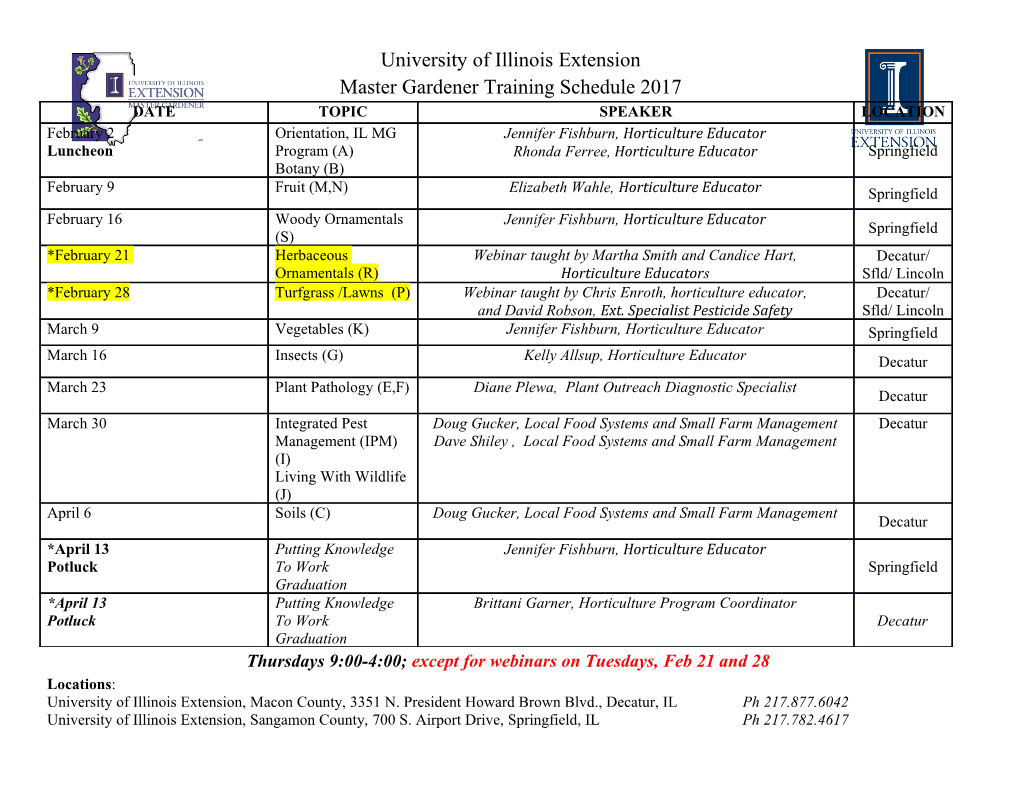
C Svngs SEIKO INSTRUMENTS SINGAPORE PTE LTD From wages to non-wage related cost cutting measures, we have done the best we can to prevent retrenchments. Mr Ho Wai Heng, Deputy Managing Director most The Metal Industries Workers’ Union (MIWU) has a good relationship for years with watchmaker Seiko Instruments Singapore Pte Ltd. pro-business When the downturn struck all of a sudden at the tailend of last year, economy MIWU was able to offer solutions to keep them going in the hope of an upturn soon. The Labour Movement understands that “I was among the pioneer batch of Singaporeans that helped set up operations here in 1973. About 40 per cent of the staff here are like companies must stay afloat for workers we kept me, and we have worked for decades together. In this crisis, our precision engineering sector has been hard hit but lucky for us, we could talk openly to keep their jobs. The Government’s company in about it to MIWU and find solutions. By October 2008, demand for Seiko Instruments’ movement which Jobs Credit scheme has provided a big we manufacture dropped and our production quantities dipped by 30 per the black cent. We took some pro-active steps to prepare for worsening times. The boost to keep workers employed. NTUC most difficult decision was to cut the Annual Wage Supplement (AWS) and performance bonus because this affects workers directly. After negotiations, and our affiliated unions have also been AWS was untouched, but we cut bonus by 50 per cent. We explained to MIWU and our workers that this was critical to ensure that the company working with companies to minimise entered 2009 in the black. Failure to do this could mean that the survival of the company would be at risk and many would have lost their jobs. job losses. These measures include NON-WAGE RELATED COST CUTTING MEASURES sending workers for training under We also came up with a list of non-wage related cost-cutting measures. We decreased staff on our production lines and did away with overtime. The Skills Programme for Upgrading and company also scaled down on investments for non-critical items, postponed the overhaul of the plant and upgrading of wastewater treatment facilities. Resilience (SPUR), implementing shorter We also cut down on business-related travel to headquarters in Japan and Mr Ho Wai Heng, instead, opted for teleconferencing. We sold two of four company vehicles work weeks and introducing temporary Deputy Managing Director and scaled down or postponed company functions. Staff too chipped in with energy-saving initiatives. We cut benefits such layoffs. Without these measures, as mobile phone allowances and reduced flexi-benefits by 40 per cent for a year. But we retained our Wellness programme because we want to keep our retrenchment and unemployment figures workers healthy, especially in bad times. Despite everything, we had to lay off 26 non-traditional source (NTS) would have been much higher. contract workers who have always been a buffer workforce for us. The plant has had 15 years of non-stop production and this year will be the first time that we face such a crisis. At Seiko Instruments, core staff went for training for a Certificate in Integrated Knowledge of Jigs and Fixtures Design, a 57-hour course for 20 employees to enhance their knowledge in the specialised skill. From wages to other non-wage related cost cutting meaures, we have done the best we can to prevent retrenchment.” 62 63 C Svngs MURATA ELECTRONICS SINGAPORE (PTE) LTD “In the electronics sector, we are quite used to seasonal first company fluctuations of about 20 per cent to 30 per cent in production orders. But in this downturn, our sales dipped sharply and we are operating at 15 per cent of normal capacity, a level never before seen since we began operations in to go on spur Singapore 36 years ago. As makers of capacitors, electronic components of consumer products like cars and mobile phones, we have never seen such bad times. We tried our best to retain staff. We saved as many as 300 jobs in Singapore by taking a few counter- measures. One of these was to send our core staff for training under SPUR. We worked with UWEEI and e2i (Employment and Employability Institute) to make sure we gave this core group the right training to re-position the company in this competitive industry. We opted to send a first batch of about 50 core staff for the National ITE Certificate (NITEC) courses in Mechatronics in December. A second batch has also gone for training. Now, we are all eagerly awaiting the return of our SPUR trainees. They will definitely be able to help this company move faster and better in this industry. FLEXI-WORK ARRANGEMENTS Another