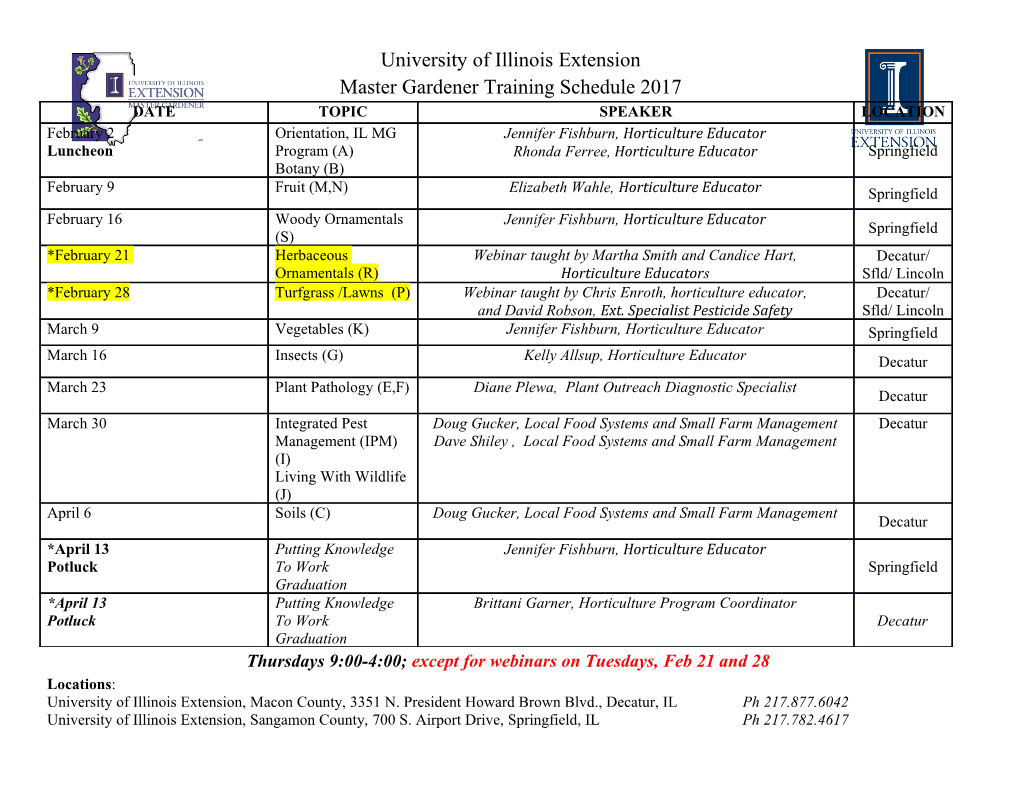
2020 AFS Proceedings of the 124th Metalcasting Congress Paper 2020-029 (12 pages) Prediction of Entrained Oxide Inclusions and Oxide Induced Defects During Directional Flow in Aluminum Casting Colin D. Ridgeway The Ohio State University, Columbus, Ohio Keith Ripplinger Honda Engineering North America, Anna, Ohio Duane Detwiler Honda R&D Americas, Raymond, Ohio Alan. A. Luo The Ohio State University, Columbus, Ohio Copyright 2020 American Foundry Society little as 5 seconds at 1292F (700C) the aluminum oxide, 6 ABSTRACT or Al2O3, layer can be as thick as 24nm. The newly formed oxide film often becomes entrained into the melt It is well known that the entrainment of double oxide during ladle transfer, adding charge material, or during bifilms formed during flow and solidification has the pouring process. Alternatively, in alloys that contain detrimental effects on the mechanical properties of cast greater than 2% Mg, MgO oxides films can form on the aluminum products. Degassing, filtration and metal flow surface and are equally stable.5 Once entrained, the oxides design are generally employed to reduce the presence of are extremely difficult to remove, as the they are entrained defects, yet, oxide bifilms are still present in a thermodynamically stable and completely insoluble majority of castings and their locations are often unknown within the melt.4 Fluxing or degassing can be used to often leading to severe quality issues. In this work, a new remove a majority of the oxides that form on the surface, model, termed Oxide Entrainment Number (OEN), is however, during pouring, fresh oxides will reform on the proposed to predict the location and severity of bifilms surface of the melt pool as it is exposed to the and oxide induced defects in final cast structures. The atmosphere. These new oxides, often called ‘young model is developed by examining bifilms formation oxides,’ are then entrained as the molten material fills the events and tracks newly formed bifilms via free surface mold, making entrained oxide inclusions an unavoidable tracking. Simple geometry patterns promoting directional defect in aluminum castings.8 flow were designed to compare the defect location and severity in optimal vs sub-optimal flow conditions. The OXIDE FILM FORMATION & ENTRAINMENT proposed OEN model has been coupled with ProCAST As previously mentioned, molten aluminum will form a (defined as Software 1 from this point on in this paper) thermodynamically stable oxide film instantaneously and experimentally validated with aluminum A356 when it is exposed to an atmosphere. This oxide layer casting. does not harm the melt, and actually protects molten aluminum below the oxide film. However, when the Keywords: oxide inclusion, bifilm entrainment, aluminum surface of the melt is disturbed, the oxide film will fold casting, modeling, defect prediction over itself and the solid film will be entrained below the surface. This mechanism and other common entrained defects are described in Figure 1. The structure of the INTRODUCTION entrained inclusions consists of two solid layers of film separated by a void of air or gas trapped between them. Entrained oxide inclusions are some of the most common Due to the inability of the solids to re-bond, the inner and most detrimental defects that reside in castings with surfaces of the bifilms remain permanently unbonded and numerous studies citing a severe reduction in the tensile the void between them is permanently entrained.9 This strength, fatigue strength and ductility.1-5 The prevalence structure is most notably seen in Figure 1B & 1C. of oxide inclusions or bifilms in cast structures can be Conversely the outer portion of the bifilm is wetted and attributed to two factors: the rapid formation of oxides, acts as a substrate for nucleation and solidification. and the stability of the oxides within the melt. Whenever the melt is exposed to a gaseous environment such as air, The oxide entrainment mechanisms are simple in nature the molten aluminum will instantaneously react with the but are difficult to avoid. One of the most common ways air and form an oxide layer.6,7 Thiele has shown that in as for oxide films to become entrained below the surface is Page 1 of 12 2020 AFS Proceedings of the 124th Metalcasting Congress Paper 2020-029 (12 pages) during movement or ladle transfer of the molten material. to pouring and are no longer present in the final casting. As the molten material is transferred for pouring, the Removal of old oxides is often done by drossing the surface is perturbed, and small waves form as seen in surface prior pouring, pouring through a filter, and using Figure 1A. As the waves crash back into the surface, the fluxing agents. If old oxides do enter the cast structure, it surface film folds over itself and the double sided film is often difficult to detect them non-destructively. structure of the bifilm is created while the momentum of Extremely