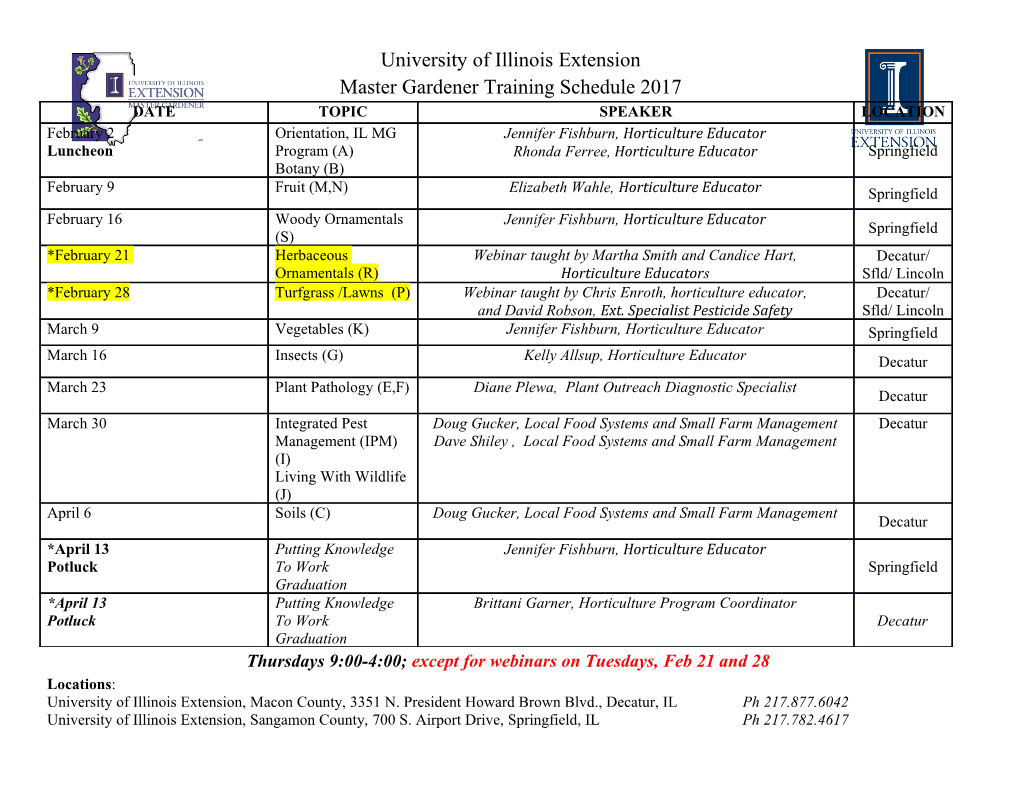
Transactions on Engineering Sciences vol 6, © 1994 WIT Press, www.witpress.com, ISSN 1743-3533 A computational method for the analysis of viscoelastic structures containing defects G. Ghazlan," C. Petit," S. Caperaa* " Civil Engineering Laboratory, University of Limoges, 19300 Egletons, France & School of Mechanical Engineering, C.M.A.O. Automatic Production, B.P. 1629, 65016 Tarbes, France ABSTRACT A computational method is presented for the analysis of quasi-static, li- near, small strain structures containing defects. The method of analysis involves the use of a discrete creep spectrum to simplify the equations governing the viscoelastic process. Viscoelastic constitutive equations are then given in terms of middle surface strains and curvatures and their conjugated stress resultants. This leads to great savings in the amount of computer storage needed to solve problems involving three-dimensional loadings. Solutions are then obtained by a "forward marching" process where solutions of a particular time are found from those at a previous time. A method is presented which eliminates the need to store the solu- tions at all previous time steps, and is therefore very efficient. An illustra- tive example in the case of viscoelastic cracked material is included. INTRODUCTION The analysis of a viscoelastic material presents many difficulties for real problems of complex geometry. Analytical solutions to problems involving creep displacements are often obtained by applying the correspondence principle [1,2] which makes use of the fact that the equations governing viscoelastic behaviour become analogous to the equations of elasticity by the application of a Laplace transformation. Analytical solutions are limi- ted however to problems to which the associated elastic solution may be Transactions on Engineering Sciences vol 6, © 1994 WIT Press, www.witpress.com, ISSN 1743-3533 384 Localized Damage found, and for problems involving complicated boundary conditions, nu- merical techniques need to be used. The use of the finite element method for the solution of such problems has been demonstrated by Zienkiewicz and Watson [3] and Zienkiewicz et al [4]. Although such numerical tech- niques allow solution of complicated problems, they require large amounts of computer storage and data preparation. In order to reduce computer storage requirement and reduce the computational effort, we formulate the constitutive equations in terms of middle surface strains and curvatures and their conjugated stress resul- tants. We begin with a discussion of a mechanical constitutive equation for thin structures undergoing small deformations and which are subjected to mechanical stresses. It is assumed that the viscoelastic behaviour of a material can be represented by a discrete creep function (a finite series of Kelvin elements coupled with an elastic and viscous response). Using this assumption of wide validity, the incremental constitutive equations can be performed analytically. Thus the difficulty of computer storage require- ments is avoided and the complete past history of stresses is represented by some auxiliary tensors. BEHAVIOUR OF VISCOELASTIC MATERIAL The stress-strain relation for a linear viscoelastic