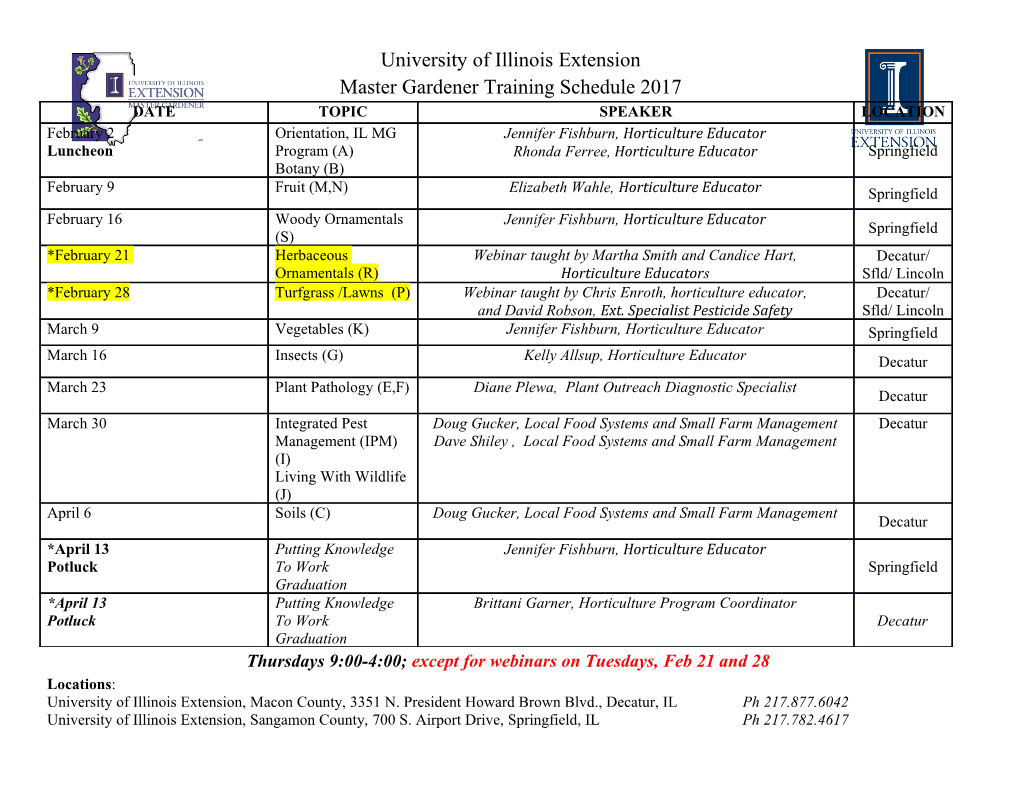
RSC Advances PAPER Calcination-free production of calcium hydroxide at sub-boiling temperatures† Cite this: RSC Adv.,2021,11,1762 Sara Vallejo Castano,˜ ab Erika Callagon La Plante, acd Sho Shimoda,a Bu Wang, e Narayanan Neithalath,f Gaurav Sant*acgh and Laurent Pilon *bc Calcium hydroxide (Ca(OH)2), a commodity chemical, finds use in diverse industries ranging from food, to environmental remediation and construction. However, the current thermal process of Ca(OH)2 production via limestone calcination is energy- and CO2-intensive. Herein, we demonstrate a novel aqueous-phase calcination-free process to precipitate Ca(OH)2 from saturated solutions at sub-boiling temperatures in three steps. First, calcium was extracted from an archetypal alkaline industrial waste, a steel slag, to produce an alkaline leachate. Second, the leachate was concentrated using reverse osmosis (RO) processing. This elevated the Ca-abundance in the leachate to a level approaching Ca(OH)2 saturation at ambient temperature. Thereafter, Ca(OH)2 was precipitated from the concentrated leachate by forcing a temperature excursion in excess of 65 C while exploiting the retrograde solubility of Ca(OH)2. This Received 4th October 2020 nature of temperature swing can be forced using low-grade waste heat (#100 C) as is often available at Accepted 10th December 2020 power generation, and industrial facilities, or using solar thermal heat. Based on a detailed accounting of DOI: 10.1039/d0ra08449b the mass and energy balances, this new process offers at least z65% lower CO2 emissions than rsc.li/rsc-advances incumbent methods of Ca(OH)2, and potentially, cement production. 7,8 Introduction form calcium carbonate (CaCO3). For example, 1 t of Ca(OH)2 can uptake 0.59 t of CO2. Thus, any process that emits less than Calcium hydroxide (Ca(OH)2), also known as portlandite, slaked- 0.59 t of CO2 over the course of Ca(OH)2 production has the or hydrated-lime nds wide use in industries and applications potential to achieve a “carbon-negative” outcome. Carbonation such as: soil stabilization in road and building construction,1,2 reactions can also result in cementation.9,10 This is signicant as 3 11 bleaching in the Kra paper process, and as a occulant in water the ability to utilize Ca(OH)2 as a cementation agent, or indeed 4,5 treatment. According to the U.S. Geological Survey (USGS), as a feedstock (for CaO) could greatly diminish the CO2 emis- “ global lime (Ca(OH)2 and CaO) production was 420 million sions associated with traditional cement ( ordinary portland 6 ” metric tons (t) in 2018. Moreover, Ca(OH)2 is of interest in the cement : OPC) production. Today, however, the production of climate change context because it can uptake/sequester CO2 to Ca(OH)2 features a CO2 footprint similar to OPC production ( 1t of CO2 per t of Ca(OH)2 produced). This is because Ca(OH)2 production, similar to OPC production is based around the age- aLaboratory for the Chemistry of Construction Materials (LC2), Department of Civil old process of limestone calcination (i.e., thermal decomposi- and Environmental Engineering, University of California, Los Angeles, CA 90095, “ ” tion, which results in the desorption of the