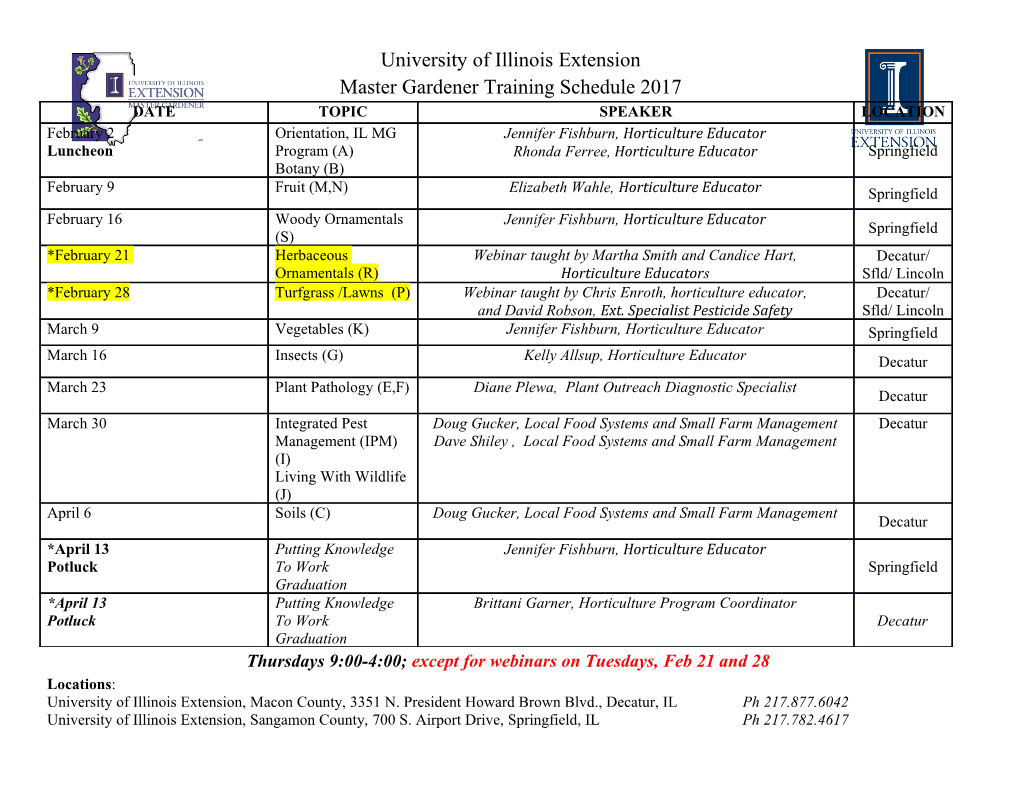
Interscience Research Network Interscience Research Network Conference Proceedings - Full Volumes IRNet Conference Proceedings 2-12-2012 Proceedings Of International Conference on Advanced Research in Mechanical Engineering DR. CH R. VIKRAM KUMAR Dept. of Mechanical Engineering N.B.K.R.I.S.T, Vidyanagar Follow this and additional works at: https://www.interscience.in/conf_proc_volumes Part of the Mechanical Engineering Commons Recommended Citation KUMAR, DR. CH R. VIKRAM Dept. of Mechanical Engineering, "Proceedings Of International Conference on Advanced Research in Mechanical Engineering" (2012). Conference Proceedings - Full Volumes. 9. https://www.interscience.in/conf_proc_volumes/9 This Book is brought to you for free and open access by the IRNet Conference Proceedings at Interscience Research Network. It has been accepted for inclusion in Conference Proceedings - Full Volumes by an authorized administrator of Interscience Research Network. For more information, please contact [email protected]. Exprimental Investigation on Effect of Process Parameters In Cold Backward Extrusion P. J. Pawar & D. D. Patil Department of Production Engineering, K.K.W.I.E.E & R, Nashik, India. E-mail : [email protected], [email protected] Abstract - Cold backward extrusion is one of the youngest forming processes. It shows numerous qualitative advantages like high production rate, short piece production time, better surface quality and good static and dynamic quality’s of formed component. Having such enormous application, some of biggest hindrances are power requirement of process to form the product at cold state and non- homogeneous distribution of strain, as result dimensional instability occurs. Aim of study is to find the effect of process parameters in cold backward extrusion process used to manufacture aluminum collapsible tubes. Extrusion force, stroke length, slug diameter and back pressure are treated as process variables while response of power, extrusion length, thickness of diaphragm and thickness of nozzle is recorded. Experimental trials with subsequent data collection are performed and empirical relation amongst the process variable and performance measures were determined by means of response surface methodology (RSM). Results reveals some stimulating fact about cold backward extrusion process, it is observe that all process parameters has influence the response. Keywords - cold backward extrusion, response surface methodology. homogeneous, which means cold backward extrusion I. INTRODUCTION process deals with a non-stationary process behavior Extrusion, though one of the most important which produced dimensional instability [1,4]. manufacturing processes today, is a relatively young Many researchers contributed to predict effects of metalworking process. Some of the latest developments various process parameters. A. H. Elkholy [5] within the manufacturing industry have revealed how introduced analytical model for studying hydrostatic emerging extrusion technologies can be used to reduce extrusion. The model is use to investigate various production lead time and manufacture mass range of parameters affecting extrusion, these parameters being: product [1,2]. The main benefits cold backward die cone angle, reduction ratio and frictional coefficient extrusion process offer as compared to other die shape. Model is extended to optimize power manufacturing process are optimal usage of material, requirement and frictional losses. high production rate with short piece-production time and forms coupled with a good surface quality, good Effect of reduction ratio on power requirement of static and dynamic properties of the components due to process is significant while improvement in the process the favorable fiber structure and work hardening [1,2,3]. can be possible [4, 6]. M. Gierzynska-dolna [7] With these merits cold backward extrusion processes is performed attempt to optimum selection of extrusion capable to produce complex part design for special condition for determined range of process parameter, purpose use and serve for many industries like Minimization of crack with in product was established pharmaceutical, aerospace, automobile, consumer goods as main criterion. K. Kuzman [6] discus the influence of etc. tool geometry, friction and lubrication as well as work- piece properties on balanced material flow in combined Having such enormous advantages some of the extrusion process. J. Mstowski [4] worked on biggest hindrance in the full scale application of cold optimization of cold backward extrusion; aim of the backward extrusion technology are requirement of huge study was constant thickness of internal anti-frictional amount of power to form product in to cold state [1], cladding on a plain bearing in one operation. Study which