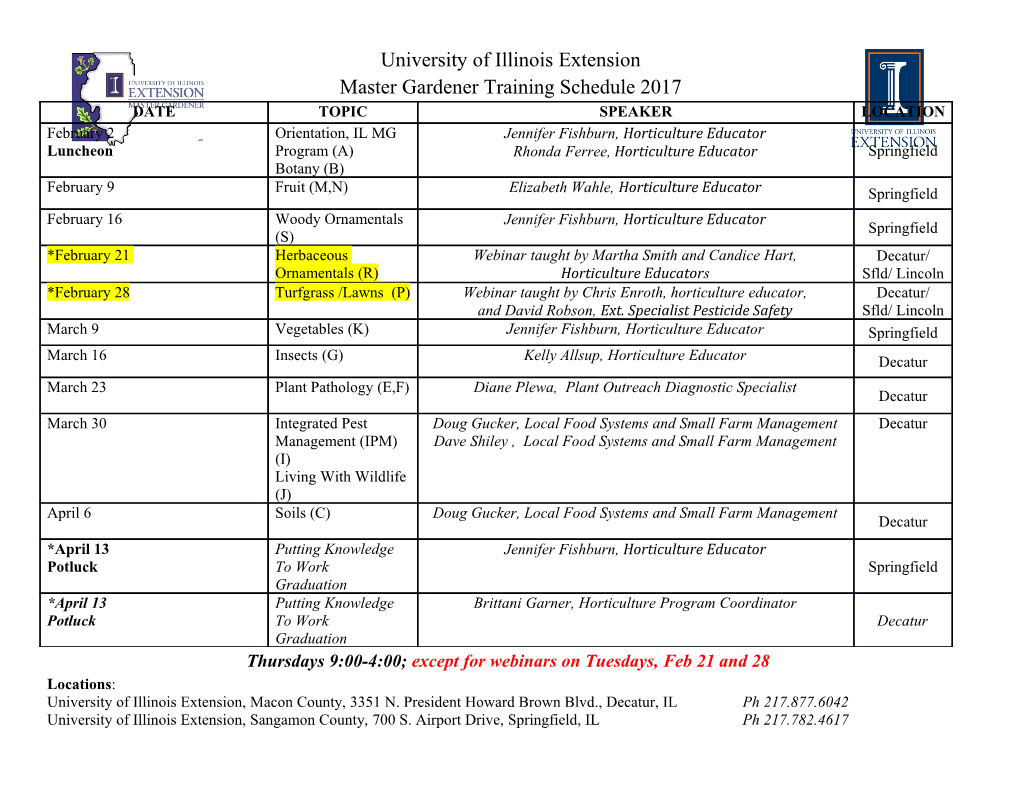
ISSN: 2689-1204 Research Article Journal of Applied Material Science & Engineering Research Design, Fabrication and Construction of Cupola Furnace for Metallurgical Industries Ocheri C Department of metallurgical and Materials Engineering, University *Corresponding author of Nigeria, Nsukka, Nigeria Ocheri C, Department of metallurgical and Materials Engineering, University of Nigeria, Nsukka, Nigeria Submitted: 10 Sept 2020; Accepted: 16 Sept 2020; Published: 13 Oct 2020 Abstract A 350 kilogram per hour capacity Cupola Furnace was designed and fabricated from locally available materials for the production of cast iron using pig iron, oily or contaminated steel scraps, foundry returns and fluxes. The main fuel used is metallurgical coke. After analyzing the design parameters, the metallic shells were fabricated in four segments for easy lining: the stack zone, preheating zone, combustion zone and the hearth. Mild steel sheet of 4 mm thickness was procured, marked out as per the design drawing, sliced, rolled into cylindrical shapes and welded together at each seam. The internal configuration was lined first with asbestos paper measuring 4 mm thick using water-glass to enable it adhere to the internal shell of the segments, thereafter, a less dense insulating refractory material was used and finally fireclay refractory bricks were used for lining as they interface directly with the molten metal. The various segments were then assembled and erected with the blower connected to the combustion zone. The research work also contains the materials and components bill. Keywords: Assembling, Cupola-furnace, Design, Fabrication, 1.5Cr) hardness thus obtained is of the order of 700 Brinell. This Refractories being almost un-machineable. It is used in parts requiring high abrasion resistance. Introduction Cupola furnace is a melting device used in foundries majorly to Cupola furnace is similar to a small blast furnace. It is cylindrical produce cast iron and bronzes. It is a continuous melting shaft in shape and the cambers are arranged vertically. It is usually furnace capable of processing different range of raw materials fabricated with mild steel (flat sheet plates) and special clay or from pig iron, oily and contaminated scraps, foundry returns and refractory bricks are used as inner lining materials. It utilizes coke ferroalloys [1]. Its main energy source is metallurgical coke. It is & limestone as the main source of fuel and fluxing agent one of the oldest methods of producing cast iron, and it remains respectively. The furnace is mainly used, for the casting of grey the dominant method because of its simplicity and low fuel cost. cast iron and for the casting of white or chilled cast iron. Grey cast The size of a cupola is expressed in diameter and can range from iron is produced by melting together low quality foundry pig iron 0.5 m to 4 m [5]. The overall shape is cylindrical and the equipment scrapped casting and coke in a cupola. The fractured of this type of is arranged vertically, usually supported by three or four legs. The cast iron gives a grey appearance and has got most of its carbon in overall look is similar to a large “smokestack” [5]. The bottom of a graphite form. Hence, it is soft, easily machinable metal with the cylinder is fitted with doors, which swing down and out to high damping capacity and high compressive strength. It has self- “drop bottom”. The top where gases escape can be open or fitted lubricating characteristics. with a cap to prevent rain from entering the cupola. To control emissions, a cupola may be fitted with a cap that is designed to White or chilled cast iron: same mode of production as grey cast pull the gases into a device to cool the gases and remove particulate iron but has no graphite and is, therefore white in color. The whole matter [9]. of carbon content in this type of cast iron is in the form of either free cementite or cementite in lamellar pearlite. White cast iron is The shell of the cupola being usually made of steel has refractory very hard, brittle and wear resistant iron. Hardness of 400 Brinell brick and plastic refractory patching material lining it. The bottom is can be obtained by keeping silicon below 1%, carbon to about 2% lined in a similar manner but often a clay and sand mixture (“Bod”) in cast iron the toughness and strength of white cast iron is doubled may be used, as this lining is temporal. Finely divided coal (sea coal) by small additions of Nickel, and chromium (e.g. 4.5% Ni and can be mixed with the clay lining so that when heated the coal J App Mat Sci & Engg Res, 2020 www.opastonline.com Volume 4 | Issue 4 | 134 decomposes and the bod becomes slightly friable, easing the opening and coke are added until the level reaches the charging doors. The up of the tap hole. The bottom lining is compressed or rammed against metal charged would consist of pig iron; scrap steel and domestic the bottom doors [1]. Some cupolas are fitted with cooling jackets to returns [8]. keep the sides cool and with oxygen injection to make the coke fire burn hotter. Additionally, the cupola is a counter flow vertical shaft An air blast is introduced through the wind box and tuyeres located furnace and offers the high possibility of good melting efficiency near the bottom of the cupola. The air reacts chemically with the compared with batch type melters [2]. carbonaceous fuel thus producing heat of combustion. Soon after the blast is turned on, molten metal collects on the hearth bottom The current growing rate of unemployment became more where it is eventually tapped out into a waiting ladle or receiver. pronounced because most of our indigenous companies are in As the metal is melted and fuel consumed, additional charges are comatose simply because of non-availability of fast wearing spare added to maintain a level at the charging door and provide a parts. Therefore, the design and fabrication of cupola furnace continuous supply of molten iron. using locally sourced materials and indigenous technology will ameliorate the situation thereby making it easier for metallurgical At the end of the melting campaign, charging is stopped but the air institutions to cast simple and complex spare parts to keep our blast is maintained until all of the metal is melted and tapped off. industries functional. It will also assist research engineers to The air is then turned off and the bottom doors opened allowing further their research with a view to improving the quality of the residual charge material to be dumped [10]. products and develop new materials. Materials and Methods Working Principles of the Cupola Furnace Materials For many years, the cupola was the primary method of melting The materials utilized for the design and fabrication of cupola used in iron foundries. The cupola furnace has several unique furnace are: mild steel plates, steel angle bars, steel pipes, M24 characteristics, which are responsible for its widespread use as a bolts and nuts, asbestos sheets, less dense/insulation refractory melting unit for cast iron. bricks, dense refractory bricks (fireclay), electric centrifugal (i) The cupola is one of the only methods of melting which is blower, refractory cement, magnesite powder, zircon sand and continuous in its operation water glass (sodium silicate, Na₂SiO₃). (ii) High melt rates (iii) Relatively low operating costs Cupola Furnace Design and Material Selection (iv) Ease of operation Considerations The main parts of the cupola furnace are the vertical steel shell The construction of a conventional cupola consists of a vertical (comprising the well/hearth, combustion/melting zone, preheating steel shell, which is lined with refractory bricks. The charges are zone and charging zone), the tuyeres, electric centrifugal blower and introduced into the furnace body by means of an opening the bottom cover. The design of the cupola furnace is based on approximately half way up the vertical shaft. The charges consist considerations and functionality of the various components/parts, of alternate layers of the metal to be melted, coke fuel and design cost, local availability of materials/components, availability of limestone. The fuel is burnt in air, which is introduced through fuel and the ease of fabrication process and the lining of the internal tuyeres positioned above the hearth. The hot gases generated in the wall. Figures 1-8 show various parts of the furnace while figure 9 lower part of the shaft ascend and preheat the descending charge [4]. shows the 2D CAD view of the cupola furnace is presented in Fig. 1 The cupola is of the drop bottom type with hinged doors under the hearth, which allows the bottom to drop away at the end of melting to aid cleaning and repairs. At the bottom front is a tap hole for the molten iron at the rear, positioned above the tap hole is a slag hole. The top of the stack is capped with a spark/fume arrester hood. The internal diameters of cupola are 380 mm which can be operated on different fuel to metal ratio, giving melt rates of approximately 350 kilograms per hour. The operation cycles for the cupola, consist of closing and propping the bottom hinged doors and preparing a hearth bottom. The bottom is usually made from low strength moulding sand and slopes towards the tapping hole. A fire is started in the hearth using lightweight timber; cokes are charged on top of the fire and is burnt by increasing the air draught from the tuyeres. Once the coke bed is ignited of the required height, alternate layers of metal, flux Figure 1: Shows the collection of Chambers J App Mat Sci & Engg Res, 2020 www.opastonline.com Volume 4 | Issue 4 | 135 Figure 5: shows the Charging Chamber Figure 2: shows the Melting Chamber Figure 3: Development of the Melting Chamber Figure 6: shows the Flanges Figure 4: shows the Pre –heating Chamber Figure 7: Shows the Air Trapped Cover J App Mat Sci & Engg Res, 2020 www.opastonline.com Volume 4 | Issue 4 | 136 with spy holes in order for the operator to view the melting operation within the combustion zone.
Details
-
File Typepdf
-
Upload Time-
-
Content LanguagesEnglish
-
Upload UserAnonymous/Not logged-in
-
File Pages8 Page
-
File Size-