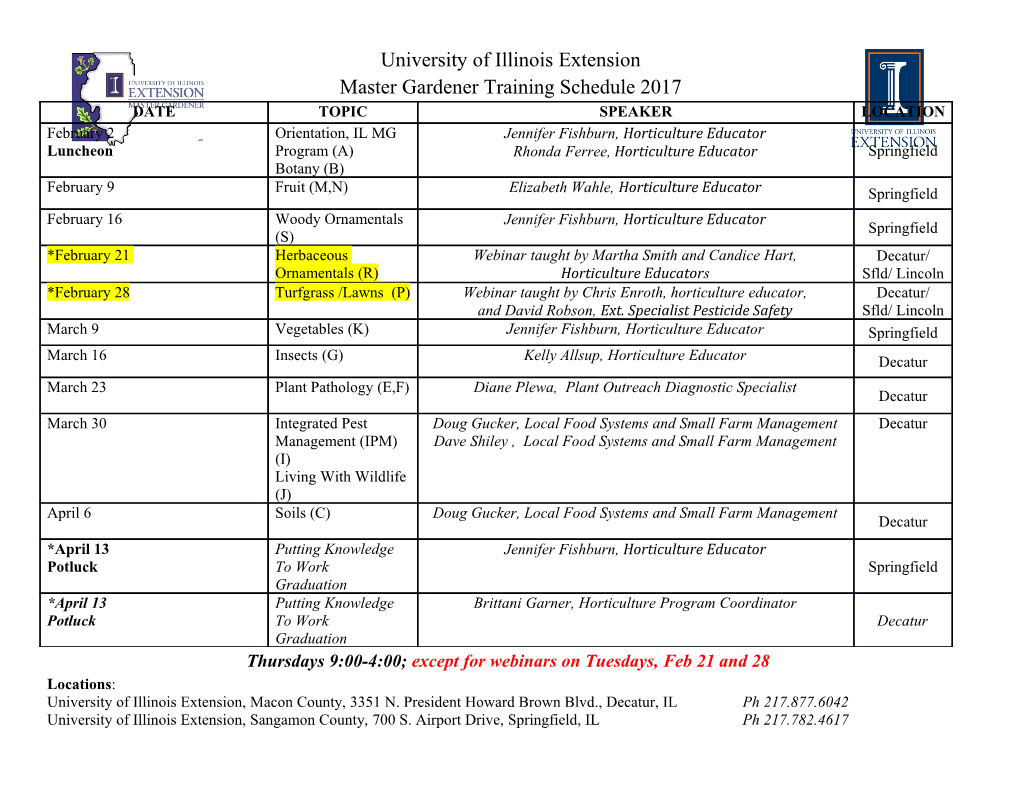
Ding et al. Chin. J. Mech. Eng. (2019) 32:20 https://doi.org/10.1186/s10033-019-0331-0 Chinese Journal of Mechanical Engineering ORIGINAL ARTICLE Open Access Hierarchical Optimization of Landing Performance for Lander with Adaptive Landing Gear Zongmao Ding1,2* , Hongyu Wu1,3, Chunjie Wang1,4 and Jianzhong Ding1 Abstract A parameterized dynamics analysis model of legged lander with adaptive landing gear was established. Based on the analysis model, the landing performances under various landing conditions were analyzed by the optimized Latin hypercube experimental design method. In order to improve the landing performances, a hierarchical optimization method was proposed considering the uncertainty of landing conditions. The optimization problem was divided into a higher level (hereafter the “leader”) and several lower levels (hereafter the “follower”). The followers took condition‑ ing factors as design variables to fnd out the worst landing conditions, while the leader took bufer parameters as design variables to better the landing performance under worst conditions. First of all, sensitivity analysis of landing conditioning factors was carried out according to the results of experimental design. After the sensitive factors were screened out, the response surface models were established to refect the complicated relationships between sensi‑ tive conditioning factors, bufer parameters and landing performance indexes. Finally, the response surface model was used for hierarchical optimization iteration to improve the computational efciency. After selecting the optimum bufer parameters from the solution set, the dynamic model with the optimum parameters was simulated again under the same landing conditions as the simulation before. After optimization, nozzle performance against damage is improved by 5.24%, the acceleration overload is reduced by 5.74%, and the primary strut improves its performance by 21.10%. Keywords: Landing gear, Soft landing, Sensitivity analysis, Response surfaces, Hierarchical optimization 1 Introduction of interesting regions will be more complex and harsh, Legged lander has been used for deep space exploration and landing in multiple regions to accomplish diferent because of its high landing stability and terrain adapt- detection missions may be needed. So it is required that ability [1]. In order to isolate vibration and reduce load the lander has better terrain adaptability and its landing during soft landing, the legged lander generally uses the gears are reusable. plastic material such as honeycomb as the main absorber Considering those requirements, Adaptive landing to design the landing gear. However, the performances of gear was proposed as a possible solution. Refs. [3–5] these landing gears are unable to be adjusted during soft introduced hydraulic system, intelligent materials and landing. In order to cope with complex landing terrain, pyrotechnics devices into the design of landing gear to larger design margin should be reserved, resulting in the realize adaptive control. Among them, magnetorheo- heavier soft landing system [2]. With the continuous pro- logical damper (MR damper) is widely studied because gress of deep space exploration, the terrain environment of its cheerful prospect. In Refs. [2, 6–9], the single MR damper was designed and analyzed in detail, and the equivalent mathematical model of its characteristics was *Correspondence: [email protected] obtained. Refs. [10–13], which proposed a variety of con- 1 School of Mechanical Engineering and Automation, Beijing University of Aeronautics and Astronautics, Beijing 100083, China trol strategies for the lander with adaptive landing gears, Full list of author information is available at the end of the article proved the efectiveness of adaptive gears in enhancing © The Author(s) 2019. This article is distributed under the terms of the Creative Commons Attribution 4.0 International License (http://creat iveco mmons .org/licen ses/by/4.0/), which permits unrestricted use, distribution, and reproduction in any medium, provided you give appropriate credit to the original author(s) and the source, provide a link to the Creative Commons license, and indicate if changes were made. Ding et al. Chin. J. Mech. Eng. (2019) 32:20 Page 2 of 12 soft landing performances. Previous studies mostly dis- Landing gear cussed the implementation of adaptive lander, and few Load concerned the soft landing performance optimization Primary strut Main for the adaptive lander. But performance optimization Body is of great importance for the weight reduction of lander Secondary strut and it benefts the improvement of terrain adaptability. Existing researches about landers optimization mostly Nozzel Footpad focus on conventional passive control lander [14–16]. Furthermore, the worst condition uncertainty caused by Figure 2 Main structures of the lander the change of design variables was ignored in the exist- ing researches. And the selection or optimization of the parameters was just based on the typical condition, honeycomb core as bufer component. Te relationship which leads to the instability of soft landing safety. of secondary strut between the cushioning force fa and Aiming at the uncertainty of the worst condition, a hier- the bufering stroke da is shown in Figure 3, while the archical optimization method was proposed to update the characteristic of primary strut will be discussed later. worst condition dynamically during the progress optimiz- Take Refs. [17, 18] as reference, the structure param- ing the adaptive bufer parameters. First, a dynamic analy- eters of the lander at touchdown is selected (Table 1). sis model of adaptive lander was established, and its soft Te dynamic analysis model of soft landing was estab- landing performance was analyzed and evaluated. Ten lished by ADAMS, and gravity environment was set in the response surface was adopted to participate the itera- the moon. Te lander footpad numbering and the coor- tive computation of hierarchical optimization. Te lander dinates defnition is shown in Figure 4, where Os-XsYsZs with the optimized adaptive bufer was simulated. Te is global coordinate system, Oc-XcYcZc is centroid con- results show that the optimization efectively improves trol coordinate system, αe is the equivalent slope of land- the soft landing performance, which verifes the feasibility ing surface, the speed along Xs is vertical velocity vx and of the hierarchical optimization method. the speed along Xs is horizontal velocity vz. Te rotation angles from O -X Y Z to O -X Y Z in order of Z-X-Y are 2 Dynamic Model of the Lander s s s s c c c c defned as: φ (rotation about the X ), θ (rotation about the 2.1 Confguration and Coordinate System Defnition s Y ) and ψ (rotation about Z ). Te contact force between of Lander s s footpad and landing surface was