material can be written in terms of creep functions where Gap~fs(i) are the components of the creep tensor G(t) and (Tctp(t) are the components of the strain and stress tensors. According to the results of Biot and Mandel [5], the creep tensor G(t) is written in terms of a discrete creep spectrum G^(t) = [<%b + E(l-e-'^)G^ + ,<%] HO (2) t=l where G^\ G^\ and G^\i = 1..JV, are fourth-rank tensors to be de- termined to represent any particular creep function of interest, Y(t) is the Heaviside unit step function, and A» are positive scalars. According to Love's first order theory for thin structures, the consti- tutive equation (1) can be written in terms of generalized variables 2 2 t = EE / dr (3) 7=i,=i-/ Transactions on Engineering Sciences vol 6, © 1994 WIT Press, www.witpress.com, ISSN 1743-3533 Localized Damage 385 where 6ap(t), Xap(f) a-re the middle surface extensional strain and curva- tures, N~ft(t), M^s(t) are the generalized stresses (stress resultants), and //i, fj>2 are constants and given by : fii = l//i, ^2 — 12/k^, where h is the structure thickness. In order to determine the components of the creep tensors Gr , G^°°' and G , we consider the generalized Kelvin model shown in Figure 1 in which K^piS* -^-ap^S designate modulus of elasticity where %^^, 'H^p-fS ^^ coefficients of viscosity and TV is the number of Kelvin-Voigt elements used to approximate the material's behaviour. The creep function of the mechanical model is given by i /(<) = [ + + no K\ •A°1 Figure 1 : Generalized Kelvin- Voigt model The comparison between (2) and (4) gives FORMULATION OF DIFFERENTIAL EQUATIONS When the previous mechanical model is subjected to the stress , the rate of the total strain — "xT ^ ,' is given by , (5) at 1=1 dt dt where e^(t), c~(t) and c^(t) are the total strain in the spring, in the dashpot and in the i*** Kelvin element. The first differential equation Transactions on Engineering Sciences vol 6, © 1994 WIT Press, www.witpress.com, ISSN 1743-3533 386 Localized Damage is then obtained from equation (5) using generalized variables Ca0-r*W 1 1 fl ( ^i-W-y^W 1 AT o I = — J I .f v^ — Xa/3T*(*) J "^* I ^M^(t] ) *=1 V X^^l ^iir',} The second differential equation is determined by ^ where cr^'(tf), and 0^ (t) are the stresses in the i^ spring and dashpot respectively. The second differential equation is obtained from equation (8) using generalized variables INCREMENTAL CONSTITUTIVE EQUATIONS The solution process of a step-by-step nature is used. Considering the time step Atn = tn — ^n-ij we assume that the time derivative during each time increment is constant. A linear approximation is used for generali- zed stresses, therefore the incremental constitutive equations can now be obtained from the two previous differential equations [6] = ££"«** + where Map^t is a fourth order tensor which can be interpreted as the compliance tensor. It is given by *W = <%, + E [i- Tw- (i-«"^"^l + ;^«-«Si (€a^)n-i and (%a/3)n-i represent the influence of the complete past history of generalized stresses. They are given by 22 TV ( ^i N^n-l) } = ££ A«.G5>, + 5> (10) Transactions on Engineering Sciences vol 6, © 1994 WIT Press, www.witpress.com, ISSN 1743-3533 Localized Damage 387 where A; = G^^ (1 - e~*«*ir«**») which represent the