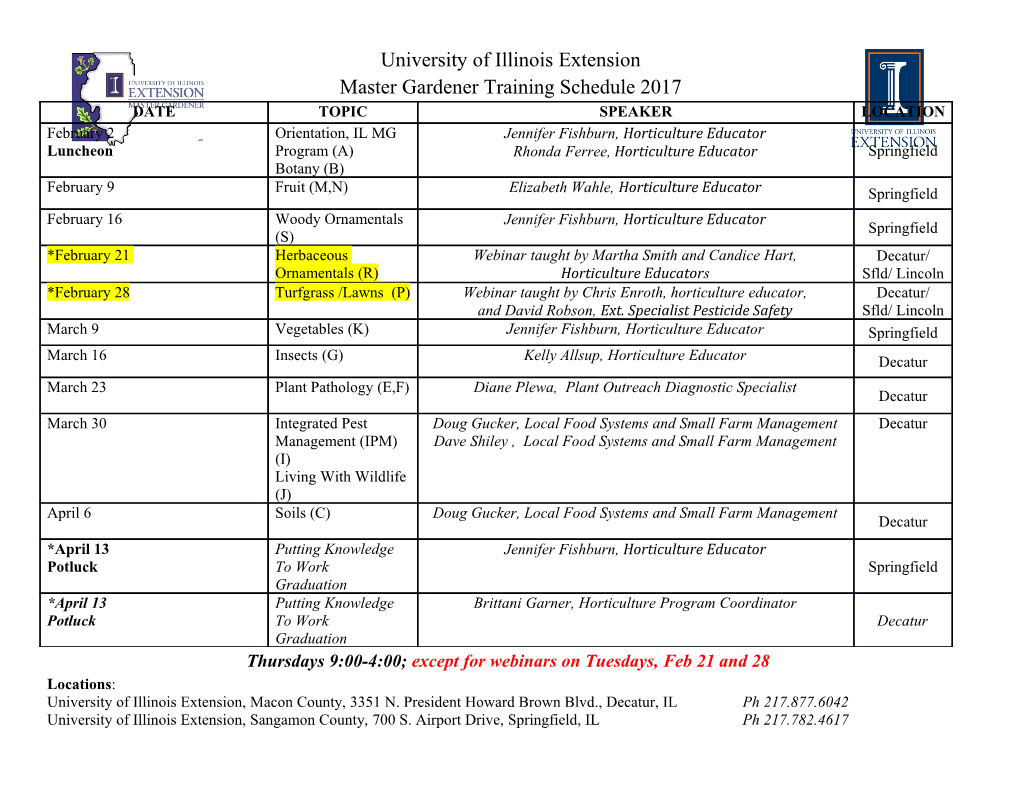
RSC Advances View Article Online PAPER View Journal | View Issue Patterning order and disorder with an angle: modeling single-layer dual-phase nematic Cite this: RSC Adv.,2019,9, 8994 elastomer ribbons† Vianney Gimenez-Pinto ‡*ab and Fangfu Yeacd Liquid crystal polymer networks have demonstrated a rich variety of actuation behavior and stimulus- responsive properties. Actuation in these single-phase materials is given by spatial variations in their liquid crystal director microstructure in balanced coexistence with rubber elasticity. However, experimental studies have shown that complex actuation in elastomeric materials can also be engineered by combining well-defined isotropic regions along with liquid crystalline ordered regions. Via finite element elastodynamics simulations, we investigate the actuation behavior of these dual-phase nematic elastomer ribbons based on several key design factors: director orientation, pattern orientation, Received 13th November 2018 as well as domain and sample size. We demonstrate the variety of shapes that these materials can Accepted 12th February 2019 Creative Commons Attribution 3.0 Unported Licence. exhibit, including twisting, bending, accordion folding, and hybrid flat-helix states. Overall, our DOI: 10.1039/c8ra09375j simulations show an exceptional agreement with experimental observations, providing light for the rsc.li/rsc-advances further development of soft stimulus-responsive materials with complex microstructures. Liquid crystal polymer networks are hybrid materials that deformation. A non-uniform director microstructure produces encode complex shape transformation and stimulus-responsive a non-uniform distribution of strains under external stimulus, capabilities given the coexistence of liquid crystalline order and driving then complex actuation. a crosslinked polymer network with characteristic rubber-like Nonetheless, additional design approaches can be imple- This article is licensed under a elasticity. By engineering complex microstructures in the mented towards engineering complex spatial distribution of nematic director eld, complex shape actuation under external inner strains in the material and, as a result, complex actuation stimulus can be custom-designed in these materials. A wide under external-stimuli. Recently, Liu et al.16 synthetized single- Open Access Article. Published on 18 March 2019. Downloaded 9/26/2021 9:08:47 PM. variety of nematic director patterns in delicate combination layer dual-phase thin- lm elastomer actuators, which inge- with the elastic response, have demonstrated an exquisite niously combine well-dened isotropic regions and twist- repertoire of shapes, including the formation of cones,1 pyra- nematic liquid crystalline regions. Yang and Zhao17 also ach- mids where Gaussian curvature is suppressed by in-plane vari- ieved synthetizing single-layer hybrid elastomer samples within ations of the director,2 chiral helicoids and elastic springs,3–8 their studies implementing non-uniform optical inscription of foldable actuators,6,9–13 and other complex bio-inspired isotropic–liquid crystalline patterns. Furthermore, Katsonis and morphologies.14,15 The vast majority of these single-phase coworkers18 recently developed elastomer lms with stripes of designs are based on spatial variations of the nematic director isotropic and liquid crystal domains and implemented them for eld within the sample. When external stimuli such as light, the study of high-power light-driven actuation in paired chiral temperature change, variation in chemical environment, etc. ribbons. Similarly to single-phase liquid crystal elastomers, change the liquid crystalline order parameter, inner strains these dual-phase materials can display a variety of out of plane arise in the material and produce a macroscopic shape actuation behavior covering chiral twisting and bending, as well as the formation of accordion folds. Here, actuation is encoded aBeijing National Laboratory for Condensed Matter Physics, CAS Key Laboratory of within the nematic director microstructure coexisting in So Matter Physics, Institute of Physics, Chinese Academy of Sciences, Beijing combination with the over-imposed in-plane isotropic pattern. 100190, China. E-mail: [email protected] Combining order and disorder in the microstructure of bDepartment of Chemical Engineering, Columbia University, USA liquid crystal elastomers has also been implemented in bi-layer c School of Physical Sciences, University of Chinese Academy of Sciences, Beijing dual-phase materials within the past 15 years. Ikeda and 100049, China coworkers19 rst introduced photo-responsive dual-phase dSongshan-Lake Materials Laboratory, Dongguan 523808, China † Electronic supplementary information (ESI) available. See DOI: bilayer elastomers with one isotropic layer and an anisotropic 20 10.1039/c8ra09375j smectic layer. Also, Dai et al. synthetized humidity-responsive ‡ Current addresses: Department of Physics and Astronomy, University of dual-layer elastomers with an isotropic layer in coexistence with Pennsylvania and Department of Physics, Temple University. 