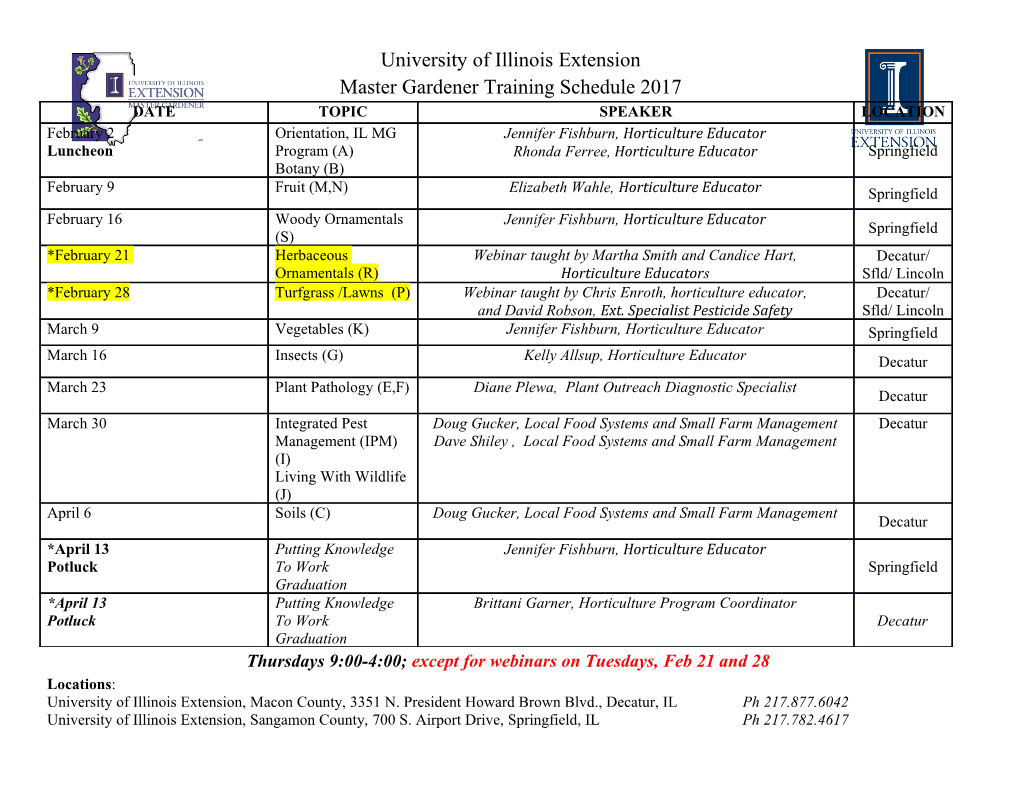
machines Article Investigation of the Mechanical Properties of a Carbon Fibre-Reinforced Nylon Filament for 3D Printing Flaviana Calignano 1,* , Massimo Lorusso 2 , Ignanio Roppolo 3 and Paolo Minetola 1 1 Department of Management and Production Engineering, Politecnico di Torino, Corso Duca degli Abruzzi 24, 10129 Turin, Italy; [email protected] 2 Istituto Italiano di Tecnologia, Center for Sustainable Future Technologies IIT@Polito, Corso Trento 21, 10129 Turin, Italy; [email protected] 3 Department of Applied Science and Technology, Politecnico di Torino, Corso Duca degli Abruzzi 24, 10129 Turin, Italy; [email protected] * Correspondence: fl[email protected]; Tel.: +39-011-090-7218 Received: 19 July 2020; Accepted: 2 September 2020; Published: 4 September 2020 Abstract: Additive manufacturing (i.e., 3D printing) has rapidly developed in recent years. In the recent past, many researchers have highlighted the development of in-house filaments for fused filament fabrication (FFF), which can extend the corresponding field of application. Due to the limited mechanical properties and deficient functionality of printed polymer parts, there is a need to develop printable polymer composites that exhibit high performance. This study analyses the actual mechanical characteristics of parts fabricated with a low-cost printer from a carbon fibre-reinforced nylon filament. The results show that the obtained values differ considerably from the values presented in the datasheets of various filament suppliers. Moreover, the hardness and tensile strength are influenced by the building direction, the infill percentage, and the thermal stresses, whereas the resilience is affected only by the building direction. Furthermore, the relationship between the mechanical properties and the filling factor is not linear. Keywords: additive manufacturing; 3D printing; fused filament fabrication; carbon fibre; mechanical testing 1. Introduction Additive manufacturing (i.e., 3D printing) is constantly evolving due to open source technologies [1–3] and the possibility of producing complex geometries with lower costs, faster production times, and less waste [4–6] than traditionally manufactured parts [7]. Moreover, with the increase in available materials, 3D printing has found applications in the aerospace and architectural industries (e.g., creating complex lightweight and structural models) [8,9], art fields [10,11], and medical fields (e.g., printing tissues and organs) [12,13]. However, most plastic 3D printed products are still used primarily as conceptual prototypes rather than functional components because of the poor mechanical and functional properties of the neat polymer used in 3D printing. The development of polymer composites solves these problems [14]. The incorporation of fibre and nanomaterial reinforcements into polymers allows the manufacture of polymer matrix composites, which are characterized by high mechanical performance and excellent functionality [14,15]. One process that has been extensively utilized in the fabrication of polymeric 3D printed parts is fused deposition modelling (FDM), which was developed by Stratasys Inc. In 2009, Stratasys’s FDM printing patent expired, opening up the market for low-cost FDM 3D printers. For non-Stratasys 3D printers, this process is usually referred to as fused filament fabrication (FFF). In FFF, a thin filament wire is extruded through a heated nozzle (Figure1). Machines 2020, 8, 52; doi:10.3390/machines8030052 www.mdpi.com/journal/machines Machines 2020, 8, 52 2 of 13 Machines 2020, 8, x FOR PEER REVIEW 2 of 13 The FFF headfabrication moves (FFF). in the In FFF, x and a thin y directions,filament wire whereasis extruded the through platform a heated moves nozzle in(Figure the z1). direction. The FFF The part is manufacturedhead moves by the in the sequential x and y directions, build-up whereas of these the layered platform depositions,moves in the z duringdirection. which The part each is new layer fuses withmanufactured material that by hasthe sequential already build-up been deposited. of these layered The depositions, final strength, during which quality, each cost new andlayer production time of thefuses parts with fabricated material that by has FFF already are influenced been deposited. by someThe final process strength, parameters, quality, cost and such production as layer thickness, time of the parts fabricated by FFF are influenced by some process parameters, such as layer thickness, infill pattern,infill extruder pattern, extruder uniformity uniformity and and/or/or build-bed build-bed temperature, temperature, and by and the bypresence the presence of reinforcing of reinforcing materials (e.g.,materials carbon (e.g., carbon fibres, fibres, glass glass fibres fibres [16 [16]).]). Machines 2020, 8, x FOR PEER REVIEW 