large oxides will occasionally appear on x-ray the wave pulls the bifilm beneath the surface, effectively or micro computed tomography (micro-CT), however, entraining the structure. Bifilms can also be entrained by online inclusion detection techniques such as LiMCA are the addition of charge material to the melt. As additional rarely used in mass production of aluminum castings.10,11 material is added, the solid charge material will break the Thus, old oxides are often only identified after a surface oxide film and drag the film below the surface. component has failure and the fracture surface presents During this process the solid film from the surface will the entrained oxide. tend to wrap itself around the charge material and fold into a network like structure, increasing the surface area Young oxides are much more prevalent in final cast of the defect. structures and are much more difficult to detect. The current maximum resolution for micro-CT is ~400 nm The last major mechanism in which oxides are entrained making it nearly impossible to locate all entrained young occurs during the pouring stage when the molten metal oxides. Furthermore, the same issue as with old oxides enters the mold. As the molten metal exits the crucible the occurs, micro-CT cannot be used for online oxide previously non-oxidized material below the surface is detection in mass production and oxides are often only exposed to the environment. The newly exposed material detected in a destructive manner. forms fresh young oxides which are then entrained due to turbulent flow as the molten material folds over itself Both young and old oxides also have large affinity to inside the mold. Campbell has shown that turbulent flow induce other forms of defects including gas porosity and occurs in aluminum alloys when the gate velocity exceeds shrinkage porosity. Campbell argues that the pressure 0.5m/s highlighting the need for proper molding design.9 required for gas pores to form either homogeneously or heterogeneously is so great that the practicality of such nucleation rarely occurs.4,5 Instead the non-wetted inner of the bifilm offers a perfect initiation site for the excess gas to reside with limited formation energy. Excess gas is able to permeate the solid and inflate or unfurl the bifilm as shown in Figure 1 (Area C). If sufficient gas is within the melt, the bifilm can be completely unfurled into a spherical morphology and give the appearance of a gaseous pore, though the surface area of the pore will be entirely oxidized. Similarly shrinkage porosity requires a critical drop in the metallostatic feeding pressure, and the easiest initiation site for shrinkage is in the presence of a bifilm. As the melt solidifies the dendrites will begin to pull away from one another. Thus the presence of the crack-like structure of the bifilm offers a site for shrinkage initiation and bifilm is pulled apart and creates an irregular shaped void. If this process were to occur without the presence of a bifilm, there would be a significant requirement of formation energy as the solid would need to physically pull apart the solidifying Figure 1: Various oxide entrainment mechanisms where black lines indicate oxidized surfaces (A) Wave structure. entrainment (B) A folded over bifilm (C) Gas precipitation within the bifilm structure. (D) An internal In the case that excess gas within the melt or casting is pore with an oxidized surface and (E) A bubble trail. able to heterogeneously nucleate near the mold wall, it is still likely that this pore will contain some level of oxygen OXIDE DETECTION AND PREVENTION inside. The oxygen trapped in the pore with will then Entrained oxide inclusions are often characterized by their instantaneously oxidize the surface area of the pore as size and are termed either Young or Old Oxides. Old described by Thiele and shown in Figure 1 (Area D). oxides range from 1-5mm in thickness and form when the After oxidation, the gas pore will then float towards the molten surface is exposed to elevated temperatures for an top of the melt or casting due to its low density and in its extended period of time. Young oxides range from 10 - wake leave a bubble train as shown in Figure 1E. The 500nm and form during the pouring process.5 In general, bubble trail left behind will also be made up of small old oxides can be completely removed from the melt prior defects with included surface areas. Page 2 of 12 2020 AFS Proceedings of the 124th Metalcasting Congress Paper 2020-029 (12 pages) into the fluid and are tracked through solidification. The The culmination of the entrained oxides as well as each of created particles range from 25-31μm which is more these oxide induced defects can then lead to a greater realistic, though it will not capture or accurately depict all volume of the defects within the casting.
Details
-
File Typepdf
-
Upload Time-
-
Content LanguagesEnglish
-
Upload UserAnonymous/Not logged-in
-
File Pages12 Page
-
File Size-