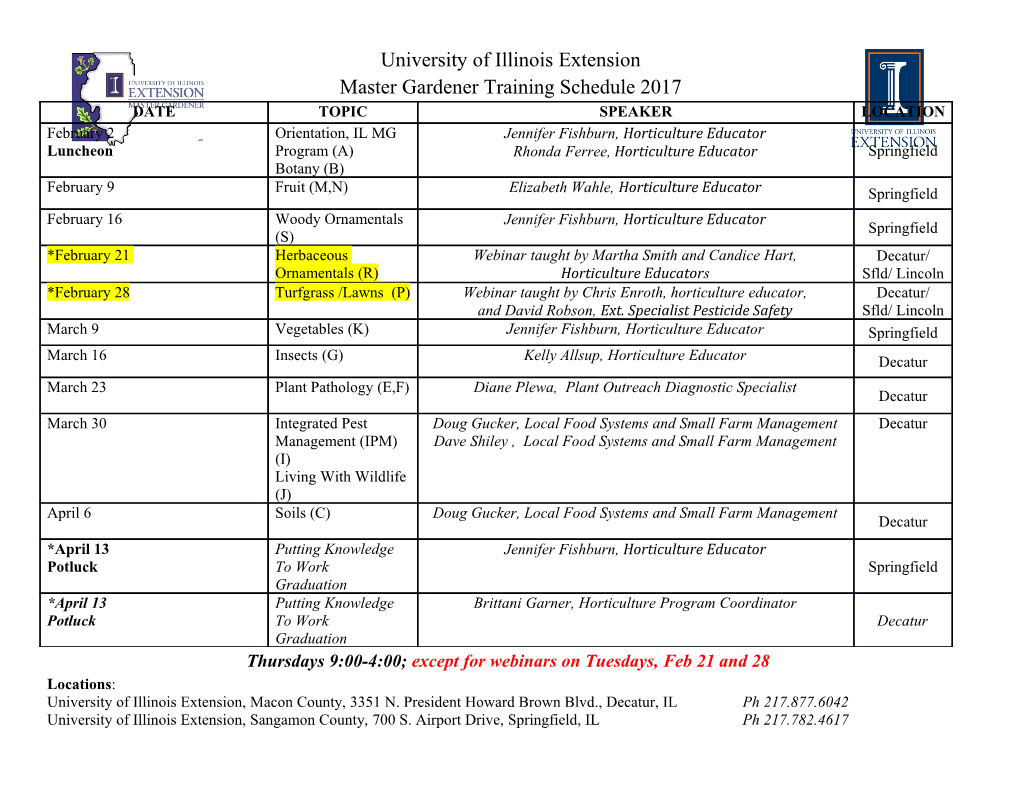
in that year, where he was engaged in the research and development he joined the Department of Electrical and Electronic Engineering, Oita of communication network architectures and communication switch- University, and is currently an Associate Professor of the same Univer- ing software. He joined the Division of Medical Informatics, Shi- sity. His research interests have been on electromagnetic direct/inverse mane University Hospital, in 2004. He moved to the Department of scattering and FDTD analysis of the electromagnetic environment. Dr. Medical Informatics, Shimane University School of Medicine, in Kudou is a member of the IEICE of Japan, the IEE of Japan and the 2005. His research interests include information processing systems Japanese Society of Medical and Biomedical Engineering. in hospitals as well as computational learning theory and its appli- cation. He is a member of the Institute of Electronics, Information Takashi Kano was born in Tokyo, Japan, in and Communication Engineers of Japan, the Japanese Society for 1949. He received his B.Eng. degrees from Artificial Intelligence, the Japan Society for Health Care Manage- Sophia University, Tokyo, Japan, in 1973. He ment, and the Japanese Society for Clinical Pathway. received his Ph.D. degree from Toa University, Yamaguchi, Japan, in 2004. Since 1973, he Takato Kudou was born in Oita, Japan, in has worked at the Department of Medical Engi- 1963. He received his B.Eng., M.Eng. and D. neering Service in Mitsui Memorial Hospital for Eng. degrees in communication engineering, all 32 years. Since 2006, he has been working at from Kyushu University, Fukuoka, Japan, in the Department of Biomedical Engineering, Faculty of Health and 1985, 1987 and 1990, respectively. From 1990 Medical Care, Saitama Medical University. Prof. Kano is a member to 1994, he was a Research Associate of the of the Japanese Society of Medical and Biomedical Engineering, the Department of Computer Science and Communica- Healthcare Engineering Association of Japan and the Japanese Society tion Engineering, Kyushu University. In 1994, of Medical Instrumentation. EMC EMI in Modern AC Motor Drive Systems Firuz Zare, Queensland University of Technology Brisbane, QLD, Australia Email: [email protected] Abstract—In this paper, several aspects of high frequency related analysis but the conditions are completely different at high issues of modern AC motor drive systems, such as common mode frequencies. voltage, shaft voltage and resultant bearing current and leakage Electromagnetic Interference (EMI) is a major problem in currents, have been discussed. Conducted emission is a major prob- recent motor drives that produces undesirable effects on elec- lem in modern motor drives that produce undesirable effects on tronic devices. In modern power electronic systems, increasing electronic devices. In modern power electronic systems, increasing power density and decreasing cost and size of a system are mar- power density and decreasing cost and size of system are market ket requirements. Switching losses, harmonics and EMI are the requirements. Switching losses, harmonics and EMI are the key key factors which should be considered at the beginning stage factors which should be considered at the beginning stage of a of a design to optimise a drive system. design to optimise a drive system. Common mode voltage creates shaft voltage through electro- static couplings between a rotor and stator windings and the ro- tor and a frame which can cause bearing currents when the shaft Introduction voltage exceeds a breakdown voltage level of the bearing grease. Nowadays, more than 60 percent of the world’s energy is used An increase in the carrier frequency of voltage-source Pulse to drive electric motors. Due to growing requirements of speed Width Modulated (PWM) inverters based on high-speed control, pulse width modulated inverters are used in adjustable switching devices has improved operating characteristics of the speed drives. Rapid developments in semiconductor technolo- inverters. High speed switching can generate the following se- gy have increased the switching speed and frequency of power rious problems due to high dv/dt: switches dramatically. In a motor drive system, a voltage source • Ground current escaping to earth through stray capacitors converter with hard switches generates high dv/dt, which inside a motor causes leakage currents due to stray capacitances in an electric • Conducted and radiated noises motor. As shown in Fig.1, a modern power electronic drive • Shaft voltage and bearing current consists of a filter, a rectifier, a DC link capacitor, an inverter Models of parasitic couplings and high frequency com- and an AC motor. Many small capacitive couplings exist in the ponents for an inverter fed induction motor drive system motor drive systems