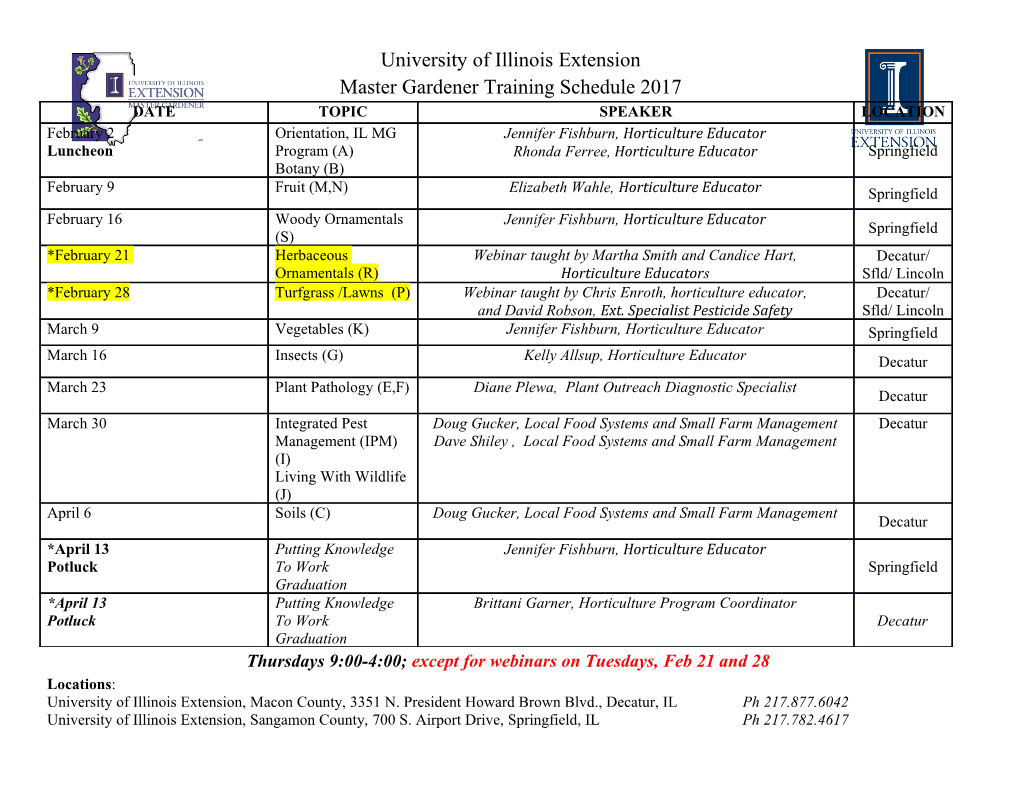
NASA CONTRACTOR NASA CR-2224 REPORT CS| CVI DEVELOPMENT AND EVALUATION OF MAGNETIC AND ELECTRICAL MATERIALS CAPABLE OF OPERATING IN THE 800° TO 1600° F TEMPERATURE RANGE by P. E. Kueser and J. W. Toth Prepared by WESTINGHOUSE ELECTRIC CORPORATION Lima, Ohio for Lewis Research Center NATIONAL AERONAUTICS AND SPACE ADMINISTRATION • WASHINGTON, D. C. • MARCH 1973 1. Report No. 2. Government Accession No. 3. Recipient's Catalog No. NASA CR-2224 4. Title and Subtitle 5. Report Date DEVELOPMENT AND EVALUATION OF MAjG^TJC-AND,.- .,.,-..., March 1973 ELECTRICAL MATERIALS CAPABLE OF OPERATING- IN THE ' 6. Performing Organization Code 800° TO 1600° F TEMPERATURE RANGE 7. Author(s) 8. Performing Organization Report No. P. E. Kueser and J. W. Toth WAED 68. 05E iu. Work Unit No. 9. Performing Organization Name and Address Westinghouse Electric Corporation 11. Contract or Grant No. Lima, Ohio NAS 3-6465 13. Type of Report and Period Covered 12. Sponsoring Agency Name and Address Contractor Report National Aeronautics and Space Administration 14. Sponsoring Agency Code Washington, D. C. 20546 15. Supplementary Notes Project Manager, Russell A. Lindberg, Materials and Structures Division, NASA Lewis Research Center, Cleveland, Ohio 16. Abstract This report summarizes results of a research program on electrical materials for advanced space electric power systems. The areas investigated included improved high-temperature magnetic materials, high-temperature capacitor materials, ceramic-to-metal bore-seal technology, and simulated-space environmental testing of electric-power system components. 17. Key Words (Suggested by Author(s)) 18. Distribution Statement High temperature; Insulation; Boron nitride; Unclassified - unlimited Capacitors; Aging; Ceramics; Vacuum; Mag- netic; Electrical; Bore seal; Plasma arc spraying; Space; Conductors; Materials 19. Security Qassif. (of this report) 20. Security Classif. (of this page) 21. No. of Pages 22. Price* Unclassified Unclassified 31 $3.00 * For sale by the National Technical Information Service, Springfield, Virginia 22151 TABLE OF CONTENTS Section Title Pa; I INTRODUCTION . 1 II PROGRAM I - HIGH TEMPERATURE MAGNETIC MATERIALS 3 A. Summary of Technical Results 3 B. Conclusions and Recommendations 7 1. Conclusions 7 2. Recommendations 8 III PROGRAM II - HIGH TEMPERATURE CAPACITOR FEASI- BILITY 9 A. Summary of Technical Results 9 B. Conclusions and Recommendations 12 1. Conclusions 12 2. Recommendations 12 IV PROGRAM III - BORE SEAL DEVELOPMENT AND COM- BINED MATERIALS INVESTIGATION 15 A. Summary of Technical Results , 5 1. Magnetic Materials ,„ 2. Conductor Materials .. _ 3. Insulation Materials ._ a. Rigid ,g b. Flexible 2Q c. Plasma-arc sprayed A^Oo Interlaminar Insulation 20 d. Conductor Insulation 20 B. Conclusions and Recommendations 23 1. Conclusions 23 2. Recommendations 26 REFERENCES 27 ill FIGURES Number Title Pagt 1 Stress to Produce 0.4 Percent Creep Strain in 10,000 Hours Based Upon Extrapolations Using the Larson-Miller Parameter 5 2 Magnetic Induction Versus Temperature at a Mag- netization of 250 to 300 Oersteds for High Temperature Magnetic Alloy Developed on this Program Compared to Existing Alloys 6 3 Figure of Merit (M) for Four Different Dielectric Materials Expressed as the Relative Ratio f-^-1 10 [_MBNj 4 Three Element Sputtering Assembly and Associated Fixturings 11 5 A Five-Layer Stacked Capacitor Showing Tabbed Wafers and Electrode Geometries and Electrode Orientation Necessary for Parallel Electrical Interconnection 13 6 Capacitance Versus Temperature and Time at In- creased DC Energizing Voltages (Constant Temperature; 1100°F) in Vacuum for a Five Wafer Multilayer Pyrolytic Boron Nitride Capacitor 14 7 Overall Summary of Room Temperature Flexural Strength of 99.8% Beryllia (Thermalox 998) Bars and Brazed Modulus-of-Rupture Assemblies as Pre- pared and for Various Exposure Conditions ... 17 8 Assembled 4-inch-diameter Bore Seal Capsule ... 18 9 Cutaway View of Test Stator Without a Bore Seal . 21 10 Cutaway View of Vacuum Furnace Showing the Stator Test Specimen Installed 23 11 Stator Conductor Resistance vs. Endurance Test Time at 1100° and 1300°F Conductor Hot-Spot Temperatures 24 12 Stator Insulation System Performance, Phase-to- Phase vs. Endurance Test Time - 1100°F Model . 24 13 Stator Insulation System Performance, Phase-to- Phase vs. Endurance Test Time - 1300°F Model . 25 IV TABLES Number Title Page I Application Temperatures for Potential High Temperature Rotor Magnetic Materials 7 II Bore Seal Materials Evaluated 15 III Insulation Performance of 1100° and 1300°F Stators (Hot-Spot Temperatures) in a Vacuum in the 10~^ Torr Range 25 SECTION I INTRODUCTION This is the final report on NASA Contract NAS3-6465 summarizing the program results and technical developments on magnetic, capac- itor, electrical conductor, electrical insulation and bore seal materials suitable for application to advanced space electric power systems. The contract consisted of three programs as follows: Program I - Magnetic Materials for High-Temperature Operation. Program II - High-Temperature Capacitor Feasibility. Program III - Bore Seal Development and Combined Materials Investigations Under a Space Simulated Environment. Program I was directed toward the improvement and further develop- ment of magnetic materials suitable for application in the rotor of a generator or motor in advanced space electric power systems. Program II was carried out to determine the feasibility of build- ing a lightweight compact capacitor suitable for operation up to 1100°F in vacuum with low electrical losses. One type of appli- cation for such a device is in static power conditioning apparatus for space applications. Program III extended the bore seal development work initiated under Contract NAS3-4162 (ref. 1)*. The ultimate objective of this program was to design and fabricate a four-inch diameter ceramic to columbium-1% zirconium bore seal capsule for life testing in the 1100° to 1400°F temperature range. Materials com- patibility was determined by life-test evaluation of constructed test models in which the various magnetic, electrical and insula- tion materials were applied to the designs as they would be in actual space electric power components. Detailed reporting of the work accomplished on these programs is given in three Topical Reports entitled "High Temperature Mag- netic Materials (WAED 67.34E)" (ref. 2), "High Temperature