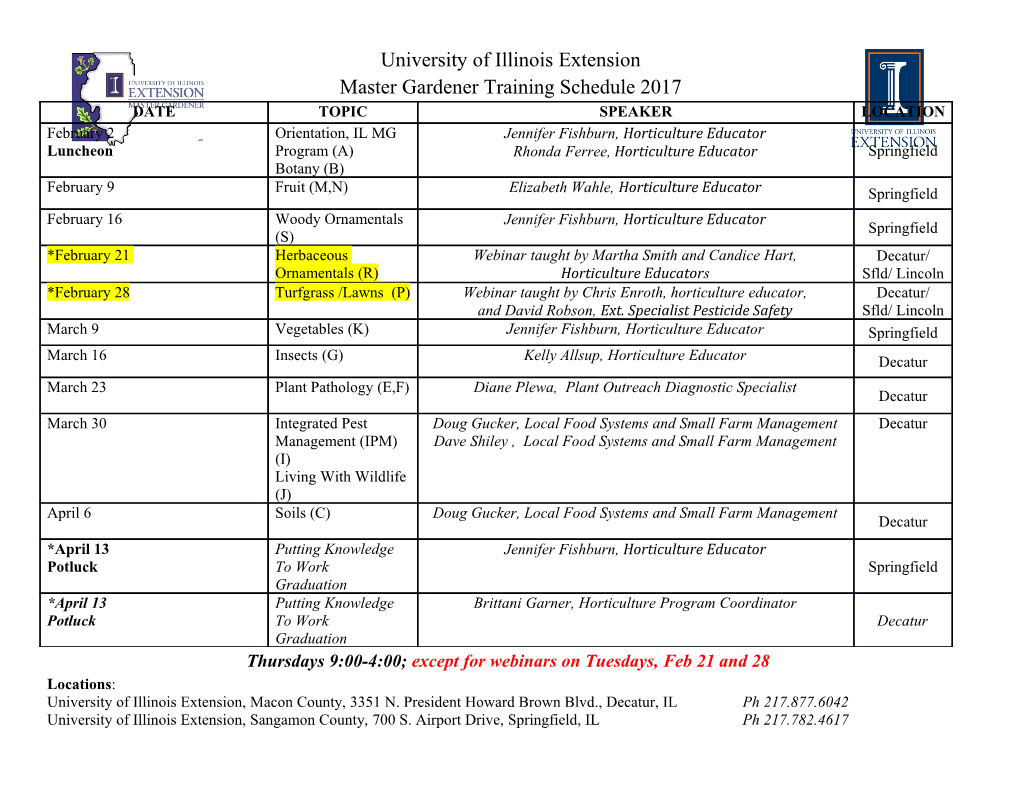
Homepage Contact Sitemap Webmail Telephone / e-mail Home page > Output - Ausgabe 18/2017 > Design for urban mining – sustainable construction planning Design for urban mining – sustainable construction planning by Prof. Annette Hillebrandt hillebrandt{at}uni-wuppertal.de Global raw material deposits have shifted their location. Many raw materials are no longer at their original source: they are bound up in new, anthropogenic structures, above all buildings. The paradigmatic change affecting the construction industry in the anthropocene – the epoch in which human impact on the earth’s biology, geology and atmosphere has become paramount – entails the separation of construction processes and materials, and high-quality recycling of the latter. Encapsulated in the concept of ‘urban mining’, this involves circular planning and costing over the entire life cycle of a building, including its ecological impact. Conversely, it signifies a departure from linear economic thinking, with its one-way logic of expansion, one-sided view of investment costs, and ultimate landfill disposal scenarios. Future buildings are being planned not for waste, but as interim deposits (‘mines’) of raw materials. In this scenario, suspect materials are entirely excluded, and the industry is committed to a responsible product policy in which the principal stands warranty for the building, the manufacturer for its products and materials, and planners and builders for its construction and future deconstruction – a major reform Prof. Annette Hillebrandt program in line with the sustainable development goals (SDG) of the United Nations as well as federal German sustainability strategy. Published 45 years ago, Donella and Dennis Meadows’ The Limits to Growth1, subtitled a “Report for the Club of Rome’s Project on the Predicament of Mankind,” predicted the dwindling resources and environmental pollution that are today an integral part of the world we live in. At the time, the Meadows’ vision was rejected as dystopic or simply ignored. Germany holds a deposit of more than 50 billion tons of anthropogenic material in the form of goods or waste products, and this volume is currently growing at an annual rate of 10 tons per head of the population.2 A vast amount of this material is ascribable to buildings and infrastructure,3 sectors in which input is some three times higher than output in terms of demolition scrap. But demolition waste is also growing: in 2014 the construction sector was responsible for 52 percent of all waste, and although in relation to overall economic growth these figures may seem marginally positive,4 the fact remains that between 1996 and 2014 absolute volumes of waste scarcely dropped. Moreover, the almost 90 percent recycling figure quoted in official statistics4 is misleading, as it also covers “other [subsidiary] uses of material” including road building and landfill. We are still far removed from a truly circular value added chain in which construction and deconstruction form a closed system. For this reason the Federal Environment Agency and other bodies have called for creative approaches to coping with the bottlenecks and rising import prices that will predictably affect Germany’s future supply of raw materials.2 In this context the concept of “urban mining” becomes highly relevant – an approach that sees our entire built environment as a gigantic interim storage facility for raw materials. To conserve this facility, existing deposits must be exploited and future building policies informed by a “design for urban mining” tailored to that purpose. Such a project will aim to drastically reduce the consumption of raw materials in the construction sector, and hence to protect the earth, air, and water on which all life is based. Decoupling the economic chain from the continuous consumption of primary raw materials, its cyclic system will make an important contribution to the sustainable qualitative growth called for in Germany’s Federal Resource Efficiency Program “ProgRess II.” 5 The transformation and reuse/rededication of a building is often – not only from an ecological but also from an economic point of view – a better alternative than demolition and rebuilding. Core reconditioning, i.e. the continuing use of the load-bearing frame after removal of all other materials, is particularly worthwhile, as the frame comprises the bulk of a building’s mass – all the more so in the case of concrete-frame buildings, given that concrete, a long-life, resource-intensive material, is still not consistently recyclable. For planners this means prioritizing flexibility. To enable new spatial divisions, ground plans should be free of load- bearing walls and reduced to a skeleton of struts and beams. In this way the same performance can be achieved with substantially less material, a