mineralized CO2 USA. E-mail: [email protected]; Tel: +1 310 206 3084 bound within the limestone and accounts for z65% emissions bDepartment of Mechanical and Aerospace Engineering, University of California, Los associated with the process; the remainder being from the Angeles, CA 90095, USA. E-mail: [email protected]; Tel: +1 310 206 5598 z cInstitute for Carbon Management, University of California, Los Angeles, CA 90095, combustion of fossil fuels to power kiln operations) at 900 C 12,13 USA to produce CaO, the precursor of Ca(OH)2; that is subse- dDepartment of Materials Science and Engineering, University of Texas, Arlington, TX quently granulated and hydrated (i.e., contacted with water) to 76019, USA produce Ca(OH)2. In addition, the process requires quarried eDepartment of Civil and Environmental Engineering, University of Wisconsin, limestone that not only consumes nonrenewable mineral Madison, WI 53706, USA resources, but also disrupts ecosystems, and causes pollution fSchool of Sustainable Engineering and the Built Environment, Arizona State and biodiversity destruction.14,15 University, Tempe, AZ 85287, USA gDepartment of Materials Science and Engineering, University of California, Los Ca-Containing alkaline wastes accrue as a waste-/by-product Angeles, CA 90095, USA of numerous large-scale industries. This includes, for example, hCalifornia Nanosystems Institute, University of California, Los Angeles, CA 90095, slags from iron and steel production, and y ashes from coal USA combustion. These materials are not only produced in large † Electronic supplementary information (ESI) available. See DOI: amounts on an ongoing basis, but there exist tremendous 10.1039/d0ra08449b 1762 | RSC Adv.,2021,11,1762–1772 © 2021 The Author(s). Published by the Royal Society of Chemistry Paper RSC Advances historical reservoirs of these materials in the U.S. and across the Materials and methods world.16–18 For example, even now the U.S. produces greater than 17 million t of slag19,20 and 91 million t of coal combustion Slag leaching residuals. Of the latter, only 58% are benecially utilized.21 And, Slag leachates were prepared by contacting 1, 3, 5, and 10 g of global waste reservoirs host well over a billion tons of slag,16 and a technical basic oxygen furnace (BOF) slag (i.e., a crystalline tens of billions of tons of y ash,22–24 based on broad estimates. slag‡) with 100 mL DI water to achieve solid to liquid mass Underutilized quantities of alkaline wastes, i.e., y ashes and fractions (s/l) of 0.01, 0.03, 0.05, and 0.1, respectively. To slags, are routinely disposed in landlls, which not only implies prepare the slag for leaching, slag nes (<9.5 mm) were dried at a waste disposal cost (“tipping fees”, NB: the average tipping fee 70 C for 24 h, ground for 1 hour in a planetary ball mill (MSK- in the U.S. is on the order of $50 per t),25 but can also result in SFM-1), and manually sieved to retain particles with a size lower environmental damage.26–29 Therefore, with a specic goal of than 106 mm. Batch leaching was conducted in 200 mL plastic enhancing waste utilization, resource recovery and reutiliza- bottles under either unstirred or stirred conditions at room tion, and circular economy, we demonstrate an