Capac- itor (WAED 67.24E)" (ref. 3), and "Bore Seal Development and Simulated Space Evaluation of High-Temperature Electrical Mater- ials and Components (WAED 67.46E)" (ref. 4). Seven Quarterly * References are identified at the end of this report, Reports (refs. 5, 6, 7, 8, 9, 10, and 11) were also written to report progress as the programs were carried out. Sections II, III, and IV summarize the technical results on mag- netic materials (Program I), capacitor materials (Program II), and bore seal and materials compatibility test models (Program III). Each section contains a technical discussion and conclu- sions and recommendations for that program. SECTION II PROGRAM I - HIGH TEMPERATURE MAGNETIC MATERIALS A. SUMMARY OF TECHNICAL RESULTS The objective of this program was to investigate methods of im- proving the magnetic and mechanical properties of materials suitable for application in the rotor of a generator or motor in advanced space electric power systems. Particular emphasis was placed on improving material strength at high temperature while retaining useful magnetic properties. The investigation was centered in four areas, as follows: 1. Precipitation hardened magnetic materials for application in the 1000° to 1200°F temperature range. 2. Investigation for raising the alpha-to-gamma transforma- tion temperature in cobalt-iron alloys. 3. Dispersion strengthened magnetic materials for applica- tion in the 1200° to 1600°F temperature range. 4. Creep testing of Nivco alloy. Two precipitation hardened magnetic alloys were developed through the laboratory stage for application in rotating electrical ap- paratus operating in the 1000° to 1200°F temperature range. One experimental martensitic type alloy and one cobalt-base alloy sur- passed the magnetic and mechanical properties of similar alloys commercially available, particularly for the 1000° to 1200°F temperature range. The greatest improvement exhibited over presently available alloys was in thermal stability. The rever- sion to austenite (non-magnetic) in the experimental martensitic alloys began about 150°F higher than in 15 percent nickel marag- ing steel. The precipitation hardened cobalt-base alloy exhibited excellent creep properties to 1200°F. Under similar test con- ditions, the creep strain of this alloy was one-third that of commercially available Nivco alloy. Attempts to increase the alpha-to-gamma transformation tempera- ture in the cobalt-iron system alloys did not produce useful results. In most cases, the addition elements depressed the transformation temperature. Two dispersion strengthened magnetic alloys were developed as candidates for application in the 1200° to 1600°F temperature range in rotating electrical apparatus, one each in the cobalt base system and in the iron-27 percent cobalt system. The cobalt base alloy demonstrated the capability of being able to sustain 10,000 psi stress for 10,000 hours with less than 0.4 percent creep strain at a temperature within the 1200° to 1600 F range. Also, in this range the coercive force was always less than 12 oersteds, while saturation magnetization
Details
-
File Typepdf
-
Upload Time-
-
Content LanguagesEnglish
-
Upload UserAnonymous/Not logged-in
-
File Pages33 Page
-
File Size-