which may be neglected at low frequency are investigated to determine suitable models to predict ©2009 IEEE 53 Fig.2 shows the capacitive cou- Diode dc-Link plings of an induction motor and a Voltage Filter Rectifier Capacitor Inverter Cables Motor view of stator slot, where: Supply Cwr is the capacitive coupling be- tween the stator winding and rotor Cws is the capacitive coupling be- Filter tween the stator winding and stator frame Crs is the capacitive coupling be- tween the rotor and stator frame Cww is the capacitive coupling between turns of stator winding C is the capacitive coupling of PE ball ball bearing Fig.3 shows a general structure of Fig. 1. A power electronic motor drive system with capacitive couplings. a ball bearing and shaft in an AC ma- chine. As shown in this figure there are some balls between outer and in- ner races with lubricated grease be- Stator (s) tween the balls and the races. There Stator End Motor are capacitive couplings between the Winding Frame outer and inner races. During opera- Cww Crs Cwr tion, the distances between the balls Winding (w) and races may be changed and will Shaft C ball Ballbearing vary the capacitance values and resul- tant electric field between the races and balls. Due to this fact, this capac- Ballbearing Cball itance has a nonlinear value. Lubricat- Rotor ed grease in the ball bearing cannot Cwr withstand a high voltage and a short Cww End circuit through the lubricated grease Stator Cws Winding Rotor (r) may happen, thus this phenomenon can be modelled as a switch. Fig. 2. A view of stator slot and capacitive coupling in an induction motor. PWM inverters have been found to be a major cause of motor bearing failures in inverter motor drive sys- tems. All inverters generate common Outer Race Inner Race mode voltages relative to the ground, Ball which make bearing current through Outer Race motor parasitic capacitances. dBO CBO According to Fig.4.a, phase volt- ages and a common mode voltage (Vn) Shaft Ball can be derived based on the power C S converter voltages (Va, Vb,Vc). Each d BI CBI leg voltage of a three phase inverter Inner Race is given by: V 5 V 1 V (a) (b) (c) a an n Vb 5 Vbn 1 Vn (1) Vc 5 Vcn 1 Vn Fig. 3. (a) general structure of a ball bearing (b) a view of ball, outer and inner races and capacitive couplings (c) simple model of a ball bearing. And then: bearing currents and shaft voltage over a wide frequency Va 1 Vb 1 Vc 5 Van 1 Vbn 1 Vcn 1 3Vn (2) range. A high frequency model of an electric motor is an important issue for power electronic engineers, which helps It is clear that in a three-phase1 system: 2 them to analyse leakage and bearing currents and to design EMI filters. At low frequency, an equivalent circuit of an Van 1 Vbn 1 Vcn 5 0 (3) electric motor consists of inductances and resistances with- out considering stray capacitances and skin effect. These So, the common mode voltage can be calculated as: issues become more important at high speed switching ap- plications due to high dv/dt. Vn 5 Va 1 Vb 1 Vc /3 (4) 54 ©2009 IEEE 1 2 In a three phase power inverter, a DC voltage is converted to three phase voltages with 120° phase shift. Fig.4.b shows three phase leg voltages of an inverter with common mode voltage. V V V The trend in increasing switch- a b c ing frequency improves the quality of current waveforms in motor drive systems but due to short switching time, a high dv/dt is produced across the motor terminal. The leakage current is created by a high voltage Van Vbn Vcn stress during switching time and ca- pacitive coupling in an AC motor. Vn Fig.5 shows a simple equiva- (a) lent model of an induction motor which contains main capacitances 60 between the windings, rotor and the stator frame. 40 20 Analysis of an Electric Motor at High Frequency 0 The stray capacitance between the windings and the stator frame is the –20 most significant parasitic compo- –40 nent compared to the other stray capacitances which generate signifi- –60 cant conducted emission noise. At high frequency, an electric motor can be modeled as distributed capac- (b) itors, inductors and resistors as shown in Fig.6 and the maximum Fig. 4. (a) three phase voltage source inverter (b) PWM voltage. frequency can be determined using the standing wave’s equation. We consider one v section to model the motor at high frequency as shown in Fig.6.b and Winding Rotor only the stray capacitance between the windings and the stator has been considered. Each motor has different high frequency parameters due to its structure, size and materials. Cwr Cws Crs Cball Calculation of Cws The first step is to measure the magnitude and the phase values of the impedance in terms of frequency based on two different Stator Frame connections of the windings.
Details
-
File Typepdf
-
Upload Time-
-
Content LanguagesEnglish
-
Upload UserAnonymous/Not logged-in
-
File Pages6 Page
-
File Size-