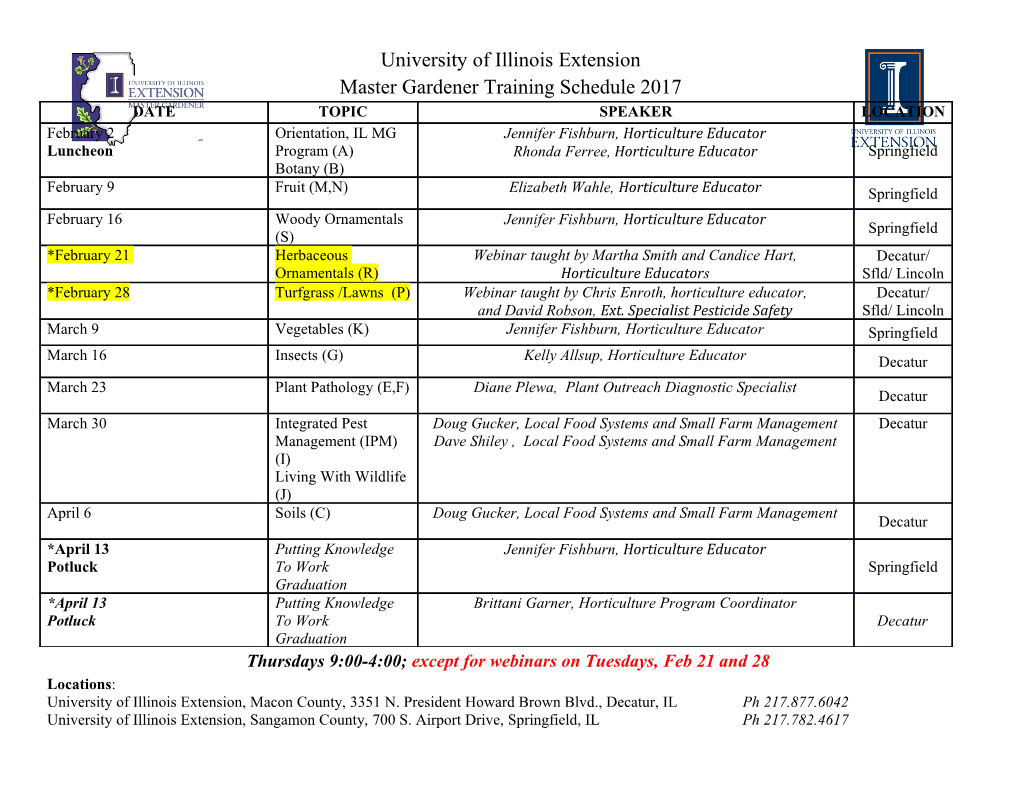
Cryogenics 41 &2001) 513±520 www.elsevier.com/locate/cryogenics Thermodynamic analysis of GM-type pulse tube coolers q Y.L. Ju *,1 Cryogenic Laboratory, Chinese Academy of Sciences, P.O. Box 2711, Beijing 100080, People's Republic of China Received 29 January 2001; accepted 28 June 2001 Abstract The thermodynamic loss of rotary valve and the coecient of performance &COP) of GM-type pulse tube coolers &PTCs) are discussed and explained by using the ®rst and second laws of thermodynamics in this paper. The COP of GM-type PTC, based on two types of pressure pro®les, the sinusoidal wave inside the pulse tube and the step wave at the compressor side, has been derived and compared with that of Stirling-type PTC. Result shows that additional compressor work is needed due to the irreversible entropy productions in the rotary valve thereby decreasing the COP of GM-type PTC. The eect of double-inlet mode on the COP of PTC has distinct improvement at lower temperature region &larger TH=TL). It is also shown that the COP of GM-type PTC is independent of the shape of the pressure pro®les in the ideal case of no ¯ow resistance in the regenerator. Ó 2001 Elsevier Science Ltd. All rights reserved. Keywords: Pulse tube cooler; GM-type; Thermodynamic analysis 1. Introduction achieved [13]. All these machines use a compressor and a valve system to produce pressure oscillation in the In general pulse tube cooler &PTC) requires a phase cooler system. They are called GM-type PTCs. shifter system, located at the hot end of the pulse tube, A GM-type PTC, shown in Fig. 1, only diers from to achieve an optimum phase angle h between the gas the Stirling-type at the compressor side of the cooler. ¯ow rate and the pressure oscillation inside the pulse Instead of a piston compressor the GM-type uses a ro- tube to increase the cooler performance. The so-called tary valve or several electromagnetic valves to generate ori®ce [1] and double-inlet [2] modes are two of the most the pressure oscillations in the cooler. In the ideal case well-known con®gurations. Other innovations are multi- the compressor is isothermal and reversible. The com- bypass [3], two-piston [4], four-valve [5], inertance tube pressor heat is removed in the aftercooler. The rotary [6], active-buer [7], inter-phasing [8], and double-ori®ce valve connects the PTC system alternatively to a con- [9]. stant high pressure pH and a low pressure pL. In recent years multi-stage 4 K-PTCs [9±11] have been This paper is a continuation of our previous papers on reported with multi-layered hybrid magnetic materials the thermodynamic aspects of pulse tubes [14±17]. We in the coldest regenerator region. Two-stage PTCs can will discuss the thermodynamic losses of the rotary valve provide more than 0.5 W cooling power at 4.2K and and the coecient of performance &COP) of GM-type meet the cooling requirements of superconducting de- PTC in this paper. General expressions for the COP of vices operating at 4 K [12]. By using 3He as the working GM-type PTC, based on two types of pressure pro®les, ¯uid the lowest temperature below 1.8 K has been the sinusoidal wave inside the pulse tube and the step wave at the compressor side, have been derived and compared with those of Stirling-type PTCs. q This work was partly carried out at Faculty of Applied Physics, Eindhoven University of Technology, P.O. Box 513, NL-5600 MB Eindhoven, The Netherlands. 2. Thermodynamic analysis * Tel.: +86-10-6262-7302; fax: +86-10-6256-4049. E-mail address: [email protected] &Y.L. Ju). Fig. 2shows the compressor and the rotary valve 1 On leave from Faculty of Applied Physics, Eindhoven University of Technology, P.O. Box 513, NL-5600 MB Eindhoven, The Nether- parts of a GM-type PTC with enthalpy ¯ows and en- lands. tropy ¯ows in it. Consider the control volume at left 0011-2275/01/$ - see front matter Ó 2001 Elsevier Science Ltd. All rights reserved. PII: S 0 0 1 1 - 227 5 & 0 1 ) 0 0 1 23 - 0 514 Y.L. Ju / Cryogenics 41 82001) 513±520 Nomenclature q gas density A area h phase angle C ¯ow conductance g viscosity CP heat capacity at constant pressure fV dissipation rate, see Eq. &11) CV heat capacity at constant volume w ratio of ¯ow conductance, see Eq. &24) H enthalpy T notation for