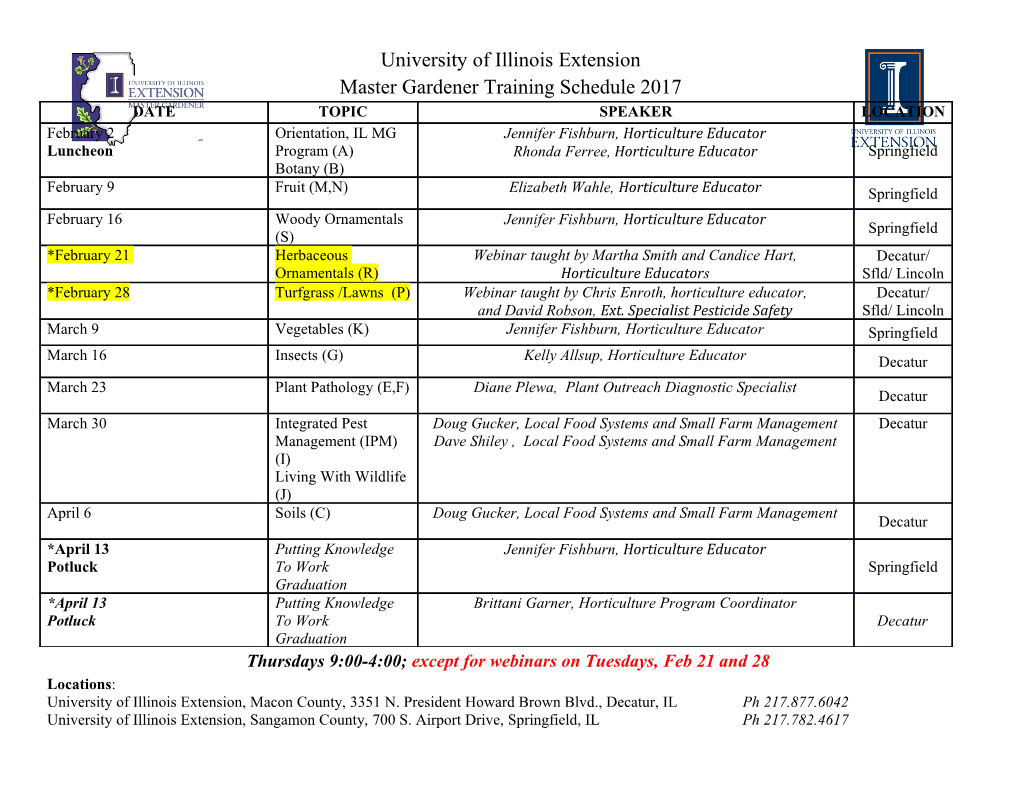
MECH427/527 and AA 284a Advanced Rocket Propulsion Lecture 2 Thrust Equation, Nozzles and Definitions Prepared by Arif Karabeyoglu Mechanical Engineering KOC University Fall 2019 Stanford University Advanced Rocket Propulsion Derivation of the Static Thrust Expression x • Force balance in the x direction I :Unity Tensor τ : Stress Tensor T + P nˆ d A + PI −τ ⋅ nˆ d A = 0 P : Pr essure ∫ a x ∫( ) x Pa : Ambient Pr essure As Ac Pe : Exit Pr essure • Assumption 1: Static firing/ External gas is at rest Ue : Exit Velocity • Assumption 2: No body forces acting on the rocket T :Thrust Force Stanford University 2 Karabeyoglu Advanced Rocket Propulsion Derivation of the Static Thrust Expression • First Integral: – Since As+Ac and Ae+Ac are closed surfaces and Pa is constant P nˆ d A = 0 P nˆ d A = 0 ∫ a x ∫ a x As +Ac Ac +Ae – These integrals can be separated and combined to yield the following simple expression for the first integral P nˆ d A = P A ∫ a x a e As Stanford University 3 Karabeyoglu Advanced Rocket Propulsion Derivation of the Static Thrust Expression • Second Integral: – Assumption 3: No body forces on the working gas – Momentum equation: u :Velocity Vector ∂ρ u + ∇⋅(ρ uu + PI −τ )= 0 ρ : Density ∂t – Assumption 4: quasi-steady operation – Define control volume (cv) as volume covered by Ac+Ae – Assumption 5: cv is constant in time – Integral of the momentum eq. over the cv ∫∇⋅(ρ uu + PI −τ ) dv = 0 cv Stanford University 4 Karabeyoglu Advanced Rocket Propulsion Derivation of the Static Thrust Expression • Second Integral: – Use Gauss’s Theorem to obtain ∫(ρ uu + PI −τ ) ⋅nˆ dA + ∫(ρ uu + PI −τ ) ⋅nˆ dA = 0 Ac Ae – With use of the no slip condition, this equation takes the following form in the x-direction ˆ 2 PI nˆ d A u 2 A P A PI −τ ⋅ n d A + ρeue Ae + Pe Ae = 0 ⇒ ( −τ ) ⋅ x = −ρe e e − e e ∫ ( ) x ∫ A Ac c – We have used the following assumptions • Assumption 6: Quasi 1D flow at the nozzle exit. Higher order averaging terms are ignored. Velocity parallel to x-axis at the exit plane • Assumption 7: τ ⋅nˆ d A ≅ 0 ∫ x Ae • Average quantities have been introduced at the exit plane d A P ≡ P d A ue ≡ u ⋅nˆ d A ρe ≡ ρ x e ∫ x ∫ x ∫ A Ae Ae e Stanford University 5 Karabeyoglu Advanced Rocket Propulsion Derivation of the Static Thrust Expression • Combined to obtain the thrust force 2 m! : Mass Flow Rate T = ρeue Ae + (Pe − Pa )Ae • Introduce the mass flow rate: m! = ρeue Ae T = m! ue + (Pe − Pa )Ae • Two terms can be combined