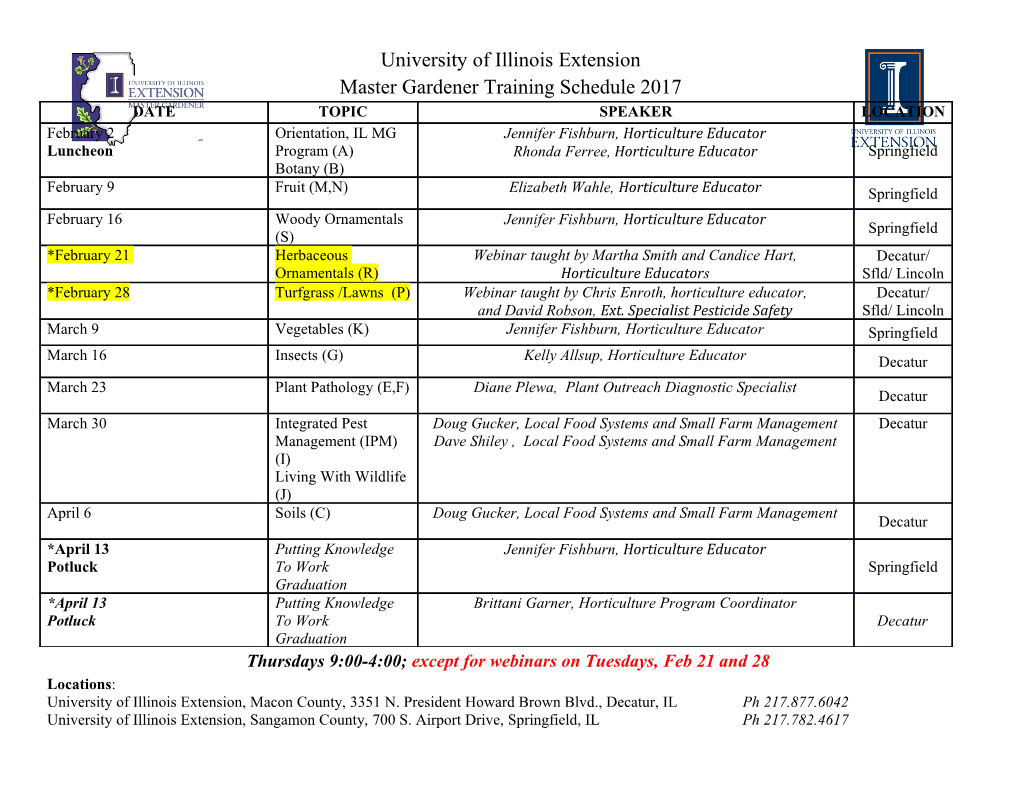
metals Article Mathematical Modeling of Postcombustion in an Electric Arc Furnace (EAF) Niloofar Arzpeyma *, Mikael Ersson and Pär G. Jönsson Department of Materials Science and Engineering, Royal Institute of Technology (KTH), Stockholm 100 44, Sweden; [email protected] (M.E.); [email protected] (P.G.J.) * Correspondence: [email protected] Received: 4 April 2019; Accepted: 7 May 2019; Published: 10 May 2019 Abstract: Numerical modeling was used to study the capability of postcombustion in an electric arc furnace (EAF) equipped with virtual lance burners. The CO flow rate at the molten bath surface was estimated using the off-gas data obtained close to the outlet of an EAF. Then, the effect of the secondary oxygen flow rate on postcombustion was studied. The results show a CO flow rate of 0.6 kg s 1 and · − 0.8 kg s 1 for operation modes of burner and burner + lancing. Increase of the secondary oxygen · − flow rates of 60% and 70% result in 17% and 7% increase in the postcombustion ratio (PCR) for the burner and burner lancing modes, respectively. Keywords: EAF; postcombustion; CFD 1. Introduction The high amount of carbon monoxide produced in an electric arc furnace (EAF) is an important source of chemical energy. The heat generated by postcombustion (PC) of CO can be captured by scrap. This contributes to a reduction of the electrical energy in an EAF. The PC process can be applied effectively in EAFs by using PC systems designed as supersonic oxygen injectors embedded in the furnace walls [1–5]. The supersonic jets result in an increased gas penetration into the melt compared to the subsonic ones which is caused by a high dynamic pressure. However, superstoichiometric ratios of oxygen to fuel in burners can also improve the PC efficiency [5]. Li and Fruehan [2] used computational fluid dynamics (CFD) to study the effect of PC on the heat generation in an EAF equipped with four PC injectors. The de-PC reaction, due to the reaction of CO2 with carbon in the melt and the electrode surfaces, was included in the model. Their results showed that the heat transfer efficiency is lower for a flat bath condition than for a bath containing a scrap pile. Besides, de-PC reduces the amount of CO2 and as a result, less chemical energy is available in the furnace. Januard et al. [3] studied PC optimization in an industrial furnace equipped with a PC injector tool. They used a dynamic control and set points to control the oxygen injectors. The amount of CO and CO2 was monitored continuously using near infrared (IR) laser diode spectroscopy during the furnace operation. A high concentration of CO2 was observed during the refining stage during the foaming slag formation. Zhonghua et al. [4] also developed a CFD model to study PC in an EAF. The reaction rate was determined based on both temperature and turbulence data. They showed that when using multiple top PC injectors and oxygen, an excess ratio can improve the PC efficiency. Thomson et al. [5] studied the effect of the burner oxygen to fuel ratio on the energy efficiency of an EAF using the data from off-gas determinations. The electrical energy consumption and tap-to-tap time was reduced due to a higher burner oxygen to fuel ratio. Chan et al. [6] focused