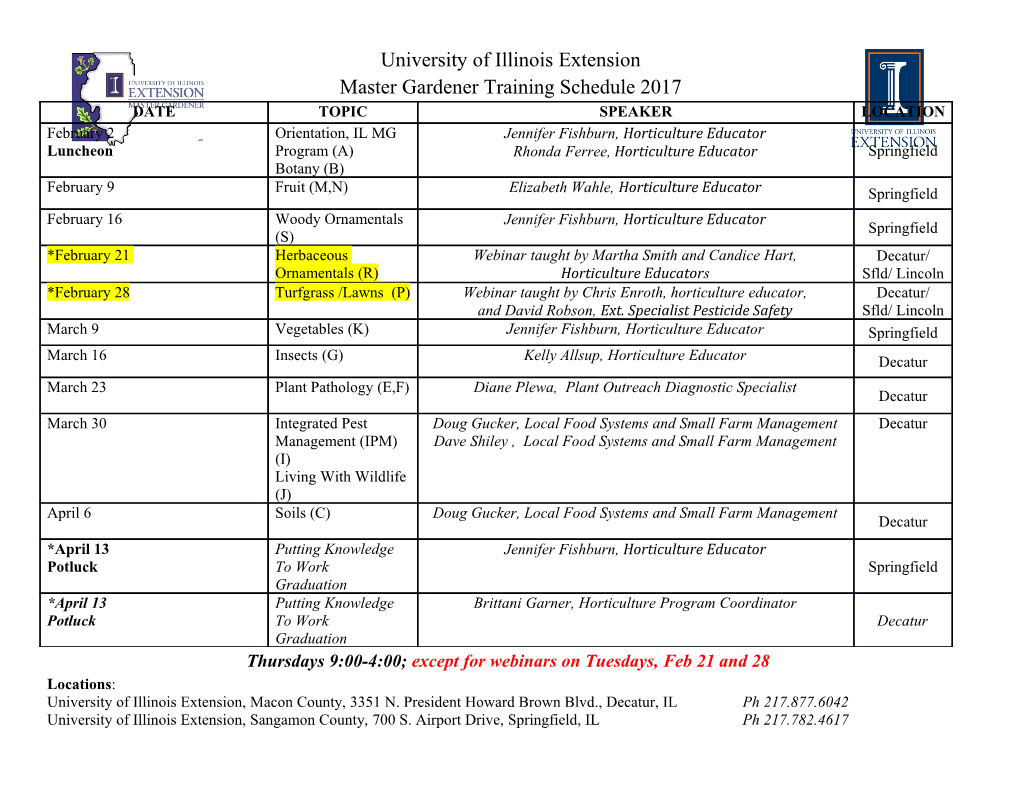
A Review of Industrial Aeroelasticity Practices at Dassault Aviation for Military Aircraft and Business Jets E. Garrigues To cite this version: E. Garrigues. A Review of Industrial Aeroelasticity Practices at Dassault Aviation for Military Aircraft and Business Jets. Aerospace Lab, Alain Appriou, 2018, pp.1-34. 10.12762/2018.AL14-09. hal- 01935273 HAL Id: hal-01935273 https://hal.archives-ouvertes.fr/hal-01935273 Submitted on 5 Dec 2018 HAL is a multi-disciplinary open access L’archive ouverte pluridisciplinaire HAL, est archive for the deposit and dissemination of sci- destinée au dépôt et à la diffusion de documents entific research documents, whether they are pub- scientifiques de niveau recherche, publiés ou non, lished or not. The documents may come from émanant des établissements d’enseignement et de teaching and research institutions in France or recherche français ou étrangers, des laboratoires abroad, or from public or private research centers. publics ou privés. Aeroelasticity and Structural Dynamics E. Garrigues (Dassault Aviation) A Review of Industrial Aeroelasticity E-mail: eric.garrigues@dassault- Practices at Dassault Aviation for aviation.com Military Aircraft and Business Jets DOI: 10.12762/2018.AL14-09 ircraft structure design is a complex industrial process that requires multidisciplinary Aanalyzes and considerations in fields as diverse as aerodynamics, structure, materials and systems, as well as the right compromise between the constraints imposed by these different fields, in order to meet the overall performances required for aircraft. In the field of business jets and military aircraft, given the research into ever more efficient aerodynamic formulas, the constant desire to design "as light as possible", and the increase in fuselage sizes, aircraft flexibility has increased considerably over the last few decades. This has required the consideration of increasingly complex aeroelastic coupling phenomena that are present in the flight envelope from the very first phases in aircraft development. The challenge goes far beyond the domain of aerostructural performance alone, since aeroelasticity can also have a significant impact on related domains, such as aircraft performances, handling qualities, or system design. It has merely reinforced the potentially major impacts of aeroelasticity on the risks, costs and deadlines for new aircraft programs: aeroelasticity is now seen as one of the main disciplines in design, and as one of the "critical" processes in the aircraft development logic. This highly-challenging context has been the source of major and constant modifications in the field of aeroelasticity since the 1990s at Dassaultviation. A Today, this trend continues, and aeroelasticity will have to tackle a series of entirely new challenges and needs, and continue to reinvent itself at the same pace if it is to avoid hampering innovation and future technological breakthroughs. In this perspective, this article gives an overview of the current best industrial practices in terms of aeroelasticity in the military aircraft and business jet domains at Dassault Aviation. The main aspects of this challenging and exciting field are covered: the numerical methods and tools, the experimental validation process, the aircraft program expectations and aspects relating to human organization. It discusses the principles and guidelines rather than details about the basic equations and methods. The last part presents the future industrial challenges in the field of aeroelasticity for Dassault Aviation. Introduction The design of aircraft structures is a complex industrial process that In the field of business jets, given the research into ever more effi- requires multi-disciplinary analyses and considerations in fields as cient aerodynamic formulas, the constant desire to design "as light diverse as aerodynamics, structure, materials or systems, as well as possible" and the increase in fuselage sizes, the flexibility of air- as the need to find the right compromise between the constraints craft has grown considerably over the last few decades. This has imposed by these different fields, in order to meet the overall perfor- required the consideration of increasingly complex aeroelastic cou- mances required for aircraft. pling phenomena that are present in the aircraft flight envelope from Issue 14 - September 2018 - A Review of Industrial Aeroelasticity Practices at Dassault Aviation AL14-09 1 the very first phases of development. The challenge goes far beyond simplified, and sometimes very conservative, methods to analyze the domain of aerostructural performance alone, since aeroelastic- this phenomenon. ity can also have a significant impact on related domains, such as aircraft performances, handling qualities or system design. Between the end of the 