by introducing the effective exhaust velocity, Ve T = m! Ve • Maximum thrust for unit mass flow rate requires – High exit velocity – High exit pressure • This cannot be realized. Compromise -> optimal expansion Stanford University 6 Karabeyoglu Advanced Rocket Propulsion Convergent Divergent Nozzle Design Issues Pt2 :Chamber Stagnation Pr essure P*: Pr essure @ M 1 = Stanford University 7 Karabeyoglu Advanced Rocket Propulsion Convergent Divergent Nozzle Design Issues • For isentropic flow - perfect gas-no chemical rxns 1. Mass flow rate relation for chocked flow Tt 2 :Chamber Stagnation Temperature 1 2 ⎡ γ +1 ⎤ R :Gas Cons. A P ⎛ 2 ⎞γ −1 m t t2 ⎢ ⎥ R :Universal Gas Cons. ! = ⎢γ ⎜ ⎟ ⎥ u RTt2 ⎝ γ +1⎠ ⎣⎢ ⎦⎥ 2. Area relation (Nozzle area ratio-pressure ratio relation) 1 1 1 ⎧ ⎡ γ −1 ⎤⎫2 1 At ⎛ γ +1⎞γ −1⎛ Pe ⎞γ ⎪⎛ γ +1⎞⎢ ⎛ Pe ⎞ γ ⎥⎪ ≡ = ⎜ ⎟ ⎜ ⎟ ⎨⎜ ⎟ 1− ⎜ ⎟ ⎬ Mw: Molecular Weight ε A 2 ⎜ P ⎟ ⎜ γ −1⎟⎢ ⎜ P ⎟ ⎥ e ⎝ ⎠ ⎝ t2 ⎠ ⎪⎝ ⎠⎢ ⎝ t2 ⎠ ⎥⎪ A : Nozzle Throat Area ⎩ ⎣ ⎦⎭ t ε : Nozzle Area Ratio 3. Velocity relation 1 ⎧ ⎡ γ −1 ⎤⎫2 γ : Ratio of Specific Heats ⎪ 2γ RuTt2 ⎢ ⎛ Pe ⎞ γ ⎥⎪ ue = ⎨ 1− ⎜ ⎟ ⎬ γ −1 M ⎢ ⎜ P ⎟ ⎥ ⎪ w ⎢ ⎝ t2 ⎠ ⎥⎪ ⎩ ⎣ ⎦⎭ • Solve for pressure ratio from 2 and evaluate the velocity using 3. Stanford University 8 Karabeyoglu Advanced Rocket Propulsion Maximum Thrust Condition • Thrust equation: T = m! ue + (Pe − Pa )Ae • At fixed flow rate, chamber and atmospheric pressures, the variation in thrust can be written as dT = m! due + (Pe − Pa )dAe + Ae dPe • Momentum equation in 1D Aρ u du + AdP = 0 m! du = −AdP • Substitute in the differential expression for thrust dT dT = (Pe − Pa )dAe = (Pe − Pa ) dAe • Maximum thrust is obtained for a perfectly expanded nozzle Pe = Pa Stanford University 9 Karabeyoglu Advanced Rocket Propulsion Other Nozzle Design Issues A) Equilibrium: – Mechanical: – Needed to define an equilibrium pressure – Very fast compared to the other time scales – Thermal: – Relaxation times associated with the internal degrees freedom of the gas – Rotational relaxation time is fast compared to the other times – Vibrational relaxation time is slow compare to the rotational. Can be important in rocket applications. – Calorically perfect gas assumption breaks down. – Chemical: – Finite time chemical kinetics (changing temperature and pressure) – Three cases are commonly considered: – Fast kinetics relative to residence time- Shifting equilibrium (Chemical composition of the gases match the local equilibrium determined by the local pressure and temperature