simulated by nonlinear Figure 1 shows the overall confguration of the lander spring damping model and Coulomb friction model [15]. studied in this paper, which consists of a main body and four symmetrically distributed landing gears (Figure 2). Te main body is a mounting platform for various 2.2 Adaptive Bufer and Its Control Strategy detecting instruments and control subsystem. All of the Unlike the conventional landing gears, such as honey- landing gears, with the same confguration and size, are comb core and air bag, bufer characteristics of adaptive composed of one primary strut, two secondary struts bufer are able to be controlled by adopting some struc- and one footpad. Te connection between struts is tures or intelligent material. So the adaptability of lander realized through a universal joint, so as between struts equipped with this kind of bufer can be improved. Even and main body, while the footpad is connected with the if the adaptive control system fails, the adaptive landing primary strut by the ball joint. Te primary struts are gear will degenerate to the conventional passive landing adaptive bufers, and the secondary ones use aluminum gear but not palsy, which ensures the safety and reliability of the landing system [11]. Considering the maturity of techniques, MR damper was chosen as carrier for adaptive control strategy. Te main components of adaptive bufer are spring and MR damper, in which the spring provides restoring force, and MR damper provides damping force. Te structure of adaptive bufer is shown in Figure 5. Te magnetic feld strength of the coil is changed by controlling the energiz- ing voltage, so as to dynamically adjust the damping coef- fcient of MR damper. Figure 1 Confguration of the lander According to the existing research results, the MR damper produces a large damping force at a relatively Ding et al. Chin. J. Mech. Eng. (2019) 32:20 Page 3 of 12 20 will afect the stable operation of the instruments on 15 board and is undesired. To preserve the transportability 10 of the strategy, the conventional linear damping force model is adopted. Te damping force of MR damper / kN 5 a f is controlled to keep a linear relation with the bufer 0 velocity by adjusting the applied current. Te equiva- -5 lent force of adaptive bufer can be simplifed as shown -10 -0.16 -0.080 0.08 0.16 0.24 in Eq. (1) [21–23]: da / m f =−cs˙ + ks, Figure 3 Force–stroke relationship of secondary strut (1) where f is the equivalent force, c is the equivalent damp- ing coefcient, k is the equivalent stifness coefcient and s is the cushioning stroke of the bufer. Table 1 Parameters of the lander at touchdown To ensure the controlling fexibility and promptness, Parameter Value a jump control strategy based on the minimum energy Mass of load (kg) 1650 principle was adopted to realize the adaptive adjust- Mass of landing gear (kg) 15 ment of the damping coefcient [13]. Considering the Height of mass center (mm) 2500 symmetry of the land model, the damping coefcient Radius of footpad’s lower surface (mm) 100 control function is shown as Eq. (2): − + Distance between two adjacent footpads (mm) 4000 cmax cmin ˙ ˙ cmax cmin ci = sgn −θ + ψ si + , 2 2 (2) where ci is the equivalent damping coefcient of damper 1 i, and cmin, cmax are the lower and upper limit to be XC 2 controlled.
Details
-
File Typepdf
-
Upload Time-
-
Content LanguagesEnglish
-
Upload UserAnonymous/Not logged-in
-
File Pages12 Page
-
File Size-