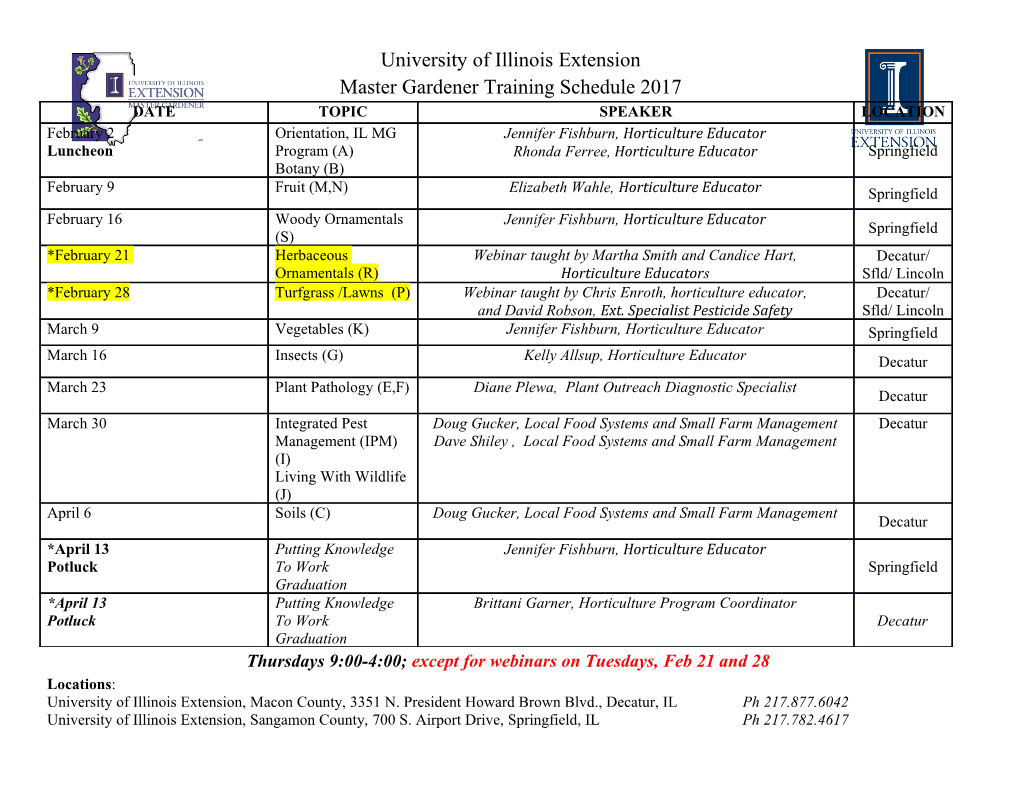
PROCESSING AND MICROSTRUCTURE EFFECTS ON THE STRENGTH AND THE LOCALIZED CORROSION RESISTANCE OF ULTRA-FINE GRAINED Al-Mg-Si ALLOYS A Dissertation by RAMATOU LY Submitted to the Office of Graduate and Professional Studies of Texas A&M University in partial fulfillment of the requirements for the degree of DOCTOR OF PHILOSOPHY Chair of Committee, Homero Castaneda-Lopez Co-Chair of Committee, Karl. T. Hartwig Committee Members, Ankit Srivastava Hong Liang Head of Department, Ibrahim Karaman December 2019 Major Subject: Materials Science and Engineering Copyright 2019 Ramatou Ly ABSTRACT Improving the strength, and the corrosion resistance of aluminum alloys simultaneously through aging treatment, and grain refinement is a challenge as these two properties are mutually exclusive. In this work, we investigated the effects of shear banding, dynamic recrystallization, and precipitation on the corrosion susceptibility, and the strength of an ultra-fine grained (UFG) AA6061 aluminum alloy. For that, we extruded the material by equal channel angular pressing (ECAP) up to seven passes following route Bc combined with a post-aging treatment at 100 ⸰C. We first characterized the microstructure after processing in depth before investigating corrosion susceptibility by accelerated immersion tests, and electrochemical testing. We found that after 3 ECAP passes, the AlFeSi intermetallic compounds are fragmented and closely spaced along the shear direction and within the shear planes of the material making this direction and plane highly susceptible to pitting. Besides, the shear bands are preferred regions for precipitation after post- aging treatment. Therefore the corrosion susceptibility of UFG AA6061 alloys is tailored by the shear bands network of the material, and the precipitation within the bands.The immersion and electrochemical tests reveal that filiform corrosion, and intergranular corrosion (IGC) are severe when the material is partially recrystallized and peak aged. Also, the bulk potentiodynamic response is significantly affected by the bulk composition, and the precipitation within the shear bands. In addition, passivation is easier after ECAP regardless of the post-aging treatment. However the passive film is less stable. We also found that dynamic recrystallization decreases the susceptibility to IGC even at peak aging by reducing the volume fraction and the length of the shear bands. Thus in UFG AA6061 aluminum alloys, the energy stored in the grains seems to influence the susceptibility to IGC more than grain boundary precipitation. ii DEDICATION To my parents, my family, and all my friends from Cote d'Ivoire, France, Senegal, Mali, and the United States who have always motivated me, encouraged me, and extended all the help and the support I needed to succeed in this journey. iii ACKNOWLEDGEMENTS I would like to thank my advisor Dr. Homero Castaneda, and my co-advisor Dr. Karl Hartwig for their guidance, and support throughout my Ph.D. My thanks also go to my committee members, Dr. Ankit Srivastava, Dr. Bruce Tai, and Dr. Hong Liang for their interests in my research. Thank you to Dr. Xinghang Zhang for advising me before moving to Purdue University. I am grateful to all the professors and staffs who helped me in my research, and my studies. Thank you to Robert Barber, and Michael Elverud for their technical assistance in performing the ECAP. Thank you to Murat Kaynak, and Dharmesh Patel for their help, time and sympathy. Thanks also go to Dr. Stanislav Verkhoturov for assisting me with the SIMS, Dr. Chun Hsin Kuo for helping me with the SEM, and Dr. Wilson Serem for his guidance with the AFM. I am thankful to Dr. Ahmad Ivan Karayan for his advice, and contributions to the work presented. Many thanks to Yenny Cubides for helping me with the drawings, Wahaz Nasim for his assistance during the EBSD analysis, and Abhinav Srivastava for guiding me during the mechanical testing. Thank you to Dr. Indranhil Roy, and Dr. Agathe Robisson, for their dedication, and unconditional support when I started my Ph.D. journey at Texas A&M. Thanks also go to my friends Shuang Quin, Parvin Karimi, Lin Chen, Yash Parikh, Hanna Hlushko, Chin-Hua Cheng, Taymaz Jozaghi and the whole corrosion group for making my time at Texas A&M University a great, and unforgettable experience. iv CONTRIBUTORS AND FUNDING SOURCES This work was initially supported by SCHLUMBERGER. The ECAP processing and the mechanical testing were supervised by Dr. Karl T. Hartwig, co-advisor - emeritus professor in the Department of Materials Science & Engineering of Texas A&M. The corrosion testing were supervised by Dr. Homero Castaneda, advisor-Assistant professor in the Department of Materials Science & Engineering of Texas A&M - Director of the national corrosion & materials reliability lab. Sections 3, 4, and 5 