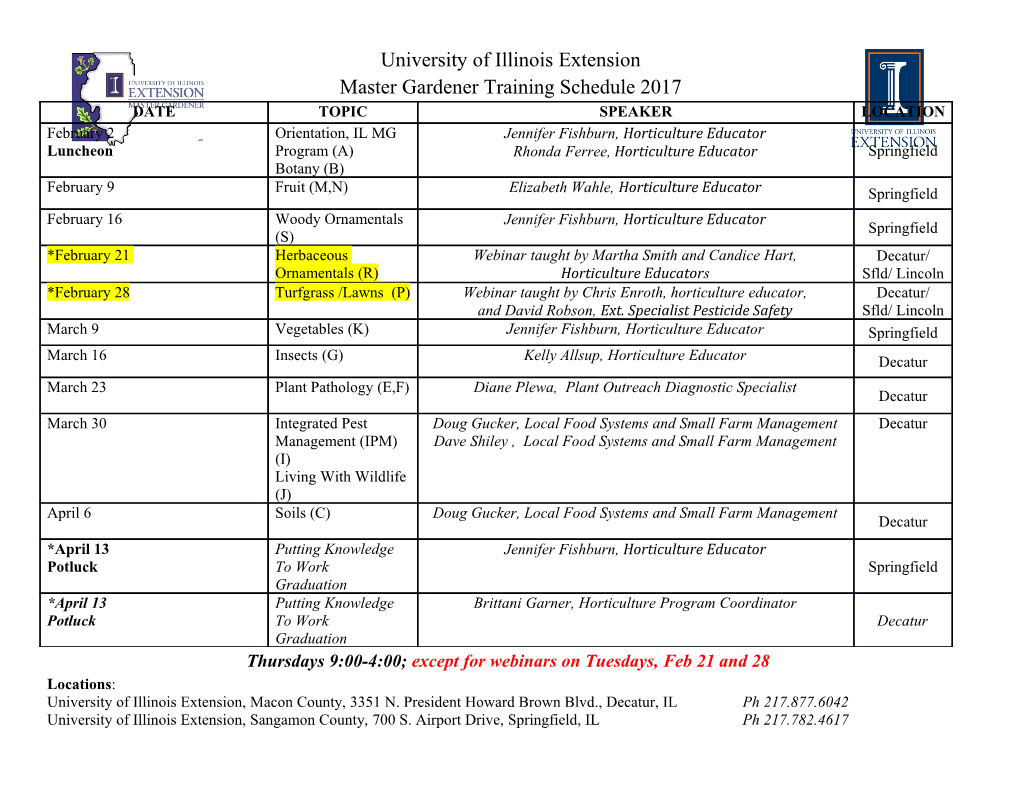
EUROPEAN COMMISSION Brussels, 15.09.2009 C(2009)6874 final Subject: State aid N 357/2009 — United Kingdom Individual R&D aid to GKN ASL Sir, 1. PROCEDURE (1) The aid measure under assessment was pre-notified on 21 November 2008. Two meetings took place between the Commission and the UK authorities during the pre- notification phase, the first on 25 November 2008 and the second on 28 April 2009. The UK authorities notified the measure on 16 June 2009, and it was registered on the same day. (2) On 10 July 2009, the Commission sent electronically a request for information to the UK authorities, to which the UK authorities replied on 4 August 2009. (3) The Commission sent a request for a delay extension on the basis of Article 4(5) of Council Regulation (EC) No 659/1999 on 10 August 2009, which the UK authorities accepted on 17 August 2009. 2. DESCRIPTION OF THE MEASURE 2.1. Legal basis (4) The legal basis of the notified measure is Section 1 of the 1982 Civil Aviation Act. It enables the Secretary of State to exercise a general duty of ‘organising, carrying out The Rt Hon David MILIBAND Secretary of State for Foreign Affairs Foreign and Commonwealth Office King Charles Street London SW1A 2AH United Kingdom Commission européenne, B-1049 Bruxelles – Europese Commissie, B-1049 Brussel – Belgium Telephone: 00 32 (0) 2 299.11.11 and encouraging measures for (…) the designing, development and production of civil aircraft’. 2.2. The beneficiary (5) The beneficiary of the measure is GKN Aerospace Services Limited. (6) GKN group is a global engineering business operating in the automotive, aerospace and off-highway sectors. The activities of the group in the automotive sector account for around 68 % of the group’s revenue and comprises GKN Driveline, Powder Metallurgy and other automotive companies, which supply a variety of components to the global car and light vehicle markets. The activities of the group in the aerospace sector account for around 21 % of the group’s revenue and comprise activities concentrated on structural components, propulsion systems and special components for both military and civil aerospace markets. The activities of the group in the off- highway sector account for around 11 % of the group’s revenue and comprise the design and manufacture of steel wheels and driveline systems for the global agricultural, construction and industrial machinery markets. The GKN group has operations in over 30 countries with 36 500 employees in subsidiary companies plus 3 500 in joint ventures. In 2008 it achieved sales of £4.6 billion and a profit of £167 million. (7) The beneficiary of the aid, GKN Aerospace Services Limited, is a fully owned subsidiary of GKN plc. An acquisition programme in the late 1990s began to transform GKN into an international first-tier supplier to the world’s major prime contractors with participation in some of the world’s most advanced programmes, including the Airbus A380 ‘Superjumbo’. (8) GKN Aerospace Services Limited supplies composite aircraft structures and is an active player in the design and manufacture of complex metal alloy structures and special products such as canopy systems, aircraft transparencies and de-icing systems. Approximately […]∗ % of GKN’s revenues are derived from the defence sector. The business operates from technology, engineering and manufacturing facilities in the US, Mexico, UK, Germany, India and Australia. 2.3. Context and description of the project (9) On 19 December 2007, GKN was selected by Airbus as the preferred bidder for the wing component and assembly manufacturing facilities at the UK Filton site, and for the A350 XWB contract to design, develop and manufacture the rear spars and fixed trailing edge work packages (R&D project). On 14 September 2008, GKN signed the contract with Airbus for the R&D project. GKN’s acquisition of the site was completed on 5 January 2009. (10) The R&D project under assessment consists of research and development activities on part of the A-350 XWB. The A-350 XWB family consists of three types of airplanes, the A 350-900 (which should be available from 2013), the A 350-800 (which should be available from 2014) and the A 350-1000 (which should be available from 2015). The A350 XWB is of conventional airliner appearance with a double-lobe (ovoid) ∗ Business secret. fuselage cross-section that gives a greater internal cabin width than previous Airbus types, uses significantly more new materials (with around 52 % composite compared to 26 % on the A380), flies faster than A330 Airbus aircraft that the A350 XWB complements and replaces (around Mach 0.85), offers the latest generation of engine technology (the Rolls-Royce Trent XWB) and improved fuel efficiency due to the increased use of light-weight composites. In order for these airplanes to be capable of flying long ranges, faster than previous Airbus aircraft and offer the latest generation of new engine technology, the necessary and significant weight reduction will be mainly achieved by introducing new all-composite wings and fuselage based on new materials. (11) GKN will be responsible for the design, development and manufacture of the following components for the A350 XWB wings: - Composite [...] rear spars; - [...]; - [...]; - [...]; - [...]; - [...]; - [...]; - [...]