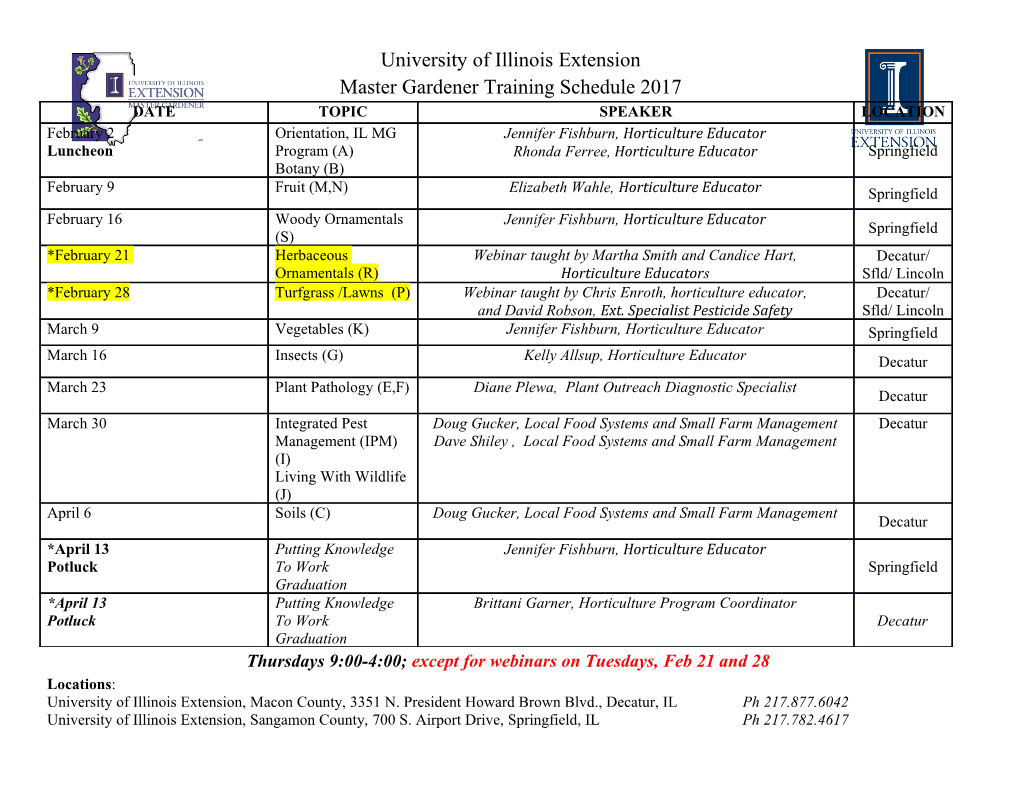
Gordon Food Service® U.S. Stewardship Report 2016 2 A MESSAGE FROM THE GORDON FAMILY Gordon Food Service is a multi-generational family-managed business. TABLE OF CONTENTS Taking care of what we have been blessed with and passing it on to those who come after us embodies the Gordon family philosophy. 2 A Message from the Our company was founded on serving the community. In 1897, Gordon Food Gordon Family Service began as a butter-and-egg delivery business, working with local farmers to ensure a steady supply of quality products to grocers. This built a deep 3 Environmental appreciation for the land and the people who grow the food that sustains us. Responsibility It also built personal ties to the communities we worked in and served along the way—a family that includes everyone connected to the food and products • Distribution Centers we deliver. • Transportation We recognize the responsibility we have to care about the people we interact with and employ, as well as to protect the resources we use while conducting • Corporate our business. This responsibility is called stewardship—a concept that describes our company’s history, our culture and our future aspirations. It’s integral to • Home Office our business practices and the decisions we make impacting our customers, • Supply Chain employees, vendors, and the communities we serve. • Customer Service In our fourth annual Gordon Food Service Stewardship Report, we take a look at our 2016 stewardship efforts in three major areas: • Product Offerings • Ensuring Corporate Sustainability 9 Social Responsibility • Minimizing Environmental Impact • Promoting Social Responsibility • Employees In 2016, we took a significant step towards our commitment to increase our • Diversity & Inclusion use of renewable energy sources by constructing a wind farm. Our investment • Community will contribute to our financial sustainability and reduce our environmental impact in the future. Service to our customers and communities is one of the most important ways we demonstrate the principle of stewardship and, ultimately, it’s one of the primary purposes of our family business. Our employees have a passion for serving their teams, their customers, and their communities—we call it their Heart to Serve. In 2016, our teams demonstrated their commitment to community service by supporting more than 80 organizations across North America. We are grateful to our customers and vendors who have helped us extend our corporate stewardship commitment. Sustained financial performance enables us to serve our customers, provide jobs, support communities and continue the environmental and social investments outlined in this report. The Gordon Family 3 ENVIRONMENTAL RESPONSIBILITY Stewardship is defined as “the careful and responsible management of something entrusted to one’s care.” We believe the planet has been entrusted to all of us to safeguard for future generations. Following are some of the most significant and recent steps we’ve taken to minimize our environmental impact. ENERGY USED PER CASE Distribution Centers DELIVERED COOLER CONSERVATION We implemented process and technology changes in our DC refrigeration systems resulting in reduced energy utilization: -5.5% -9.5% • Applied variable frequency drive technology to compressors and -4.1% -2.4% evaporators in order to match energy delivered with varying load requirements to save energy. • Implemented higher suction pressures and lower discharge pressures in 2013 2014 2015 2016 order to minimize the compressor workload required to achieve and maintain internal pressures. 0.97 0.88 0.84 0.82 kwh/case kwh/case kwh/case kwh/case • Applied vapor barriers in order to minimize condensation and the amount of warm air infiltration into the refrigerated space which require energy to remove. • Implemented automated energy management tools to optimize system performance. PROVIDING FOOD HANDLING PEACE OF MIND 31.9 % Our distribution centers earned high marks in five-point inspections conducted by AIB International. The AIB audit is not mandatory, but one we enter voluntarily—a 932 third-party analysis that assures customers of our food handling integrity. The AIB gives an overall grade based on our methods and practices, maintenance, cleaning, pest management, and overall management. A perfect AIB International score is 1,000. Among the high points, Taunton and yearly average score on cumulative reduction in food handling at our Houston distribution centers earned their highest scores distribution centers. kwh/case from 2011-2016. ever—975. SPOTLIGHT ON CENTRAL STATES Three cross- functional action teams in our Central States Division worked together to implement ideas beneficial to the planet and produced cost savings results. A few highlights of the initiatives implemented in 2016: • Fuel savings: The