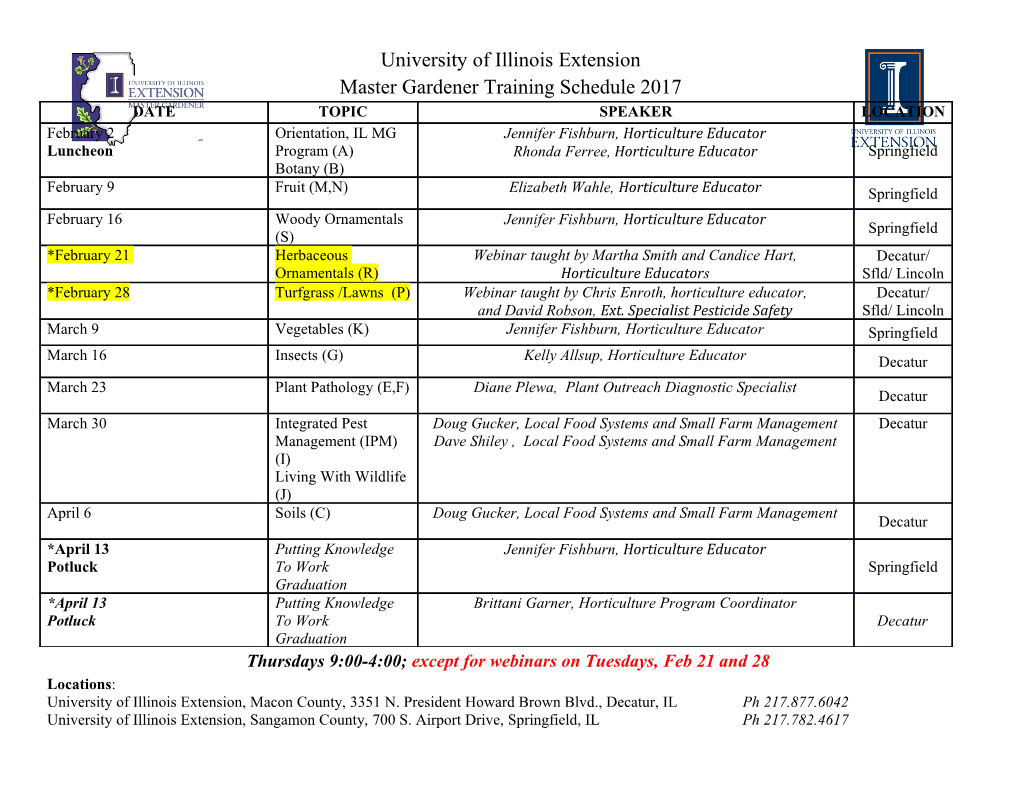
ON THE PLAYABILITY OF STRINGED INSTRUMENTS This dissertation is submitted for the degree of Doctor of Philosophy 3 October 2003 Paul M Galluzzo, Trinity College Supervisor: Professor J Woodhouse To Mom i ACKNOWLEDGEMENTS In the period between October 2000 and September 2003, I have had the good fortune to have as supervisor Professor J. Woodhouse, to whom very special acknowledgement is due for his most valuable advice and encouragement. Other individuals who at some point contributed to the production of this thesis or the research presented herein include: Hugh, Srikanth, Garreth, Len, Paresh, Dan, Jonathan, Paul R., Frank, David M., Robin, Glenn, Mom and Dad, Philippe, Jan, Simon, Ken, Sondipon, Derek, David T., Susannah, James, Andrew, Tim, Peter, Malcolm, Keith, Jo, Andrew P., Andrew G., Hannah, and of course Eleanor and Beatrice1. And finally, Clare G. deserves a special mention for bravely volunteering the use of her cello in this project. This project was financially supported by the Engineering and Physical Sciences Research Council. The ongoing love and support of Rachel underpins the writing of this dissertation and the research behind it. 1For future reference: Hugh Hunt (lecturer, PhD advisor), Srikanth Phani (DVRO), Garreth Ryder (technician), Len Howlett (technician), Paresh Date (control group), Dan Auger (control group), Jonathan Paxman (control group, anti- windup), Paul Roberts (control group, floating point precision, optical encoder), Frank Dolman (technician), David Miller (chief technician), Robin Langley (professor, head of DVRG), Glenn Vinnicombe (lecturer, control group), Mom and Dad, Philippe Duffour (DVRO), Jan Maciejowski (lecturer, now head of control group), Simon Smith (technician, electronics), Ken Johnson (professor, tribology), Sondipon Adhikari (DVRO), Derek Smith (lecturer, experiment), James Talbot (DVRO), Andrew Pick (DVRO), Andrew Grime (DVRO), Tim Love (computing), Peter Clarkson (computing), Malcolm Smith (lecturer, control group), Keith Glover (control group, now head of dept.), David Trippett (pianist), Susannah Ticciati (cellist), Jo Moodie, Andrew Moodie, Hannah Moodie, and of course Eleanor and Beatrice Outram (daughters of Martin Outram, who chose creative names for the robot). And finally, Clare Gilmour. ii FOREWORD As first noticed by Helmholtz, strings vibrate in a “V-shape” when they are bowed correctly and a full tone is produced, where the vertex of the “V” shuttles back and forth along the visible envelope of the string’s motion. If the instrument is bowed incorrectly, i.e. the instrument does not “speak”, then this “Helmholtz motion” is not produced, and the shape of the string as it vibrates will be quite different. The goal of this research is to gather experimental data from a stringed instrument and use it in the on-going development of a theoretical model of the mechanics of the bowed string, which can be used to investigate which aspects of the violin, strings or bow influence the ease with which this “Helmholtz motion” can be produced. The design, testing and application of a robotic bowing machine are described, which