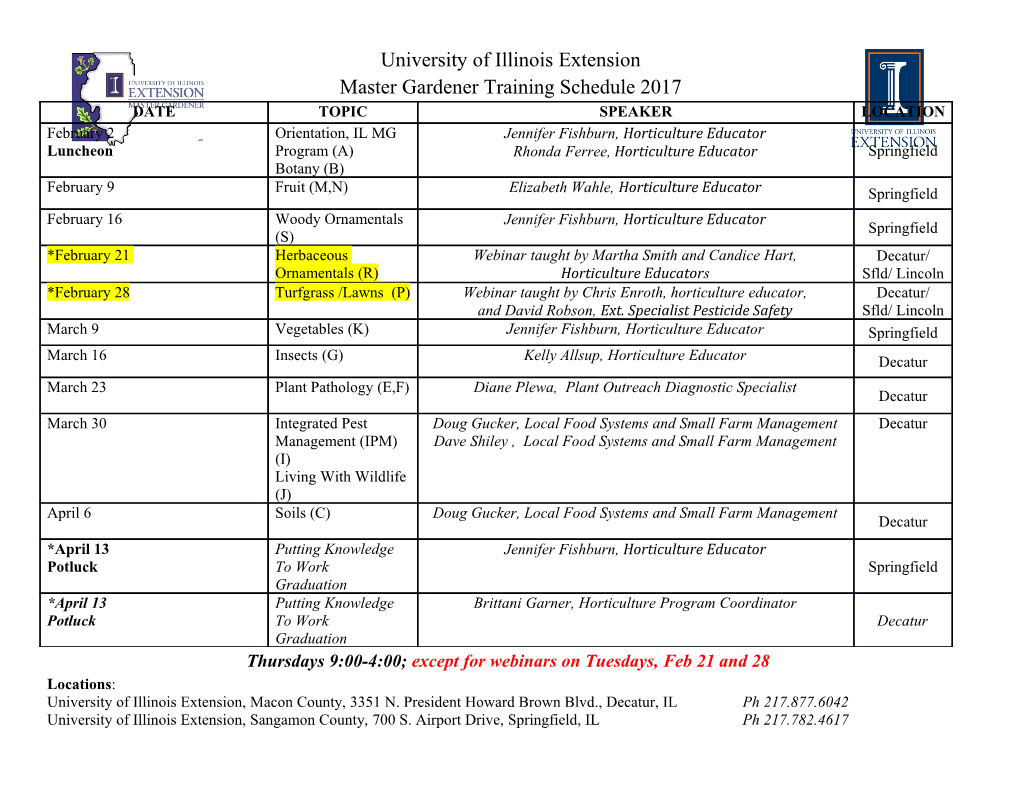
A NONLINEAR CONTACT ALGORITHM PREDICTING FACET JOINT CONTRIBUTION IN THE LUMBAR SPINE A Thesis Presented in Partial Fulfillment of the Requirements for the Degree Master of Science in the Graduate School of The Ohio State University By Kimberly Anne Vandlen, B.S. Industrial and Systems Engineering ******* The Ohio State University 2009 Master’s Examination Committee Dr. William S. Marras, Advisor Dr. Daniel A. Mendelsohn ABSTRACT It is hypothesized that the facet joints may play an important role in the causality behind back pain. Previous biomechanical models lack detailed facet geometry and contact modeling, the inclusion of cartilage, and the modeling of the full lumbar spine. The objective of this study was to more realistically assess facet loading in an existing low back biomechanical model. The second objective of this study was to demonstrate how the model including facets reports load distribution in pushing and pulling tasks. Several new components were added to an existing biomechanical model: realistic geometry (based on CT & MRI), more accurate facet radii of curvature, articular cartilage thickness, and contact algorithms which defined the contact between each lumbar spine facet. Trials were run once with facets turned on, and repeated with facets turned off. Resultant disc loads were lower in the model with facets. The model clearly showed facet to lamina contact for many of the trials studied. Facets at L4/L5 and L5/S1 bore about 40% of the total load through those segments. The nonlinear model performed well. The facets bear a large portion of the load though the lumbar spine. Load transmission percentage results with the facet model are comparable to previous studies. The facets bore a greater amount of load in pushing tasks than in pulling tasks. The direction of the offloading of the intervertebral discs is not as straightforward as previously hypothesized. Including realistic facets in the model does ii not necessarily result in decreased anterior-posterior shear loads within the disc under these loading conditions. iii ACKNOWLEDGEMENTS I would like to extend a special thank you to my advisor, William Marras, for his support while I have worked in the lab and during the thesis journey. He pushed me to challenge myself in ways that I hadn’t done before, and I am stronger for it. Thanks also to the second member of my committee, Dan Mendelsohn, who lent his expertise and his time for many question-filled meetings. Thank you to my cohorts in the Biodynamics Lab, especially the modeling team. Greg, Cliff and Peter contributed a tremendous amount of knowledge and time to aid in my understanding of the whole system. Thanks also to Greg for reviewing my thesis. The working environment I was surrounded with could not have been more pleasant. Finally, thank you to my family. My parents have supported me throughout. All of my gratitude goes to my husband Jeff, whose patience and encouragement kept me strong. iv VITA November, 6 1983 …………………………….. Born - Hillsdale, MI, U.S.A. 2006 .