approach to temperature. Stirring was controlled using a Corning LSE extract Ca-from alkaline industrial wastes,30,31 and produce orbital shaker (6780 NP) at 200 rpm. Solution aliquots of 2 mL Ca(OH)2 via a calcination-free process. While herein we focus on were extracted aer 0, 5, 10, 30, 60, 180, 360 and 720 minutes for alkaline industrial wastes, of course, the broad contours of this analysis of total dissolved calcium, silicon, sodium, aluminum, process are also applicable to alkaline rock species, which and magnesium analysis using a PerkinElmer Avio 200 induc- although harder to solubilize unless externally stimulated,32,33 tively coupled plasma – optical emission spectrometer (ICP- offer the potential to offer a near-limitless source for alkaline OES). Prior to elemental analysis, the samples were ltered element extraction. through 0.2 mm syringe lters and then diluted in 5 vol% HNO3. The ICP-OES was calibrated using standard solutions contain- New concept ing the elements of interest in concentrations of 0, 0.1, 1, 10, 25, 50, and 100 ppm which were prepared using analytical (1000 The conceptual basis of our new process involves the leaching/ ppm) standards purchased from Inorganic Ventures. dissolution of Ca-bearing wastes to mobilize Ca-species in The chemical composition (in mass%) of the simple oxide solution (see process ow diagram, Fig. S1†). This results in an constituents of the slag was measured using X-ray uorescence aqueous Ca-abundance that is typically substantively lower than (XRF). The BOF slag was dominantly composed of CaO (38 À1 the saturation concentration of Ca(OH)2 ( 21.2 mmol L at pH mass%), followed by Fe2O3 (31%), SiO2 (13%), MgO (6%), and ¼ ¼ 30,31,35 12.475 and T 25 C (ref. 34)). Therefore, it is necessary Al2O3 (4%). This information was used to quantify calcium to concentrate the leachate by a factor of 2 or more times nCa;slnðtÞ extraction (XCa) according to: XCa ¼ ; where nCa,sln(t) depending on the initial Ca-content of the leachate. Such n Ca;slag concentration is achieved by reverse osmosis (RO) based ion- are the moles of calcium in the solution at time t, and nCa,slag are separations wherein by means of size and/or charge exclu- the moles of calcium in the solid slag as measured by XRF. The 2+ 2+ À 36 _ 1 sion; divalent cations (e.g.,Ca ,Mg ) can be enriched in the calcium leaching rate nCa (in mmolCa/h ) at time t was dened retentate stream. RO is used to achieve large production rates of ½Caðt; S=LÞ as: n ¼ V ; where V is the solution volume and t saturated solution and to improve the energy efficiency of the Ca t b b concentration process. The retentate is then subjected to is the leaching time. The leaching rate affects the production a temperature swing, e.g., using low-grade waste heat (#100 C) rate (“yield”) of Ca(OH)2, and the efficiency of slag valorization as derived from the ue gas of a power plant or another heavy because, from stoichiometry, one mole of Ca-leached from the industry operation, wherein the retrograde solubility of Ca(OH)2 slag should produce one mole of Ca(OH)2 as per the reaction: 2+ À 4 (ref.
Details
-
File Typepdf
-
Upload Time-
-
Content LanguagesEnglish
-
Upload UserAnonymous/Not logged-in
-
File Pages11 Page
-
File Size-