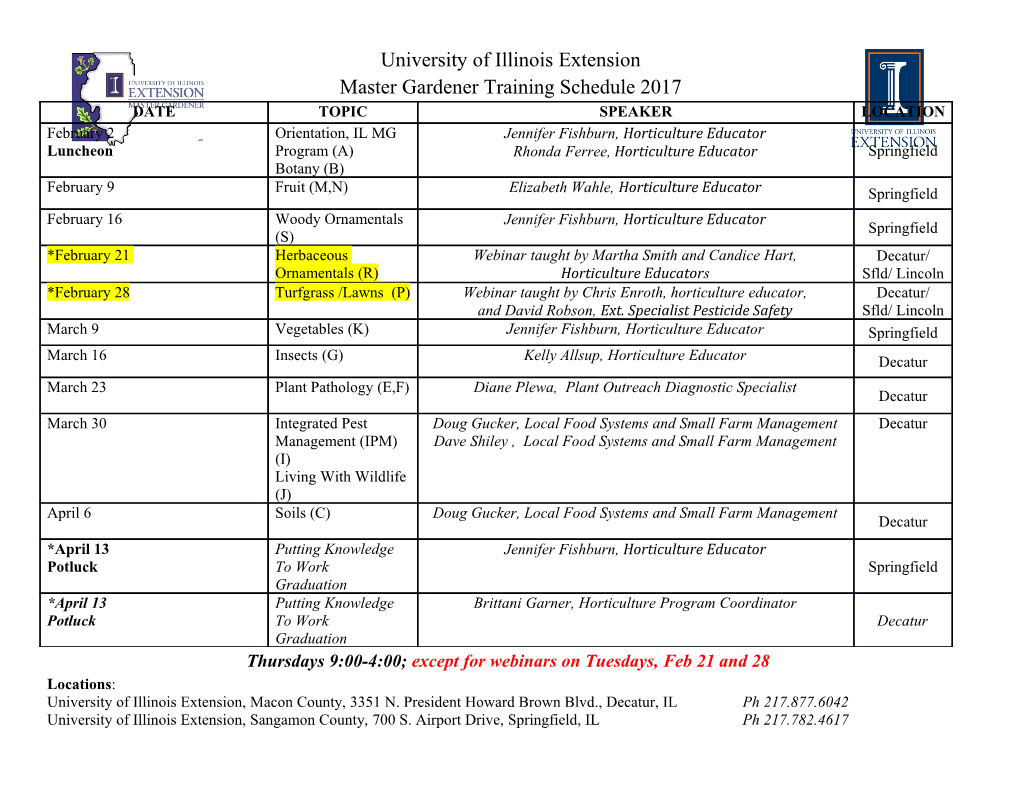
THE METHANIZER A Small Scale Biogas Reactor for a Restaurant R. Vasudevan, O. Karlsson, K. Dhejne, P. Derewonko, J.C. Brezet Delft University of Technology, Faculty of Industrial Design Engineering, Landbergstraat 15, 2628CE, Delft, The Netherlands, [email protected], +31 152782738. Abstract The purpose of this study is to determine the technical and economic feasibility of a small- scale bioreactor called the Methanizer for a restaurant. The bioreactor converts organic waste produced by the restaurant into methane. This methane can be used to power the restaurant’s cooking stoves. The system proposed is a double-tank, batch-fed bioreactor. This product will help reduce the need for natural gas as well as cut down on landfill use. Results from the technical analysis showed that the product would take 6 m3 of space, but is capable of saving a natural gas equivalent of 735 m3/year and 1470 m3/year for a small and medium sized restaurant, respectively. Economic analysis showed that the product is not economically viable for a small-scale restaurants but increased gas prices, subsidies, payment plans and scaling up to larger restaurants would make the Methanizer marketable. Producing a marketable Methanizer is estimated to take around four years and would therefore be possible in 2013. Keywords Bioreactor, Sustainability, Restaurant Industry, Food Waste, Biogas 1. Introduction It has become increasingly clear that the way that man interacts with the natural environment needs to change. Climate change caused by greenhouse gas emissions has become a major issue and the amount of waste being produced is causing a multitude of problems. All industries need to take a hard look at how they can change their activity to have a smaller impact on the environment. Restaurants are one such industry. Knowledge Collaboration & Learning for Sustainable Innovation ERSCP-EMSU conference, Delft, The Netherlands, October 25-29, 2010 1 Restaurants use a significant amount of fuel to power gas stoves. This primary source of this fuel is natural gas, a fossil fuel. Restaurants also produce a large amount of organic waste, which is usually taken by the municipality to sit in landfills. These two factors cost restaurants money and impact the environment in different ways. The product described in this report called the Methanizer decomposes the waste and produces fuel that would be able to power a gas stove. If done correctly, the utilization of the Methanizer would save restaurants money as well as reduce their impact on the environment. The following paper discusses the feasibility of producing the Methanizer for a restaurant. First, the technical concepts are explained. This is followed by some preliminary design decisions. Afterwards, energy and economic analyses are performed to really test the feasibility of this product. Finally, recommendations for implementation in the future are discussed. 2. Project Definition The research question asks if it feasible to implement a small-scale bioreactor for a restaurant? The concept being explored here is a bioreactor that will take a restaurant’s organic waste and produce methane, which can then be used to power a stove in the kitchen. This must be analyzed on a technical, energy and economic level. This would reduce a restaurant’s need for fossil fuels, reduce their waste processing cost, and burn up the methane that would become another greenhouse gas added to the atmosphere if the waste were to end up in a landfill. 3. Project Approach In order to determine whether or not the Methanizer is feasible, both technical and economic aspects must be investigated. Technical feasibility refers to whether or not the waste produced by a restaurant is sufficient to produce a significant amount of methane. The energy payback for the bio reactor is also taken into account in the technical feasibility. This means the energy used to run the Methanizer must be less than the energy that the Methanizer saves. The economic feasibility depends on the cost payback of the bio reactor system. The data used in the technical and economic feasibility analyses were determined through literary research and interviewing restaurants and experts in bioreactors. The restaurant interviews produced figures for volume of biomass waste, natural gas usage, and monthly The 14th European Roundtable on Sustainable Production and Consumption (ERSCP) The 6th Environmental Management for Sustainable Universities (EMSU) 2 gas cost for an average restaurant. The bioreactor research produced figures for capital cost, maintenance costs and schedule, and the food waste to methane production rate. 4. Background Research In this Section the theory behind the biogas production is described. First, biogas is explained. This is followed by an explanation of the reactor. After that, biogas functionality is explained both the generally and specifically for a restaurant. 