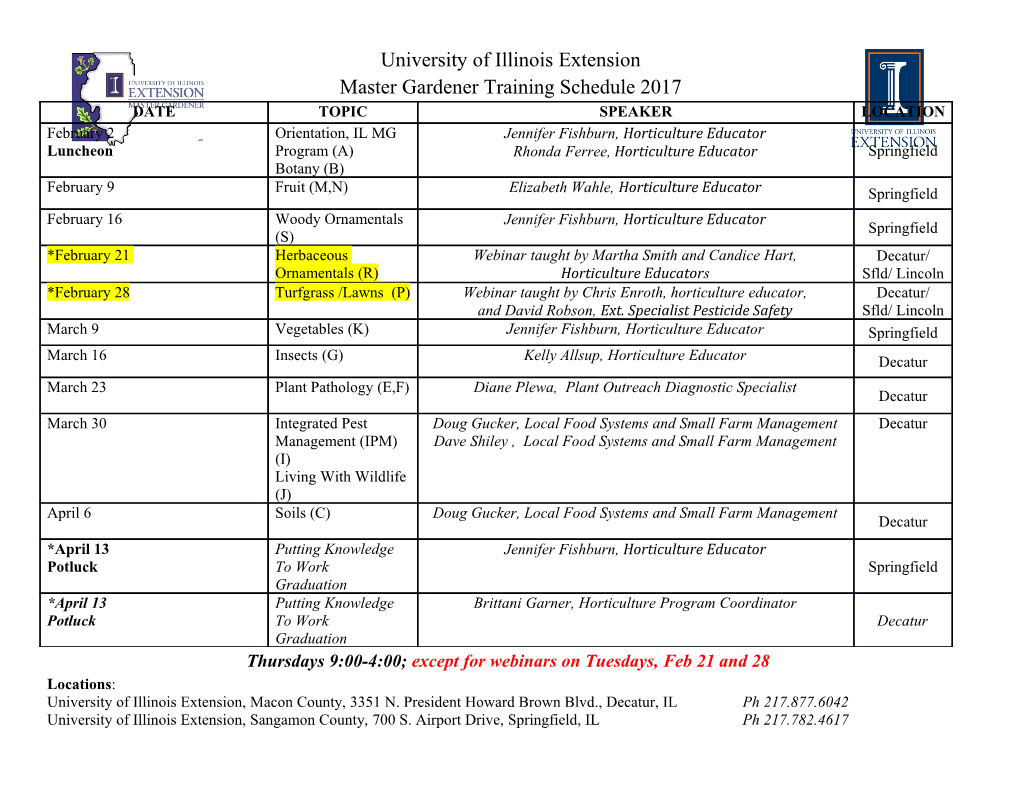
Europaisches Patentamt (19) European Patent Office Office europeenpeen des brevets EP 0 862 594 B1 (12) EUROPEAN PATENT SPECIFICATION (45) Date of publication and mention (51) intci.6: C08J 7/04, B41M 5/26 of the grant of the patent: 08.09.1999 Bulletin 1999/36 (86) International application number: PCT/GB96/02710 (21) Application number: 96935176.6 (87) International publication number: (22) Date of filing: 06.11.1996 WO 97/19128 (29.05.1997 Gazette 1997/23) (54) RELEASE FILM TRENNFOLIE FILM ANTIADHERENT (84) Designated Contracting States: (56) References cited: DE FR GB IT EP-A- 0 349 141 WO-A-90/06958 DE-A- 2 832 281 (30) Priority: 21.11.1995 GB 9523765 21.11.1995 US 560762 PATENT ABSTRACTS OF JAPAN vol. 015, no. 285 (C-0851), 19 July 1991 & JP 03 100027 A (43) Date of publication of application: (TOR AY IND INC), 25 April 1991, 09.09.1998 Bulletin 1998/37 DATABASE WPI Section Ch, Week 8545 Derwent Publications Ltd., London, GB; Class A23, AN (73) Proprietor: E.I. DU PONT DE NEMOURS & 85-280986 XP002026801 & JP 60 192 628 A (DIA COMPANY INCORPORATED FOIL KK) , 1 October 1985 Wilmington Delaware 19898 (US) DATABASE WPI Section Ch, Week 931 1 Derwent Publications Ltd., London, GB; Class A32, AN (72) Inventor: HIGGINS, David, Edward 93- 088392 XP002026802 & J P 05 032 035 A (Ol KE North Yorkshire Y021 2HJ (GB) KOGYO KK) , 9 February 1993 DATABASE WPI Section Ch, Week 9429 Derwent (74) Representative: Jones, Alan John et al Publications Ltd., London, GB; Class A11, AN CARPMAELS & RANSFORD 94- 239020 XP002026803 & JP 06 172 723 A 43 Bloomsbury Square (AS AH I KASEI KOGYO KK) , 21 June 1994 London, WC1A2RA (GB) PATENT ABSTRACTS OF JAPAN vol. 013, no. 372 (C-627), 17 August 1989 & JP 01 126389 A (DAINICHISEIKA COLOR & CHEM MFG CO LTD;OTHERS: 01), 18 May 1989, DO ^> O) io CM CO 00 Note: Within nine months from the publication of the mention of the grant of the European patent, any person may give notice the Patent Office of the Notice of shall be filed in o to European opposition to European patent granted. opposition a written reasoned statement. It shall not be deemed to have been filed until the opposition fee has been paid. (Art. a. 99(1) European Patent Convention). LU Printed by Jouve, 75001 PARIS (FR) EP 0 862 594 B1 Description [0001] This invention relates to a release film and to a method for the production thereof. [0002] Abherents or release agents are generally solid or liquid film-forming materials employed to reduce or prevent 5 adhesion between two surfaces. They are employed in a variety of industrial processes, including metal casting, food preparation and packaging, polymer processing and paper coating, in the production of moulded resin articles, stamping foils and pressure-sensitive adhesive tapes, and in applications such as thermal transfer printing. Typical abherents include natural and synthetic waxes, metal salts of fatty acids, particularly stearic acid, and polymers, such as polyvi- nylalcohols, polyamides, polyolefins and silicone resins. 