principle expressible in the rule of thumb “lightness before mass.” Fig. 1: m.schneider a.hillebrandt architektur: “Metallwerkstück Briel” Corporate HQ – façade 100 percent recyclable with planned increase in value Likewise, the core structure should be designed so that room heights can be adjusted to various future uses rather than reduced to the legal minimum. Conversion of a residential block into commercial use, for example, often calls for media ducts – along with ventilation, air conditioning, sprinkler etc. installations – in dropped ceilings or floor cavities. The required room height should in future be calculated into the design on the drawing board. In the same way, space must be left in vertical shafts for technical upgrading, and shafts should be placed so as to optimize scope for future spatial configurations, whether large or small in scale. Access walkways, including stairways and elevators, must also be scaled to cope with future usage scenarios (the more people a building holds, the bigger the escape routes should be). In practice this may mean, in the worst case – i.e. where building regulations stipulate precise height limits – dispensing with an entire story. Conversely, however, building regulations should be flexible enough toward future needs to allow vertical extensions, except in the case of landmarked buildings or homogeneous ensembles. Almost a century ago, Le Corbusier called for the free façade – today the concept is more topical than ever. The reuse of a building depends on the flexibility of its façade, and here the needs of commercial buildings and offices differ from those of residential blocks. The modern façade can be an energy producer, a green cooling layer fostering biodiversity, or a data platform transmitting information, news, and goods. One thing it will always be is a thermal jacket, and in this respect demands have risen steeply in recent decades and are still rising. The evolutionary development of a façade is based on the exchangeability, replacement and reuse of its materials – which presupposes recyclability. Likewise with interior walls and fittings, whose useful life (in offices and commercial buildings) is reckoned today at ten years.6 Underlying the long-term but changing use of buildings is the concept of resilience, with its wide spectrum of meanings, including waste avoidance, resource conservation, reduction in requirements, repairing, re-envisioning, and above all recycling. Of all these aspects, reducing requirements (or “sufficiency”) is the highroad to conserving resources and avoiding waste. To give only one example: in 2000, average living space per head in Germany was 39.5 sq m; in 2016 it was already 46.5 sq m, an increase of almost 18 percent. The forecast for 2050 is 51 sq m per head.8 If this tendency continues, the rebound effect will annihilate all efficiency gains made at the material level. Action must, therefore, be taken at the political level to counter empty residential accommodation, lack of demand (in structurally weak areas), and empty luxury residences (in fashionable and expensive cities). Fig. 2: Recycling in the construction sector While on the programmatic level sufficiency entails reducing individual and sharing communal living space, the concept is also applicable to other levels. Regulations should be extended, for example, to allow the on-site recycling of contaminated spoil on (above all brownfield) building sites, where it often occurs, rather than having to cart it to special treatment plants. Similarly, so far as choice of material and detail are concerned, it may be appropriate to leave installations visible rather than conceal them under additional cladding or rendering. Dispensing with e.g. a dropped ceiling or plaster finish in favor of naked underlying materials should be reckoned a positive value in terms of material sustainability. And the on-site reuse of specific components (e.g. old bricks or floorboards) is both resource-saving and waste-avoiding, although the market for such measures is admittedly small – to date only landmarked and hand-restored buildings are generally given such care. Urban mining can only work on the basis of planning and use of materials and sections that can be readily and economically separated, dismantled, and recycled. Rather than cementing everything together, which is still the most common construction technique, elements should be connected, for example with clips, bands, and hook fastenings, or laid one above the other. Coherent retrieval of materials by type (without contamination from other types) is the key to efficient, economical recycling. But this is only possible if all system components belong to the same group of materials.
Details
-
File Typepdf
-
Upload Time-
-
Content LanguagesEnglish
-
Upload UserAnonymous/Not logged-in
-
File Pages4 Page
-
File Size-