8994 | RSC Adv.,2019,9, 8994–9000 This journal is © The Royal Society of Chemistry 2019 View Article Online Paper RSC Advances a nematic layer with splay conguration. In both cases, the materials. Our study shows that dual phase elastomer ribbons stacked arrangement of one isotropic and one liquid crystalline can exhibit similar actuation to their single-phase counterparts, layer added mechanical strength to the sample, avoiding frac- or a modied deformation by the inuence of inactive isotropic ture and cracking. We note that these mechanically reinforced domains, depending on their size relative to sample size. bi-layer dual-phase strips arrange order and disorder along In materials with a striped isotropic–nematic pattern, sample thickness. Conversely, single-layer dual-phase materials narrow inactive isotropic stripes do not distort overall implement in-plane order–disorder patterns, allowing further morphology aer actuation, and only changes in the magnitude options for design parameters towards engineering complex of the actuation and stimulus response are observed. Wider actuation, such as signicant variations in the size of isotropic isotropic stripes can distort and/or isolate the effect of their regions as well as the use of in-plane angles in the material adjacent active nematic regions affecting overall out-of-plane microstructure. actuation. In these later cases, we observe at inactive regions In this work, we perform nite-element elastodynamics in coexistence with active morphing regions. Wide-stripe simulations for investigating the actuation of these novel single- samples exhibit distorted-bending, distorted-twisting, accor- layer dual-phase materials given their order–disorder patterned dion folds and hybrid twist-at morphologies depending on microstructure as well as director conguration in the nematic stripe width and angular offset. Our simulation study sheds regions. This numerical method had successfully demonstrated light on the different morphologies reported by experimental a wide variety of in-plane and out-of-plane actuation behavior in groups that previously synthetized these materials, and give single-phase nematic elastomers including chiral bending,8 insights on the key design factors for engineering actuation in twisting,8,22 cone and anti-cone (saddle) formation,21 accordion smart materials by patterning order and disorder with an angle. folds,9 origami boxes,11 and bas-relief designs,21 given by Methods: We implement nite element elastodynamics different complex director microstructures. Also, nite element simulations as developed by Selinger and coworkers.23 For this, elastodynamics has been implemented for studying the actua- each three-dimensional sample is discretized to an unstruc- 22 24 Creative Commons Attribution 3.0 Unported Licence. tion of smectic elastomers. However, until now there is no tured tetrahedral mesh with an open source CAD so ware. record of this approach being implemented for the study of The system is described via the Hamiltonian dual-phase patterned elastic solids. More importantly, given the 1 X 1 X H ¼ m n 2 þ V tC t3 t3 t freshness of single-layer experimental realizations, the current 2 n n 2 ijkl ij kl n t literature still lacks theoretical and numerical studies for these novel dual-phase rubbery materials. X Àa0 V t3 t Q t À Q t Here, we focus on single-layer dual-phase elastomers with ij ij ij;flat t a 90 degree twist-nematic conguration in the nematic region, analyze the effect of a varying offset angle in director macro- where implementing the Green-Lagrange non-linear strain This article is licensed under a 3 ¼ v v v v structure as well as a varying offset angle in the orientation of tensor ij iuj + jui + iuk juk allows large deformations. Cijkl the isotropic pattern. Overall, we demonstrate the different corresponds with the elastic stiffness tensor of an isotropic ¼ cases and geometries where curling, folding, bending and elastic solid (rubber). Coupling between nematic order, Qij Shn n À d/3i and strain 3 is given by the term a(Q À Qref) Open Access Article. Published on 18 March 2019. Downloaded 9/26/2021 9:08:47 PM. accordion-like folds appear under external stimulus in these i j ij ij ij Fig. 1 Schematics of dual-phase nematic actuators: white regions have nematic order with 90 degree twist between top and bottom substrates. Grey regions correspond with isotropic states. In the fabrication of these
Details
-
File Typepdf
-
Upload Time-
-
Content LanguagesEnglish
-
Upload UserAnonymous/Not logged-in
-
File Pages7 Page
-
File Size-