general parameter, see Eq. &56) l length U notation for general parameter, see Eq. &59) L length of regenerator W dissipation parameter, see Eq. &61) nà molar ¯ow rate s time p pressure x angular frequency Q heat Subscripts R ideal gas constant 0 average value S entropy 1 ori®ce t time 2double-inlet t period c A amplitude T temperature ac aftercooler u velocity c compressor U internal energy chx cold heat exchanger V volume à hhx hot heat exchanger V volume ¯ow rate H hot end, high-pressure side W work L cold end, low-pressure side Z ¯ow impedance m molar quantity Greeks r regenerator a ratio of molar ¯ow rate, see Eq. &25) t tube, total aV volumetric thermal expansion coecient V rotary valve side, which contains the compressor and the aftercooler. The system is in steady state unchanged over one Applying the ®rst law of thermodynamics to this system, cycle, so the average internal energy U_ 0. Eq. &1) be- the rate of increase of the internal energy U_ is given by comes à à _ à à _ _ W_ Q_ H À H 2 U H mL À H mH W À Qac; 1 ac mH mL _ If the gas is an ideal gas and if it enters and leaves the where Qac is the heat extracted in the aftercooler. The heat ¯ow and the molar ¯ow rates are positive when control system at room temperature TH, the enthalpy at they ¯ow into the control volume. We consistently de- note ¯ows of extensive quantities with an asterisk * on à top &like H) and the rate of change of extensive quan- tities of a certain system with a dot on top &like U_ ). For heat ¯ows and entropy production rates, which are pa- rameters rather than changes in functions of state, we will use the dot notation. Fig. 1. Schematic diagram of a GM-type PTC: &1) compressor; &2) Fig. 2. Control volume of the compressor and the rotary valve parts aftercooler; &3) rotary valve; &4) regenerator; &5) cold end heat ex- with enthalpy ¯ows and entropy ¯ows in it. The control volume at the changer; &6) pulse tube; &7) hot end heat exchanger; &8) buer; &9) or- left side contains the compressor and the aftercooler; the right side i®ce; &10) double-inlet. contains the rotary valve and the connecting tubes. Y.L. Ju / Cryogenics 41 82001) 513±520 515 the low- and the high-pressure sides are equal. Eq. &2) _ THSV becomes fV : 11 W_ _ _ W Qac: 3 The COP of GM-type PTC is given by The second law gives the rate of increase of the en- ! Q_ T T S_ _ L L H t tropy S: COPGM 1 À : 12 W_ TH À TL W_ Q_ à à _ ac _ S À S mL À S mH Sac: 4 TH The system is in the steady state over one cycle, so the 3. COP of GM-type PTC !sinusoidal function) average entropy production rate S_ 0. Eq. &4) can be rewritten as Based on our previous paper [15] about Stirling-type PTC we will derive below the expressions for the COP of Q_ à à ac _ S mL À S mH Sac: 5 GM-type PTC. Assuming the pressure pro®les inside the TH tube are sinusoidal For an ideal gas, we have pt p0 p1 cos xt: 13 à à à pH The volume ¯ow rate through the ori®ce and double- S mH À S mL ÀnR ln : 6 pL inlet valves can be expressed as For the ideal case the compressor works reversibly, à _ V 1 C1 pt À p0C1p1 cos xt; 14 Sac 0. Combining with Eq. &3), the work needed to compress the gas from the low pressure p to the high à L V 2 C2 pc À pt; 15 pressure pH sides of the compressor is given by where C1 and C2 are the ¯ow conductances of the ori®ce à p _ H W nTHR ln : 7 and double-inlet valves, respectively. The gas velocity at pL the hot end of the tube can be approximated as Consider the control volume at the right-hand side in 1 à à 1 u V À V C p À p ÀC p À p : 16 Fig. 2, which contains the rotary valve and the con- H A 1 2 A 1 t 0 2 c t necting tubes. The system is also in steady state over one t t cycle. The enthalpy ¯ows entering and leaving the sys- The gas velocity at the cold end of the tube is given by tem at the compressor side are equal, so there is no net [15] enthalpy change due to this gas ¯ow. Also there are no CV Lt dpt enthalpy ¯ows entering and leaving this system at the uL uH : 17 CP p0 dt regenerator side. The rotary valve works isothermally, so in the case of an ideal gas no heat has to be extracted We assume here that the ®lling factor of the regenerator from it.
Details
-
File Typepdf
-
Upload Time-
-
Content LanguagesEnglish
-
Upload UserAnonymous/Not logged-in
-
File Pages8 Page
-
File Size-