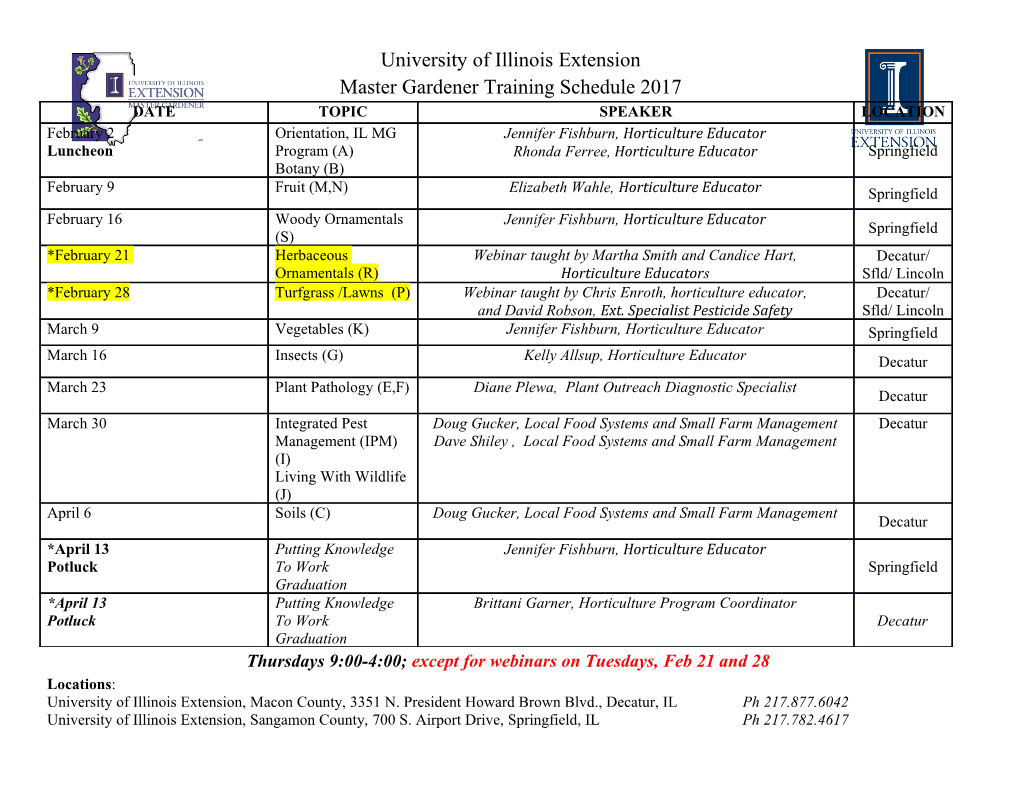
PAPER Evaluation of a Microsilica-Based Additives in Al2O3–MgO Refractory Castables T. dos Santos Jr., L. F. Krol, A. P. Luz, C. Pagliosa,V. C. Pandolfelli The first heating cycle of MgO-containing refractory castables is usually considered a challenge by the pro- ducers of such products due to the significant mass loss, associated with magnesium hydroxide decomposi- tion between 350–450 °C, that might result in their spalling or even explosion. In order to allow faster and safer drying of this sort of refractory system, a microsilica-based additive (SioxX-Mag) has been developed. Thus, this work focused on investigating the action of this commercial additive in high-alumina castables bonded with 6 mass-% of MgO and prepared with the addition of formic acid. Flowability, hot Young’s modulus, thermogravimetric analyses, cold and hot mechanical measurements were carried out to infer the properties of the compositions with and without the selected SiO2-based product. According to the collected results, the addition of 1 mass-% of the microsilica-containing additive to the designed castables resulted in higher flow and reduced MgO hydration. Consequently, even when subjecting these samples to a very high heating rate (20 °C · min–1), no explosion was detected. When increasing the firing tempera- ture, the interaction among Al2O3–MgO–SiO2 induced the increase of the castables’ mechanical strength up to 900 °C, but liquid phase formation was identified in the tested compositions above 1000 °C, causing the drop of their mechanical properties. Nevertheless, thermodynamic calculations and experimental tests indicated that the formed liquid should progressively react with the castables’ components, giving rise to refractory phases such as mullite and forsterite. Hence, the evaluated microsilica-based additive can be a potential solution to adjust the drying behavior and prevent the explosion of MgO-containing castables. Although eq. 1 is a simple reaction, the 1 Introduction control of brucite formation in the matrix T. dos Santos Jr., L. F. Krol, A. P. Luz, Besides its high melting point (2800 °C), fraction of MgO-containing castable com- V. C. Pandolfelli good compatibility with basic slags and positions during mixing, curing and/or dry- Federal University of São Carlos great likelihood of reacting with alumina ing stages is a difficult task, as various pa- Materials Engineering Department at high temperatures for spinel (MgAl2O4) rameters (i.e., temperature, water amount São Carlos, SP, 13565-90 generation, magnesium oxide (MgO) is and magnesia granulometry, surface area Brazil pointed out as a potential binder com- and volume) might affect the growing of pound, which can replace the traditional this hydrated phase [5–10]. Consequently, C. Pagliosa calcium aluminate cement, in refractory it is of utmost importance to optimize the RHI Magnesita, Research and Development castable systems comprising low CaO con- nucleation and growing rate of Mg(OH)2 Center tent [1–4]. This binder action is related to during the processing of such refractories, Contagem, MG, 32210-050 MgO hydration reaction with water and in order to inhibit cracking and flaws for- Brazil further brucite [Mg(OH)2] formation, as in- mation in their structure. Many studies re- dicated in eq. 1. Consequently, the brucite