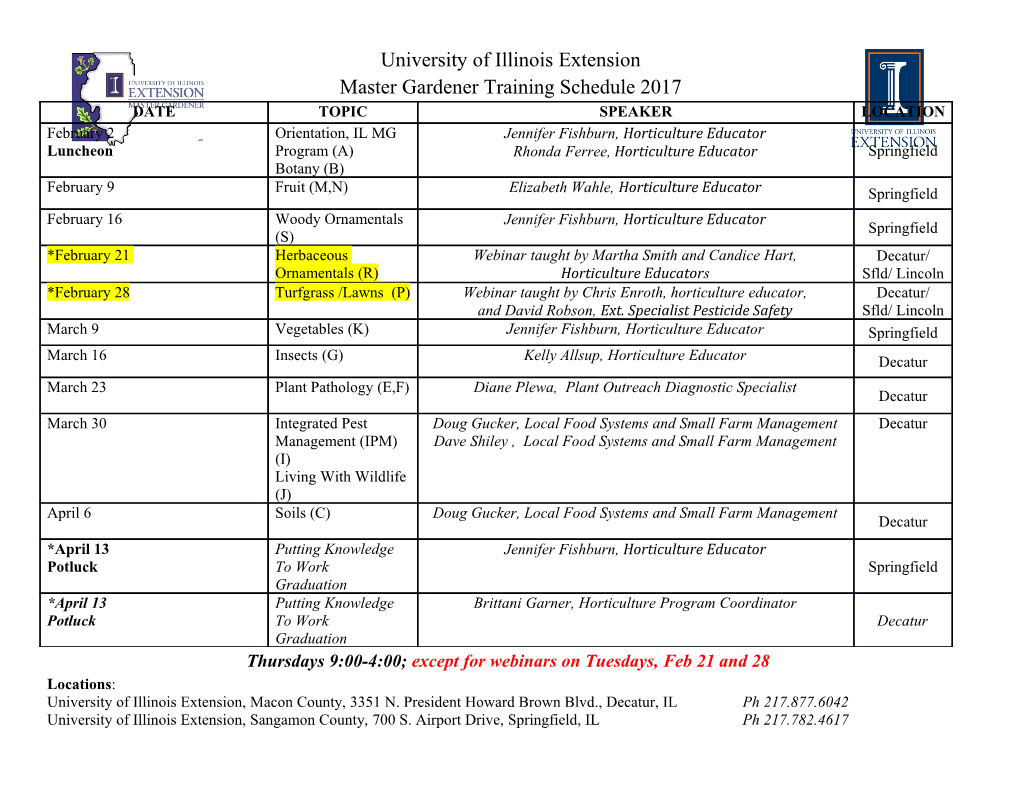
International Journal of Engineering Research and Technology. ISSN 0974-3154, Volume 12, Number 6 (2019), pp. 802-808 © International Research Publication House. http://www.irphouse.com The Evaluation of the Threshold Stress Intensity Factor and the Fatigue Limit of Surface-Cracked Specimen Considering the Surface Condition Ki-Woo Nam1, Won-Gu Lee2 and Seok-Hwan Ahn3,* 1,2 Department of Materials Science and Engineering, Pukyong National University, Busan 48513, Republic of Korea. 3 Department of Aero Mechanical Engineering, Jungwon University, Chungbuk 28024, Republic of Korea. Abstract cracks[1]. It was reported that the non-propagation of surface cracks is related to the constant threshold stress intensity In this study, the threshold stress intensity factor and fatigue factor for surface crack lengths larger than 0.5 mm [2]. For limit of surface-cracking materials were evaluated according cracks smaller than 0.5 mm, it was not the threshold stress to the variation of stress ratio and aspect ratio with reference intensity factor but rather the stress identical to the fatigue to the fatigue limit of a gentle-grind specimen, severe-grind limit that was the limit condition for very small defect specimen, and shot-peened severe-grind specimen. Surface propagation. For microcrack problems, the assumption of a cracks in the gentle-grind, severe-grind, and shot-peened small nonlinear domain does not hold. Haddad [3] introduced severe-grind specimens could be used to evaluate the a valid formula for the dependency of the threshold stress threshold stress intensity factor and fatigue limit according to intensity factor on the crack length by adding the microcrack the stress ratio and aspect ratio using the equivalent crack length to the crack length. Moreover, Tange et al. [4] provided length. As the surface crack length increased, the fatigue limit a more convenient formula for evaluating the threshold stress decreased rapidly at a small stress ratio and large aspect ratio. intensity factor by removing the microcrack length from the However, the depth of the surface cracks decreased rapidly at Haddad formula, and they conducted research on minimizing a small stress ratio and aspect ratio. As the surface crack the damage to shot-peened welds caused by surface cracks length increased, the threshold stress intensity factor rapidly using this formula and the Newman–Raju formula [5, 6-9]. increased at a small stress ratio and large aspect ratio. Moreover, Ando et al. [10] presented a formula for evaluating However, the surface crack depth rapidly increased at a small the threshold stress intensity factor considering the size of the stress ratio and aspect ratio. The reduction ratio of the fatigue plastic zone, so that the fatigue limits and threshold stress limit at the surface crack length of the same stress ratio was intensity factors of all surface-cracking materials could be larger than 0.4 at an aspect ratio 0.1. However, the surface evaluated. crack depth was larger than 0.1 at an aspect ratio of 0.4. For a surface crack length of the same stress ratio, the rate of In this study, the threshold stress intensity factors and fatigue increase in the threshold stress intensity