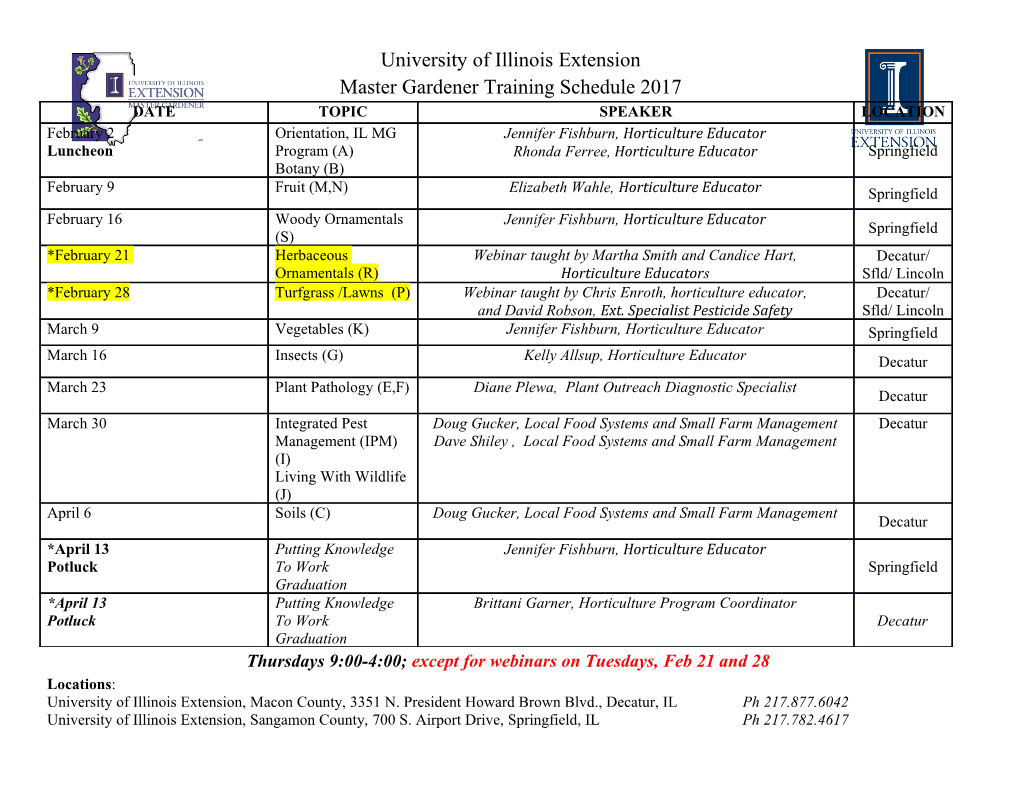
ABSTRACT Title of Document: Airframe Integrity Based on Bayesian Approach Jose Luis Hurtado-Cahuao, PhD, 2006. Directed By: Professor, Mohammad Modarres, Department of Mechanical Engineering. Aircraft aging has become an immense challenge in terms of ensuring the safety of the fleet while controlling life cycle costs. One of the major concerns in aircraft structures is the development of fatigue cracks in the fastener holes. A probabilistic- based method has been proposed to manage this problem. In this research, the Bayes’ theorem is used to assess airframe integrity by updating generic data with airframe inspection data while such data are compiled. This research discusses the methodology developed for assessment of loss of airframe integrity due to fatigue cracking in the fastener holes of an aging platform. The methodology requires a probability density function (pdf) at the end of SAFE life. Subsequently, a crack growth regime begins. As the Bayesian analysis requires information of a prior initial crack size pdf, such a pdf is assumed and verified to be lognormally distributed. The prior distribution of crack size as cracks grow is modeled through a combined Inverse Power Law (IPL) model and lognormal relationships. The first set of inspections is used as the evidence for updating the crack size distribution at the various stages of aircraft life. Moreover, the materials used in the structural part of the aircrafts have variations in their properties due to their calibration errors and machine alignment. A Matlab routine (PCGROW) is developed to calculate the crack distribution growth through three different crack growth models. As the first step, the material properties and the initial crack size are sampled. A standard Monte Carlo simulation is employed for this sampling process. At the corresponding aircraft age, the crack observed during the inspections, is used to update the crack size distribution and proceed in time. After the updating, it is possible to estimate the probability of structural failure as a function of flight hours for a given aircraft in the future. The results show very accurate and useful values related to the reliability and integrity of airframes in aging aircrafts. Inspection data shown in this dissertation are not the actual data from known aircrafts and are only used to demonstrate the methodologies. AIRFRAME INTEGRITY BASED ON BAYESIAN APPROACH By Jose Luis Hurtado Cahuao. Dissertation submitted to the Faculty of the Graduate School of the University of Maryland, College Park, in partial fulfillment of the requirements for the degree of Doctor of Philosophy 2006 Advisory Committee: Professor Mohammed Modarres, Chair/Advisor Dr. Paul Hoffman Professor Emeritus Marvin Roush Professor Ali Mosleh Professor Bilal Ayyub Professor Sreeramamurthy Ankem © Copyright by Jose Luis Hurtado Cahuao 2006 DEDICATION This thesis is dedicated to my kids, Loredana and Robin whose support has proved invaluable to my research. ii ACKNOWLEDGEMENTS There are many people to thank for their support and encouragement, without whom this thesis would