has allowed the speed and force of a bow as it plays a cello to be controlled. Extensive measurements of various aspects of the motion of a cello string being bowed by the bowing machine are presented, and compared with predictions from nominally similar theoretical models. Although certain models do reflect the qualitative behaviour seen in experiment under some conditions, all show vast room for improvement. Aspects of theoretical predictions that are at odds with experimental results, and would therefore impede efforts to use theoretical modelling in the design of a more “playable” violin, are subse- quently described. Shortcomings of each model are attributed to physical defects of the theories underpinning them, and various modifications are discussed and tested. This dissertation is the result of my own work and includes nothing which is the outcome of work done in collaboration except where specifically indicated in the text. iii CONTENTS Acknowledgements i Summary ii Contents iii List of figures vii Nomenclature xi 1 Background 1 1.1 Literature review . 3 1.1.1 Modelling the bowed string . 3 1.1.2 Application of theory to playability . 19 1.2 Aim and structure of thesis . 26 2 Experiment I: physical apparatus and feedback control 29 2.1 Alternative design concepts . 30 2.2 Design strategies for feedback controllers . 31 2.2.1 Design requirements . 31 2.2.2 Force control . 32 2.2.3 Speed control . 38 2.2.4 Controller implementation environment . 39 2.3 Measurement techniques . 40 2.3.1 Measurement of bow/string contact force . 40 2.3.2 Speed measurement . 42 2.4 Detailed mechanical design . 43 2.5 Summary . 49 3 Experiment II: analyzing and improving performance 50 3.1 Performance of speed controller . 51 3.1.1 Velocity and acceleration step responses . 51 3.1.2 Fine-tuning the existing feedback controller . 53 3.1.3 Anti-windup techniques . 54 iv 3.1.4 Open-loop controller used to boost response time . 55 3.1.5 The worst case . 58 3.2 Performance of force controller . 59 3.2.1 Force controller step response . 59 3.2.2 Maintaining constant force during position variation . 60 3.3 Summary: combined performance . 63 4 Experiments with rigid point bow 65 4.1 Experimental setup . 66 4.2 Bridge force measurement . 67 4.2.1 Data acquisition . 68 4.2.2 Bridge force “signature” waveforms . 69 4.2.3 String vibration waveform identification algorithm . 72 4.3 Maps of vibration waveform . 78 4.3.1 Schelleng diagram: vibration regime in the N-¯ plane . 78 4.3.2 Guettler diagram: pre-Helmholtz duration in N-a plane . 86 4.3.3 Vibration regime in the N-vb plane . 105 4.4 Summary of findings . 115 5 Simulations results 118 5.1 Simulations with steady sliding friction curve . 119 5.1.1 Schelleng diagram: vibration regime in the N-¯ plane . 119 5.1.2 Guettler diagram: pre-Helmholtz duration in N-a plane . 125 5.2 “Reconstructed friction curve” simulations . 130 5.2.1 Schelleng diagram: vibration regime in the N-¯ plane . 131 5.2.2 Guettler diagram: pre-Helmholtz duration in N-a plane . 136 5.3 “Plastic thermal model” simulations . 138 5.3.1 Schelleng diagram: vibration regime in the N-¯ plane . 