counter-measure we put in place was to implement shorter work weeks. We used to run the plant every day in a month. We now run for just 20 days and work eight-hour shifts instead of 12-hour shifts. This affects the pay packet of employees and I personally explained the situation to them. Mr Masatoshi Koike, They know why this was necessary in this crisis as it saves jobs. Senior Managing Director management also took a pay cut recently to demonstrate that everyone in this company shares the pain equally. We also cancelled the Annual Dinner and Dance to cut down expenses.” When orders were down last year, UWEEI very quickly held talks with Murata and it became the first company to go on SPUR to save jobs. There were about 300 redundant jobs in the company at that time. Mr Cyrille Tan, General Secretary, UWEEI Job Saving arrangements such Number of Workers Retrenched in as shorter work Unionised Sectors on Weekly Basis Measures weeks, temporary 1,000 are Working layoffs, redeployment as well as managing 900 To help businesses wage costs through save jobs and the flexible wage 800 retain workers, the system. From Government has January to March 700 introduced several 2009, a total of 68 initiatives such as 600 unionised companies the Jobs Credit and 23,914 workers 500 scheme and the had gone through Skills Programme shorter work weeks 400 for Upgrading and or temporary layoffs. Resilience (SPUR). Through all 300 When orders were down in the global electronics market, the Number of workers NTUC and our these efforts, we affiliated unions 200 United Workers of Electronic and Electrical Industries (UWEEI) have been able to also worked with avoid run-away 100 worked with companies in the sector to minimise job losses. employers to retrenchments in the implement cost- One such company is Murata Electronics Singapore (Pte) Ltd unionised sector. 0 cutting measures at Retrenchments in which became the first company to send core staff for training the company level. Week 1 Week 2 Week 3 /4 Week 1 Week 2 Week 3 Week 4 Week 1 Week 2 Week 3 Week 4 unionised companies These measures under the Skills Programme for Upgrading and Resilience peaked around Lunar include implementing January 2009 February 2009 March 2009 New Year but have flexible work (SPUR) last December. since slowed down. 64 65 Cp!"#i$ “The first thing our company did in the last quarter of 2008 ready now for when we realised that business was down was to re-affirm that we will TESA TAPE ASIA PACIFIC PTE LTD not retrench. We knew that the strategies we put in place as long- term players in this market will see us through this rough patch. One bigger orders of the first things we did was to purchase a new rewinding machine for our non-adhesive tape business. Our products are known for quality, but we wanted to move up several notches on this front for the future. The rewinding machine would cut wastage by 30 per cent. When we were running the old machine, we suffered a level of wastage that was not acceptable. Almost one in two spools of tape that we produced could not meet our quality standards and we had to discard it. With this machine, we would get almost perfect spools of non-adhesive tape and the downtime gives our staff time to train and get used to the machine as well. We are now waiting for big Mr Daniel Ng, orders for this business. Production Director We also made use of the downtime to overhaul our other older machines. In the last 10 years, we have been running three shifts round the clock with not much time for major overhauls. We also decided that there was no better time than now to run in-house courses to When we were running raise quality awareness among workers and refresh their knowledge the old machine, we on safety measures. My management and I worked closely with our suffered a level of union, Chemical Industries’ Employees Union (CIEU), to come up with suitable courses. Our market in Europe has new and more stringent wastage that was not requirements for eco-friendly products. We need to meet those new acceptable. Almost one standards and raise quality awareness. In Singapore, we are the only in two spools of tape plant that manufactures PVC adhesive tapes that can meet the REACH that we produced could requirement for earth-friendly products for the European markets.” not meet our quality A MATURE WORKFORCE NURTURED standards and we had Many of the staff at Tesa Tape are in their 40s and have been with the company from the start. In this downturn, the company managed to discard it. With this excess manpower by running training programmes.
Details
-
File Typepdf
-
Upload Time-
-
Content LanguagesEnglish
-
Upload UserAnonymous/Not logged-in
-
File Pages58 Page
-
File Size-