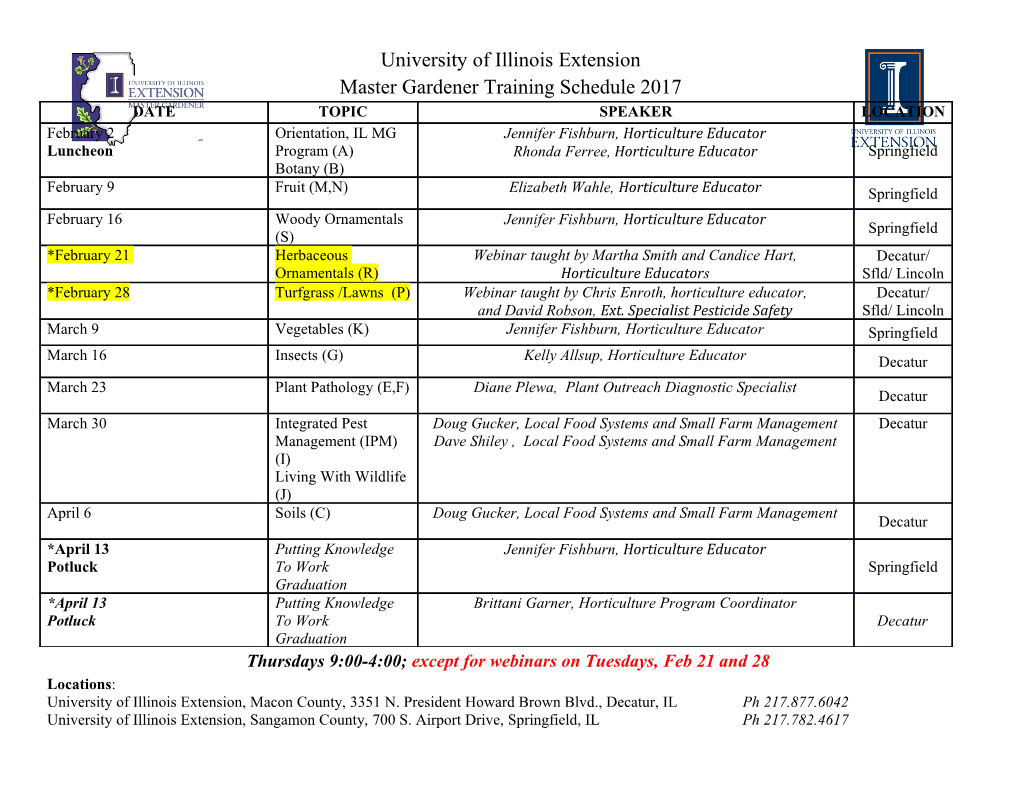
Europa,schesP_ MM M II II INI Ml IN II Ml II I II J European Patent Office © Publication number: 0 501 374 B1 Office europeen des brevets^ , © EUROPEAN PATENT SPECIFICATION © Date of publication of patent specification: 06.09.95 © Int. CI.6: C07C 68/08, C07C 69/96 © Application number: 92103058.1 @ Date of filing: 24.02.92 © Process for purifying dimethyl carbonate. © Priority: 26.02.91 JP 53148/91 @ Inventor: Nishihira, Keigo, c/o Ube Chemical Factory @ Date of publication of application: Ube Industries, Ltd., 02.09.92 Bulletin 92/36 1978-10, Oaza Kogushi Ube-shi, © Publication of the grant of the patent: Yamaguchi-ken (JP) 06.09.95 Bulletin 95/36 Inventor: Yoshida, Shinichi, c/o Ube Chemical Factory © Designated Contracting States: Ube Industries, Ltd., DE ES FR GB IT 1978-10, Oaza Kogushi Ube-shi, © References cited: Yamaguchi-ken (JP) EP-A- 0 021 211 Inventor: Tanaka, Shuji, c/o Ube Chemical EP-A- 0 139 442 Factory DE-A- 2 706 684 Ube Industries, Ltd., 1978-10, Oaza Kogushi Beilsteins Handbuch der Organischen Ube-shi, Chemie, 4th Edition (1920), Vol. 2, p. 534 & Yamaguchi-ken (JP) Drude, Zeitschrift fur Physicalische Chemie Ser. A, Vol. 23 (1897), p. 310. © Representative: Hansen, Bernd, Dr. Beilsteins Handbuch der Organischen Dipl.-Chem. et al Chemie, 4th Edition, 4th Supplement (1976), Hoffmann, Eitle & Partner Vol. 2, part 3, p. 1847. Patent- und Rechtsanwalte, 00 Postfach 81 04 20 © Proprietor: UBE INDUSTRIES, LTD. D-81904 Munchen (DE) 12-32, Nishihonmachi 1-chome 00 Ube-shi, Yamaguchi-ken 755 (JP) Note: Within nine months from the publication of the mention of the grant of the European patent, any person may give notice to the European Patent Office of opposition to the European patent granted. Notice of opposition shall be filed in a written reasoned statement. It shall not be deemed to have been filed until the opposition fee has been paid (Art. 99(1) European patent convention). Rank Xerox (UK) Business Services (3. 10/3.09/3.3.3) 1 EP 0 501 374 B1 2 Description is industrially not practical. DE-A-27 06 684 discloses a process for the This invention relates to a process for purifying separation of dimethyl carbonate from its mixtures dimethyl carbonate which is useful as a synthesis with methanol by breakage of the azeotropic mix- starting material for an aromatic polycarbonate and 5 ture by an extraction medium having certain prop- various chemical products and as a solvent. More erties, i.e. (a) inert, aprotic, organic liquid, (b) hav- particularly, it relates to a process for purifying ing a boiling point above 100°C, (c) fully miscible dimethyl carbonate which comprises distilling off with dimethyl carbonate, (d) and having a dielectric and separating methanol from a mixture of constant between 4 and 90, and (e) a dipol mo- dimethyl carbonate and methanol in the presence io ment between 1 .5 and 5 Debye. of dimethyl oxalate. As a process for preparing dimethyl carbonate, SUMMARY OF THE INVENTION there have been practiced, for example, the meth- od of reacting carbon monoxide, methanol and an An object of the present invention is to provide acid by using copper chloride Japanese Patent 75 a process for purifying dimethyl carbonate which Publications