factor was smaller limits of surface-cracking materials were evaluated according than 1.0 at an aspect ratio of 0.4; however, the surface crack to the stress ratio and surface crack aspect ratio with reference depth was larger than 1.0 at an aspect ratio of 0.4. This is to the fatigue limits of the gentle-grind specimen, severe-grind because when the aspect ratio became large, cracks specimen, and shot-peened severe-grind specimen [11], propagated in the depth direction rather than the surface considering the machining process. direction and at the same time when became similar to the surface crack length. Keywords: threshold stress intensity factor, fatigue limit, 2. FRACTURE MECHANICS OF A SEMIELLIPTICAL stress ratio, aspect ratio, surface crack length, surface crack SURFACE CRACK IN A FINITE PLATE depth The fatigue limit and threshold stress intensity factor of a semielliptical surface crack in a finite plate can be evaluated as follows. 1. INTRODUCTION When a through-wall crack with a crack length of 2푐 in an Most of the experiments to determine the fatigue crack growth infinite plate is subjected to the bending stress of 휎퐵, 퐾 can rate and the threshold stress intensity factor were performed be calculated using Equation (1). for large cracks and large through-wall cracks. As can be seen from actual fatigue failures, however, a failure occurs from 퐾 = 휎퐵√휋푐 (1) very small cracks and is initiated by their growth. The Meanwhile, the semielliptical surface crack 퐾 in a finite importance of small cracks was recognized from scientific and plate can be evaluated using the Newman–Raju formula [5]. practical perspectives, and it was found that small cracks do As shown in Fig. 1, when a semielliptical surface crack with a not follow the crack growth laws obtained from large surface crack length of 2푐 and a surface crack depth of 푎 in * Corresponding author 802 International Journal of Engineering Research and Technology. ISSN 0974-3154, Volume 12, Number 6 (2019), pp. 802-808 © International Research Publication House. http://www.irphouse.com a finite plate is subjected to the uniform bending stress of 휎퐵, When a through-wall crack with a crack length of 2푐 exists 퐾 can be obtained using Equation (2) [10]. in an infinite plate, however, the threshold stress intensity factor can be evaluated using Equation (7). 푅 푅 ∆퐾푡ℎ(푐) = ∆휎휔푐 √휋푐 (7) 푅 In this case, ∆퐾푡ℎ(푙) according to the stress ratio (R) is obtained using the ASME standard formula in Equation (8). 푅 표 ∆퐾푡ℎ(푙) = ∆퐾푡ℎ(푙)√(1 − 푅) (8) The threshold stress intensity factor of a semielliptical surface crack can be obtained by substituting Equation (4) into Equation (7). When Equation (7) is applied to a semielliptical crack, it is the maximum value of 퐾 that determines ∆퐾푡ℎ. As 퐾 becomes largest when 훽 is largest in Equation (2), the maximum value of 훽 is substituted into Equation (5). Fig. 1. Schematic illustration of a finite plate containing a semi-circular crack 3. EVALUATION METHOD AND SPECIMENS 푎 푎 푐 푎 푎 푐 퐻( , , , ∅)퐹( , , , ∅) The production process is known to have significant effects on 퐾 = 푡 푐 푏 푡 푐 푏 휎 √휋푎 = 훽휎 √휋푎 (2) 푎 퐵 퐵 the fatigue characteristics of parts. Such effects are √푄( ) 푐 detrimental or beneficial, as shown in Table 1. where, 퐹 and 푄 are geometrical correction functions, 퐻 is Table 1. Factors affecting the fatigue characteristics of parts the correction function for the bending stress, 푡 is the thickness of the finite plate, 푏 is the half of the width of the Detrimental Beneficial finite plate, and ∅ is the angle of the tip of the semielliptical Hardening Carburizing surface crack. 