not have been possible. Firstly my advisor, Dr. Mohamed Modarres for discussions and guidance, and to give me the opportunity to work with him, whose enthusiasm for continue improving are probably the most valuable lessons I have learned from this PhD, and his continual support and encouragement have kept me going over the last three or so years. I would like to thank Dr. Paul Hoffman for providing technical guidance, resources and funding for my research assistantship throughout this PhD. I would also like to thank Dr. Marvin Roush for introducing me to reliability engineering and supporting during my studies. I would like to thank the many friends and colleagues who have helped in one way or another, especially Francisco Joglar for his understanding friendship, his contributions to the ideas developed herein, and her unstinting support. Reza Azarkhail, Genebelin Valbuena and Mohammad Pour-Gol-Mohamad for their technical assistance throughout the course of this thesis Finally my family, who have been great over the years and never raised an eyebrow when I claimed my thesis would be finished in the “next month” for nearly a year. iii TABLE OF CONTENTS LIST OF TABLES v LIST OF FIGURES vii LIST OF SUBSCRIPTS xi Chapter 1 Introduction 1 1.1 Historical background 2 1.2 Technical Background 3 1.2.1 Stresses 3 1.2.2 Crack Size 4 1.2.3 Tensile Strength 4 1.2.4 Fatigue 5 1.2.5 Fatigue in the Aerospace Industry 5 1.2.5.1 Safe-Life method 8 1.2.5.2 Fail-Safe method 8 1.2.5.3 Damage-Tolerance Method 9 1.3 Objectives 11 1.4 Motivation 11 1.5 Contributions 13 1.6 Application 13 1.6.1 Aircraft 13 1.6.2 Analysis Location 14 1.6.3 Materials 15 1.6.4 Models 15 1.6.5 Structure 16 Chapter 2 Technical Description of Fatigue Crack Growth / Material Properties 19 2.1 Fatigue Crack Growth Phenomenon 19 2.2 Linear Elastic Fracture Mechanics 24 2.2.1 Stress Intensity Factor 25 2.2.2 Crack tip Plastic Zone Size 28 2.2.3 Fracture Toughness 30 2.3 Sigmoidal Shape da/dN Curve 33 2.4 Effect of Stress Ratio Stress on fatigue Crack Growth 36 2.5 Effects of complex time history loads on fatigue crack growth 37 2.6 Material Properties 40 ii 2.6.1 Mechanical Properties 40 2.6.2 Elastic modulus (E) 42 2.6.3 Yield strength (Sy) 42 2.6.4 Ultimate strength (Sult) 44 Chapter 3 Data Collection 47 3.1 Load Spectrum - Background 47 3.2 Calculation of Spectrum Load 49 3.2.1 Fatigue Life Expended Index (FLE) 54 3.3 Initial Crack Size Distribution 55 3.3.1 Equivalent Initial Flaw Size 56 3.3.2 Time-To-Crack Initiation 56 3.4 Crack Observation (Evidence) 59 Chapter 4 An Integrated Approach for Assessing the Crack Growth Under Variable Amplitude Loading 63 4.1 Crack Growth Assessment 63 4.1.1 Global Approach 64 4.1.2 Cycle-by-Cycle Approach 65 4.2 Non-interaction models 67 4.2.1 Walker Model 67 4.2.2 Forman Model 70 4.3 Interaction model: Closure Model 73 4.4 Failure Criteria 78 4.5 Crack Growth Estimation and Uncertainty Propagation 79 4.6 Model Verification 81 Chapter 5 Probabilistic Parameter Estimation of the Models. 88 5.1 Lognormal Distribution as a Representation of Crack Size Distribution. 