influence of the i** Kelvin element. In the context of a finite element model, the governing equations of the discretized system are derived from the principle of virtual displacement [7]. The generalized strains are derived from shape functions in a standard manner [7]. The equilibrium equations can be written as [#*•]„ {A(«f )„} = {Af}„ + {AF-}^ (11) where the tangent matrix [Kr]n and the viscous vector Af'\_i are given by , [*T]« = \ [B]T[ J*A = {F}n — {-F}n-i is the external load vector increment, n-i is the viscous load vector increment corresponding to the complete past history of strains and [Cn] is the generalized constitutive matrix which can be determined numerically by the inverse of the com- pliance tensor. STRESS AND STRAIN INTENSITY FACTORS Fracture mechanic approach of viscoelastic materials It has been shown that for plane problems, the asymptotic field at crack tip can be described by four parameters : two stress intensity factors and two strain intensity factors. And then, in viscoelastic materials the cor- respondence principle enables the users to assume the corresponding elas- tic problem. Stress and displacement fields in the singular area are given by [8] : , t) = T . j ^ (13) and ha/3 are the well known functions of 0 [9]. p(t) is shear modulus : Transactions on Engineering Sciences vol 6, © 1994 WIT Press, www.witpress.com, ISSN 1743-3533 388 Localized Damage k — 3 — 4z/ in plane strain k — (3 — i/) (1 + i/) in plane stress Here we consider v the poisson ratio constant. The strain intensity factor Kp(t) can be defined by : (14) with (13) and (14) we obtain the relationship between stress and strain intensity factors : 9a(3 q/3 (15) 9a/3 Numerical crack opening displacement method In this paper, we propose to use the numerical crack opening displacement (C.O.D) in order to obtain Kp(t). The displacement field is obtained from the viscoelastic finite element model presented before. The C.O.D noted [%a](r,Z) is defined by : [u«](r, t) = u«(r, TT, t) - ua(r, -TT, t) (16) the strain intensity factors are obtained from equation (14) : (17) the stress intensity factor KJ(t) is obtained from equation (15) (18) CREEP ON A THREE POINT BENDING TEST The numerical method developed in this paper will be illustrated by a plane stress problem. Its dimensions are : length 360mm, width 100mm and thickness 50mm. The load F(t) = 1000 JV, is located at the centre of the beam. The structure contains a finite crack of 50 mm in length. The creep function for the material is represented by equation (4) with N = 1 and the constants of the creep function are assumed as in Table /. KQ MPa Ki MPa 7/1 MPa.min 2500 2500 30000 Table I: Constants used in creep function Transactions on Engineering Sciences vol 6, © 1994 WIT Press, www.witpress.com, ISSN 1743-3533 Localized Damage 389 V \/ A/ Figure 2 : Three point bending test half mesh In Figure 3, the crack opening displacement is plotted for various times. Strain intensity factor Kj(t) is computed from equation (17) and the stress intensity factor KJ(t) is computed from equation (18), while the shear modulus fi(t) is obtained from the creep function.
Details
-
File Typepdf
-
Upload Time-
-
Content LanguagesEnglish
-
Upload UserAnonymous/Not logged-in
-
File Pages8 Page
-
File Size-