ported the use of different additives that Corresponding author: T. dos Santos Jr. crystals tend to fill in pores and voids found allow the adjustment of MgO-water reac- E-mail: [email protected] in the consolidated structure, increasing the tion, which can induce an effective incor- cohesion among the refractory constituents poration of MgO as binder in monolithic Keywords: MgO, hydration, brucite, and the overall mechanical strength level of products [4, 11–15]. Some authors also refractory, SioxX-Mag the samples during their curing and drying stated that, when this hydration reaction is stages. speed up during the early magnesia-water Received: 18.03.2019 contact, Mg(OH)2 crystals may be better Accepted: 01.04.2019 (eq. 1) accommodated in the resulting structure refractories WORLDFORUM 11 (2019) [3] 67 PAPER as the castables will not be fully hardened silicates (M-S-H gels) with distinct stoichi- fraction. According to the supplier of this yet [3, 16]. ometry, depending on the MgO and SiO2 product [31–33], the addition of 2 mass-% Among the MgO hydrating agents, formic molar ratio (M/S). For instance, Kalousek of SioxX-Mag to MgO castables contain- and acetic acids proved to be good options et al. [26] reported that a gel phase with ing 6 mass-% of SiO2 resulted in improved to control brucite formation in high-alumina chrysotile stoichiometry, Mg3Si2O5(OH)4, flowability, mechanical strength and large compositions, leading to the development can be obtained when M/S is equal to 1,5. pieces were molded without showing of refractories with high green mechanical On the other hand, when M/S is around cracking associated with magnesia hydra- strength [3, 4, 15–17]. However, in general, 0,75, talc phase [Mg3Si4O10(OH)2] might tion. Additionally, the tested compositions the high hydration level of such magnesia- be formed. These amorphous compounds presented higher explosion resistance. bonded products results in a significant limit the hydration of MgO grains, as they Although SioxX-Mag have been designed spalling/explosion trend for the prepared coat the surface of this oxide inhibiting for magnesia-based castables, most likely samples, when they are subjected to their its interaction with water. Consequently, this additive can act minimizing the explo- first heating cycle. As observed in previous cracking and flaws formation in the consoli- sion trend of high-alumina compositions research [15], the detected explosions of dated castables can be minimized with the containing MgO in their matrix fraction. It MgO-bonded castables took place mainly in reduction of brucite content formed in the is also expected that this product may fa- the 350–450 °C temperature range, due to matrix fraction of the microstructure, and vor a better control of magnesia hydration the steam pressure derived from brucite de- the likelihood of further spalling/explosion and improve the castables’ flow and green composition and carboxylates’ desorption. event during the first thermal cycle of these mechanical strength levels. Thus, this work Thus, in order to minimize or prevent the materials is significantly decreased. Moreo- investigated the effect of adding SioxX- formation of cracks or even the explosion of ver, some studies [14, 25] highlight that it is Mag to high-alumina vibratable castables MgO-containing castables, likely solutions