90 5.2 Inverse Power Law Relationship (IPL) as a Representation of Life (life expended) and Crack Size. 93 5.3 IPL –Lognormal Relationship. 94 5.4 Parameter Estimation Using MLE 97 5.5 Estimation of the Prior Distribution of Crack Size as Crack Grows for Bayesian Parameter Estimation 99 5.6 Markov Chain Monte Carlo (MCMC) 102 iii 5.6.1 Monte Carlo integration 102 5.6.2 Metropolis-Hasting and Gibbs Sampling 103 5.6.2.1 Burn-in period 106 5.7 Genetic Algorithm (GA) 107 Chapter 6 Bayesian Updating Process of the Crack Size Distribution 117 6.1 Bayesian Updating of Crack Size Distribution 118 6.2 Posterior pdf for FLE = 100% 125 6.2.1 Posterior Initial Crack Size pdf for FLE = 100% 128 6.2.2 Posterior Model Parameters 133 6.2.3 Posterior Initial Crack Size pdf for FLE = 100% - MCMC 138 6.3 Forecasting Probability of Failure for a Specific FLEj% 140 6.4 Decision Making Methodology 141 Chapter 7 Analysis of the results 146 7.1 Monte Carlo Simulation 146 7.2 Crack Growth Model Comparisons 147 7.3 Selection of Lognormal Distribution 148 7.4 Parameter Estimation 149 7.5 Bayesian Analysis 150 7.6 Decision Making 155 Chapter 8 Conclusions & Recommendations 165 Appendix A PCGROW code for crack growth –closure model example calculation. 169 Appendix B WinBUGS code for parameter estimation example calculation. 176 References 178 iv LIST OF TABLES Table 1.1 Parameters of crack growth models. 16 Table 2.1 Typical cases of fatigue problems. 20 Table 2.2 Characteristics of the three regimes of fatigue crack growth [2]. 35 Table 2.3 Properties for the aluminum 7075-T651. 45 Table 3.1 Flight and stresses description. 52 Table 3.2 Spectrum summary for the 25 aircrafts. 53 Table 3.3 Observed number of various crack sizes for the 25 aircrafts. 62 Table 4.1 Walker parameters. 70 Table 4.2 Forman Parameters. 73 Table 4.3 Crack growth lookup table for 7076-T6 [75]. 77 Table 4.4 Materials properties for the 7057-T6. 78 Table 4.5 Beta values. 83 Table 5.1 Goodness of fit results. 92 Table 5.2 IPL-Lognormal mean parameters at the FLE showed – Based on Walker crack growth model. 99 Table 5.3. IPL-Lognormal mean parameters at the FLE showed – Based on Forman crack growth model. 100 Table 5.4 IPL-Lognormal mean parameters at the FLE showed – Based on Closure crack growth model. 101 Table 5.5 IPL-Lognormal mean parameters values using three estimation methodologies. 115 Table 6.1 Updated Lognormal Parameters for the Three Crack Growth models – Conjugate. 122 Table 6.2 Lognormal distribution parameters at FLEj% for each aircraft – MCMC. 124 Table 6.3 Model parameters updating. 138 Table 7.1 Differences between Conjugate and MCMC approach. 153 Table 7.2 Initial crack size Conjugate and MCMC at 100% FLE. 154 Table 7.3 Prediction results FH= 1000 – crack size XS. 156 v Table 7.4 Prediction results FH= 1000 – crack size S. 157 Table 7.5 Prediction results FH= 1000 – crack size L. 158 Table 7.6 Prediction results FH= 1000 – crack size XL. 159 Table 7.7 Aircrafts to maintenance. 163 Table 7.8 Aircrafts to maintenance after the box plot analysis.
Details
-
File Typepdf
-
Upload Time-
-
Content LanguagesEnglish
-
Upload UserAnonymous/Not logged-in
-
File Pages206 Page
-
File Size-