………………………………………….. B.S. Mechanical Engineering Hope College, Holland, MI 2006-Present …………………………………… Research Assistant The Biodynamics Laboratory The Ohio State University FIELDS OF STUDY Major Field: Industrial and Systems Engineering v TABLE OF CONTENTS Page Abstract ………………………………………………………ii Acknowledgements ………………………………………………………iv Vita ……………………………………………………….v List of Tables ……………………………………………………..viii List of Figures ………………………………………………………ix Chapters: 1. Introduction …………………….…………………………1 1.1 Anatomy …………….…………………………2 1.2 Potential Pain Pathways ………….…………………………4 1.3 Facet Modeling …………….…………………………5 1.4 Biomechanical Model …….…………………………9 2. Methods ………………………………………………………11 2.1 Overview ………………………………………11 2.2 Modeling Software Overview ………………………13 2.3 Material Properties ………………………………13 2.4 Lumbar Spine Geometry ………………………………14 2.5 The Articular Facets ………………………………………17 2.6 Model Building ………………………………………21 2.7 Experimental Conditions ……………………………....23 3. Results ………………………………………25 4. Discussion ………………………………………41 5. Conclusions and Future Work ………………………………………51 5.1 Conclusions ………………………………………51 vi 2.2 Future Work ………………………52 Bibliography ………………………………………………………54 vii LIST OF TABLES Table Page 1.1 Percentages of total sample (n=25) population…………………………………..4 1.2 Previous spine FEM and contact models………………………………………...8 2.1 Model material properties………………………………………………………13 2.2 Anthropometric data of test subject…………………………………………….15 2.3 Constants for ADAMS IMPACT function……………………………………..21 3.1 Conditions tested in facet model………………………………………………..25 3.2 Percentage of max contact load relative to max resultant load without facets….40 4.1 Facet static load transmission literature………………………………………....48 viii LIST OF FIGURES Figure Page 1.1 Facet joint capsule……………………………...………………………………..3 2.1 Methods flowchart…………………….………………………………………..12 2.2 Lumbar spine model with facet contacts..………………………………………16 2.3 Overlap of contacting bodies……..…………………………………………….18 2.4 Problem description, contact with coated bodies...……………………………..19 2.5 Force-displacement curves for L4/L5…………………………………………..20 2.6 Graphical representation of facet contact……………………………………….22 3.1 Percent difference (pushing, heavy load)………………………………….……28 3.2 Percent difference (pushing, light load)……………………………....………...28 3.3 Percent difference (pulling, heavy load)………………………………….….…29 3.4 Percent difference (pulling, light load)……………………………....………....29 3.5 Average of resultant disc loads, facets on…………………………….………...32 3.6 Average of resultant disc loads, facets off…………………………….………..32 3.7 Left and right resultant contact forces………………………………….……….33 3.8 Pushing, superior disc loads with and without facets…………………..…….....34 3.9 Pulling, superior disc loads with and without facets…………………..………..34 3.10 Pushing, inferior disc loads, with and without facets…………………..……...36 3.11 Pulling, inferior disc loads, with and without facets…………………..………36 ix 3.12 Pulling/50% handle height/light – disc & facet loads L4/L5……………………..38 3.13 Pulling/50% handle height/light – disc & facet loads L5/S1……………………..38 3.14 Pushing/50% handle height/heavy – resultant loading comparison………………39 3.15 Comparison of load born by facets with different stiffness values……………….40 4.1 Graphical example of facet to lamina contact……………………………………...42 x CHAPTER 1 INTRODUCTION The study of the causality behind low back pain is an ongoing one in the world of biomechanics because of the