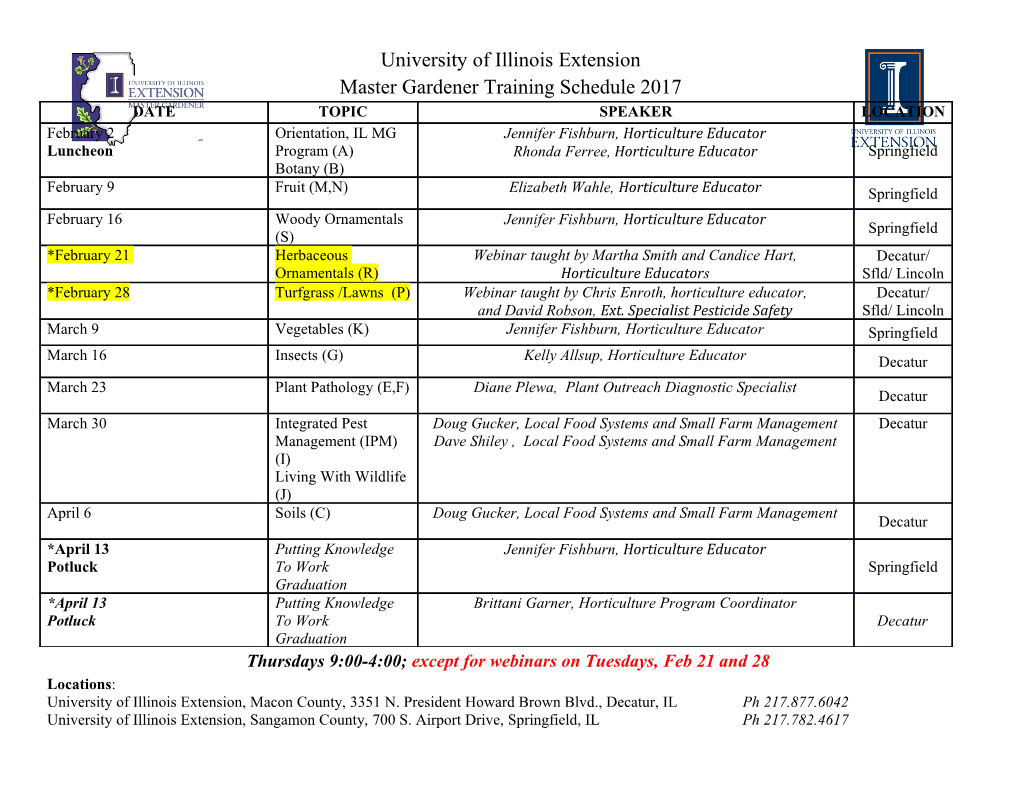
Secondary Air Interaction with Main Flow in Axial Turbines by Metodi B. Zlatinov B.S.E. Mechanical and Aerospace Engineering Princeton University (2009) Submitted to the Department of Aeronautics and Astronautics in partial fulfillment of the requirements for the degree of Master of Science in Aeronautics and Astronautics at the MASSACHUSETTS INSTITUTE OF TECHNOLOGY June 2011 c Massachusetts Institute of Technology 2011. All rights reserved. Author.............................................................. Department of Aeronautics and Astronautics May 19, 2011 Certified by. Choon S. Tan Senior Research Engineer of Aeronautics and Astronautics Thesis Supervisor Accepted by . Eytan H. Modiano Associate Professor of Aeronautics and Astronautics Chair, Graduate Program Committee 2 Secondary Air Interaction with Main Flow in Axial Turbines by Metodi B. Zlatinov Submitted to the Department of Aeronautics and Astronautics on May 19, 2011, in partial fulfillment of the requirements for the degree of Master of Science in Aeronautics and Astronautics Abstract Secondary air, known as purge air, is injected through seals in the hub and shroud of axial turbines to prevent hot gas ingestion into the endwall cavities. An investiga- tion into the interaction of purge flow with turbine main flow has been undertaken, to determine where losses are generated, how they are generated, and what are the most effective ways for reducing them. The effect of purge flow design on the sys- tem's susceptibility to ingestion was also studied. Tools developed for accomplishing these objectives include: a consistent framework for isolating entropy generated due to viscous effects, a procedure for factoring out individual loss categories, and a linear model for secondary air flow response to the main flow pressure field. These tools, applied to steady computations, elucidate four routes through which change in loss generation is brought about by purge air injection: a shear layer between purge and main streams, modification of the secondary flow through the blade passage, an in- crease in degree of reaction, and the potential for reducing tip clearance flow (for the case of purge flow injected from the shroud). It was further determined that purge air mass flow and swirl velocity are effective parameters for mitigating loss, with a potential for 70% reduction in purge flow losses. By contrast, purge slot ax- ial inclination and gap width do not affect the loss characteristics of purge flow by more than 6%. The benefit of pre-swirling purge flow can be negated by decreased sealing effectiveness, if ingestion is driven by the pressure non-uniformity associated with the rotor upstream influence. However for a representative vane-rotor stage, in which the vane-induced circumferential pressure non-uniformity dominates in the intra vane-rotor gap, pre-swirling purge flow can be beneficial to deterring hot gas ingestion. Finally a framework has been formulated for assessing the time-averaged impact of unsteady vane-rotor interaction on purge flow-induced loss generation. Pre- liminary results suggest that flow unsteadiness can result in substantially higher losses associated with