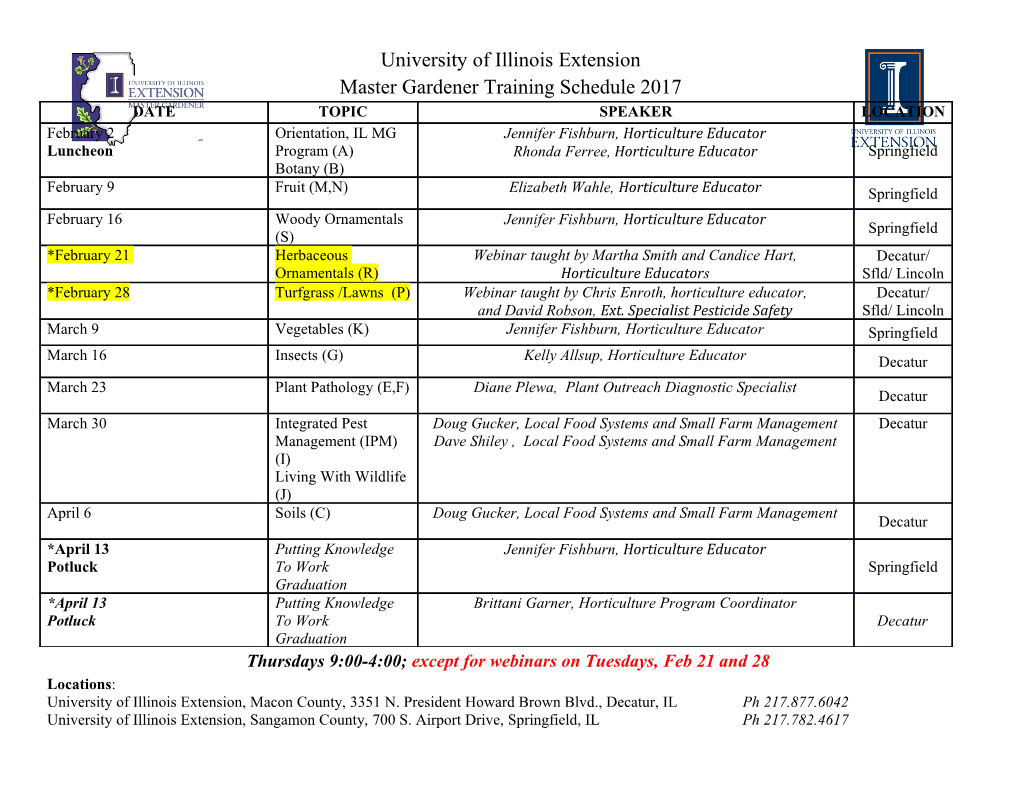
Second Generation Electric Vehicle Development at the University of Kansas By Patrick Gordon Collins Submitted to the graduate degree program in the Department of Mechanical Engineering and the Graduate Faculty of the University of Kansas in partial fulfillment of the requirements for the degree of Master of Science. _________________________________ Chair: Dr. Christopher Depcik _________________________________ Dr. Bedru Yimer _________________________________ Dr. Huazhen Fang Defended: April 24th, 2015 The Thesis Committee for Patrick Collins certifies that this is the approved version of the following thesis: Second Generation Electric Vehicle Development at the University of Kansas By Patrick Gordon Collins _________________________________ Chair: Dr. Christopher Depcik Accepted: ____________, 2015 ii Abstract Due to more stringent emissions and fuel economy standards, many automotive manufacturers are implementing more electric and hybrid vehicles into their model fleets. Hybrid and purely electric powertrains offer more sustainable transportation methods; however, larger sport utility vehicles and trucks occupy a significant majority of the vehicles on the road in the United States. To this end, this work covers the development of a second generation electric sport utility vehicle at the University of Kansas. Chapter 2 of this thesis outlines the use of CAN bus in the automotive industry throughout the evolution of the Electronic Control Module. Chapter 2 also showcases the different types of control modules installed in vehicles. CAN bus theory of operation, message formats, error handling, wiring techniques, and additional vehicle networking methods are also discussed. Lastly, electric vehicle case studies at the University of Kansas are presented to illustrate the importance and benefits of implementing CAN bus. Chapter 3 focuses on the development of the JimmE-V. The JimmE-V serves as a research vehicle that has features similar to EVs available to consumers. In order for the vehicle to generate research quality data, vehicle operation and systems integration are discussed. CAN bus communication allows components to be controlled, calibrated, and monitored in real-time allowing the JimmE-V to be adjusted for a variety of research studies. Safety information is also provided due to the high voltage potential when working with EVs. The different causes for vehicle failure are additionally included in this chapter. Chapter 4 examines the complete energy and emissions produced by the JimmE-V. This chapter highlights the energy used in the vehicle manufacturing process in addition to examining the benefit of reusing vehicle components. Furthermore, a Life-Cycle Analysis (LCA) was generated using Argonne National Laboratory’s Greenhouse Gasses, Regulated Emissions, and Energy Use in Transportation (GREET) model. The LCA provides estimations for the JimmE-V’s energy use and emissions produced throughout the vehicle’s lifetime use. Accompanying this information is information regarding the iii production and recycling of LiFePO4 batteries. This work’s LCA efforts for the JimmE-V are compared to the previous LCA efforts for the VW Beetle. Drive cycle data