. (12) GKN will integrate the pre-manufactured spars with the fixed trailing edge components and assemble them into a complete trailing edge assembly. GKN will then be responsible for delivering the complete trailing edge structure for further integration into the wing structure. (13) GKN will conduct industrial research (into material and design innovation process) and experimental development activities (regarding fibre placement manufacturing process, spar tooling, fixed trailing edge tooling, flexible assembly cells, one-way assembly, paint and sealant improvements, determinate assembly and metrology) from 2008 till 2015. (14) GKN has developed strong wing capabilities, with an emphasis on composites. It became a design and build partner on the Airbus A380 Wing Trailing Edge that now has direct applications in propulsion systems such as the General Electric GenX fan case planned to power the B787. GKN expanded the scope of its deployment of composite technologies for the A400M composite wing spar programme which was the first use of composites on this scale on a primary wing structure. As an immediate follow on GKN Aerospace also secured the design and build full wing trailing edge programme. (15) The A350 XWB will allow continuing development of technologies directly derived from the developments utilised in the A400M. However, the A350 XWB wing spars demand significant additional critical technology development compared to that of the A400M1 military airlifter spar package. The utilisation of composite materials for the A350 XWB wing structures will require significant engineering and manufacturing technology to meet the requirements laid down by Airbus for the A350 XWB 1 The Airbus A400M is a four-engine turboprop military transport and tanker, designed and built by Airbus Military. The first delivery is expected for 2012. programme. The formulation and materials development are specific to the A350 XWB and not based on any existing knowledge. (16) The project will further enhance the knowledge of applying composite technology in the aerospace sector. This has several advantages. It has a smaller environmental footprint since composite components are much lighter than metal ones, leading to lighter aircraft which are more fuel efficient. It gives the airplane better structural integrity for equivalent weight and the ability to produce more complex shapes, which is important because of demanding design criteria for new aircraft. It also has advantages in terms of corrosion resistance, fatigue resistance and reduced life cycle costs due to low maintenance requirements. (17) The project comprises ten work packages, whose main features are presented below. Work package 1: Materials (18) GKN is responsible for developing the requirements and processes specific to the A350 XWB of a composite material, called M21E, whose formulation is developed by Hexcel (Hexcel M21E). The chemical properties of the material present challenges in terms of the lay down and forming processes required. (19) The composite material has been through several iterations and GKN has worked with Hexcel to maximise its processability at all stages of manufacture. This has included developing water jet cutting techniques as well as cutter development for machining and drilling. (20) In addition to the composite material, GKN will install a new fastener system requiring new methods of installation to be developed and integrated into the manufacturing process. In order to fully optimise their design and manufacturing processes, GKN will need to undertake extensive coupon testing and development trials to fully evaluate the limits of the material properties and features. Work package 2: Fibre placement manufacturing process (21) The various stages of the composite manufacturing process for the A350 XWB rear spar will draw on the experience gained from shorter spars as part of A400M, but it has been further streamlined by an ever higher use of automated equipment, especially during the part-to-part jigless assembly stage. The challenge of this work package is that the gull wing profile of the wings, their length and weight require finding new fibre placement manufacturing processes. The gull wing profile of the wings results in highly curved inboard spars, which will provide a challenge for the production and fibre placement processes. The A350 XWB wing span is 50 % longer and much heavier than the A400M wing, which requires finding a technical solution to establishing the key parameters for the fibre placement machines and programming software. Wing loading rate improvement is needed — the A400M has a 140 tonnes maximum take-off weight, against 250 to 300 tonnes for the A350 XWB. Work package 3: Spar tooling (22) Mould tools must be made thinner than ever before to improve efficiency and achieve the specified high production rates.
Details
-
File Typepdf
-
Upload Time-
-
Content LanguagesEnglish
-
Upload UserAnonymous/Not logged-in
-
File Pages36 Page
-
File Size-