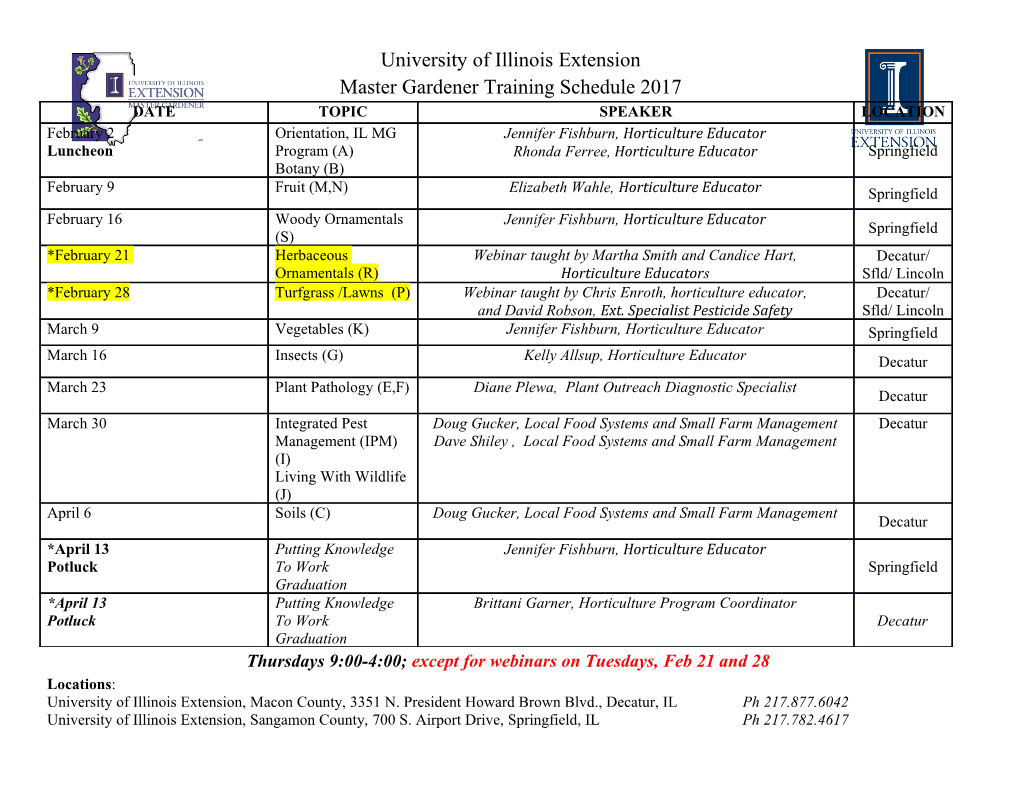
Reactor technologies Metso Outotec has a long history of achievements as a Benefits hydrometallurgical technology provider. The reactor lies at the • Case-proven metallurgical superiority core of high quality leaching, precipitation and metal recovery. • Flexible and reliable operation Metso Outotec’s OKTOP® Reactor Family presents a tailored • High availability solution for customers’ process requirements and needs, with • Easy and safe maintenance respect to various metals such as copper, zinc, nickel, and • Optimized solution for minimized lifetime costs precious and special metals. Selecting the right OKTOP Reactor begins from the process. Due to our unrivalled process and equipment know-how and numerous implementation projects, we know what types of reactors work well in industry, and how to reliably scale laboratory tests up to industrial size. Through a combination of an optimized process and Metso Outotec reactors, we can guarantee you the best lifetime value, maximized metallurgical results and secure operations. Metso Outotec philosophy Metso Outotec has been building reactors for various hydrometallurgical applications for four decades. We have experience not only as a technology provider but also based on running reactors at our own plants. Our installation base includes hundreds of reactors for leaching, precipitation and metal recovery purposes. Metso Outotec reactor solutions have always been aimed at optimizing metallurgical results, securing operations and best lifetime value. We know that every plant and process is unique, with varying requirements. Due to the integrated nature of the process and reactor, each OKTOP Reactor is designed for a specific purpose. Modular and tailored reactor design For us, a reactor is far more than a tank. Metso Outotec will provide you with the complete OKTOP Reactor delivery package, enabling you to choose the accessories you need. Advanced modularity also lies at the core of OKTOP Reactor design. Our high volume of reactor installations and long-term research work has allowed us to optimize each design element. The reliable scalability criterion of OKTOP modules has been achieved through decades of continuous development. The vast process know-how is used to choose the optimized reactor solution based on the aforementioned industrially proven elements and modular design enables us to tailor reactors quickly and efficiently to your needs. The reactor design procedure and computer aided design tools OKTOP Reactor – ensure design quality. the complete solution for your process needs Maximized metallurgical results + Secure operations = Best lifetime value Precipitation, solution purification and metal recovery the process result that makes the difference. In leaching, the reactors leaching rate and recovery rule the economics. The selection The optimization of precipitation reactors is not as of a reactor solution is performed based on factors limiting straightforward as for leaching reactors: in most cases, no the leaching rate, typically chemical reaction, gas dissolution single economical criterion predominates. Furthermore, or particle diffusion. Metso Outotec’s hydrometallurgical many of the economical drivers involved are difficult to process portfolio contains processes falling into each measure directly in laboratory tests. In the compromise category of rate limiting factor. While some basic Metso between different design criteria, the key issue relating to the Outotec approaches are applied, achieving an economically precipitation process, in identifying the financially optimum optimum solution usually requires a tailored reactor design. solution, lies in converting mass transfer phenomena into Years of research experience have established a formula for measurable quantities linked to process targets, such as an iterative research cycle defining the design criterion for productivity, operability and sludge quality. In practice, the optimal leach reactor lifetime costs. Metso Outotec design often aims at a high precipitation rate, Secure operations via high design quality and unique which reduces the number of reactors required. In addition, solutions tailor-made OKTOP Reactors guarantee the high quality of the precipitate. All OKTOP Reactors enable one-piece removal of the agitator. The replacement time is thereby reduced to half an Leaching reactors hour. Adjustable overflow well in an OKTOP Reactor. The new The initial investment has a very low impact on the lifetime overflow well design secures operation by eliminating the cost of a typical reactor in a hydrometallurgical plant: it is number of vulnerable extra nozzles. Metso Outotec reactor concept: • Integration of process design, automation and equipment • Tailored to customer’s needs and raw materials • Outstanding scale-up characteristics due