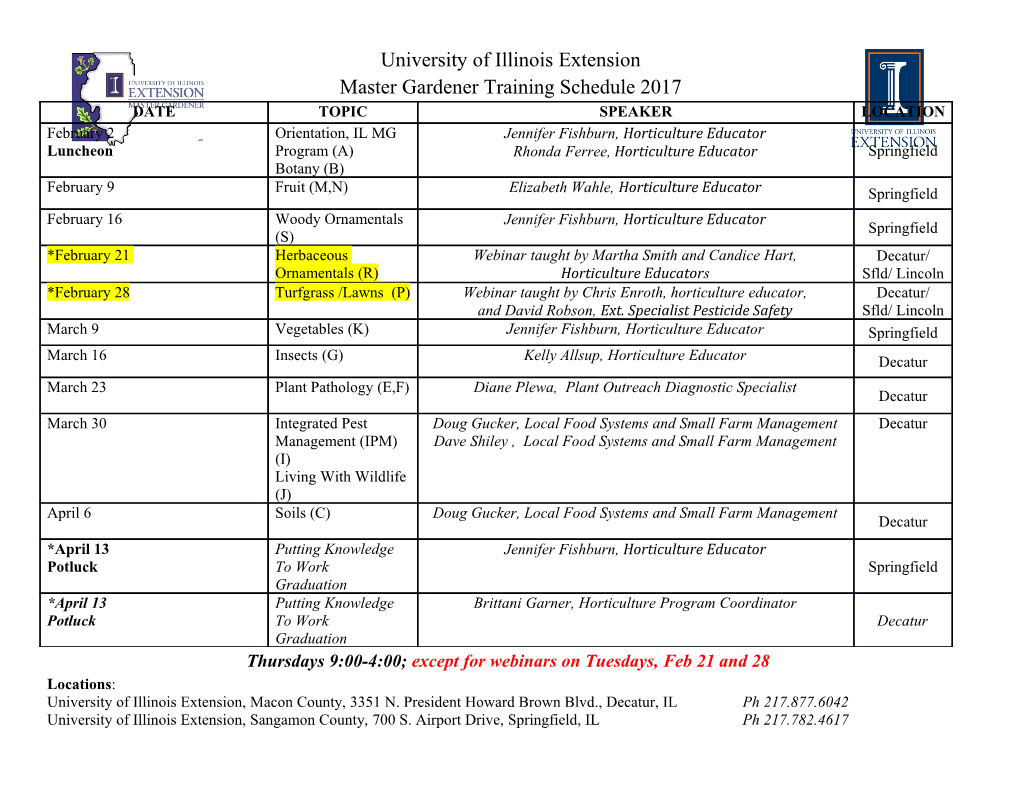
Newsletter | Your update on what’s new from DENSO Aftermarket Sales Issue number 46 | July/August 2015 Menu > Follow the links below! Inside this issue… > DENSO Lambda Sensors: manufacturing expertise > Out now! Latest Starters & Alternators > AEC became DENSO’s first engineering base for diesel range extension engine component applications outside Japan. > automotive Diamonds wins Loyalty Award > EE region: tradeshows round-up Opening of expanded Aachen > DENSO goes to Hollywood Engineering Centre heralds > May we introduce… new era of DENSO innovation Further demonstrating its European capability to design, said Masato (Max) Nakagawa, DENSO International Europe’s newly appointed develop, engineer and test parts and systems from President, CEO & CTO. “We are a vehicle-wide perspective, DENSO AUTOMOTIVE particularly proud of the all-new electronic Deutschland GmbH, a subsidiary of Japan-based DENSO laboratory. We can now offer in-house development of hardware and software Corporation, has expanded its Aachen Engineering for engine control units (ECU) used Centre (AEC). The opening ceremony took place at the on diesel and gasoline engines. newly expanded site in Wegberg, Germany on 2nd June. This laboratory also facilitates the accommodation of electric and hybrid The latest expansion means that AEC new European powertrain development technologies to European specifications. has the capacity to serve its European and shared their vision of further growth. The European region plays a global customers in the areas of powertrain, leadership role in the automotive industry electronics and electrical systems. Compared to the original engineering with respect to the creation of advanced At the opening ceremony, new AEC centre, which was opened in 2005, the technologies and innovative designs. Director Kenzo Yano welcomed guests facilities and offices have been enlarged The reinforcement of our local engineering from DENSO Japan, construction from 2,110 to 9,500 square metres. and development capability is key to company Takenaka Europe, pm5 AEC became DENSO’s first engineering DENSO’s success.” Projektmanagement, and all AEC base for diesel engine component associates present. applications outside Japan. It was further As an added milestone, AEC associates expanded in 2010, with powertrain surprised Mr. Nakagawa with “thank you” DENSO Japan (DNJP) Executive component engineering becoming part messages for 10 years of dedication to Director Yukihiro Shinohara, Head of the of the centre’s expertise. AEC and its growth, and a large bouquet Diesel and Gasoline Injection Business of congratulatory flowers, celebrating his Unit, and Katsuhiko Takeuchi, Head of “With the expansion of AEC, we are promotion and new position within the DNJP Diesel Business Unit, hailed the laying the foundation for our future”, European DENSO organisation. www.denso-am.eu 2 DENSO Newsletter: Your update on what’s new from DENSO Aftermarket Sales Issue number 46 | July/August 2015 DENSO Lambda Sensors: > Lambda sensors, also referred to as oxygen (or O2) sensors, are the most manufacturing expertise important sensors for engine control. meets ceramic craftsmanship Since launching in 2008 lambda sensors have become Although such control devices improved in quality and reliability, they proved an integral part of modern car engines. DENSO extremely costly in large-scale production. explains why this is and how its pioneering sensor Longer development times for specific part technology offers OEMs and the aftermarket optimised applications also meant that the original objectives of developing a wider variety efficiency and environmental performance. of vehicle specifications, creating market demand for fuel efficiency and increasing The Introduction of EMS The performance of the engine was emission standards were not being largely defined by pre-set properties efficiently met. In the old days, the engine of a car was of the carburettor, valve positions and controlled by a so-called open loop control the distributor. Most of these components The search for a low-cost flexible system. The engine could run smooth, were electro-mechanical, and to a solution was found by adopting rough, or not even at all, and to adjust large extent were subject to wear, technical design principles from the this required certain changes to various vibrations, moisture, heat, and other electronic industry. In the 1970s, vehicle components. These components primarily well-known enemies of such devices. manufacturers started to change their regulated air and fuel supply, as well as These systems were not only labour- engine control by slowly implementing compression, ignition and combustion intensive to maintain but also sensitive what is nowadays known as Engine cycle timings. to malfunctions. Management Systems (EMS). DENSO