10 [0003] A release agent is conveniently employed in association with a polymeric support film. When associated with a support film a release agent must satisfy apparently conflicting criteria, by bonding firmly to the support while providing easy and complete release from an opposing surface. Silicone resins, based on a silicon-oxygen polymer backbone with pendant aliphatic or aromatic carbon side chains, have assumed importance as release agents in recent years, and generally confer good release characteristics. For example EP-323063-A discloses an oriented polymeric film is having a release layer of a silicone resin and a volatile inhibitor. EP-342826-A and EP-416765-A describe a release film formed from a self-supporting polymeric film substrate and a polyurethane resin containing polydialkylsiloxane. However, with such prior art release films, the adhesion of the release layer to the film substrate can be inadequate. Furthermore, the release properties achieved are not always sufficient for all applications. Consequently there exists a commercial requirement for improved release films. 20 [0004] The use of silicone resins, when applied to a film substrate during production thereof, is frequently liable to evolve volatile siliceous debris, which not only constitutes a health hazard, possibly necessitating the wearing of dust masks and protective clothing by plant operatives, but also, and importantly, severely contaminates the film production line and renders it unsuitable for the subsequent production of alternative film grades. [0005] It may be necessary to sequentially apply a number of coating layers in order to obtain the required release 25 characteristics. At least one of the aforementioned coating layers is traditionally applied to the film substrate after the production of the film has been completed, ie "off-line", which results in an increase in the number of process steps required to produce the coated film. There is a need to be able to achieve the required release characteristics by a single coating application, preferably during the film making process, ie "in-line", in order to simplify and improve the efficiency of the production process. 30 [0006] We have now devised an improved release film which reduces or substantially overcomes at least one of the aforementioned problems. [0007] Accordingly, the present invention provides a release film comprising a polymeric film substrate having on at least one surface thereof, a release layer formed from a release composition comprising a mixture of a curable silicone resin and a curable polyurethane resin comprising at least one ethylenically unsaturated group. 35 [0008] The invention further provides a method of producing a release film which comprises forming a polymeric film substrate, applying a release composition to at least one surface of the substrate, the release composition comprising a mixture of a curable silicone resin and a curable polyurethane resin, and curing the release composition to form a release layer. [0009] The invention also provides a thermal transfer printing receiver sheet comprising a polymeric film substrate 40 having on at least one surface thereof, a dye-receptive receiver layer, and a release layer on the surface of the receiver layer remote from the substrate, the release layer being formed from a release composition comprising a mixture of a curable silicone resin and a curable polyurethane resin. [0010] The polymeric film substrate is a film capable of independent existence in the absence of a supporting base. [0011] The substrate to which a release composition is applied to yield a release film according to the invention may 45 be formed from any suitable film-forming, polymeric material. Thermoplastics materials are preferred, and include a homopolymer or copolymer of a 1 -olefin, such as ethylene, propylene and but-1-ene, a polyamide, a