훽 is the geometrical correction factor that integrated the geometrical correction functions. When the Grinding Honing length of a through-wall crack in an infinite plate that Machining Polishing represents the same 퐾 under the same stress is assumed to be Plating Burnishing the equivalent crack length 푐푒, Equations (1) and (2) become Equation (3). Welding Rolling EDM and ECM Shot peening 퐾 = 휎퐵√휋푐푒 = 훽휎퐵√휋푎 (3) Summarizing Equation (3), the relationship between 푐푒 and 푎 can be expressed as shown in Equation (4). From a detrimental aspect, grinding, machining, and welding may cause metal fatigue cracks on the tensile surface. Curing, √푐푒 = 훽√푎 (4) plating, and electrical discharge machining may a leave hard, 푅 brittle surface. Electrochemical machining may damage or Therefore, the dependency of ∆퐾푡ℎ for the semielliptical weaken surface grain boundaries. From a beneficial aspect, all surface crack in a finite plate on the crack length can be the listed processes induce compressive residual stress, evaluated using Equation (5) derived by replacing 푐 of thereby improving the fatigue life. Shot peening is most Equation (1) with 푐푒 of Equation (4). commonly used, because it provides the maximum 2 −1 compressive residual stress to various materials and parts. ∆퐾푅 푅 푅 푎 −1 휋 푡ℎ(푙) ∆퐾푡ℎ = 2훽∆휎휔√ 푐표푠 { 2 ( 푅 ) + 1} (5) 휋 8훽 푎 ∆휎휔 Fig. 2 shows the S–N curves for various types of processing. The reference curve is for the case of the gentle-grind where 훽 is the function of ∅. The evaluation value of 퐾 specimen, which showed a fatigue limit of 414 MPa. The varies depending on the angle of the crack tip that evaluates severe-grind specimen showed a faster cutting speed and a 푅 푅 퐾. 휎휔 is the fatigue limit of the plate, and ∆퐾푡ℎ(푙) is the larger cut. In this case, large surface tensile residual stress that threshold stress intensity factor when a very long through-wall lowers fatigue strength occurs because of fatigue. As the crack 2푐0 exists in an infinite plate. The fatigue limit of a figure shows, the fatigue limit of the severe-grind specimen 푅 surface-cracking material (휎휔푐) can be obtained using was 338 MPa, which was approximately 18% lower than that Equation (6), which was derived by substituting Equation (4) of the gentle-grind specimen. The final curve represents the on the equivalent crack length into Equation (5) [10]. fatigue limit of the shot-peened severe-grind specimen. The 2 figure shows that this specimen exhibited a fatigue limit of 푅 ∆퐾푅 휋∆휎휔푐 휋 푡ℎ(푙) 614 MPa, which was approximately 48% higher than that of 푐푒 {푠푒푐 ( 푅 ) − 1} = ( 푅 ) (6) 2∆휎휔 8 ∆휎휔 the gentle-grind specimen. This increase in the fatigue limit occurred because the tensile residual stress caused by severe 803 International Journal of Engineering Research and Technology.
Details
-
File Typepdf
-
Upload Time-
-
Content LanguagesEnglish
-
Upload UserAnonymous/Not logged-in
-
File Pages7 Page
-
File Size-