No. 11129/1970 and No. 45655/1980), can provide dimethyl carbonate with high quality, the method of interesterifying a cyclic carbonate wherein the azeotropic phenomenon of dimethyl such as ethylene carbonate with methanol in the carbonate and methanol is excluded, and methanol presence of a catalyst (U.S. Patents No. 3,642,858 can be, distilled and separated easily. and No. 3,803,201, and Japanese Patent Publica- 20 The present inventors have run intensive inves- tion No. 27658/1985), and the method of subjecting tigations and have found that dimethyl carbonate carbon monoxide and nitrite to vapor reaction in and methanol do not constitute an azeotropic com- the presence of a catalyst (Japanese Unexamined position in the three-component system of dimethyl Patent Publications No. 274816/1989 and No. oxalate, dimethyl carbonate and methanol and 201146/1990). However, in either of the methods, 25 thereby accomplished the present invention. dimethyl carbonate is obtained as a mixture with That is, the present invention is a process for methanol so that separation from methanol is in- purifying dimethyl carbonate which comprises dis- dispensable for purifying dimethyl carbonate. tilling a mixture of dimethyl carbonate and metha- Dimethyl carbonate and methanol constitute an nol in the presence of dimethyl oxalate to separate azeotropic mixture in a composition ratio of 30 : 70 30 and remove methanol from the mixture, wherein (weight ratio), and thus, it is difficult to separate the dimethyl oxalate is added in an amount of 0.3 or mixture by distillation under normal pressure. more in terms of the mole fraction. Thus, many investigations have been carried out with regard to a method for purifying dimethyl BRIEF DESCRIPTION OF THE DRAWINGS carbonate starting from a mixture of both of the 35 above components, and various proposals have Fig. 1 is a graph showing the measured results been made. For example, there has been proposed of gas-liquid equilibrium of dimethyl carbonate and the method of obtaining a crystalline product en- methanol, and Fig. 2 shows a processing diagram riched in dimethyl carbonate by cooling as dis- of the continuous preparation process. closed in U.S. Patent No. 3,803,201, the method of 40 separating the mixture by distillation and thereby DESCRIPTION OF THE PREFERRED EMBODI- breaking the azeotrope under pressure as dis- MENTS closed in Japanese Patent Publication No. 3463/1984, and the method of separation by dis- In the following, the present invention is de- tillation and thereby adding a hydrocarbon such as 45 scribed in more detail. hexane and heptane as disclosed in Japanese Un- The amount of dimethyl carbonate and metha- examined Patent Publication No. 41820/1979. How- nol is not particularly limited. The amount of ever, these methods cannot satisfy the industrial dimethyl oxalate to be added is 0.3 or more, pref- requirements. The method of applying extraction erably 0.5 or more, in terms of the mole fraction of and distillation with water is not economical since 50 dimethyl oxalate in the three components-systems dimethyl carbonate dissolves well in water and is in order to enhance separation efficiency. With easily saponified so that a high loss is caused. An regard to the separation