Transportation Team initiated a campaign to reduce truck idle time—through communication and training they were able to cut down idle time by 15 hours a week, and reduce fuel consumption and emissions. • Electricity savings: The Warehouse Maintenance Team initiated use of LED lighting, motion sensors, energy audits and more, reducing energy consumption and saving more than $67,000 on the energy bill in year one. • Paper invoice savings: The division’s Information Systems and Technology Team championed an effort to reduce printing and paper usage, eliminating waste and saving $8,000 in its first year. • Zero-Credit Focus: The Transportation Team implemented a program to reward drivers with zero credits. Initial results have shown an improvement in delivery accuracy for customers and a reduction of $120,000 in transportation credits. 4 BATTLE OF THE BUILDINGS Five Michigan facilities—Clay Campus, 651 Freezer, Home Office, Brighton, and Green Oak—participated in the West Michigan U.S. Green Building Council competition with other companies in a “Biggest Loser”-style contest to reduce energy usage. The Clay Campus was awarded second place in the Mixed Use category for a 5.29 percent energy reduction across the four buildings that share an energy meter at that location. Initiatives included: • Refrigeration Process Changes: Small changes in settings created big impacts on our energy consumption, the most significant energy load on We recycle cardboard, plastic, our distribution centers. steel, aluminum, wood pallets • Lighting: Fixtures and bulbs were updated at both the 50th Street and and waste oil, diverting tons of Clay distribution centers. material from landfills in 2016. • Leak Detection Study: We partnered with Midwest Energy for a leak detection study at our Clay Distribution Center identifying sources of compressed air leaks, which place increased demand on air compressors. • Energy Audit: Identified additional opportunities and recommended action plans. SAVINGS SHINES As part of an ongoing sustainability program at one of our specialty companies, the Halperns’ Steak & Seafood plant in Kalamazoo, MI replaced its compressor with one that’s 50 percent more efficient. All of the plant’s processing area lights were replaced with LED fixtures equipped with occupancy sensors, increasing available light while using less energy. GORDON FOOD SERVICE Transportation total gallons of fuel per case shipped: MANY HAPPY RETURN TRIPS Driving an empty truck wastes time and fuel. Our freight management partner, Capstone Logistics Services, works to make sure we maximize our fleet and -9.3% -1.6 % 0.0% reduce trips by bringing products from suppliers near customer delivery points 2011 2012 2013 back to the distribution center. Backhauls utilize our fleet in a much more sustainable manner. product orders -0.2% 0.0% -2.2% 185,626 transported 2014 2015 2016 CAPSTONE U.S. ANNUAL POUNDS 6-year cumulative 2,894,425,450 lbs. 14 .4 % gallons/case reduction. FULLY LOADED = 72,361 53-FOOT TRAILERS ENOUGH TO CIRCLE THE EARTH OVER CLOSING THE DISTANCE 564,000 delivery miles reduced in 2016 by route consolidation and 22 times realignments across our Great Lakes Central, Great Lakes West, Ohio Valley, Florida and Carolinas divisions. 5 Corporate ENERGY REVOLUTION We took a significant step toward minimizing our environmental impact by constructing a wind farm in Michigan’s Huron County with 14 turbines, each capable of generating up to 2 megawatts per hour of electrical power. The benefits: turbines • A fixed-cost renewable energy source to offset one-third of the power 14 needed to operate all of our U.S. locations. • Preventing about 120,000 tons of carbon dioxide and greenhouse gas emissions annually. PAPER SAVERS Each day, our drivers leave the distribution centers with a packet of paperwork including customer invoices and delivery instructions. By reformatting these documents to allow more lines per page, we were able to reduce the amount megawatt of paper used by thousands of pages. Paper invoices also were eliminated for per hour Store deliveries. capacity each E-PAY EFFICIENCY 2 Electronic payment enhancements introduced in 2016 enable customers to view payment history and pay invoices electronically reducing printed documents and handling time. Home Office 12.6 WASTE NOT We have a corporate partnership with CompRenew, a non-profit recycler that educates youths, equips adults with work skills and closes the digital divide TONS by refurbishing equipment for poor families. In 2016 we recycled 12.6 tons of of electronic eWaste from our Home Office and the divisions who send their equipment waste recycled or to Grand Rapids. During an Employee Recycling Day at the Home Office, an refurbished
Details
-
File Typepdf
-
Upload Time-
-
Content LanguagesEnglish
-
Upload UserAnonymous/Not logged-in
-
File Pages15 Page
-
File Size-