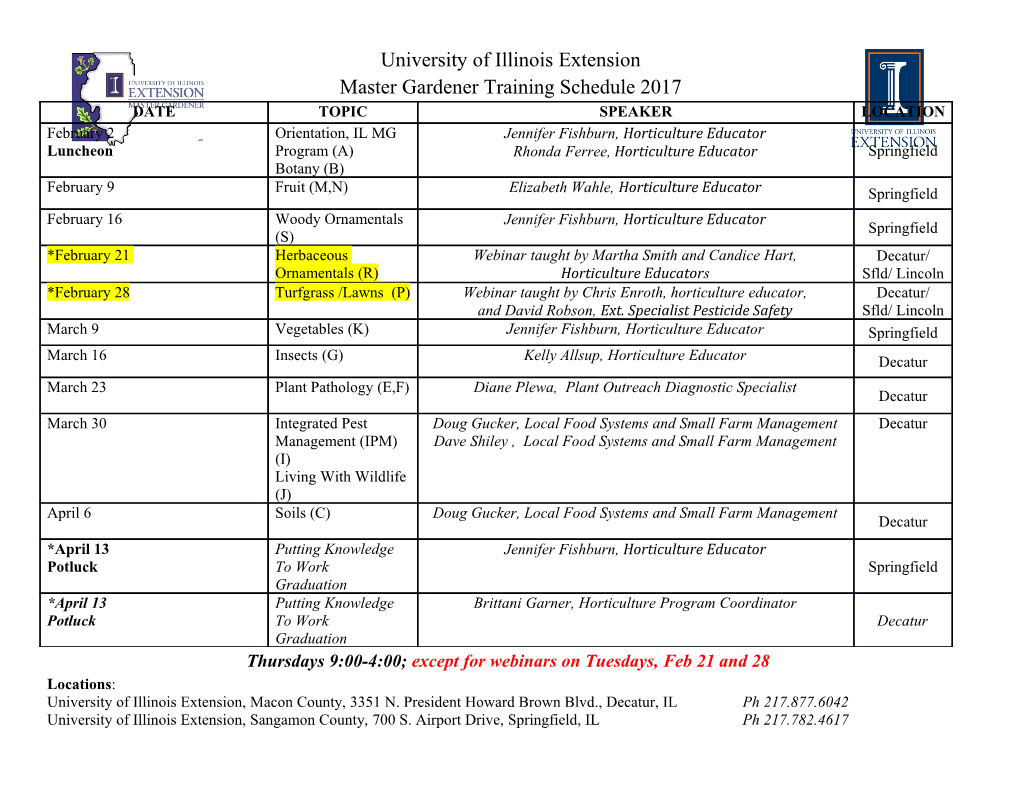
Fluid Dynamic Assessment of Sensor Geometry For Micro System Applications Mohamed Hassan Ph.D. Thesis In The Department of Mechanical and Industrial Engineering Presented in Partial Fulfillment of the Requirements for the Degree of Doctor of Philosophy at Concordia University Montreal, Quebec, Canada September, 2015 © Mohamed Hassan, 2015 CONCORDIA UNIVERSITY School of Graduate Studies This is to certify that the thesis prepared By: Mohamed Hassan Entitled: Fluid Dynamic Assessment of Sensor Geometry for Micro System Applications and submitted in partial fulfillment of the requirements for the degree of Doctor of Philosophy complies with the regulations of the University and meets the accepted standards with respect to originality and quality. Signed by the examining committee: -------------------------------------------------- Dr. (chair) -------------------------------------------------- Dr. Metin Yaras (External Examiner) -------------------------------------------------- Dr. Samuel Li (Ext.-to-Program) -------------------------------------------------- Dr. Hoi Dick Ng (Examiner) -------------------------------------------------- Dr. Ion Stiharu (Examiner) -------------------------------------------------- Dr. Georgios Vatistas (Examiner) -------------------------------------------------- Dr. Wahid Ghaly (Supervisor) Approved by ------------------------------------------------------------------------------------------- Department Chair or Graduate Program Director ----------------2015-------------------------------------------------------------------------------------- Dean, Faculty of Engineering and Computer Science ABSTRACT Fluid Dynamic Assessment of Sensor Geometry for Micro System Applications Mohamed Hassan, PhD. Concordia University, 2015 In this work, the fluid dynamic behaviour around a proposed micro-sensor geometry is assessed. The sensor is intended for use in micro devices and is represented by two cubes (or elements) set in tandem. The flow is described by the Navier-Stokes equations and is solved by Direct Numerical Simulation (DNS) using ANSYS-CFX. Flow visualization using an existing experimental setup is carried out to visualize the flow pattern around the sensor using the soap film technique, where the flow is considered to be two-dimensional incompressible. This visualization is intended to verify the DNS that is carried out for the same cases. Results for the flow pattern and the vortex shedding frequency that are obtained from both numerical simulations and experimental investigations compare favorably, for three different values of Reynolds number, which verifies the numerical approach. A parametric study on the effect of geometry in the limit of 2D incompressible flow of water is carried out. This study shows that the inter-element spacing strongly affects the flow in the inter-element cavity; it also shows that the thickness of the downstream element affects the downstream shear layer. Both of these geometric parameters control the vortex shedding in the wake and the drag coefficient particularly on the downstream element. This parametric study also suggests that a ‘general’ linear correlation between Strouhal and Reynolds numbers (modified to include geometric parameters) is valid for all variables investigated in this work. The DNS of air in the limit of 2D and 3D flow is considered at three subsonic inflow Mach numbers. The flow simulation results are verified against basic flow physics, available experimental data and interpretations of vortex shedding behaviour particularly in 3D flow. For air flow in the 2D limit, the vortex shedding frequency expressed in terms of Roshko number (rather than Strouhal number) correlates well with Reynolds number at iii all Mach numbers. For both 2D and 3D flows, the vortex shedding frequency, flow behavior and drag coefficient compare reasonably well with available experimental data. The drag coefficient and Strouhal number computed from DNS will serve as a first step towards inferring the flow pressure and velocity, when the proposed sensor is built. Hence achieving one of the main goals of this work. iv DEDICATION This thesis is dedicated to my mother, my wife and my children. v ACKNOWLEDGEMENTS First and foremost, all praise be to Allah. I gratefully and sincerely acknowledge the continued support, guidance and encouragement provided over the years by my supervisor Dr. Wahid Ghaly. He spent many hours helping and teaching me during the course of my PhD study at Concordia University. I thank him for all the lessons and precious advice provided throughout the research. I would also like to thank the Egyptian Ministry of Defense for giving me the opportunity to go through my PhD study at Concordia University. Moreover, I would like to thank all members of the MIE department, the faculty and staff for all the support and encouragement (and tolerance) they have shown towards me throughout the years of my tenure at Concordia. Special thanks go to Dr. Mohamed Fayed for his consistent support in carrying out the experimental work. Also great thanks to Dr. Vatistas and Dr. Ng for letting me use the lab and the instruments. I would also like to thank my colleagues for having a good working environment and providing me with valuable assistance, encouragement and friendship; in particular, Raja Ramamurthy. Finally, the ultimate acknowledgement is to my parents, my wife, my children and my sisters for their continuous and unending love, prayer and support. vi TABLE OF CONTENTS LIST OF FIGURES .......................................................................................................... x LIST OF TABLES ......................................................................................................... xiv LIST OF SYMBOLS ...................................................................................................... xv Chapter 1 INTRODUCTION AND LITERATURE REVIEW.................................... 1 1.1 Introduction ............................................................................................................................ 1 1.1.1 Sensor applications ......................................................................................................... 1 1.1.2 Background of velocity sensing ...................................................................................... 3 1.1.3 Background of pressure sensing ..................................................................................... 3 1.1.4 Sensor challenges ............................................................................................................ 6 1.2 Literature review .................................................................................................................... 6 1.2.1 Pressure sensor ................................................................................................................ 7 1.2.2 Velocity (flow rate) sensor .............................................................................................. 9 1.2.3 Vortex flow meter ......................................................................................................... 11 1.2.4 Survey of turbulence models......................................................................................... 14 1.2.5 Survey of the wake structure behind a single body....................................................... 16 1.2.6 Two bluff bodies in tandem arrangement ..................................................................... 20 1.3 Motivation ............................................................................................................................ 23 1.3.1 Proposed new sensor ..................................................................................................... 24 1.4 Research objectives .............................................................................................................. 26 1.5 Concluding remarks ............................................................................................................. 26 1.6 Research plan ....................................................................................................................... 27 1.7 Thesis outline ....................................................................................................................... 28 Chapter 2 EXPERIMENTAL WORK ......................................................................... 29 2.1 Introduction .......................................................................................................................... 29 2.2 The test rig ........................................................................................................................... 29 2.3 Preparing the test rig ............................................................................................................ 31 2.4 Visualization procedures ...................................................................................................... 32 vii 2.5 Discussion of the results ...................................................................................................... 32 2.5.1 Experimental flow field images .................................................................................... 33 2.5.2 Calculation of the soap film velocity ............................................................................ 36 2.5.3 Calculation of vortex shedding frequency .................................................................... 36 2.5.4 A sample experimental case .........................................................................................
Details
-
File Typepdf
-
Upload Time-
-
Content LanguagesEnglish
-
Upload UserAnonymous/Not logged-in
-
File Pages158 Page
-
File Size-