in the nozzle) – Slow kinetics relative to residence time- Frozen equilibrium (Chemical composition of the gases is assumed to be fixed) – Nonequilibrium kinetics (Nozzle flow equations are solved simultaneously with the chemical kinetics equations) Stanford University 10 Karabeyoglu Advanced Rocket Propulsion Other Nozzle Design Issues B) Calorically perfect gas – Typically not valid. Chemical composition shifts, temperature changes and vibrational non-equilibrium. C) Effects of Friction – Favorable pressure gradient unless shock waves are located inside the nozzle. – The effects can be list as • Nozzle area distribution changes due to displacement layer thickness • Direct effect of the skin friction force • Shock boundary layer interaction-shock induced separation. • Viscous effects are small and generally ignored for shock free nozzles D) Multi Phase Flow Losses E) Effects of 3D flow field – Velocity at the exit plane is not parallel to the nozzle axis, because of the conical flow field. Stanford University 11 Karabeyoglu Advanced Rocket Propulsion Other Nozzle Design Issues – Types of nozzle geometries • Conical nozzle – Simple design and construction – Typical divergence angle 15 degrees (~2% Isp loss) – 3D thrust correction can be significant 1+ cos(α ) T = m! u + (P − P )A e 2 e a e α : Nozzle Cone Angle • Perfect nozzle – Method of characteristics to minimize 3D losses – Perfect nozzle is too long • Optimum nozzle (Bell shaped nozzles) – Balance length/weight with the 3D flow losses • Plug nozzle and Aerospike nozzle – Good performance over a wide range of back pressures Stanford University 12 Karabeyoglu Advanced Rocket Propulsion Optimum Bell Nozzle - Example Stanford University 13 Karabeyoglu Advanced Rocket Propulsion Plug and Aerospike Nozzles Stanford University 14 Karabeyoglu Advanced Rocket Propulsion Definitions-Thrust Coefficient • Thrust equation: T = m! ue + (Pe − Pa )Ae • Thrust coefficient: T m! ue ⎛ Pe Pa ⎞ Ae CF ≡ = + ⎜ − ⎟ At Pt2 At Pt2 ⎝ Pt2 Pt2 ⎠ At • For isentropic flow and calorically perfect gas in the nozzle the thrust coefficient can be written as 1 ⎧ γ +1 γ −1 ⎫2 2 ⎡ ⎤ ⎪⎛ 2γ ⎞⎛ 2 ⎞γ −1 ⎢ ⎛ Pe ⎞ γ ⎥⎪ ⎛ Pe Pa ⎞ Ae CF = ⎨⎜ ⎟⎜ ⎟ 1− ⎜ ⎟ ⎬ + ⎜ − ⎟ ⎜ γ −1⎟⎜ γ +1⎟ ⎢ ⎜ P ⎟ ⎥ ⎜ P P ⎟ A ⎪⎝ ⎠⎝ ⎠ ⎢ ⎝ t2 ⎠ ⎥⎪ ⎝ t2 t2 ⎠ t ⎩ ⎣ ⎦⎭ Stanford University 15 Karabeyoglu Advanced Rocket Propulsion Definitions - c* Equation • Mass flow equation (choked and isentropic flow of a calorically perfect gas in the convergent section of the nozzle): 1 2 ⎡ γ +1 ⎤ At Pt2 ⎢ ⎛ 2 ⎞γ −1 ⎥ m! = ⎢γ ⎜ ⎟ ⎥ RTt2 ⎝ γ +1⎠ ⎣⎢ ⎦⎥ • Definition of c*: P A c* ≡ t2 t m! • c* can be expressed in terms of the operational parameters as 1 2 ⎡ γ +1 ⎤ ⎢1 ⎛γ +1⎞γ −1 RuTt2 ⎥ c* = ⎜ ⎟ ⎢γ ⎝ 2 ⎠ M w ⎥ ⎣⎢ ⎦⎥ Stanford University 16 Karabeyoglu Advanced Rocket Propulsion Definitions – Specific Impulse and Impulse density • Combine the definitions of the thrust coefficient and c* to express the thrust T = m! c*CF Energy of the gases Flow in the nozzle In the chamber • Think of nozzle as a thrust amplifier and CF as the gain • Specific Impulse: Thrust per unit mass expelled T c*C go :Gravitational Cons. on Earth I ≡ = F sp ρ : Pr opellant Density m! go go p • Impulse Density: Thrust per unit volume of propellant expelled T T m! go ! m! Vp ≡ δ ≡ = = Ispρ p ρ p V!p m! go V!p Stanford University 17 Karabeyoglu Advanced Rocket Propulsion Definitions – Total Impulse, Average Thrust, Delivered Isp • The total impulse is defined as tb tb Itot ≡ ∫Tdt = ∫ m! Ispgodt 0 0 • Average thrust tb 1 I tb :Total Burn Time T ≡ Tdt = tot M :Total Pr opellant Mass tb ∫ tb p 0 • Delivered Isp I I tot ( sp )del = M p go Stanford University 18 Karabeyoglu Advanced Rocket Propulsion Thrust Coefficient Curves (from Sutton) γ =1.2 Pt2 Pa → ∞ Burn out P P Underexpanded t2 a Pe = Pa Lift off Overexpanded Pt2 Pa = Stanford University 19 Karabeyoglu Advanced Rocket Propulsion Observations on the Thrust Coefficient Curves • For the specific value of γ =1.2 • CF varies from 0.75 to 2.246 – Assuming chocked flow – CF is order 1 • For the case of convergent nozzle ε =1 – For P t 2 P a < 2 .3 subsonic flow in the nozzle – CF varies from 0.75 (optimal) to 1.25 • For convergent divergent nozzles ε >1 – For a given pressure ratio P t 2 P a there exists an optimum area ratio that maximizes the thrust coefficient – Right of the optimum is overexpanded • Shock structure is initially outside the nozzle • For larger area ratios shock moves inside the nozzle and the boundary separation takes place • This has a positive impact on the CF Stanford University 20 Karabeyoglu Advanced Rocket Propulsion Observations on the Thrust Coefficient Curves – Left of the optimal is underexpanded • No separation in this case • Optimal area ratio increases with increasing pressure ratio – Upper stages have large nozzle area ratios (i.e.70) – Booster stages have low area ratios (i.e.
Details
-
File Typepdf
-
Upload Time-
-
Content LanguagesEnglish
-
Upload UserAnonymous/Not logged-in
-
File Pages22 Page
-
File Size-