on the formation of NOx due to the air ingress from the slag door using a CFD model. Reduced CO and H2 levels due to a generation of NO were observed. They also Metals 2019, 9, 547; doi:10.3390/met9050547 www.mdpi.com/journal/metals Metals 2019, 9, 547 2 of 14 showed that an additional oxygen injection through the burners increases the furnace temperature representative for PC reactions. MetalsThe 2019 EAF, 9, x FOR modelled PEER REVIEW in this study represents an existing furnace equipped with a virtual2 of 14 lance burnerThe (VLB) EAF system.modelled The in VLBthis study system represents is a compact an existing injection furnace tool whichequipped operates with a in virtual the three lance main modesburner of (VLB) (i) burner, system. (ii) The burner VLB+ systemlancing, is a and compact (iii) lancing. injection It consiststool which of threeoperates inlets in tothe supply three main the main oxygen,modes of secondary (i) burner, oxygen, (ii) burner and + fuel.lancing, Melting and (iii) of scraplancing. and It heatingconsists upof three the cold inlets zones to supply inside the the main furnace startsoxygen, in thesecondary burner mode,oxygen, and and refining fuel. Melting starts in of the scrap burner and+ heatinglancing up mode the bycold increasing zones inside the flow the rate offurnace oxygen starts from in the the main burner nozzle. mode, Previous and refining studies star showedts in the thatburner the + power-on lancing mode time by and increasing electrical the energy isflow reduced rate of in oxygen EAFs usingfrom VLBthe main systems nozzle. [7, 8Previous]. Figure studies1a shows showed the geometry that the power-on of the fluid time inside and the modelledelectrical energy VLB. The is reduced inlets and in outletsEAFs using for oxygen VLB sy andstems fuel [7,8]. are Figure shown 1a at sh theows left the and geometry right sides of the of the figure,fluid inside respectively. the modelled VLB. The inlets and outlets for oxygen and fuel are shown at the left and right sides of the figure, respectively. (a) (b) Figure 1. (a) The virtual lance burner (VLB) domain; right: front view of the outlet and left: side view; Figure 1. (a) The virtual lance burner (VLB) domain; right: front view of the outlet and left: side view; (b) the whole computation domain of the electric arc furnace (EAF) model. (b) the whole computation domain of the electric arc furnace (EAF) model. A summaryTable of previous 1. Summary CFD of previous models computational studying combustion fluid dynamics in EAF (CFD) is shownmodels. in Table1. In these Combustion Off-gas CFDRef., Date models, CFD the Model combustion Dim source wasReactions oxygen injectorsPredictions installed for the PC, while in thisDomain study, a CFD model is developed to study the influence of the VLB efficiency on theSource PC in anData EAF. This is done PC of CO Temperature profile Chemical-reaction byLi et adjusting al., the secondary oxygenDissociation flow rate toof increaseMass transfer PC. of CO, Oxygen Whole Species 3D Y 2003 [3] CO2 O2 and CO2 injectors furnace Radiation Table 1. Summary of previousde-PC computationalRadiation fluid dynamics (CFD) models. Combustion of Chan et Temperature profile Burner Species * CO, H2, and Combustion Off-Gas Whole al., Ref., Date