138 5.3.2 Guettler diagram: pre-Helmholtz duration in N-a plane . 147 5.4 Summary of findings . 152 6 Improving simulations in light of experiments 155 6.1 Interpreting experiments and simulations . 156 6.2 Friction at first slip . 158 6.2.1 Interpreting the experimental observations . 158 6.2.2 Incorporating contact area growth into simulations . 160 6.2.3 Results from simulations with contact area growth . 160 6.2.4 Creep distance . 162 6.3 “Overshoots” with reconstructed friction curve . 162 6.4 Plastic thermal model: the ky vs. £ curve . 166 6.4.1 ¹s at first slip is too large . 167 6.4.2 Flybacks in bridge force at first slip . 167 6.4.3 Overheating at high bow speeds . 170 6.4.4 Helmholtz motion into double slipping . 173 6.5 Modelling creep . 175 6.5.1 Flybacks at first slip that are not steep . 175 6.5.2 Apparent creep before first slip . 176 6.5.3 Other evidence of creep . 178 v 6.6 Summary of findings . 180 7 Experiments with real bow 182 7.1 Experimental setup . 183 7.2 Results . 184 7.3 Summary of findings . 191 8 Conclusions and future work 192 8.1 Main findings of thesis . 192 8.2 Suggestions for future investigation . 195 Bibliography 197 vi LIST OF FIGURES 1.1 illustration of Helmholtz motion . 1 1.2 string model used by Raman . 3 1.3 Friedlander’s graphical construction for the calculation of f and v . 5 1.4 Friedlander’s ambiguity, plotted in the f vs. v plane . 6 1.5 space-time diagram of waves travelling along the string with reference to simulations . 8 1.6 reflection model used by Cremer . 8 1.7 space-time diagram of transverse and torsional waves travelling along the string . 10 1.8 Illustration of the cause of “differential slipping” for bows with finite width . 13 1.9 McIntyre, Schumacher and Woodhouse’s “two-haired bow” . 13 1.10 Two alternative models used to describe the compliance of bow hair . 14 1.11 illustration of thermally-induced hysteresis in friction vs. velocity plane . 16 1.12 “thermal viscous” model for rosin friction . 17 1.13 “thermal plastic” model for rosin friction . 18 1.14 Schelleng diagram . 20 1.15 string displacement at the start of a “perfect transient” . 23 1.16 space-time diagram of the two waves generated at the start of a “perfect transient” . 25 2.1 alternative designs for bowing machine . 30 2.2 feedback compensator configuration . 31 2.3 typical bowing gesture . 32 2.4 example of the success of the transfer function identification technique . 33 2.5 initial mechanical design . 35 2.6 frequency response of rod (“bow”), with old mechanical design . 36 2.7 frequency response of rod (“bow”), with new mechanical design . 36 2.8 block diagram of feedback controller used to control force . 37 2.9 equivalent mechanism for linear motor alone . 38 2.10 equivalent mechanism for linear motor with feedback compensator . 39 2.11 position of strain gauges to indirectly measure bow force . 41 2.12 calculation of contact force using strain gauge . 41 2.13 calibration curve for strain gauge . 42 2.14 schematic drawing of bowing machine . 43 2.15 photograph of apparatus . ..
Details
-
File Typepdf
-
Upload Time-
-
Content LanguagesEnglish
-
Upload UserAnonymous/Not logged-in
-
File Pages217 Page
-
File Size-