to modular delivery package and design elements • Fast track equipment development for novel metallurgical process solutions OKTOP Reactor Family OKTOP Reactors have been successfully applied in treating solid-liquid, gas-liquid, gas-liquid-solid and liquid-liquid systems for leaching, precipitation, crystallization, oxidation, reduction and solvent extraction. Process requirements are met by configuring reactor design elements such as the agitator, tank design and baffles. Decades of experimental, design and operational activities have resulted in a large number of separate reactor solutions as well as proven design elements and principles, which have now been launched as the generally applicable OKTOP Reactor Series. In most cases, a proven reactor solution can be selected for a given processing task. In very demanding cases, however, we use more specific design approaches based on fluid dynamical analysis, and develop the individual reactor solution you require. OKTOP Reactor design begins with the determination of the process parameters. The unique design cycle, including physical modeling, leaching and precipitation tests, fluid dynamical analysis, computational mechanical design and life cycle analysis, enables us to provide an unmatched solution. OKTOP Reactor 1000 Series OKTOP Reactor 1000 Series Agitator type: Multipurpose. Agitation intensity: Moderate. Macro and micro agitation: Good compromise between micro and micro. Case example: Iron removal, Zhuzhou Smelter Group, Benefits: Very wide application China, 2008 rage due to high configurability and Zhuzhou Zinc Smelter expanded its operations through direct leaching and solution purification processes designed infallible functioning. by Metso Outotec. A hydrometallurgical zinc process requires an iron outlet in order to control the iron concentration in Selected when: Process results gained through moderate agitation. the process solution. Zhuzhou iron removal is based on goethite precipitation. The drivers for process optimization are Process example: Iron precipitation is an iron content in the iron precipitate, oxygen efficiency and the total volume of the built reactor capacity. An optimization example of highly configured function was defined for each driver in laboratory tests. The flexibility of series 1000 allowed an impeller configuration, OKTOP 1000. simultaneously obtaining a clear maximum for each driver. Metso Outotec provided the total solution, with both Economic driver to Number of references and customer: secured functioning. process and equipment guarantees. • Multipurpose agitator • Moderate agitation intensity • Good compromise between macro and micro agitation • Very wide application range due to high configurability and infallible functioning • Selected when process results are gained through moderate agitation • Number of references and secured functions economic drivers to customer OKTOP Reactor 2000 Series OKTOP Reactor 2000 Series Agitator type: Gas-liquid-solid. Agitation intensity: High. Macro and micro agitation: Micro generally higher than macro when compared to Case example: Nickel matte leaching, Norilsk Nickel Harjavalta, Finland, 1995 1000 Series. Benefits: High gas hold-up including Following the expansion and refurbishment of the Harjavalta nickel plant, its leaching reactors were replaced by new increased gas retention time, technology. The initial reason for the replacement of the old Pachuca type reactors was that they provided no control excellent gas dispersion and dissolution, abrasive mixing. over the leaching rate or oxygen consumption. The new OKTOP 2000 Reactors were designed to fulfill challenging Selected when: Gas dispersion rate is the dispersion duties in three phase, gas-liquid-solid, conditions, and the new approach enabled the optimal adjustment liming factor of the reaction rate. of the leaching rate and oxygen consumption for different feed rates by gas flow rate and impeller rotation speed. A Process example: Iron oxidation, lean H2S positive side effect of using a series 2000 reactor was the reduction in the average nickel content of the leach residue precipitation, nickel matte leaching. by 50%. Another impressive improvement was achieved in iron removal efficiency, and the suppression of hydrogen Economic driver to Smaller reactors possible gas liberation regarding the electric furnace matte. customer: due to high gas utilization rate. • Gas-liquid-solid agitator • High agitation intensity, especially in bottom region • Micro agitation generally higher than in 1000 series • High gas hold-up including increased gas retention time, excellent gas dispersion and dissolution, abrasive mixing • Selected when the gas dispersion rate is the limiting factor
Details
-
File Typepdf
-
Upload Time-
-
Content LanguagesEnglish
-
Upload UserAnonymous/Not logged-in
-
File Pages12 Page
-
File Size-