purge flow injection. Thesis Supervisor: Choon S. Tan Title: Senior Research Engineer of Aeronautics and Astronautics 3 4 Acknowledgments The work presented in this thesis took shape over the course of two exciting years, and through the synergistic efforts of a myriad of people. Here, I would like to express my gratitude to those colleagues, teachers, friends, and family who have also taught me much that cannot be included in the following chapters. Let me begin by thanking my research adviser, Dr. Choon Tan. His tactful guidance has helped me overcome the numerous challenges that inevitably threaten to discourage a graduate student at every turn. Every time I have walked across the hall, in a mild state of panic, to convince him that the latest impasse is a definitive one, he has cheerfully suggested otherwise. And though I was often incredulous, with admirable patience, he has let me go off and convince myself in my own way. His vote of confidence has given me the opportunity to explore ideas, take responsibility for my work, and internalize knowledge that would have otherwise simply brushed me by. I am indebted to many colleagues at Siemens Energy, starting with Dr. Matt Montgomery and Dr. Tito Islam, who coordinated the collaboration between MIT and Siemens. Dr. Montgomery's experience in the field, and his remarkable ability to paraphrase a not-so-eloquent graduate student's words into something coherent, have been invaluable assets to our team. I am very grateful to Dr. Barry Brown, who designed the turbine stage for this project, and to Melissa Harris, who got the project off the ground. The computational results Melissa provided me with put me months ahead in my work. Manoj Singh was also a wonderful help, taking over from Melissa and providing many additional results. I thank Dr. Dave Little and Dr. Dave Canon for participating in many discussions, providing valuable insight into industry practices. In addition, Dr. Little's thought-provoking comments always challenged me to be thorough in my work. Dr. Todd Ebert has also been extremely kind and willing to help, going out of his way to provide me with detailed replies to numerous question. And of course, I am thankful to Siemens CKI, an MITEI Sustaining Member, for funding this work, as well as Eni S.p.A., for supporting me 5 with a generous fellowship for the first nine months at MIT. A very special thanks goes out to Professor Nick Cumpsty, for the illuminating discussions that helped guide our research. I was always impressed by the insightful comments he would give, after being briefed on half a year's worth of progress in a mere one hour. My fellow lab-mates have also been a great support and source of knowledge, especially Jeff Defoe, who helped me get CFX up and running on our computer cluster. Lastly, and most importantly, I thank my family - my sister, who's example I have followed since I was old enough to know right from wrong; my mother, who has guided and encouraged me with a patient, devoted, and invisible hand; and my caring and kind wife-to-be, Ashley, who brings balance and harmony to my days. 6 Contents 1 Introduction 23 1.1 Literature Review . 24 1.2 Objectives of Present Work . 25 1.3 Contributions and Findings . 