Newsletter: Your update on what’s new from DENSO Aftermarket Sales Issue number 46 | July/August 2015 3 Lambda sensors in EMS How EMS systems work: Lambda sensors, also referred to as A technical overview oxygen (or O2) sensors, are the most important sensors for engine control, • Several sensors monitor critical processes in and around the engine, providing feedback to the Electronic and provide signals to the engine Electronic Control Unit (ECU). Control Unit (ECU) on how well the engine is performing. The concept behind this is • The ECU processes the information and based on programmed rules both a simple and brilliant one. decides which actions to take. • Several actuators receive instructions from the ECU to adjust certain A lambda sensor is an electronic device parameters (for example the injection timing, EGR valve aperture, ignition that measures the concentration of oxygen advance angle, fuel pump pressure, etc). (O2) in the exhaust gas from an engine, relative to the outside air. The engine ECU • The result of this is again monitored by the sensors, and a closed control uses the signal from the lambda sensor to loop is realised. understand if the engine is running within Optimal control Engine condition precise specifications. The most important of actuators information specification to monitor is the air-fuel Engine ratio. In relation to each other, either too ECU much fuel or air entering the combustion chamber can cause serious long-term Actuators Sensors engine failure. Both situations can be • Ignition coil EMS • Mass Airflow recognised very reliably and accurately by • Injector (Engine Management System) Sensor the lambda sensor. Based on its feedback • Throttle motor • Water temperature sensor signal, the engine ECU adjusts the amount • EGR Valve • Fuel Pump etc. Engine • O2 sensor of fuel injected into the engine. In order for • Knock sensor etc. the sensor to work effectively, it must be located in or near the exhaust manifold. These lambda sensors are known as Engine information regulating sensors. Engine control detection The lambda sensor also completes • Modern vehicles use multiple ECUs, and EMS is integrated in the overall additional functions within modern engine vehicle electronic system. This system allows communication between several configurations including diagnosing the ECUs (e.g. for infotainment, safety or air-conditioning). effectiveness of catalyst converters, • EMS systems are still developing into ever-more efficient systems, with the referred to as diagnostic sensors. further advancement of sensors, computers and actuators. DENSO Ceramics • Newer and more efficient propulsion systems mean more sophisticated EMS systems and newer generation types, such as the hybrid system. DENSO Ceramics Division is a key division of DENSO, creating products based on so-called “Technical Ceramics” that can consists of electrically insulating and manufacturers worldwide to develop and be found in many applications. Developing, heating while exposed to aggressive produce such sensors, exclusively for the engineering and manufacturing products internal engine conditions. OE business. with these high-tech materials relies on genuine craftsmanship and requires However, instead of acting, certain Because this type of sensor offered considerable expertise. ceramic compounds can also be used great reliability and accuracy, vehicle to sense specific conditions. As soon as manufacturers were able to offer a wider DENSO is globally well-known for the EMS systems emerged, DENSO Ceramics range of engine configurations for specific superb quality of two other products Division recognised the opportunity to market demands. Soon, lambda sensors coming from this division: spark plugs develop sensors that convert oxygen were a standard part of the EMS system. and glow plugs. Those products are concentrations in gasses into an electric both engine actuators, performing an voltage. Zirconium dioxide has the ability Since those early years, improvements electromechanical task based on unique to do this when heated over 400 degrees have been made to activate the sensor properties of ceramic materials which centigrade. DENSO was one of the first faster in order to generally quicken the 4 DENSO Newsletter: Your update on what’s new from DENSO Aftermarket Sales Issue number 46 | July/August 2015 Lambda sensors: A historic overview and thermal shock. To ensure a long lifetime, DENSO sensors benefit from 1976: First applications 1982: O2 sensor 1996: 1st generation 2000: Planar O2 sensor 2013: 5th generation (Volvo) with heater A/F sensors (thimble A/F sensors (PLUS 6) unique protective measures, such as their design) 2004: 3rd generation 1977: DENSO develops 1984:
Details
-
File Typepdf
-
Upload Time-
-
Content LanguagesEnglish
-
Upload UserAnonymous/Not logged-in
-
File Pages11 Page
-
File Size-