CFD Model3D Dim ReactionsMass transfer Predictions of NO, Oxygen Y Domain Radiation CH4 and NO Source Data furnace 2004 [6] CO and O2 lancing formationPC of CO Temperature profile Chemical-reaction Li et al., Dissociation of Mass transfer of CO, Oxygen Whole Zhonghua Species 3D Y 2003 [3] Species * CombustionCO of Mass transferO and of COCO Oxygeninjectors furnaceWhole et al., Radiation 3D 2 2 2 N Radiation CO de-PC andRadiation O2 injectors furnace 2009 [4] Combustion of TemperatureTemperature profile profile Burner Chan et al., Species * CO, H , and Secondary Whole Current Species * 3D Combustion of2 Mass transferMass transfer of CO, of Oxygen Y Whole 2004 [6] Radiation 3D CH4 and NO oxygen of the Y furnace work Radiation CO, H2 and CH4 O2 NO,and CO2 and O lancing furnace formation 2 burner Zhonghua et al., Species * Combustion of Mass transfer of CO Oxygen Whole 3D N * Eddy2009 [4dissipation] Radiation model (EDM) for turbulent mixingCO and finiteand rate O2 mode (FRM)injectors for chemical kinetics.furnace Temperature profile Secondary A summary of Speciesprevious * CFD modelsCombustion studying ofcombustion in EAF is shown in Table 1. In Wholethese Current work 3D Mass transfer of CO, oxygen of Y Radiation CO, H2 and CH4 furnace CFD models, the combustion source was oxygen injectors installedO2 and CO2 for thethe PC, burner while in this study, a CFD model* Eddy is dissipationdeveloped model to study (EDM) the for turbulentinfluence mixing of th ande VLB finite efficiency rate mode on (FRM) the for PC chemical in an EAF. kinetics. This is done by adjusting the secondary oxygen flow rate to increase PC. 2. Model Description 2.1. Computational Domain Metals 2019, 9, 547 3 of 14 2. Model Description 2.1. Computational Domain The computational domain is the gas phase above the molten bath surface around the electrodes, the fluid inside three VLBs located at the furnace wall and the elbow (Figure1b). The enlarged domain of the fluid inside the VLB is shown in Figure1b. The main oxygen is injected into the furnace through the central nozzle, and six secondary oxygen and six fuel jets are located around the main oxygen nozzle. The main assumptions applied to simplify the model were as follows: A flat molten bath surface • A constant flow rate of CO from the molten bath surface • No generation of NOx inside the furnace • 2.2. Reactions and Governing Equations A steady-state gas flow was modeled by solving the mass, momentum, energy, and species conservation equations. The simplified form of oxy-fuel reaction [9] overpredicts the temperature and concentration of species, but it was applied for simplicity as: CH + 2O CO + 2H O (1) 4 2 ! 2 2 Combustion of CO was assumed to be irreversible: CO + 0.5O CO (2) 2 ! 2 Dissociation reactions for species such as oxygen, water, and carbon dioxide were not taken into account. However, in order to avoid an overestimation of the temperature, a modified heat-specific capacity for each species was applied. The species source term in the species conservation equation was determined using the kinetic rate (Rk) and turbulence mixing rate (Re) which are described below.
Details
-
File Typepdf
-
Upload Time-
-
Content LanguagesEnglish
-
Upload UserAnonymous/Not logged-in
-
File Pages14 Page
-
File Size-