number of people who experience back pain. Approximately 80% of Americans will experience some type of back pain during their lifetime[1]. It is estimated that every year in the United States almost 600,000 people take time away from work to treat or recover from musculoskeletal pain or functional loss [2]. The significance of this problem should not be underestimated. A common speculation as to the causality behind low back pain is disc and facet joint degeneration[3]. As the intervertebral discs deteriorate, the zygapophyseal (facet) joints are consequently called upon to bear a greater load. The facet surfaces degenerate via ossification and the deterioration of the surrounding cartilage. The aim of this study is to develop a more realistic representation of the forces occurring in the facet joints, in order to better understand their role in spinal loading possibly leading to low back pain. 1 1. 1 Anatomy The facet joints are within the posterior elements of the spine, which are the bony processes that engage when the spine is extended or in torsion. The surfaces that touch between the upper and lower posterior elements are called articular facets, which are a part of the facet joint. These joints are reported to transmit anywhere between 2-59% of the load through the spine[4-7]. The facets are also richly innervated with branches of the spinal nerves[8]. The facet joints are so close to the intervertebral foramina, the area through which the spinal nerves pass from the vertebral canal, that it is easy for the facets to cause irritation if they are pushed beyond their physical limits via extreme torsion or bending. The facet joints are paired synovial joints that join the vertebral arch of one vertebra to the arch of the next vertebra[9]. The facet surface lies between the superior and inferior processes of a vertebra. The facet joint is the only synovial joint in the spine, and it consists of hyaline cartilage that overlies subchondral bone, with a synovial membrane and a joint capsule (Figure 1.1, [10]). The articular cartilage surrounding the bony portion of the facets is covered with a film of synovial fluid which facilitates in the gliding movement between the articular processes and to consequently reduce friction[11]. The joint is encapsulated, and the amount of space in the joint capsule has a synovial fluid capacity of approximately 1-2 mL [12], while larger facets are more likely to carry a wider capsule[13]. Finally, the outer layer of this facet capsule is known as the capsular ligament [14]. The capsular ligaments provide joint stability and act as a form of mechanical support throughout facet contact and separation. 2 Figure 1.1: Facet joint capsule. IAP, inferior articular process; SAP, superior articular process; cart, articular cartilage; men, meniscus[10]. It has been shown that the curvature of the articular facet surfaces varies both by the level of the spine as well as between subjects. Horwitz et al. [15] performed a roentgenographic study of the lumbar spine on a population of 25 human cadaveric spines (Table 1.1). Samples from the population
Details
-
File Typepdf
-
Upload Time-
-
Content LanguagesEnglish
-
Upload UserAnonymous/Not logged-in
-
File Pages68 Page
-
File Size-