was collected to examine the efficiency of the JimmE-V, and to compare the results to the VW Beetle. Lastly, the solar generation capabilities of the newly built (2013) Hill Engineering Research and Development Center are presented. Lastly, Chapter 5 focuses on the conclusions of the JimmE-V project mainly highlighting the author’s main contributions to EV projects at the University of Kansas. The author’s main contributions were centered on the powertrain of the JimmE-V including the motor, controller, ECM, and battery pack. This chapter additionally focuses on the vehicle’s future impact as a research platform. iv Acknowledgements The efforts presented in this thesis could not have been accomplished without the assistance of multiple individuals and entities. During their time at the University of Kansas, the Transportation Research Institute provided financial support to the KU EcoHawks sustainable transportation endeavors. The KU Mechanical Engineering Department provided additional project funding, and their machine shop staff members Charles Gabel and Ash Shadrick. The KU EcoHawks JimmE-V teams from 2010 until 2014 were a vital component to the JimmE-V project; specifically, Josh Petty, Nathaniel Mayhew, Dustin Bergstrom, and Kevin Helton. In addition to the undergraduate students involved with this project, there were also graduate students involved. Dr. Michael Mangus offered his knowledge and support, and the occasional tow during the initial testing of the JimmE-V. Additionally, Chenaniah Langness provided advice for electrical troubleshooting, and additional feedback during the early stages of vehicle calibration. Jonathan Mattson provided assistance during drive cycle testing by monitoring the vehicle’s data acquisition systems. Similarly, Brian Gessler and Matthew Cole aided in drive cycle testing. Lastly, EcoHawks Alumni Matthew Choate assisted in collecting drive cycle data. Former graduate student Bryan Strecker is recognized for his previous LCA efforts on the VW Beetle, and providing feedback on the JimmE-V model assumptions made in this thesis. Former graduate student Austin Hausmann is additionally recognized for his efforts involved with the JimmE-V project and helping get the 2011-2012 JimmE-V team educated on electric vehicle architecture. Dr. Christopher Depcik provided the opportunity to study electric vehicle powertrains, and was an excellent advisor offering additional resources, knowledge, and advice. In addition to colleagues, this work could not have been completed without the family support behind the scenes. Specifically, my mother, Charlene Frye, provided her love, support, and encouragement throughout my education process. Additionally, my father, John Collins, offered an infinite source of automotive knowledge in addition to his love, support, and encouragement. My step- father William Frye offered similar support, and accompanied me on many trips to the salvage yard to help locate missing pieces for the JimmE-V. Finally, none of this work could have been accomplished without the love and support of my patient wife Charlotte. v Table of Contents Nomenclature……………………………………………………………………………………………. xxii 1.1 Introduction………………………………………………………………………………………... 