26 1.4 Organization . 27 2 Research Approach 29 2.1 Multiple Levels of Modeling . 29 2.2 Purge Flow Design Parameters . 31 2.3 Computational and Analytical Tools . 32 2.4 Using Entropy as a Measure of Loss . 34 2.4.1 Entropy generation and lost work . 35 2.4.2 Volumetric entropy generation rate . 35 2.5 Summary of Research Approach . 37 3 Loss Accounting with Entropy 39 3.1 Viscous Losses vs. Thermal Mixing Losses . 39 3.1.1 Conceptual delineation of viscous and thermal mixing losses . 40 3.1.2 Practical delineation of viscous and thermal mixing losses . 43 3.2 Utility and Challenges of Volumetric Entropy Generation Rate . 46 _ 000 3.2.1 Challenges in direct evaluation of Sgen ............. 46 _ 000 3.2.2 Challenges in indirect evaluation of Sgen ............ 48 3.3 Summary of Loss Accounting with Entropy . 52 7 4 Baseline Losses 53 4.1 Loss Distribution for Baseline Turbine Stage . 53 4.2 Delineating Loss Sources . 54 4.3 Implications of Loss Source Delineation . 58 4.4 Summary of Baseline Losses . 60 5 Purge Flow-Induced Losses 61 5.1 Where are Purge Flow Losses Generated? . 61 5.2 Viscous Shear Layer . 65 5.2.1 Axisymmertic nature of the shear layer . 65 5.2.2 Control volume analysis of shear layer loss . 66 5.3 Purge-Secondary Flow Interaction . 68 5.3.1 Definition of secondary flow . 69 5.3.2 Role of hub passage vortex . 70 5.3.3 Velocity gradients dominating secondary flow loss . 72 5.3.4 Traceability of purge-secondary flow interaction loss . 74 5.4 Losses due to Change in Reaction . 78 5.5 Purge-Tip Clearance Flow Interaction . 79 5.6 Implications for Purge Flow Upstream of First NGV . 83 5.7 Summary of Purge Flow Loss Mechanisms . 83 6 Quantifying Effects of Purge Flow Design on Loss 85 6.1 Design Guidelines . 85 6.1.1 Delineating between loss mechanisms . 87 6.1.2 Effective design parameters . 88 6.1.3 Ineffective design parameters . 89 6.2 Comparison to Published Results . 91 6.3 Summary of Design Guidelines . 93 7 Effects of Purge Flow Design on Ingestion 95 7.1 Effect of Purge Flow Swirl on Ingestion . 95 8 7.2 Hypothesis . 97 7.2.1 Analogy to spring-mass-damper system . 97 7.2.2 Time-scale argument . 100 7.3 Linear Analysis of Ingestion . 102 7.3.1 Linear analysis transfer functions . 102 7.3.2 Criterion for ingestion based on linear analysis . 107 7.3.3 Criterion for ingestion vs. CFD results . 110 7.3.4 Criterion for ingestion for unsteady flow . 113 7.4 Summary of Ingestion due to Swirl . 116 8 Unsteady Effects on Purge Flow Loss 119 8.1 First Approach for Determining Loss in Unsteady Flow: Appropriate Averaging of Entropy . 120 8.1.1 Appropriate averaging of entropy for unsteady flow . 120 8.1.2 Demonstration of mass/time-averaged entropy method for de- termining loss . 121 8.1.3 Eliminating thermal mixing loss due to purge flow . 124 8.1.4 Consequences of injecting purge flow at a temperature identical to the main flow temperature . 126 8.1.5 Summary of first approach for determining loss in unsteady flow 130 8.2 Second Approach for Determining Loss in Unsteady Flow: Appropriate Averaging of Temperature and Pressure .
Details
-
File Typepdf
-
Upload Time-
-
Content LanguagesEnglish
-
Upload UserAnonymous/Not logged-in
-
File Pages157 Page
-
File Size-