efficiency, there is no apparatus to be used in the method of distillation upper limit thereof, and a range which can be under pressure is extremely expensive, and oper- industrially practiced, is represented e.g. by 0.8 to ations therewith are difficult. Also the method of 55 0.9 in terms of the mole fraction of dimethyl oxalate adding hydrocarbon includes complicated oper- in the three components-system. ations and is disadvantageous with regard to en- In the three component system of dimethyl ergy. Finally, the method of precipitation by cooling carbonate, dimethyl oxalate and methanol, dimethyl 2 3 EP 0 501 374 B1 4 carbonate and methanol do not show the EXAMPLES azeotropic phenomenon, so that methanol can be separated by distillation under normal pressure. In the following, the process of the present Next, the remaining mixture of dimethyl carbonate invention will be explained specifically by referring and dimethyl oxalate can be separated by normal 5 to Examples, but the present invention is not limit- distillation to give separated dimethyl carbonate. ed by these Examples. The remaining dimethyl oxalate can be used again by circulation. Example 1 An industrial process according to the present invention can be practiced by using a continuous io To the 6th step from the bottom of a 50 steps apparatus as shown in Fig. 2. In Fig. 2, a crude oldershaw having an inner diameter of 32 mm was reaction mixture (1) which is a mixture of dimethyl continuously fed a solution of 70 % by weight of carbonate and methanol is continuously fed to a methanol and 30 % by weight of dimethyl car- first column can (A) and also a solution of dimethyl bonate in an amount of 120 g per hour. At the oxalate is fed therein continuously. The mixture is is same time, to the 6th step from the top thereof refluxed by heating the bottom of the column to dimethyl oxalate dissolved by heating was continu- effect continuous distillation and methanol is taken ously fed in an amount of 950 g per hour. Continu- out from the top of the first column as distilled ous operation was carried out by heating the bot- solution (3). The solution (2) at the bottom of the tom and operating with a reflux ratio of about 5, first column can is a mixture of dimethyl carbonate 20 and when the system has turned to a steady state and dimethyl oxalate and is fed to a second col- (top temperature: 64.7 °C, bottom temperature: umn can (B) and refluxed to effect continuous 151.3 °C), the solution distilled from the top and distillation whereby dimethyl carbonate is taken out the bottom solution were analyzed by gas from the top of the second column as distilled chromatography. As the results, the distilled solu- solution (5.) The solution (4) at the bottom of the 25 tion from the top contained 98.8 % by weight of second tower can is dimethyl oxalate as a distilla- methanol and 1.2 % by weight of dimethyl car- tion residue and is returned to the first column can bonate and the bottom solution contained 0.1 % by (A) for circulated use whereby a continuous opera- weight of methanol, 3.5 % by weight of dimethyl tion can be effected.
Details
-
File Typepdf
-
Upload Time-
-
Content LanguagesEnglish
-
Upload UserAnonymous/Not logged-in
-
File Pages6 Page
-
File Size-