1960s (MIRAGE F1) and the end of the 1980s (FALCON 900, MIRAGE 2000, MIRAGE 4000 and the first In the military domain, the promotion of existing platforms in terms RAFALE demonstrator; also CONCORDE at Sud-Aviation), the rapid of the ability to carry multiple under-wing external store configura- growth of numerical aeroelasticity and the analysis of complex con- tions, and the adaptation of these configurations to the needs and figurations, which had been difficult to obtain through analysis up multi-role missions of customers, is also reflected by an increase until that point, were facilitated by a large number of projects at Das- in the aeroelastic phenomena present on the aircraft. The challenge sault Aviation, the acquisition of the first scientific computers and, is therefore to develop and certify new configurations by keeping in parallel, the development of structural finite-element dynamic major design modifications to a minimum (or, better yet, avoid- analyses [1]. Above all, the development of steady and unsteady ing them), while preserving all of the performances of the exist- linear aerodynamic numerical methods with interactions between ing aircraft. Aeroelasticity can motivate modifications to structures, lifting surfaces, such as the Doublet-Lattice Method (DLM) [2], [3], upgrades to fly-by-wire (FBW) standards, or modifications to the [4] contributed to this. A typical example is that of the delta/canard architecture of aircraft systems. formula without stabilizer on the RAFALE. Although in the early 1990s we may have thought that the domain Also over that same period, the development of in-flight instru- of aeroelasticity for aircraft was one that we mastered well, and ments, telemetry and signal-processing techniques made it possi- that really only required the tools and methods already envisaged ble to observe and quantify the aeroelastic phenomena, and validate in the 1960s to 1980s to be brought to maturity and industrialized the associated models (or readjust them) using wind tunnel tests on in the future, the new challenges progressively imposed at Dassault flexible mock-ups or flight tests [5]. However, we should remember Aviation at the end of the 2000s and at the start of the 21st century the accident that occurred on the first MIRAGE F1 prototype follow- (design of the RAFALE air/ground standards, the FALCON 7X/8X/5X ing horizontal stabilizer flutter at M = 0.91, at a low altitude. This aircraft and the military nEUROn UAV) have placed aeroelasticity at accident occurred on May 16, 1967 during a training flight for a the very heart of the aircraft design process, with major potential demonstration at the Paris Le Bourget airshow. It was a dark day in impact on the duration and costs of the various development phases the history of Dassault Aviation, leaving René Bigand, the test pilot and, more generally, the cost of the programs (and the associated of the aircraft, no chance at all. risks). In preparing for the future, aeroelasticity has also become an indispensable factor for innovation. During this blossoming period for aeroelasticity, full of draft projects and tests on real structures (sometimes difficult), the growth and This situation has been the source of major modifications to the maturity of the various numerical and experimental techniques has field of aeroelasticity, in terms of the methods used, the calculation been substantial at Dassault Aviation, and many of these techniques processes and the organization of human skills over the last 20 continue to be a point of reference, even to this day. This, to such an years, and, more specifically, over the last decade. Today, this trend extent that we thought at the start of the 1990s that the field of aero- continues, and aeroelasticity will have to tackle a series of entirely elasticity for aircraft was one that was mastered, and in the future new challenges and needs, and continue to reinvent itself at the would only require that the tools and methods already envisaged in same pace, if it is to avoid hampering innovation and the setup of the 1960s to 1980s reach maturity and be industrialized. future technological breakthroughs. The experience of the following period between 1990 and 2020 In this context, this article gives a complete overview of the cur- (RAFALE, FALCON 2000/7X/8X/5X and nEUROn) and the conclu- rent best industrial practices in terms of aeroelasticity in the mili- sions that are drawn from it today show that, quite on the con- tary aircraft and business jet domains at Dassault Aviation. The trary, under the influence of the market and the competition, aero- main aspects of this challenging and exciting field are covered: the elastic engineers continue to face
Details
-
File Typepdf
-
Upload Time-
-
Content LanguagesEnglish
-
Upload UserAnonymous/Not logged-in
-
File Pages35 Page
-
File Size-