polycarbonate, more preferably a polyester, and particularly a synthetic linear polyester which may be obtained by condensing one or more dicarboxylic acids or their lower alkyl (up to 6 carbon atoms) diesters, eg terephthalic acid, isophthalic acid, phthalic acid, 2,5-, 2,6- or 2,7-naphthalenedicarboxylic acid, succinic acid, sebacic acid, adipic acid, azelaic acid, 4,4'- so diphenyldicarboxylic acid, hexahydro-terephthalic acid or 1 ,2-bis-p-carboxyphenoxyethane (optionally with a mono- carboxylic acid, such as pivalic acid) with one or more glycols, particularly aliphatic glycols, eg ethylene glycol, 1 ,3-pro- panediol, 1 ,4-butanediol, neopentyl glycol and 1 ,4-cyclohexanedimethanol. A polyethylene terephthalate and/or poly- ethylene naphthalate film is preferred. A polyethylene terephthalate film is particularly preferred, especially such a film which has been biaxially oriented by sequential stretching in two mutually perpendicular directions, typically at a tem- 55 perature in the range from 70 to 125°C, and preferably heat set, typically at a temperature in the range from 150 to 250°C, for example as described in GB-A-838708. [0012] The substrate may also comprise a polyarylether orthio analogue thereof, particularly a polyaryletherketone, polyarylethersulphone, polyaryletheretherketone, polyaryletherethersulphone, or a copolymer or thioanalogue thereof. 2 EP 0 862 594 B1 Examples of these polymers are disclosed in EP-A-1879, EP-A-1 84458 and US-A-4008203. Blends of these polymers may also be employed. A poly p-phenylene sulphide film is also suitable. [0013] Suitable thermoset resin substrate materials include addition-polymerisation resins, such as acrylics, vinyls, bis-maleimides and unsaturated polyesters, formaldehyde condensate resins such as condensates with urea, mela- 5 mine or phenols, cyanate resins, isocyanate resins, epoxy resins, functionalised polyesters, polyamides or polyimides. [0014] A film substrate for a release film according to the invention may be unoriented or preferably oriented, for example uniaxially oriented, or more preferably biaxially oriented by drawing in two mutually perpendicular directions in the plane of the film to achieve a satisfactory combination of mechanical and physical properties. Formation of the film may be effected by any process known in the art for producing a polymeric film, for example a tubular or a flat film 10 process. [0015] In a tubular process simultaneous biaxial orientation may be effected by extruding a thermoplastics polymeric tube which is subsequently quenched, reheated and then expanded by internal gas pressure to induce transverse orientation, and withdrawn at a rate which will induce longitudinal orientation. [0016] In the preferred flat film process a film-forming polymer is extruded through a slot die and rapidly quenched is upon a chilled casting surface (drum) to ensure that the polymer is quenched to the amorphous state. Orientation is then effected by stretching the quenched extrudate in at least one direction at a temperature above the glass transition temperature of the polymer. Sequential orientation may be effected by stretching a flat, quenched extrudate firstly in one direction, usually the longitudinal direction, ie the forward direction through the film stretching machine, and then in the transverse direction.
Details
-
File Typepdf
-
Upload Time-
-
Content LanguagesEnglish
-
Upload UserAnonymous/Not logged-in
-
File Pages11 Page
-
File Size-