substantially increased the manufacturing cost of suggested theoretical model of velocity field permit the the product. The distribution of the comparative strain approach of geometrical optimization. for cold backward extrusion is clearly non- International Conference on Advanced Research in Mechanical Engineering (ICARME-2012) - 12th February, 2012 - Ahmedabad 1 Exprimental Investigation on Effect of Process Parameters In Cold Backward Extrusion J. Danckert [8] elaborated effect of punch land on Process Variables : cold backward extrusion. The results show that a slight The process variables chosen for the optimization tilt of the punch land changes the contact conditions of the process are as follows: between punch land and can wall causing on the punch a net force, which will deflect the punch off Centre Extrusion force : Fe (kN), leading to variations in wall thickness. S.O Onuh [9] expressed relation of die geometry and extrusion speed Stroke length : Sl (mm) of cold backward extrusion. An experimental Diameter of slug : ds (mm), investigation is made on the effects of die reduction in 2 area, die angle, loading rate on the quality of the Back pressure : Pb (N/mm ) extrusion products, extrusion pressures and flow pattern Performance measures: of cold extruded aluminium and lead alloys shapes of inner circular sections with four symmetrical Power requirement of process : Pw (watt) projections. The radii of curvature for both extruded Extrusion length : L (mm) lead and aluminium alloys and the average hardness e values of the extruded products along the projections Thickness of diaphragm : Td (mm) and along the circumferential solid positions are found to increase with increase in die reduction in area, and Thickness of nozzle : Tn (mm) slightly with increase of the loading rates [9,10]. M. Here thickness of diaphragm (Td) and thickness of Bakhshi-Jooybari [10] studied optimum die design and nozzle (Tn) are critical dimensions of specimen and aim illustrated that the extrusion load for optimum curved to be controlled with in specified limit. Maximum die is reduced by 11%, compared to that in the optimum possible range of each process variable is defined below. conical die. Variable bounds: Cold backward extrusion processes in engineering industries need to be cost and quality efficient for 380 Fe 770(kN) industries to sustain and excel in current competitive scenario. A significant improvement in process 341 Sl 344(mm) efficiency may be obtain if effect of process parameters 19 d 22(mm) on power requirement and dimensional variation are s identifies and determines the regions of critical process 50 P 125 N /( mm2 ) control factors leading to desired outputs or responses b with acceptable variations ensuring a lower cost of manufacturing. So work is carried out with aim to find III. EXPERIMENTATION effect of process parameters on power requirement and dimensional variation of final product. An extrusion press of 100 ton is utilized to manufacture aluminum collapsible tube part i.e. In this study response surface methodology is used benthovate-c, the experimental setup is as shown in Fig. to elaborate relationship between cold backward 1. Benthovate-c made of 96% pure aluminum is used for extrusion process parameters and response of the experimental trials product design of the part is as process. Response surface methodology is very useful shown in Fig. 2. and modern technique for the prediction and optimization of machining performances. Response surface methodology (RSM) is a collection of statistical and mathematical techniques useful for developing, improving, and optimizing processes. The most extensive applications of RSM are in the particular situation where several input variables potentially influence some performance measures or quality characteristics of the process [11, 12]. II. SELECTION OF PROCESS PARAMETERS AND PERFORMANCE MEASURES Mathematical model is developed by using response surface methodology. Process parameters and responses Fig. 1 : Extrusion press utilized for experimentation selected for the study are as follows. International Conference on Advanced Research in Mechanical Engineering (ICARME-2012) - 12th February, 2012 - Ahmedabad 2 Exprimental Investigation on Effect of Process Parameters In Cold Backward Extrusion q a 2 4 2 (1) Where q is numbers of input variables While factorial points use in experimental design having “q” number of variable can calculate by. q (2) n f 2 16 And axial points are calculated by. (3) na 2q 8 Fig. 2 : Specieman test sample design Total numbers of experimental trials are as follows. Pri-experimental trials are performed to record initial condition of the process utilized by industry. In N
Details
-
File Typepdf
-
Upload Time-
-
Content LanguagesEnglish
-
Upload UserAnonymous/Not logged-in
-
File Pages134 Page
-
File Size-