were supervised by Dr. Karl T. Hartwig, Dr. Homero Castaneda, Dr. Ankit Srivastava, Dr. Hong Liang and Dr. Ivan Ahmad Karayan, post-doc fellow in the Department of Materials Science & Engineering of Texas A&M. These sections were published in 2018 and 2019 in three articles listed in the biographical sketch. v NOMENCLATURE SPD Severe Plastic Deformation ARB Accumulating Roll Bonding HPT High Pressure Torsion ECAP Equal Channel Angular Processing UFG Ultra-Fine Grained GB Grain Boundary IGC Intergranular Corrosion IMC Intermetallic Compounds HAGBs High Angle Boundaries LAGBs Low Angle Boundaries SCE Saturated Calomel Electrodes EBSD Electron Backscatter Diffraction SEM Scanning Electron Microscope TEM Transmission Electron Microscope HRTEM High Resolution Transmission Electron Microscope OM Optical Microscope VPD Volta Potential Difference TOF-SIMS Time of Flight Secondary Ions Mass Spectrometry AFM Atomic Force Microscopy SKPFM Scanning Kelvin Probe Force Microscopy DRX Dynamic Recrystallization vi PFZ Precipitation Free Zone Ecorr Corrosion potential Epit Pitting potential Erep Repassivation potential OCP Open Circuit Potential CPP Cyclic Potentiodynamic Polarization Rp Polarization Resistance XRD X-Ray diffraction 3D-APT 3D Atom Probe Tomography CSL Coincidence Site Lattice vii TABLE OF CONTENTS Page ABSTRACT .............................................................................................................................. ii DEDICATION .......................................................................................................................... iii ACKNOWLEDGEMENTS ...................................................................................................... iv CONTRIBUTORS AND FUNDING SOURCES .................................................................... v NOMENCLATURE ................................................................................................................. vi TABLE OF CONTENTS .......................................................................................................... viii LIST OF FIGURES .................................................................................................................. xi LIST OF TABLES .................................................................................................................... xvi 1. INTRODUCTION .............................................................................................................. 1 1.1 Background ......................................................................................................... 1 1.2 Technical Approach ............................................................................................ 2 1.3 Dissertation Outline ............................................................................................. 3 2. LITTERATURE REVIEW ................................................................................................ 4 2.1 Aluminum and Aluminum Alloys ........................................................................... 4 2.1.1 Al-Mg-Si Alloys - The 6xxx Aluminum Series ............................... 5 2.1.2 Aluminum Alloys............................................................................. 6 2.2 Accumulative Roll Bonding ................................................................................ 7 2.3 High Pressure Torsion.......................................................................................... 8 2.4 Equal Channel Angular Pressing ......................................................................... 9 2.4.1 Dynamic Recrystallization and Shear Banding .............................. 10 2.4.2 Dislocation Density, Grain Size, Grain Boundary Characteristics .. 11 2.4.3 Influence of Hydrostatic Pressure .................................................... 13 2.5 Ultra-Fine Grained Aluminum Alloys 6xxx ........................................................ 14 2.5.1 Dynamic Precipitation .................................................................... 14 2.5.2 Influence of Aging Treatment .......................................................... 15 2.5.3 Fragmentation of Precipitates and Particles ..................................... 16 2.6 Corrosion Mechanisms in Aluminum Alloys ...................................................... 17 2.6.1 Passivation ....................................................................................... 17 viii Page 2.6.2 Pitting and Passivation Breakdown ................................................. 17 2.6.3 Influence of Alloying Elements ....................................................... 19 2.6.4 Intergranular Corrosion ...................................................................
Details
-
File Typepdf
-
Upload Time-
-
Content LanguagesEnglish
-
Upload UserAnonymous/Not logged-in
-
File Pages121 Page
-
File Size-