4.1 What is Biogas? Biogas is considered as a renewable energy source that does not contribute to the greenhouse effect. The gas consists mainly of methane, CH4, and carbon dioxide, CO2, and resembles the commonly used fossil fuel, natural gas. Biogas can be used directly for heating or for electricity production in a generator. When it is burned with oxygen the exhaust gas contains of carbon dioxide and water. This carbon dioxide is the same that is absorbed by the material while it is still alive so biogas is “carbon neutral.” On the other hand, if the methane is not burned it can be released into the air where it acts as a much stronger greenhouse gas than carbon dioxide (R. Kleerebezem, personal communication, January 13, 2010). 4.2 The Biogas Process Biogas production is complicated since it includes many steps with different organisms and reactions. In this report, however, only the basic concept will be presented. It is a chemical process that occurs in anaerobic (oxygen free) surroundings. Inside a cow’s rumen, biogas is produced naturally, for example. Biogas is produced when microorganisms degrade organic material. The organic material can contain carbohydrates, fats and proteins that all breaks down to methane and carbon dioxide plus a remnant product. The remnants contain a lot of nutrients and can be used as fertilizers by farmers. The microorganisms that degrade the material exist naturally in the organic waste, so nothing needs to be added to the process (Carlsson & Uldal, 2009). The schematic picture in Figure 1 shows the different steps that take place in a biogas reactor. Pretreatment is sometimes needed for the reactor to work properly. This can mean chopping the waste material or mixing it with water if it is too thick. The upgrading is a process where the methane content is increased to get a gas that is more similar to natural gas and therefore more easily can be used in an existing gas grid (Carlsson & Uldal, 2009). Knowledge Collaboration & Learning for Sustainable Innovation ERSCP-EMSU conference, Delft, The Netherlands, October 25-29, 2010 3 There are a variety of possible substrates. For instance, pulp from sewage plants, manure from animals or food scraps from restaurants and households are all possible substrates. There are usually no problems in mixing different types of substrates. In fact, a mixture of substrates can increase methane production. Different substrates will have different energy content which gives the maximum biogas output (Carlsson & Uldal, 2009). Figure 1: Basic Flowchart for a Biogas Reactor (Carlsson & Uldal, 2009) 4.3 The Chemical Process The schematic picture in Figure 2 shows the chemical process of biogas production. It can be divided into three main steps: hydrolysis of the raw material, fermentation and methane production. In each step, different microorganisms work together to degrade the organic material into smaller components, which results in biogas production. The microorganisms are diverse and prefer different environments. The temperature used in a biogas reactor is usually either the mesophilic temperature, around 37°C, or the thermophilic temperature, around 55°C. Since the biogas process does not produce heat, this has to be added to reach the desired temperatures (Carlsson & Uldal, 2009). However, heating to this value would require a significant amount of energy. Using a reactor at room temperature is slower, but would be appropriate for a reactor at a small scale (R. Kleerebezem, personal communication, January 13, 2010). The 14th European Roundtable on Sustainable Production and Consumption (ERSCP) The 6th Environmental Management for Sustainable Universities (EMSU) 4 Figure 2: Schematic Picture of the Chemical Process in a Biogas Reactor (Carlsson & Uldal, 2009) 4.4 Biogas from Restaurant Waste Food waste is a good substrate for biogas production with high methane exchange. However, food waste creates an imbalance in the degrading process that lowers the pH-value in the reactor. This is caused by a fast degrading process in which fat acids are produced rapidly and are not consumed quickly by methanogens. Low ph-values can have a toxic affect on the methanogens, and the methane production can be stopped (GTZ & ISAT, n.d.). Food waste also needs some preparation to optimize the production. It is important to have good separation of all the non-organic materials that cannot decompose, such as plastics and metals. Otherwise the remnant product cannot be used as a fertilizer. The food also would need to be chopped and maybe some water needs to be added due to its high percentage of dry substance. With optimal conditions the biogas from restaurant waste has a methane level of 63%, if it is digested in a batch process. The methane exchange is 0.441 Nm3/kg TS, where TS is the Knowledge Collaboration & Learning for Sustainable Innovation ERSCP-EMSU conference, Delft, The Netherlands, October 25-29, 2010 5 dry substance of the food and is 27% for restaurant waste. This gives a biogas production of 0.119 Nm3/kg waste, which can be used directly to power stoves.
Details
-
File Typepdf
-
Upload Time-
-
Content LanguagesEnglish
-
Upload UserAnonymous/Not logged-in
-
File Pages22 Page
-
File Size-