more appropriate to induce the generation containing 6 mass-% of fine MgO and pro- consist of inducing the in situ formation of of chrysotile-like gels (M/S ~1,5) in refrac- cessed with formic acid (hydrating agent). hydrotalcite-like phases [18], or incorporat- tory mixtures because the decomposition of ing polymeric fibers [3, 19, 20] or amor- these compounds above 800 °C can give 2 Materials and methods phous silica sources [21] into the designed rise to forsterite (Mg2SiO4). The latter phase Vibratable castables were designed based compositions. Such alternatives will play a helps to improve the castables’ thermome- on Alfred’s particle packing model and us- role by changing the resulting microstruc- chanical properties due to its high refracto- ing distribution modulus q = 0,26 [34]. ture and favoring easier steam withdrawal. riness (melting point ~ 1840 °C). Tab. 1 shows more information about the Silica fume and additives derived from this Refractory users and producers have been raw materials and water contents used raw material are pointed out as efficient constantly interested in finding alterna- during the preparation of such composi- options to control MgO hydration in re- tives to promote fast and save drying of tions. The main constituents of the formu- fractory systems [14, 22–24]. According to ceramic linings. In this sense, new addi- lations were tabular alumina (d ≤ 6 mm, the literature [14, 23, 25], microsilica can tives have been developed to enhance the Almatis/DE), calcined and reactive alumi- be partially dissolved in basic pH aque- permeability of castables, without affecting nas (CT3000SG and CL370, Almatis/DE) ous medium, giving rise to silicilic acid in a greater extent their green mechanical and dead-burnt MgO with d50 = 15 µm – + (HSiO3 · OH3 ). This compound might also strength [21, 27–30]. This is the case of (M30 < 212 µm, RHI Magnesita/BR). The react with brucite phase formed on MgO a silica-based drying agent (SioxX-Mag), castables processed with formic acid con- surface in a further moment, which gen- which was designed for magnesia mono- tained 0,34 mass-% of this additive. A total erates amorphous hydrated magnesium lithics presenting microsilica in their matrix of 1 mass-% of SioxX-Mag (35 mass-% SiO2, 50 mass-% Al2O3, 15 mass-% oth- ers, Elkem/NO) was incorporated into the Tab. 1 General information of the castable compositions evaluated in this work mixtures prepared with and without formic A B C D acid and, as the microsilica-based product Remarks Only MgO MgO and MgO and MgO, Formic Acid already contained a dispersing agent in its Formic Acid SioxX-Mag and SioxX-Mag composition, no Castament® FS60 (BASF/ Components [mass-%] DE) addition was required processing casta- Tabular alumina 87 87 87 87 bles C and D. The reference compositions Fine aluminas 7 7 7 7 (A and B, without SioxX-Mag) were mixed (CL 370 C e with 4 mass-% of distilled water, whereas CT 3000 SG) the ones containing this microsilica-based M30 < 212 µm 6 6 6 6 additive (C and D) contained 4,5 mass-% Formic acid 0 0,34 0 0,34 of liquid. The compositions were mixed in a rheom- Castament® FS60 0,2 0,2 0 0 eter specially developed for refractory casta- SioxX-Mag 0 0 1,0 1,0 bles.
Details
-
File Typepdf
-
Upload Time-
-
Content LanguagesEnglish
-
Upload UserAnonymous/Not logged-in
-
File Pages9 Page
-
File Size-