1 1.2 Past Efforts in Electrified Vehicles at the University of Kansas…………………………………...3 1.3 Thesis Focus……………………………………………………………………………………….. 4 Chapter 2: Vehicle Communication Networks Focusing on the Development of a Controller Area Network for a Full-Scale Electric Vehicle Conversion.……………………………………........... 6 2.1 Abstract…………………………………………………………………………………………... 6 2.2 Introduction………………………………………………………………………………………. 7 2.2.1 Electronic Control Unit Construction……………………………………………………………. 8 2.2.2 Electronic Control Unit Applications…………………………………………………………….. 8 2.2.3 CAN Bus Theory of Operation…………………………………………………………………... 11 2.2.3.2 CAN Message Frame and Error Reporting………………………………………………………. 13 2.2.4 CAN Bus Wiring and Setup……………………………………………………………………… 15 2.2.5 Additional Vehicle Networking Techniques……………………………………………………... 17 2.3 On Board Diagnostics……………………………………………………………………………. 19 2.3.2 OBD-I…………………………………………………………………………………………….. 19 2.3.3 OBD-II…………………………………………………………………………………………… 20 2.4 University of Kansas EcoHawks Case Studies…………………………………………………... 22 2.4.1 EcoHawks GEM Short-Range Electric Vehicle Swappable Battery Pack………………………. 26 2.4.2 EcoHawks 1997 GMC Jimmy KU EV 2.0………………………………………………………. 39 2.5 Conclusions………………………………………………………………………………………. 56 Chapter 3: JimmE-V Operation and Overview…………………………………………………………… 57 3.1 Abstract…………………………………………………………………………………………... 57 vi 3.2 Introduction………………………………………………………………………………………. 57 3.3 Vehicle Overview…………………………………………………………………………………60 3.4 Vehicle Chassis…………………………………………………………………………………... 62 3.5.1 Three-phase AC Induction Motor………………………………………………………………... 70 3.5.2 JimmE-V Motor Controller & Inverter………………………………………………………....... 75 3.5.3 JimmE-V Electronic Control Module……………………………………………………………. 93 3.6.1 Vehicle Traction Battery Pack…………………………………………………………………...109 3.6.2 JimmE-V Battery Management System………………………………………………………… 118 3.6.3 Manzanita Micro PFC Battery Charger………………………………………………………… 142 3.7 JimmE-V 12 VDC System……………………………………………………………………… 152 3.8 DC-DC Converters……………………………………………………………………………… 162 3.9 Electric Power Steering System………………………………………………………………… 166 3.10 Vehicle Air Conditioning System………………………………………………………………. 171 3.11 Causes for Vehicle Failure…………………………………………...…………………………. 179 3.12 Conclusion……………………………………………………………………………………….181 Chapter 4: Well-to-Wheels energy and emissions analysis of a recycled 1997 GMC Jimmy converted into a battery electric vehicle………………………………………………………………………... 182 4.1 Abstract…………………………………………………………………………………………. 182 4.2 Introduction……………………………………………………………………………………... 183 4.3 Previous Efforts for the 1974 VW Super Beetle………………………………………………... 186 4.4 Reuse of Vehicle Components………………………………………………………………….. 191 4.5.1 Lithium Battery Production……………………………………………………………………...195 4.5.2 Lithium Battery Recycling……………………………………………………………………… 198 4.6 Outcomes of this Study…………………………………………………………………………. 202 vii 4.7 GREET Recycling and Reuse Energy and Emissions Analysis………………………………... 204 4.8 GREET Electricity Energy and Emissions Analysis…………………………………………… 207 4.9 Drive Cycle Results……………………………………………………………………………...213 4.10 Hill
Details
-
File Typepdf
-
Upload Time-
-
Content LanguagesEnglish
-
Upload UserAnonymous/Not logged-in
-
File Pages263 Page
-
File Size-