3 of 13 TableFigure 1. AFigure summary 1. Fused 1. Fused of some filament filament studies fabrication fabrication on FFF with process. process.chopped fibres. Matrix Investigated ReinforcementSome researchers have correlated the build orientation (FigureLimitations 2b) to the mechanical propertiesReferences Some researchers haveMaterial correlated theProperties build orientation (Figure2b) to the mechanical properties of of the part [17–22]. The variations in quality of the meltPorosity, between weak adjacentinterfacial filaments adhesion results in a the part [17–22]. The variations in qualityTensile of strength the melt and between adjacent filaments results in a degradation degradationCarbon fibres in mechanicalABS properties (tensile strength,between compressive the fibres strength, and the matrix flexural strength,[27] tensile modulus in mechanicalhardness, properties and elastic (tensile modulus), strength, especially compressive for parts tested strength, perpendicularand fibre flexural breakage to strength, the direction hardness, of layer and elastic modulus),construction. especially forIn addition parts tested to the perpendicularorientation of the topartInterlayer the on directionthe fusion,building intralayer of platform, layer fusion, construction. the mechanical In addition Vapour-grown Tensile strength and properties of FFF partsABS are also significantly influencedand aby change the fromprocess ductile parameters to brittle of inherent[28] to the orientationcarbon offibres the part on the buildingtensile modulus platform, the mechanical properties of FFF parts are layering (Figure 2a,c), such as the layer thickness, raster angle, rasterbehaviour width, infill pattern and air gap also significantly[17,22–25]. influenced Ahn et al. [23] by determined the processStrength, that stiffness,both parameters the air gap and of inherentthe raster orientation layering had (Figure significant2a,c), such as the layer thickness,effects on the raster resulting angle, tensile rasterstrength,thermal width, whereas properties, infill these factors pattern did andnot affect air the gap compressive [17,22–25 strength.]. Ahn et al. [23] Carbon fibres ABS [30] determinedA thatsimilar both study the was air carried gap out and bydistortion, the Sood raster et andal. [17]orientation with varying had factors significant of layer thickness, effectson build the resulting geometric tolerances tensile strength,orientation, whereas raster angle, these raster factors width, did and not air agaffp:ect the the tested compressive factors influenced strength. the mesostructuralA similar study was configuration of the built part andTensile the bonding strength, and distortionDecreases within in toughness, the part. yield Lužanin et al. [26] Young’s modulus, strength and ductility and increases carried outstudied byCarbon Sood the fibres effects et al. of [17 layer]ABS with thickness, varying deposition factors angle of and layer infill thickness, percentage on build the maximum orientation, flexural[31] raster angle, and flexural in porosity with increased carbon force in FFF specimens made of polylactic acid (PLA) and concluded that layer thickness has the raster width, and air gap: the tested factorsproperties influenced the mesostructuralfibre content configuration of the built part maximum effect on the flexural strength followed by the interaction between the deposition angle and the bonding and distortion withinTensile the part.strength Lužanin and et al. [26] studied the effects of layer thickness, andCarbon the infill fibres percentage. PLA Despite its advantages over conventional manufacturing processes,[32] FFF deposition angle and infill percentagetensile on modulus the maximum flexural force in FFF specimens made of parts often exhibit low mechanical properties. One of theCritical possible factors methods for the to fracture improve the strength polylactic acidof FFF (PLA) parts andis adding concluded reinforcing that materials, layer thickness such as carbon hastoughness: the fibres, maximum bead into layup pure sequence, effectthermoplastic on the matrix flexural strength Carbon fibres PLA Fracture properties [33] followed bymaterials the interaction to form carbon between fibre-rein theforced deposition thermoplastic anglefiber composites and pullout, the infill [interfacial27–29]. percentage. Several de-bonding, studies Despite have been its advantages over conventionalconducted manufacturing related to FFF and processes, carbon fibre FFF (CF) parts composites. often exhibitandA list void of formation lowvarious mechanical studies of FFF properties. with One of chopped fibre-reinforced thermoplastics is given in TableTensile 1. strength increases with infill Carbon fibres
Details
-
File Typepdf
-
Upload Time-
-
Content LanguagesEnglish
-
Upload UserAnonymous/Not logged-in
-
File Pages13 Page
-
File Size-